La scelta della giusta temperatura di calcinazione è un passo fondamentale per garantire le proprietà e le prestazioni desiderate del materiale.La temperatura di calcinazione influenza direttamente le trasformazioni chimiche e fisiche del materiale, come la decomposizione, le transizioni di fase e la cristallizzazione.Per determinare la temperatura di calcinazione appropriata, occorre considerare la stabilità termica del materiale, la fase o la struttura desiderata e le capacità dell'apparecchiatura.Di seguito viene fornita una spiegazione dettagliata dei fattori chiave da considerare nella scelta della temperatura di calcinazione.
Punti chiave spiegati:
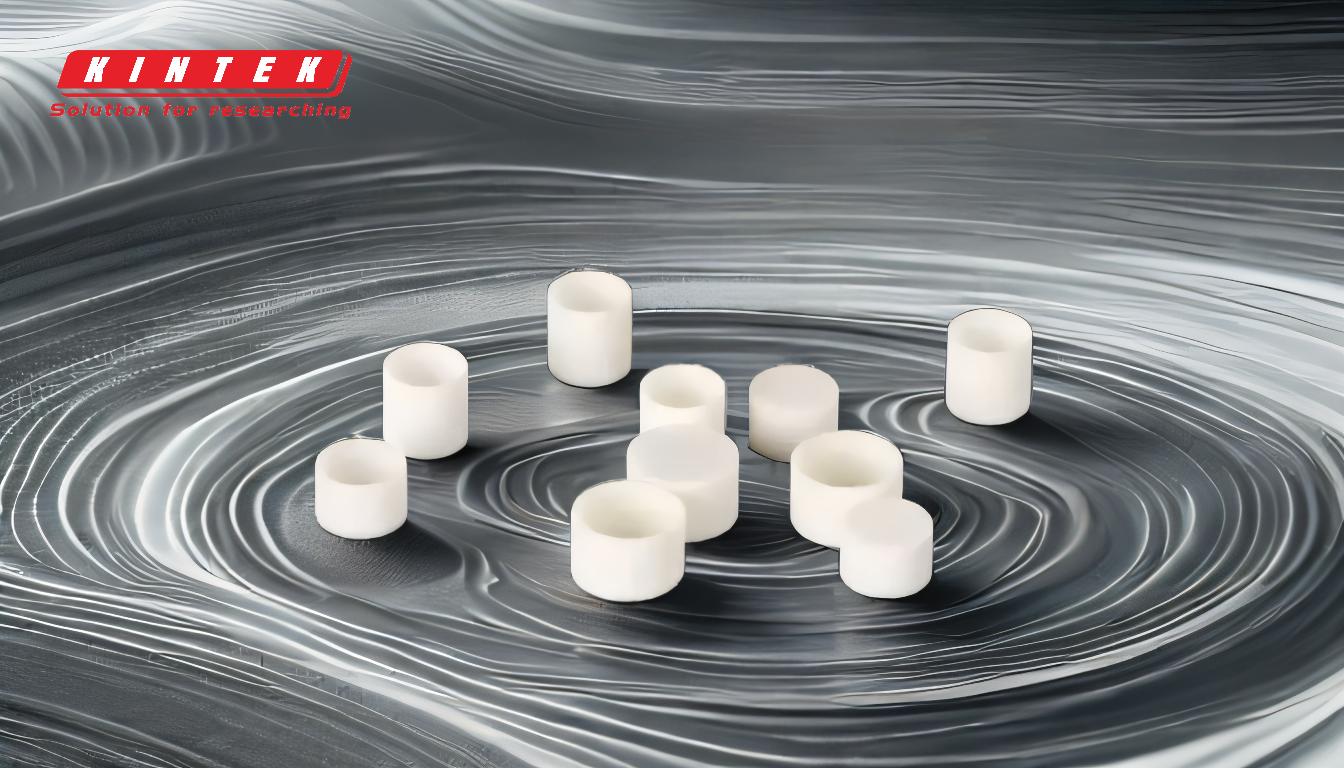
-
Comprendere il comportamento termico del materiale
- Temperatura di decomposizione termica:Determinare la temperatura alla quale il materiale subisce la decomposizione o i cambiamenti di fase.Questa può essere identificata attraverso tecniche come l'analisi termogravimetrica (TGA) o la calorimetria differenziale a scansione (DSC).
- Temperatura di transizione di fase:Identificare l'intervallo di temperatura in cui il materiale passa alla fase cristallina o amorfa desiderata.
- Stabilità termica:Assicurarsi che il materiale non si degradi o perda le proprietà previste alla temperatura di calcinazione scelta.
-
Definire il risultato desiderato
- Fase Purezza:Se l'obiettivo è ottenere una fase cristallina specifica, la temperatura di calcinazione deve essere in linea con la temperatura di formazione della fase.
- Dimensione e morfologia delle particelle:Temperature più elevate possono provocare la crescita dei grani o la sinterizzazione, mentre temperature più basse possono provocare reazioni incomplete.
- Composizione chimica:Assicurarsi che la temperatura di calcinazione non provochi reazioni indesiderate o perdita di componenti volatili.
-
Considerare i limiti dell'apparecchiatura
- Intervallo di temperatura del forno:La temperatura massima del forno dovrebbe superare di 100-200°C la temperatura di calcinazione richiesta per garantire prestazioni costanti ed evitare di operare al limite superiore del forno.
- Velocità di riscaldamento e uniformità:Il forno deve garantire un riscaldamento uniforme e un controllo preciso della temperatura per evitare gradienti termici che potrebbero influire sulle proprietà del materiale.
- Controllo dell'atmosfera:Se la calcinazione richiede un'atmosfera specifica (ad esempio, inerte, ossidante o riducente), assicurarsi che il forno possa mantenere le condizioni richieste.
-
Ottimizzazione attraverso prove sperimentali
- Esperimenti pilota:Condurre esperimenti su piccola scala per testare diverse temperature e durate di calcinazione.Analizzare le proprietà del materiale risultante per identificare la temperatura ottimale.
- Raffinamento iterativo:Regolare la temperatura in base ai risultati sperimentali, considerando fattori come la resa, la purezza della fase e la dimensione delle particelle.
- Caratterizzazione:Utilizzare tecniche come la diffrazione dei raggi X (XRD), la microscopia elettronica a scansione (SEM) e la spettroscopia infrarossa con trasformata di Fourier (FTIR) per valutare il materiale dopo la calcinazione.
-
Tenere conto dei vincoli pratici
- Efficienza energetica:Le temperature più elevate possono aumentare il consumo energetico e i costi operativi.Bilanciare le proprietà desiderate del materiale con l'efficienza energetica.
- Considerazioni sulla sicurezza:Assicurarsi che la temperatura scelta rientri nell'intervallo di funzionamento sicuro dell'apparecchiatura e non comporti rischi quali il surriscaldamento o la degradazione dei materiali.
- Scalabilità:Considerare se la temperatura scelta può essere raggiunta in modo costante in una produzione su larga scala.
-
Standard industriali e letteratura di riferimento
- Ricerca pubblicata:Esaminare gli studi su materiali simili per identificare le temperature di calcinazione comunemente utilizzate e i relativi risultati.
- Raccomandazioni del produttore:Consultare i produttori di apparecchiature per avere indicazioni sulle temperature di esercizio ottimali per materiali specifici.
- Dati storici:Se applicabile, utilizzare i dati di esperimenti o produzioni precedenti per prendere una decisione.
Considerando attentamente questi fattori, è possibile selezionare una temperatura di calcinazione che consenta di ottenere le proprietà desiderate del materiale, garantendo al contempo un funzionamento efficiente e sicuro.Il processo prevede una combinazione di comprensione teorica, convalida sperimentale e considerazioni pratiche per ottimizzare le condizioni di calcinazione.
Tabella riassuntiva:
Fattore chiave | Descrizione |
---|---|
Comportamento termico dei materiali | Identificare le temperature di decomposizione, transizione di fase e stabilità termica. |
Risultato desiderato | Definire gli obiettivi di purezza di fase, dimensione delle particelle, morfologia e composizione chimica. |
Limitazioni dell'apparecchiatura | Considerare l'intervallo di temperatura del forno, la velocità di riscaldamento, l'uniformità e l'atmosfera. |
Prove sperimentali | Condurre esperimenti pilota e perfezionare la temperatura in modo iterativo. |
Vincoli pratici | Bilanciare efficienza energetica, sicurezza e scalabilità. |
Standard di settore | Ricerche di riferimento, raccomandazioni dei produttori e dati storici. |
Avete bisogno di aiuto per scegliere la temperatura di calcinazione perfetta? Contattate i nostri esperti oggi stesso per una guida su misura!