I forni a resistenza, pur essendo molto efficienti e versatili, presentano diversi svantaggi che gli utenti devono considerare.Tra questi, l'elevato consumo di energia, l'aumento dei costi legati alla distribuzione dell'energia e all'elettricità e le difficoltà di isolamento alle alte temperature.Inoltre, la necessità di un'attenta collocazione dei materiali e la possibilità che i materiali refrattari conducano elettricità a temperature elevate sono inconvenienti notevoli.Questi fattori possono incidere sul costo complessivo e sull'efficienza dell'uso dei forni a resistenza in varie applicazioni industriali.
Punti chiave spiegati:
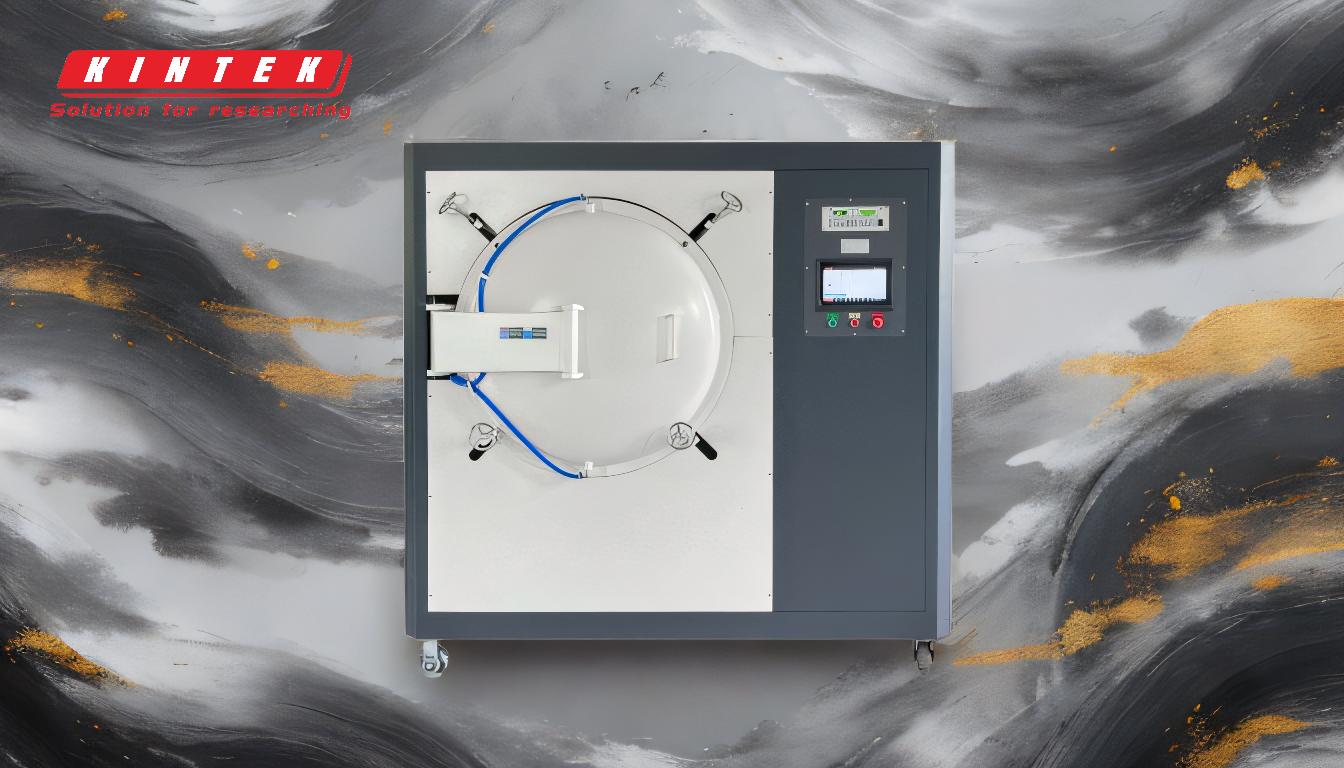
-
Alto consumo di energia:
- I forni a resistenza sono noti per il loro elevato consumo energetico.Ciò può comportare un aumento dei costi operativi, soprattutto nelle strutture in cui il forno viene utilizzato in modo intensivo.L'elevata richiesta di energia può anche richiedere l'aggiornamento dei sistemi di distribuzione dell'energia esistenti, con un conseguente aumento dei costi di installazione iniziali.
-
Aumento dei costi:
- Apparecchiature di distribuzione dell'energia:La necessità di aumentare la capacità delle apparecchiature di distribuzione dell'energia per gestire l'elevato fabbisogno energetico dei forni a resistenza può aumentare significativamente i costi di installazione iniziali.
- Costi dell'elettricità:Il costo continuo dell'elettricità può essere notevole, soprattutto nelle regioni in cui i prezzi dell'elettricità sono elevati.Questo può rendere i forni a resistenza meno convenienti rispetto ad altri metodi di riscaldamento a lungo termine.
-
Problemi di isolamento ad alte temperature:
- Quando la temperatura di riscaldamento supera i 1000°C, i materiali refrattari utilizzati nei forni a resistenza possono iniziare a condurre elettricità.Ciò richiede un'attenta cura dell'isolamento per evitare rischi per la sicurezza e garantire un funzionamento efficiente.La necessità di materiali isolanti specializzati può aumentare ulteriormente i costi.
-
Posizionamento e accessibilità dei materiali:
- Come i forni a muffola, anche i forni a resistenza possono presentare delle sfide in termini di posizionamento e accessibilità dei materiali.Il design del forno può rendere più difficile l'accesso all'interno, richiedendo un'attenta collocazione dei materiali per garantire un riscaldamento uniforme ed evitare danni.
-
Confronto con altri tipi di forno:
- Forni a muffola:Sebbene anche i forni a muffola presentino una serie di svantaggi, come tempi di riscaldamento più lunghi e problemi di accessibilità, possono essere più adatti per alcune applicazioni in cui non è richiesto un riscaldamento rapido.
- Forni a induzione:I forni a induzione, invece, non hanno capacità di raffinazione e richiedono materiali di carica privi di ossidi e di composizione nota.Ciò può limitarne l'uso in applicazioni in cui è necessaria la raffinazione.
In sintesi, se da un lato i forni a resistenza offrono un'elevata efficienza termica e buone condizioni di lavoro, dall'altro l'elevato consumo di energia, l'aumento dei costi e le difficoltà di isolamento alle alte temperature sono svantaggi significativi che devono essere considerati con attenzione.Questi fattori possono influire sul costo complessivo e sull'efficienza dell'uso dei forni a resistenza in varie applicazioni industriali.
Tabella riassuntiva:
Svantaggio | Dettagli |
---|---|
Elevato consumo di energia | Comporta un aumento dei costi operativi e può richiedere l'aggiornamento del sistema di alimentazione. |
Aumento dei costi | Costi più elevati per l'installazione iniziale e per l'elettricità continua. |
Sfide dell'isolamento | I materiali refrattari possono condurre l'elettricità a temperature superiori a 1000°C. |
Posizionamento del materiale | Richiede un posizionamento accurato per ottenere un riscaldamento uniforme e l'accessibilità. |
Confronto con altri forni | I forni a muffola e a induzione hanno pro e contro diversi. |
Avete bisogno di aiuto per scegliere il forno giusto per le vostre esigenze? Contattate i nostri esperti oggi stesso per una consulenza personalizzata!