La brasatura a induzione è un metodo altamente efficiente e preciso per unire i metalli utilizzando il calore generato dall'induzione elettromagnetica.La durata del processo dipende da diversi fattori, tra cui i materiali da unire, le dimensioni e la geometria dei componenti, il tipo di metallo d'apporto utilizzato e la potenza del sistema di riscaldamento a induzione.In generale, la brasatura a induzione può durare da pochi secondi a diversi minuti.Il processo è più veloce dei metodi di brasatura tradizionali grazie al riscaldamento localizzato, che riduce al minimo le zone termicamente interessate e i tempi complessivi del ciclo.Una corretta impostazione e l'ottimizzazione dei parametri sono fondamentali per ottenere risultati costanti e di alta qualità.
Punti chiave spiegati:
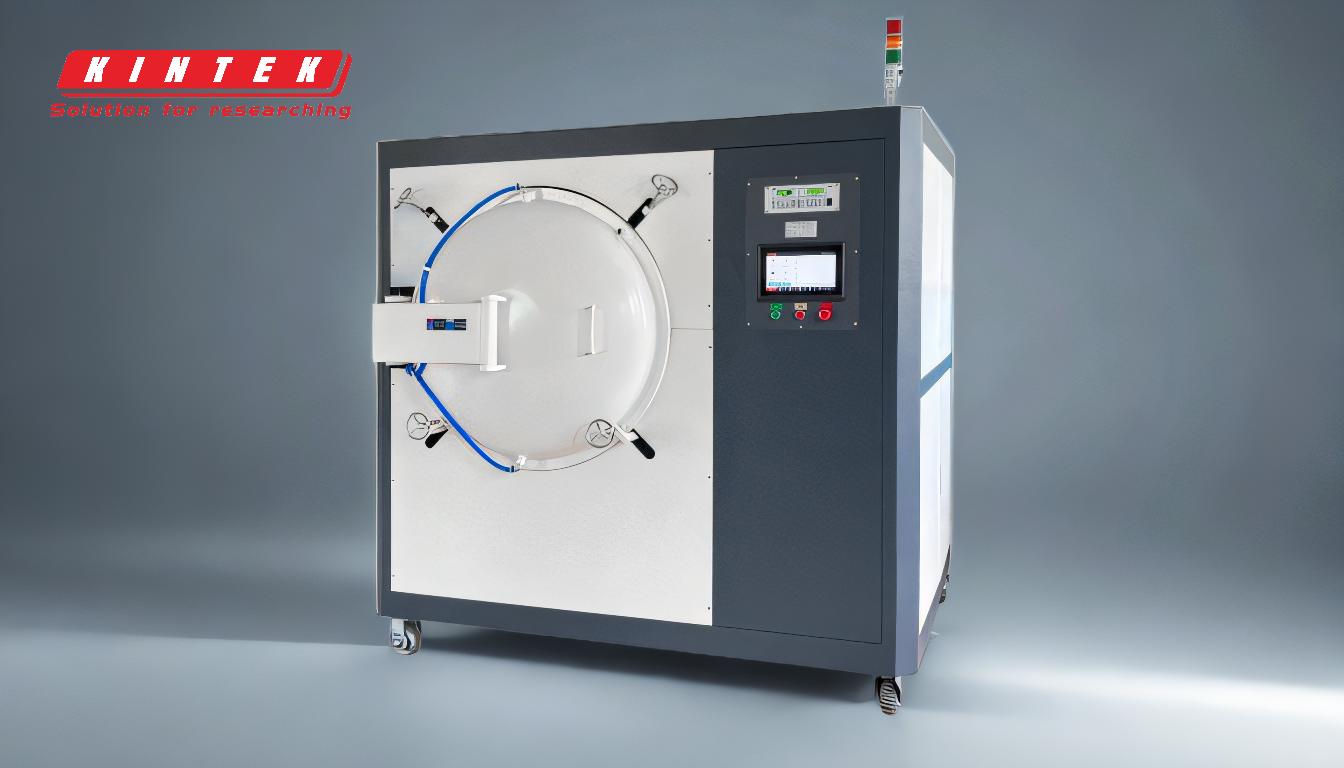
-
Fattori che influenzano il tempo di brasatura a induzione
- Proprietà del materiale:La conducibilità termica e i punti di fusione dei metalli di base e del materiale d'apporto influenzano in modo significativo il tempo di riscaldamento.Ad esempio, i materiali ad alta conducibilità termica, come il rame, si riscaldano più rapidamente di quelli a bassa conducibilità, come l'acciaio inossidabile.
- Dimensioni e geometria dei componenti:I pezzi più grandi o più complessi richiedono più tempo per essere riscaldati in modo uniforme.Le sezioni sottili si riscaldano più velocemente di quelle spesse e le geometrie uniformi sono più facili da riscaldare rispetto alle forme irregolari.
- Caratteristiche del metallo d'apporto:Il punto di fusione e le caratteristiche di flusso del metallo d'apporto influenzano il tempo di brasatura.I metalli d'apporto con punti di fusione più bassi riducono il tempo complessivo del ciclo.
- Potenza di riscaldamento a induzione:I sistemi a induzione di maggiore potenza possono generare calore più rapidamente, riducendo il tempo totale di brasatura.Tuttavia, è necessario evitare una potenza eccessiva per evitare il surriscaldamento o il danneggiamento dei componenti.
-
Tempi tipici di brasatura a induzione
- La brasatura a induzione è generalmente molto più veloce dei metodi tradizionali, come la brasatura a fiamma o in forno.
- Per i componenti di piccole dimensioni, il processo può richiedere anche solo 5-10 secondi .
- I pezzi di medie dimensioni possono richiedere da 30 secondi a 2 minuti .
- Gli assemblaggi più grandi o più complessi possono richiedere da 2 a 5 minuti o più, a seconda dei fattori sopra menzionati.
-
Vantaggi della brasatura a induzione in termini di efficienza temporale
- Riscaldamento localizzato:La brasatura a induzione riscalda solo l'area specifica in cui si trova il giunto, riducendo il tempo di riscaldamento complessivo e il consumo energetico.
- Velocità di riscaldamento rapido:Il processo di induzione elettromagnetica genera calore direttamente all'interno del pezzo, consentendo un riscaldamento più rapido rispetto ai metodi di riscaldamento esterni.
- Tempi di ciclo ridotti:La possibilità di controllare con precisione i cicli di riscaldamento e raffreddamento garantisce una produzione efficiente, soprattutto in caso di volumi elevati.
-
Ottimizzazione dei tempi di brasatura a induzione
- Progettazione corretta della bobina:La bobina di induzione deve essere progettata in modo da adattarsi alla geometria del pezzo, garantendo un riscaldamento uniforme ed efficiente.
- Regolazione dei parametri:La regolazione di parametri come la potenza, la frequenza e il tempo di riscaldamento è essenziale per ottenere risultati ottimali senza surriscaldamento o sotto riscaldamento.
- Pre-posizionamento del metallo d'apporto:Il corretto posizionamento del metallo d'apporto prima del riscaldamento garantisce una fusione e un flusso uniformi, riducendo la necessità di tempi di riscaldamento prolungati.
-
Applicazioni ed esempi
- Industria automobilistica:La brasatura a induzione è utilizzata per la giunzione di componenti come scambiatori di calore e parti di trasmissione, dove i tempi di ciclo rapidi sono fondamentali per la produzione di grandi volumi.
- Elettronica:Piccoli componenti come connettori e terminali vengono spesso brasati in pochi secondi grazie al riscaldamento a induzione.
- Aerospaziale:Assemblaggi complessi con requisiti di qualità rigorosi traggono vantaggio dalla precisione e dalla velocità della brasatura a induzione.
-
Confronto con altri metodi di brasatura
- Brasatura a torcia:In genere più lenta e meno costante a causa del controllo manuale e dell'applicazione più ampia del calore.
- Brasatura in forno:Adatta per grandi lotti, ma spesso comporta cicli di riscaldamento e raffreddamento più lunghi, il che la rende meno efficiente in termini di tempo per i pezzi di piccole o medie dimensioni.
- Brasatura a induzione:Offre la migliore combinazione di velocità, precisione e ripetibilità, rendendola ideale per i moderni ambienti di produzione.
In conclusione, la brasatura a induzione è un processo versatile ed efficiente in termini di tempo, che può essere adattato alle specifiche esigenze applicative.Comprendendo e ottimizzando i fattori che influenzano i tempi di brasatura, i produttori possono ottenere giunti di alta qualità con tempi di ciclo minimi, aumentando la produttività e riducendo i costi.
Tabella riassuntiva:
Fattore | Impatto sul tempo di brasatura |
---|---|
Proprietà del materiale | Un'alta conducibilità termica (ad esempio, il rame) si riscalda più rapidamente di una bassa conducibilità (ad esempio, l'acciaio). |
Dimensione/geometria del componente | I pezzi più grandi o complessi richiedono più tempo; le sezioni sottili si riscaldano più velocemente di quelle spesse. |
Metallo d'apporto | I metalli d'apporto a basso punto di fusione riducono i tempi di ciclo. |
Potenza di riscaldamento a induzione | I sistemi a più alta potenza riscaldano più velocemente, ma richiedono un controllo accurato per evitare danni. |
Intervallo di tempo tipico | Pezzi piccoli: 5-10 sec; pezzi medi: 30 sec-2 min; pezzi grandi: 2-5 min o più. |
Ottimizzate il vostro processo di brasatura a induzione per ottenere risultati più rapidi e di qualità. contattate i nostri esperti oggi stesso !