La velocità di riscaldamento dell'allumina dipende dall'applicazione specifica e dal tipo di forno utilizzato. In generale, la velocità di riscaldamento consigliata per i tubi dei forni di allumina è di 5-10°C/min, con una preferenza per 5°C/min per evitare shock termici e garantire una sinterizzazione uniforme. Anche la velocità di raffreddamento deve essere controllata, idealmente al di sotto di 10°C/min, con 5°C/min come valore ottimale. Rapide variazioni di temperatura possono causare stress termico, con conseguente rottura o sinterizzazione insufficiente. Per il riscaldamento iniziale, si consiglia una velocità inferiore di 150-300°C all'ora per ridurre al minimo lo shock termico. Queste linee guida garantiscono la longevità e le prestazioni dei componenti in allumina in ambienti ad alta temperatura.
Punti chiave spiegati:
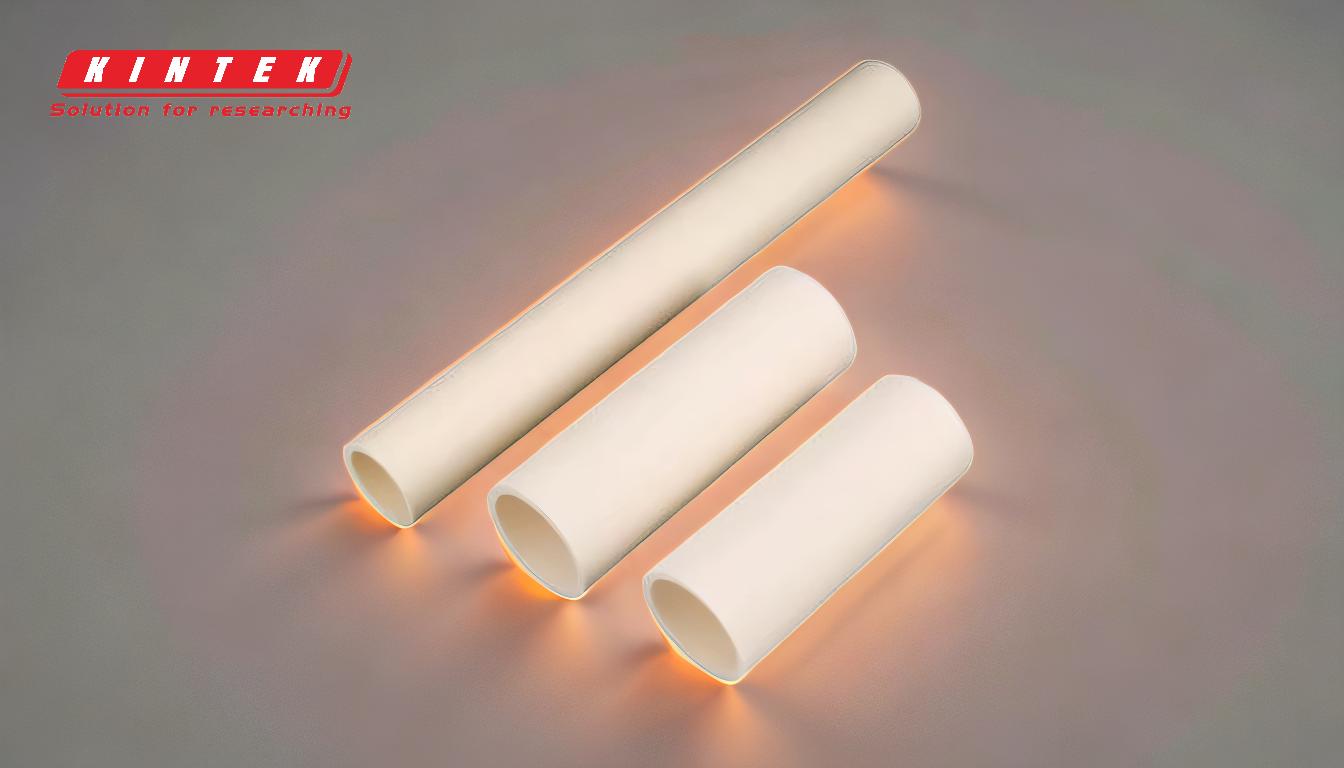
-
Velocità di riscaldamento consigliata per l'allumina:
- La velocità di riscaldamento standard per i tubi dei forni di allumina è di 5-10°C/min con 5°C/min è la velocità preferita. Ciò garantisce un riscaldamento uniforme e riduce al minimo il rischio di shock termico.
- Una velocità di riscaldamento più lenta di 150-300°C all'ora è consigliata per le prime 1-1,5 ore per ridurre lo shock termico, soprattutto durante la fase iniziale di riscaldamento.
-
Importanza del riscaldamento controllato:
- Velocità di riscaldamento eccessive (superiori a 10°C/min) possono portare a sinterizzazione insufficiente e gradi di sinterizzazione non uniformi sinterizzazione e gradi di sinterizzazione non uniformi nel materiale. Ciò comporta picchi di fusione ad alta temperatura e un aumento della cristallinità, che possono compromettere l'integrità strutturale dell'allumina.
- Il riscaldamento controllato assicura una sinterizzazione uniforme e previene le tensioni interne che potrebbero portare a crepe o rotture.
-
Considerazioni sulla velocità di raffreddamento:
- La velocità di raffreddamento deve essere inferiore a 10°C/min con 5°C/min è l'ideale. Un raffreddamento rapido può causare shock termico con conseguente rottura del materiale.
- Il raffreddamento graduale è essenziale per mantenere l'integrità strutturale dell'allumina, soprattutto dopo trattamenti ad alta temperatura.
-
Sensibilità agli shock termici:
- L'allumina è molto sensibile agli shock termici a causa della sua fragilità. Rapidi cambiamenti di temperatura possono causare crepe o rotture.
- Per ridurre questo rischio, si raccomanda una velocità di riscaldamento e raffreddamento più lenta (ad esempio, 150-300°C all'ora per il riscaldamento e 75-150°C all'ora per il raffreddamento).
-
Raccomandazioni specifiche per l'applicazione:
- Per tubi per forni in allumina le velocità di riscaldamento e raffreddamento devono essere in linea con i requisiti di progettazione e di funzionamento del forno. Il raffreddamento naturale dopo il trattamento termico deve essere evitato, in quanto può causare rapidi abbassamenti di temperatura e potenziali danni.
- Nei forni a tubo rotante fattori come l'angolo di inclinazione, la velocità di rotazione, la lunghezza del tubo e le proprietà di flusso del materiale influenzano il processo di trattamento termico. La regolazione di questi parametri può aiutare a mantenere i tassi di riscaldamento e raffreddamento ottimali.
-
Proprietà e durata del materiale:
- L'allumina ha un'eccellente resistenza agli shock termici, un'elevata densità e una resistenza agli acidi, agli alcali e all'erosione. Queste proprietà la rendono adatta ad applicazioni ad alta temperatura (fino a 1800°C).
- Il riscaldamento e il raffreddamento adeguati garantiscono la durata del materiale e ne prolungano la vita utile.
-
Consigli pratici per gli utenti delle apparecchiature:
- Impostare sempre una velocità di raffreddamento controllata nel programma del forno; evitare di interrompere bruscamente il programma a temperature elevate.
- Utilizzare variazioni graduali della temperatura per evitare stress termici e garantire prestazioni costanti del materiale.
- Monitorare attentamente il processo di riscaldamento e raffreddamento, soprattutto durante le fasi di riscaldamento iniziale e di raffreddamento finale.
Seguendo queste linee guida, gli utenti possono ottimizzare le prestazioni e la durata dei componenti in allumina in ambienti ad alta temperatura, garantendo risultati costanti e riducendo al minimo il rischio di rottura del materiale.
Tabella riassuntiva:
Parametro | Raccomandazione |
---|---|
Velocità di riscaldamento | 5-10°C/min (preferibilmente 5°C/min) |
Velocità di riscaldamento iniziale | 150-300°C all'ora per le prime 1-1,5 ore |
Velocità di raffreddamento | Inferiore a 10°C/min (idealmente 5°C/min) |
Sensibilità agli shock termici | Evitare rapidi sbalzi di temperatura per prevenire crepe e rotture. |
Vantaggi principali | Assicura una sinterizzazione uniforme, durata e longevità in ambienti ad alta temperatura. |
Avete bisogno di aiuto per ottimizzare il vostro processo di trattamento termico dell'allumina? Contattate oggi stesso i nostri esperti per soluzioni su misura!