Il processo di trattamento termico è un metodo critico utilizzato per alterare le proprietà fisiche e talvolta chimiche dei materiali, principalmente dei metalli, per ottenere le caratteristiche desiderate, come una maggiore resistenza, durezza o duttilità.Il processo prevede in genere quattro fasi fondamentali: riscaldare il materiale a una temperatura specifica, mantenerlo a quella temperatura per un periodo di tempo predeterminato, raffreddarlo secondo metodi specifici e, talvolta, eseguire ulteriori fasi come il rinvenimento o l'alleggerimento delle tensioni per perfezionare le proprietà del materiale.Queste fasi sono essenziali per garantire che il materiale soddisfi gli standard prestazionali richiesti per l'applicazione prevista.
Punti chiave spiegati:
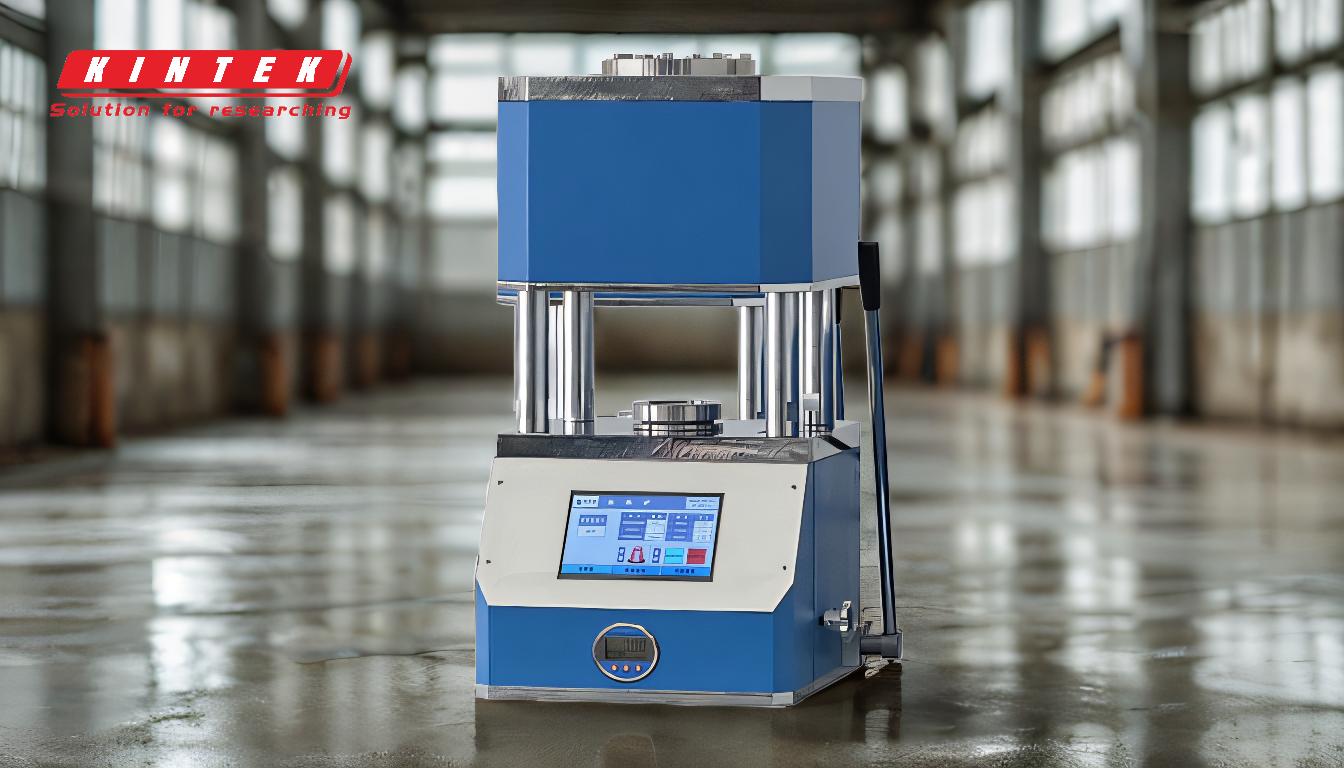
-
Riscaldamento a una temperatura specifica
- La prima fase del processo di trattamento termico prevede il riscaldamento del materiale a una temperatura precisa.Questa temperatura varia a seconda del materiale e del risultato desiderato.Ad esempio, la ricottura richiede in genere temperature più basse rispetto ai processi di tempra.
- Il riscaldamento può essere effettuato in diversi forni, come quelli elettrici, a gas o a induzione, a seconda del materiale e della scala di produzione.
- L'intervallo di temperatura può raggiungere i 1.315 °C (2.400 °F) per alcune leghe, garantendo che il materiale raggiunga la necessaria trasformazione di fase o lo stato di ricristallizzazione.
-
Mantenimento alla temperatura specificata
- Una volta raggiunta la temperatura desiderata, il materiale viene mantenuto a tale temperatura per una durata specifica.Questa fase assicura l'uniformità della microstruttura del materiale e consente di completare i processi di trasformazione o diffusione.
- Il tempo di mantenimento può variare da pochi secondi per materiali sottili a diverse ore o addirittura giorni per componenti più spessi o complessi.
- Questa fase è fondamentale per ottenere risultati coerenti, poiché un tempo insufficiente può portare a trasformazioni incomplete, mentre un tempo eccessivo può causare la crescita dei grani o altri effetti indesiderati.
-
Raffreddamento secondo i metodi prescritti
- Dopo che il materiale è stato mantenuto alla temperatura specificata, viene raffreddato con metodi controllati.La velocità di raffreddamento è fondamentale e varia a seconda delle proprietà desiderate.Ad esempio, il raffreddamento rapido (tempra) è utilizzato per indurire i metalli, mentre il raffreddamento lento è impiegato per la ricottura, per ammorbidirli.
- I metodi di raffreddamento comprendono il raffreddamento ad aria, la tempra in olio, la tempra in acqua o il raffreddamento in forno, ciascuno scelto in base al materiale e al risultato richiesto.
- Un raffreddamento inadeguato può causare problemi quali cricche, deformazioni o tensioni residue, rendendo questa fase fondamentale per il successo del processo di trattamento termico.
-
Fasi aggiuntive (facoltative)
- A seconda dell'applicazione, dopo il processo di trattamento termico iniziale possono essere eseguite fasi aggiuntive come il rinvenimento, la distensione o i trattamenti superficiali.
- Il rinvenimento, ad esempio, viene spesso utilizzato dopo la tempra per ridurre la fragilità e migliorare la tenacità, riscaldando il materiale a una temperatura inferiore.
- L'alleggerimento comporta il riscaldamento del materiale a una temperatura inferiore al suo intervallo di trasformazione per eliminare le tensioni interne causate dalla lavorazione, dalla saldatura o dalla formatura.
Queste quattro fasi costituiscono la base del processo di trattamento termico, che consente ai produttori di personalizzare i materiali per soddisfare i requisiti specifici di prestazione in settori quali l'aerospaziale, l'automobilistico e la produzione di utensili.La comprensione e il controllo di ogni fase sono essenziali per ottenere le proprietà desiderate del materiale e garantire la longevità e l'affidabilità del prodotto finale.
Tabella riassuntiva:
Passo | Descrizione | Dettagli chiave |
---|---|---|
Riscaldamento | Riscaldare il materiale a una temperatura precisa. | - La temperatura varia a seconda del materiale e del processo (ad esempio, ricottura o tempra). |
- Metodi di riscaldamento: forni elettrici, a gas o a induzione. | ||
- Le temperature possono raggiungere i 2.400°F (1.315°C) per alcune leghe. | ||
Mantenimento | Mantenere il materiale alla temperatura specificata per una durata prestabilita. | - Assicura una microstruttura uniforme e una trasformazione completa. |
- Il tempo di mantenimento varia da secondi a giorni, a seconda dello spessore e della complessità del materiale. | ||
Raffreddamento | Raffreddare il materiale con metodi controllati. | - La velocità di raffreddamento influisce sulle proprietà del materiale (ad esempio, tempra per l'indurimento, raffreddamento lento per la ricottura). |
- I metodi comprendono il raffreddamento ad aria, la tempra in olio, la tempra in acqua o il raffreddamento in forno. | ||
Fasi aggiuntive | Fasi opzionali come il rinvenimento o l'alleggerimento delle tensioni. | - Il rinvenimento riduce la fragilità e migliora la tenacità. |
- La distensione rimuove le tensioni interne causate dalla lavorazione o dalla saldatura. |
Ottimizzate le proprietà dei vostri materiali con soluzioni esperte di trattamento termico... contattateci oggi stesso !