Considerazioni generali per lo sputtering con magnetronio
Manutenzione dell'ambiente sotto vuoto
Lo sputtering magnetronico richiede un ambiente sotto vuoto impeccabile per evitare gli effetti dannosi delle impurità presenti nell'aria sulla qualità del film. L'ambiente sottovuoto non è un semplice sfondo, ma un componente critico che garantisce l'integrità e la precisione del processo di sputtering.
Nei forni a vuoto, i componenti meccanici, come le guarnizioni e le giunzioni saldobrasate, sono sottoposti a una rigorosa manutenzione per mantenere lo stato di assenza di perdite del vuoto. Questa manutenzione meticolosa è essenziale perché anche piccole perdite possono compromettere i livelli di vuoto, influenzando così la qualità del prodotto finale. Il processo di identificazione e correzione di queste perdite richiede tempo e lavoro, sottolineando l'importanza della manutenzione preventiva.
Inoltre, la contaminazione degli interni del forno può derivare da varie fonti, tra cui gas residui e particolato, che possono infiltrarsi nel sistema durante le attività di manutenzione. Tale contaminazione può portare a proprietà incoerenti del film, rendendo necessari protocolli di pulizia e convalida approfonditi per garantire che l'ambiente del vuoto rimanga incontaminato.
Aspetto della manutenzione | Importanza |
---|---|
Integrità della tenuta | Assicura un vuoto senza perdite; è fondamentale per mantenere i livelli di vuoto operativi. |
Giunti di brasatura | Richiedono un'ispezione e una manutenzione regolari per evitare perdite. |
Componenti interni del forno | Devono essere mantenuti liberi da contaminazioni per mantenere la qualità del film. |
In sintesi, la manutenzione dell'ambiente del vuoto è una pietra miliare del processo di sputtering magnetronico, che richiede un'attenzione meticolosa ai dettagli e rigorose misure preventive per garantire la produzione di film di alta qualità.
Controllo della velocità di deposizione
La velocità di deposizione è un parametro critico nel processo di sputtering magnetronico, che influenza in modo significativo sia la qualità che lo spessore del film. La velocità di deposizione determina la velocità con cui il materiale dal target viene trasferito al substrato, influenzando così l'uniformità, la densità e le proprietà finali del film depositato.
Per ottenere risultati ottimali, la velocità di deposizione deve essere controllata meticolosamente e regolata in base a condizioni specifiche. Fattori come il tipo di materiale di destinazione, lo spessore del film desiderato e le proprietà specifiche richieste per l'applicazione giocano tutti un ruolo nel determinare la velocità di deposizione appropriata. Ad esempio, una velocità di deposizione più elevata potrebbe essere adatta per applicazioni che richiedono film più spessi, ma potrebbe anche portare a problemi come scarsa adesione o non uniformità se non gestita correttamente.
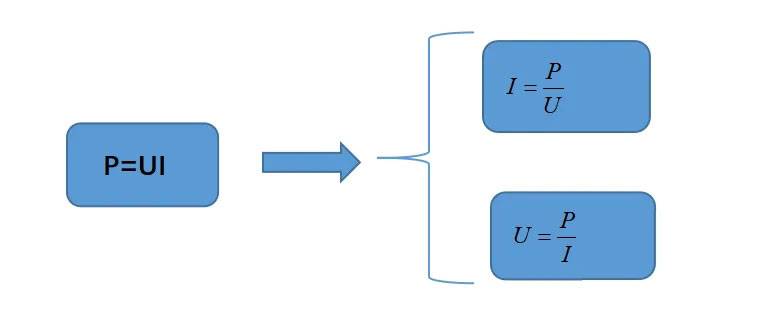
Fattore | Impatto sulla velocità di deposizione |
---|---|
Materiale di destinazione | Materiali diversi hanno rendimenti di sputtering variabili, che influenzano la velocità di deposito. |
Temperatura del substrato | Temperature più elevate possono migliorare l'adesione del film, ma possono anche alterare la velocità di deposizione. |
Potenza di sputtering | L'aumento della potenza determina in genere un tasso di deposizione più elevato, ma deve essere bilanciato con altri parametri. |
In sintesi, il controllo preciso della velocità di deposizione è essenziale per produrre film PZT di alta qualità. Questo controllo assicura che il film non solo soddisfi le specifiche di spessore richieste, ma presenti anche le proprietà desiderate, come la conducibilità elettrica e la resistenza meccanica.
Controllo della potenza e del tempo di sputtering
La potenza e il tempo di sputtering sono parametri critici che influenzano in modo significativo la qualità del film. Questi fattori devono essere regolati meticolosamente per allinearsi alle caratteristiche e ai requisiti specifici del materiale da trattare. Il livello di potenza durante lo sputtering influisce sull'energia impartita al materiale target, che a sua volta determina la velocità con cui gli atomi vengono espulsi e depositati sul substrato. Livelli di potenza più elevati consentono in genere di ottenere tassi di deposizione più rapidi, ma possono anche portare a un aumento del calore e delle sollecitazioni sul substrato, causando potenzialmente difetti o alterando le proprietà desiderate del film.
Al contrario, la durata del processo di sputtering, o tempo di sputtering, influisce direttamente sullo spessore e sull'uniformità del film depositato. Tempi di sputtering prolungati possono produrre film più spessi, ma aumentano anche il rischio di contaminazione e la probabilità di ottenere uno spessore non uniforme sul substrato. Pertanto, è essenziale bilanciare la potenza e il tempo di sputtering per ottenere una qualità ottimale del film.
Per illustrare l'importanza di questi parametri, si consideri la seguente tabella:
Potenza di sputtering (W) | Tempo di sputtering (min) | Spessore del film (nm) | Qualità del film (valutazione 1-10) |
---|---|---|---|
100 | 30 | 200 | 8 |
150 | 20 | 250 | 7 |
200 | 15 | 300 | 6 |
In questo esempio, mentre una potenza più elevata e tempi più brevi consentono di ottenere film più spessi, la qualità del film diminuisce a causa dell'aumento delle sollecitazioni e dei potenziali difetti. Pertanto, la selezione della potenza e del tempo di sputtering appropriati è un processo ricco di sfumature che richiede un'attenta considerazione delle proprietà del materiale e delle caratteristiche del film desiderato.
Materiale target e preparazione della superficie
Selezione del materiale target adatto
La selezione del materiale target è una fase critica del processo di sputtering magnetronico, che influenza in modo significativo la qualità e le prestazioni del film risultante. La scelta del materiale target influisce direttamente sulla composizione chimica, sull'integrità strutturale e sulle proprietà funzionali del film depositato. Pertanto, è essenziale selezionare un materiale di destinazione che sia in linea con i requisiti specifici e i risultati desiderati del film.
Quando si sceglie un materiale di destinazione, si devono considerare diversi fattori:
-
Composizione chimica: Il materiale di destinazione deve corrispondere alla composizione chimica desiderata del film. Ad esempio, nella preparazione di film di zirconato di piombo titanato (PZT), il target dovrebbe essere costituito da una miscela omogenea di ossidi di piombo, zirconio e titanio.
-
Purezza: L'elevata purezza del materiale di destinazione è fondamentale per evitare l'introduzione di impurità nel film, che possono degradarne le proprietà. Eventuali contaminanti possono causare difetti, ridurre la densità del film e influire sulle sue prestazioni complessive.
-
Proprietà fisiche: Le proprietà fisiche del target, come la densità e la conducibilità termica, possono influenzare il processo di sputtering e le caratteristiche del film risultante. Ad esempio, un materiale di destinazione più denso determina in genere un tasso di deposizione più uniforme.
-
Condizione della superficie: La superficie del materiale target deve essere liscia e priva di difetti per garantire uno sputtering efficiente e uniforme. Possono essere necessari trattamenti della superficie per ottenere la planarità e la pulizia richieste.
La tabella seguente riassume le considerazioni chiave per la selezione di un materiale target adatto:
Considerazione | Importanza |
---|---|
Composizione chimica | Assicura le proprietà chimiche desiderate del film. |
Purezza | Previene la contaminazione e mantiene la qualità del film. |
Proprietà fisiche | Influenza l'efficienza dello sputtering e l'uniformità del film. |
Condizione della superficie | Assicura uno sputtering efficiente e uniforme, evitando difetti nel film. |
In sintesi, la scelta del materiale di destinazione è una decisione che presenta molte sfaccettature e richiede un'attenta considerazione di vari fattori per ottenere film di alta qualità e ad alte prestazioni.
Garantire la purezza e la planarità della superficie del target
La purezza e la planarità della superficie del target sono fattori critici che influenzano in modo significativo il processo di sputtering e la qualità del film risultante. Eventuali impurità o irregolarità sulla superficie del target possono portare a incongruenze nella deposizione del film PZT, influenzandone le prestazioni complessive e l'uniformità.
Per garantire risultati ottimali, la superficie del target deve essere sottoposta a rigorosi protocolli di trattamento e ispezione. Ciò comporta:
-
Pulizia della superficie: Eliminazione di eventuali contaminanti come polvere, oli o ossidi che potrebbero compromettere la purezza del target. Vengono comunemente impiegate tecniche come la pulizia a ultrasuoni, l'incisione chimica e la pulizia con fascio ionico.
-
Ispezione della planarità: Utilizzo di strumenti metrologici avanzati come profilometri e interferometri per misurare la topografia della superficie. Eventuali deviazioni dalla planarità desiderata devono essere corrette mediante lucidatura o altre misure correttive.
Trattamento della superficie | Scopo | Tecniche comuni |
---|---|---|
Pulizia della superficie | Rimuovere i contaminanti | Pulizia a ultrasuoni, incisione chimica, pulizia a fascio ionico |
Ispezione della planarità | Verifica dell'uniformità della superficie | Profilometri, interferometri |
Rispettando meticolosamente queste procedure, è possibile garantire la purezza e la planarità della superficie del target, migliorando così la qualità e la consistenza del film PZT prodotto mediante sputtering magnetronico.
Controllo del substrato e dell'ambiente
Controllo della temperatura del substrato
La temperatura del substrato gioca un ruolo fondamentale nel determinare le proprietà finali del film depositato, come la cristallinità, la densità e la rugosità superficiale. Queste proprietà sono fondamentali per le prestazioni e la funzionalità del film, rendendo il controllo preciso della temperatura un aspetto essenziale del processo di sputtering magnetronico.
Quando la temperatura del substrato è troppo bassa, il film può presentare una scarsa cristallinità e una bassa densità, con conseguente aumento della rugosità superficiale. Al contrario, se la temperatura è troppo alta, può causare cambiamenti di fase indesiderati o addirittura danni termici al substrato. Pertanto, la temperatura deve essere regolata meticolosamente in base alle caratteristiche e ai requisiti specifici del materiale da depositare.
Ad esempio, nel caso dei film di zirconato di piombo titanato (PZT), la temperatura ottimale del substrato può variare in modo significativo a seconda della struttura di fase e delle proprietà ferroelettriche desiderate. In genere, per ottenere la fase di perovskite desiderata e la risposta piezoelettrica ottimale, si utilizzano temperature comprese tra 400°C e 600°C.
Per garantire un controllo preciso, i moderni sistemi di sputtering spesso incorporano meccanismi avanzati di monitoraggio e controllo della temperatura, come termometri a infrarossi e regolatori PID. Questi strumenti consentono regolazioni in tempo reale, assicurando che la temperatura del substrato rimanga nell'intervallo ottimale durante l'intero processo di deposizione.
Intervallo di temperatura | Proprietà del film |
---|---|
< 400°C | Scarsa cristallinità, bassa densità, elevata rugosità |
400°C - 600°C | Fase perovskite desiderata, risposta piezoelettrica ottimale |
> 600°C | Possibili cambiamenti di fase, danni termici |
In sintesi, il controllo della temperatura del substrato è un parametro critico nel processo di sputtering magnetronico, che influenza direttamente la qualità e le prestazioni del film depositato. Una corretta gestione della temperatura assicura che il film soddisfi le specifiche richieste e ne migliora la funzionalità complessiva.
Controllo del vuoto e dell'atmosfera
Il processo di sputtering per la preparazione di strati di film di zirconato di piombo (PZT) è molto sensibile alle condizioni ambientali. Per ottenere risultati ottimali, deve essere condotto in un ambiente ad alto vuoto meticolosamente controllato. Questo requisito rigoroso non è negoziabile, poiché ha un impatto diretto sull'integrità e sulle prestazioni del film PZT.
In un ambiente ad alto vuoto, l'assenza di gas atmosferici riduce notevolmente il rischio di contaminazione. Particelle trasportate dall'aria, umidità e altre impurità possono introdurre difetti nel film, compromettendone le proprietà strutturali ed elettriche. Mantenendo il vuoto, questi potenziali contaminanti vengono efficacemente eliminati, garantendo una superficie di deposizione incontaminata.
Inoltre, il controllo delle condizioni atmosferiche va oltre il semplice mantenimento del vuoto. Si tratta anche di prevenire l'ossidazione, che può alterare la composizione chimica del film di PZT. L'ossidazione può portare a variazioni nella stechiometria del film, influenzando le sue proprietà ferroelettriche e piezoelettriche. Pertanto, il mantenimento di un'atmosfera controllata è fondamentale per preservare le caratteristiche chimiche e fisiche desiderate del film PZT.
Per ottenere e mantenere questo ambiente ad alto vuoto, vengono impiegati sistemi di vuoto avanzati. Questi sistemi comprendono pompe ad alta efficienza, rilevatori di perdite e sensori di pressione che lavorano in tandem per mantenere il livello di vuoto richiesto. Il monitoraggio e la calibrazione regolari di questi sistemi sono essenziali per garantire un controllo del vuoto continuo e affidabile.
In sintesi, il controllo del vuoto e dell'atmosfera è un aspetto critico del processo di sputtering magnetronico per la preparazione di film PZT. Non solo protegge dalla contaminazione e dall'ossidazione, ma assicura anche la consistenza e la qualità del film depositato. Questo controllo meticoloso è una pietra miliare dell'intero processo, alla base del successo della fabbricazione di film PZT ad alte prestazioni.
Controllo dell'uniformità
L'uniformità è una proprietà critica dei film sottili, in particolare nel contesto della preparazione di film di piombo zirconato titanato (PZT) mediante sputtering magnetronico. Il raggiungimento di una deposizione uniforme del film è essenziale per garantire prestazioni e affidabilità costanti sull'intero substrato. Questa uniformità è gestita principalmente attraverso un controllo meticoloso del processo di sputtering, che coinvolge diversi parametri e tecniche chiave.
In primo luogo, il posizionamento e l'orientamento della sorgente di sputtering e del substrato svolgono un ruolo fondamentale per ottenere una deposizione uniforme del film. La sorgente di sputtering, in genere un materiale target, deve essere posizionata a una distanza ottimale dal substrato per garantire che gli atomi o le particelle espulse dal target siano distribuiti uniformemente sulla superficie. Inoltre, l'angolo con cui le particelle raggiungono il substrato deve essere attentamente controllato per evitare qualsiasi distorsione direzionale nel processo di deposizione.
In secondo luogo, l'impiego di tecniche avanzate come la rotazione del substrato può migliorare notevolmente l'uniformità. Ruotando il substrato durante il processo di sputtering, la deposizione del film si distribuisce in modo più uniforme, attenuando gli effetti di eventuali variazioni localizzate nell'uscita della sorgente di sputtering. Questo metodo garantisce che ogni parte del substrato riceva una quantità costante di materiale, con il risultato di un film finale più uniforme.
Parametro di controllo | Impatto sull'uniformità |
---|---|
Posizione della sorgente di sputtering | Assicura una distribuzione uniforme delle particelle |
Angolo del substrato | Previene le distorsioni direzionali nella deposizione |
Rotazione del substrato | Migliora la distribuzione uniforme del materiale |
In sintesi, il raggiungimento dell'uniformità nella deposizione di film sottili richiede una combinazione di controllo preciso della sorgente di sputtering e del substrato, nonché l'uso strategico di tecniche come la rotazione del substrato. Queste misure contribuiscono collettivamente alla produzione di film PZT uniformi e di alta qualità, essenziali per le applicazioni previste.
Monitoraggio del processo e post-trattamento
Monitoraggio e regolazione della potenza di sputtering
La potenza di sputtering è un parametro critico nel processo di sputtering magnetronico, che influenza in modo significativo lo spessore e la composizione del film depositato. Il livello di potenza influisce direttamente sull'energia degli ioni che bombardano il materiale target, che a sua volta determina la velocità con cui il materiale viene espulso e depositato sul substrato. Ad esempio, una potenza di sputtering più elevata determina in genere una velocità di deposizione più elevata, ma può anche portare a un aumento della rugosità e della non uniformità del film se non viene gestita correttamente.
Per garantire una qualità ottimale del film, è essenziale monitorare e regolare dinamicamente la potenza di sputtering. Ciò comporta l'utilizzo di sistemi di monitoraggio avanzati in grado di fornire dati in tempo reale sui livelli di potenza, sui tassi di deposizione e sulle proprietà del film. Correlando queste metriche, gli operatori possono regolare con precisione la potenza di sputtering per ottenere le caratteristiche del film desiderate. Ad esempio, se lo spessore del film si discosta dall'obiettivo, la potenza di sputtering può essere regolata per compensare, garantendo uno spessore uniforme dello strato sul substrato.
Inoltre, la composizione del film può essere influenzata dalla potenza di sputtering. Livelli di potenza diversi possono causare gradi diversi di sputtering da elementi diversi all'interno di un target multicomponente, con conseguenti cambiamenti nella stechiometria del film. Pertanto, è necessario un controllo preciso della potenza di sputtering per mantenere la composizione chimica desiderata del film. Ciò è particolarmente importante nella preparazione di film di ossidi complessi come il piombo zirconato titanato (PZT), dove il mantenimento del corretto rapporto tra piombo, zirconio e titanio è fondamentale per ottenere le proprietà elettriche e meccaniche desiderate.
In sintesi, il monitoraggio e la regolazione della potenza di sputtering non riguardano solo il controllo della velocità di deposizione, ma anche il raggiungimento del giusto equilibrio tra spessore, uniformità e composizione del film. Questo controllo dinamico assicura che il prodotto finale soddisfi i severi requisiti per le applicazioni in elettronica, ottica e altri settori ad alta tecnologia.
Post-trattamento dei film
I processi di post-trattamento sono fasi cruciali nella preparazione dei film di piombo zirconato titanato (PZT), finalizzati a migliorarne le proprietà e a garantirne la stabilità a lungo termine. Questi trattamenti includono spessoricottura eossidazioneche hanno lo scopo di affinare la microstruttura del film e migliorarne le caratteristiche meccaniche ed elettriche.
Ricottura
La ricottura consiste nel riscaldare il film a una temperatura specifica e nel raffreddarlo lentamente. Questo processo può:
- migliorare la cristallinità: Promuovendo la crescita di cristalli più grandi e uniformi, la ricottura può migliorare significativamente l'integrità strutturale del film.
- Ridurre lo stress: Le tensioni interne al film possono essere attenuate, rendendo il materiale più stabile e duraturo.
- Migliorare le proprietà elettriche: La costante dielettrica e le proprietà ferroelettriche del film possono essere ottimizzate attraverso una ricottura controllata.
Ossidazione
L'ossidazione del film comporta l'esposizione a un ambiente ricco di ossigeno, che può:
- stabilizzare lo strato di ossido: Assicurare che lo strato di ossido superficiale del film sia uniforme e stabile può prevenire problemi come la delaminazione e la degradazione nel tempo.
- Migliorare la resistenza chimica: Una superficie ossidata è meno suscettibile agli attacchi chimici, rendendo il film più robusto in vari ambienti.
- Controllo della rugosità della superficie: L'ossidazione può contribuire ad attenuare eventuali irregolarità sulla superficie del film, migliorandone la qualità complessiva e le prestazioni.
Sia la ricottura che l'ossidazione sono fondamentali nel post-trattamento, in quanto non solo risolvono problemi immediati di qualità, ma contribuiscono anche alle prestazioni e all'affidabilità a lungo termine del film.
Controllo qualità e test
I film preparati sono sottoposti a un rigoroso controllo di qualità e a test per garantire che soddisfino i severi requisiti necessari per le applicazioni previste. Questo processo coinvolge molteplici aspetti, ognuno dei quali viene valutato meticolosamente per garantire l'integrità e le prestazioni dei film.
Parametri chiave per il controllo di qualità
-
Morfologia della superficie: La superficie del film viene esaminata con microscopi ad alta risoluzione per individuare eventuali difetti come crepe, fori di spillo o irregolarità. Questa fase è fondamentale perché le imperfezioni della superficie possono avere un impatto significativo sulla funzionalità del film.
-
Misurazione dello spessore: Lo spessore del film viene misurato con strumenti di precisione come ellissometri o profilometri. La coerenza dello spessore è essenziale per ottenere proprietà elettriche e meccaniche uniformi su tutto il film.
-
Analisi della composizione: La composizione chimica del film viene analizzata con tecniche quali la diffrazione dei raggi X (XRD) e la spettroscopia a raggi X a dispersione di energia (EDS). In questo modo si garantisce che la composizione del film corrisponda alla stechiometria desiderata, che è fondamentale per l'uso previsto.
-
Proprietà elettriche: I test elettrici, che comprendono misure di resistività, capacità e costante dielettrica, vengono eseguiti per valutare le prestazioni del film nelle applicazioni elettriche. Queste proprietà sono direttamente influenzate dalla struttura e dalla composizione del film.
Metodi e strumenti di prova
Parametro | Metodo di prova | Strumento utilizzato |
---|---|---|
Morfologia della superficie | Microscopia | Microscopio elettronico a scansione (SEM) |
Misura dello spessore | Tecniche ottiche e meccaniche | Ellissometro, profilometro |
Analisi della composizione | Tecniche spettroscopiche | Diffrazione dei raggi X (XRD), EDS |
Proprietà elettriche | Misure elettriche | Misuratore LCR, analizzatore di impedenza |
Valutando sistematicamente questi parametri, il processo di controllo della qualità assicura che ogni film soddisfi gli standard predefiniti, garantendo così l'affidabilità e le prestazioni del prodotto finale.
Miglioramento continuo e considerazioni ambientali
Miglioramento continuo e ottimizzazione
La preparazione dei film sottili è un processo iterativo che richiede un controllo e un perfezionamento continui per ottenere risultati ottimali. Il processo di preparazione, dall'impostazione iniziale al prodotto finale, richiede un'analisi e un miglioramento meticolosi per migliorare sia la qualità che l'efficienza del film. Questo continuo perfezionamento coinvolge diversi aspetti chiave:
-
Monitoraggio dei parametri di processo: È essenziale monitorare e regolare regolarmente i parametri critici come la potenza di sputtering, la velocità di deposizione e la temperatura del substrato. Questi parametri influenzano in modo significativo le proprietà del film, tra cui lo spessore, l'uniformità e la qualità complessiva.
-
Aggiornamenti tecnologici: L'incorporazione di tecnologie e metodologie avanzate può portare a miglioramenti sostanziali. Ad esempio, l'uso di sistemi automatizzati per il monitoraggio e il controllo in tempo reale può ridurre l'errore umano e migliorare la coerenza del processo.
-
Controllo qualità: Sono indispensabili misure rigorose di controllo della qualità. Ciò include test completi della morfologia superficiale, dello spessore, della composizione e delle proprietà elettriche del film, per garantire che sia conforme agli standard richiesti.
-
Cicli di feedback: La creazione di cicli di feedback efficaci consente di identificare e correggere rapidamente eventuali deviazioni dai risultati desiderati. Questo approccio iterativo garantisce che ogni ciclo di preparazione del film sia migliore del precedente.
-
Considerazioni ambientali: Oltre a migliorare la qualità della pellicola, è fondamentale considerare anche l'impatto ambientale del processo di preparazione. L'adozione di metodi efficienti dal punto di vista energetico e la riduzione al minimo degli scarti possono contribuire a un ciclo di produzione più sostenibile.
Analizzando e perfezionando continuamente questi aspetti, il processo di preparazione può essere ottimizzato per ottenere film di alta qualità con una maggiore efficienza e un'impronta ambientale ridotta.
Protezione ambientale e consumo energetico
Nella ricerca di pratiche sostenibili all'interno del processo di sputtering magnetronico, è necessario porre particolare attenzione alla protezione dell'ambiente e al consumo energetico. I metodi tradizionali di sputtering, pur essendo efficaci, spesso comportano notevoli svantaggi ambientali ed energetici. Per attenuarli, l'adozione di tecniche di preparazione più ecologiche ed efficienti dal punto di vista energetico non è solo una raccomandazione, ma una necessità.
Un approccio per raggiungere questo obiettivo è l'ottimizzazione dei parametri di sputtering. Regolando con precisione fattori come la potenza di sputtering, la velocità di deposizione e la temperatura del substrato, è possibile ridurre l'impronta energetica complessiva del processo. Ad esempio, è possibile utilizzare potenze di sputtering più basse senza compromettere la qualità del film, risparmiando così energia. Inoltre, l'uso di tecnologie avanzate per il vuoto può contribuire a mantenere un ambiente più pulito, riducendo al minimo il rilascio di gas e particolati nocivi nell'atmosfera.
Inoltre, la selezione dei materiali gioca un ruolo cruciale nella sostenibilità ambientale. La scelta di materiali meno tossici e con un minore impatto ambientale può migliorare significativamente l'ecocompatibilità del processo. Questo non solo protegge l'ambiente, ma garantisce anche la conformità a normative ambientali sempre più severe.
In sintesi, se l'attenzione principale dello sputtering magnetronico è rivolta alla qualità e alle prestazioni del film PZT, l'integrazione di considerazioni ambientali ed energetiche nel processo di preparazione è altrettanto importante. Questo approccio olistico garantisce che i progressi nella tecnologia dei film siano allineati con gli obiettivi più ampi di gestione ambientale e sostenibilità.
CONTATTATECI PER UNA CONSULENZA GRATUITA
I prodotti e i servizi di KINTEK LAB SOLUTION sono stati riconosciuti da clienti di tutto il mondo. Il nostro personale sarà lieto di assistervi per qualsiasi richiesta. Contattateci per una consulenza gratuita e parlate con uno specialista del prodotto per trovare la soluzione più adatta alle vostre esigenze applicative!