Il processo di trattamento termico è una fase critica della metallurgia, che influenza in modo significativo le proprietà e le prestazioni dei componenti metallici. Il successo di questo processo dipende da diversi fattori chiave, tra cui il controllo della temperatura, la gestione del tempo, la velocità di raffreddamento e le condizioni ambientali. Queste variabili devono essere attentamente regolate in base al tipo di materiale, alle proprietà desiderate e all'applicazione finale del pezzo. Inoltre, la distribuzione uniforme della temperatura, la corretta circolazione dei gas e l'ottimizzazione del ciclo sono essenziali per garantire risultati di alta qualità. Anticipare i potenziali problemi e mantenere un controllo preciso sul processo può prevenire i difetti, ridurre i tempi di fermo e migliorare l'efficienza complessiva del trattamento termico.
Punti chiave spiegati:
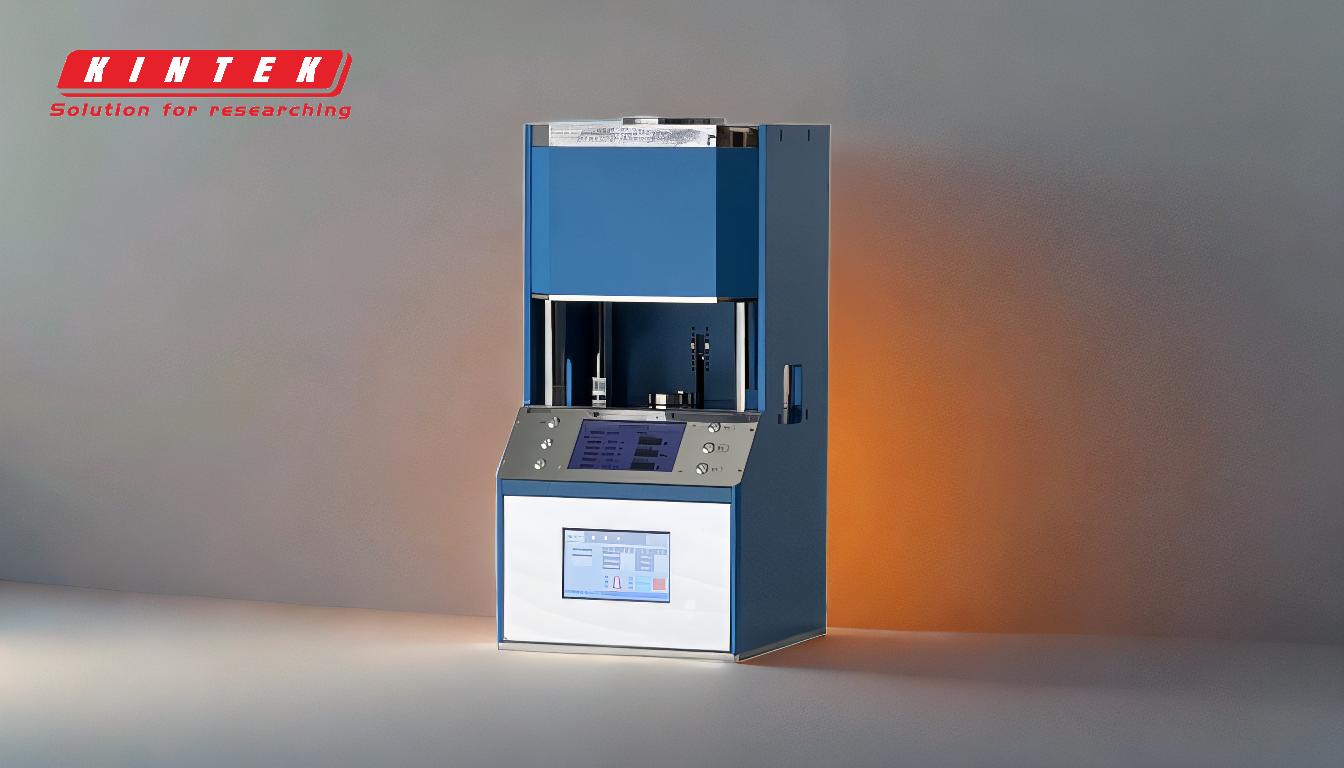
-
Controllo della temperatura:
- Importanza: La temperatura è uno dei fattori più critici nel trattamento termico. Determina le trasformazioni di fase nel metallo, che influiscono direttamente sulle sue proprietà meccaniche.
- Dettagli: Il metallo deve essere riscaldato a un intervallo di temperatura specifico, spesso con tolleranze ristrette, per ottenere la microstruttura desiderata. Il superamento o la riduzione di questo intervallo può portare a un indurimento inadeguato, a un rammollimento o addirittura a una cricca.
- Considerazioni: La temperatura massima, la velocità di riscaldamento e la velocità di raffreddamento devono essere attentamente controllate per evitare difetti metallurgici e garantire una trasformazione uniforme.
-
Tempo alla temperatura:
- Importanza: La durata della permanenza del metallo alla temperatura target influenza l'entità della trasformazione di fase e i processi di diffusione.
- Dettagli: Mantenere il metallo alla temperatura desiderata consente un riscaldamento uniforme e garantisce che l'intero pezzo raggiunga lo stato necessario. Un tempo insufficiente può causare una trasformazione incompleta, mentre un tempo eccessivo può portare alla crescita dei grani o ad altri effetti indesiderati.
- Considerazioni: Il tempo di permanenza in temperatura deve essere ottimizzato in base al tipo di materiale, alle dimensioni del pezzo e alle proprietà desiderate.
-
Velocità e metodo di raffreddamento:
- Importanza: La velocità di raffreddamento determina la microstruttura finale e la durezza del metallo.
- Dettagli: Il raffreddamento rapido (tempra) è spesso utilizzato per ottenere un'elevata durezza, mentre il raffreddamento più lento (ricottura) è impiegato per ammorbidire il metallo e migliorare la duttilità. La scelta del mezzo di raffreddamento (aria, olio, acqua o gas) e la velocità di raffreddamento devono essere adattate al materiale e al risultato desiderato.
- Considerazioni: Un raffreddamento non corretto può causare distorsioni, tensioni residue o cricche. Un controllo preciso del processo di raffreddamento è essenziale per ottenere le proprietà meccaniche desiderate.
-
Tipo di materiale e dimensioni del pezzo:
- Importanza: Materiali e dimensioni diverse richiedono parametri di trattamento termico specifici per ottenere risultati ottimali.
- Dettagli: Ad esempio, gli acciai al carbonio, gli acciai legati e i metalli non ferrosi hanno requisiti di trattamento termico specifici. I pezzi più grandi possono richiedere tempi di riscaldamento più lunghi per garantire una distribuzione uniforme della temperatura.
- Considerazioni: Il processo di trattamento termico deve essere personalizzato in base alla composizione del materiale, alla geometria del pezzo e all'applicazione prevista.
-
Distribuzione uniforme della temperatura:
- Importanza: Un riscaldamento uniforme garantisce proprietà costanti in tutto il pezzo.
- Dettagli: Le zone calde del forno devono mantenere una temperatura costante per evitare trasformazioni non uniformi. Le variazioni di temperatura possono causare punti deboli, deformazioni o altri difetti.
- Considerazioni: Un'adeguata progettazione del forno, l'isolamento e i sistemi di distribuzione del calore sono fondamentali per ottenere un riscaldamento uniforme.
-
Circolazione del gas e controllo dell'atmosfera:
- Importanza: L'atmosfera del forno può influenzare la chimica superficiale e le proprietà del metallo.
- Dettagli: In processi come la carburazione o la nitrurazione, la composizione del gas (ad esempio, la pressione parziale del carbonio o dell'azoto) deve essere controllata con precisione per ottenere la durezza superficiale e la profondità del bossolo desiderate. Per evitare l'ossidazione o la decarburazione si possono utilizzare gas inerti.
- Considerazioni: Una corretta circolazione dei gas assicura risultati costanti e previene la contaminazione o i difetti superficiali.
-
Ottimizzazione del ciclo:
- Importanza: Cicli di trattamento termico efficienti riducono il consumo di energia e i tempi di lavorazione, mantenendo la qualità.
- Dettagli: Bilanciare i tempi di riscaldamento, mantenimento e raffreddamento è essenziale per ridurre al minimo la durata del processo senza compromettere i risultati metallurgici. I sistemi di controllo avanzati possono ottimizzare i cicli in base ai dati in tempo reale.
- Considerazioni: Anticipare potenziali problemi, come malfunzionamenti delle apparecchiature o deviazioni del processo, può evitare costosi tempi di inattività e garantire una qualità costante.
-
Requisiti dell'applicazione finale e della proprietà:
- Importanza: Il processo di trattamento termico deve essere in linea con l'uso previsto del pezzo e con i requisiti di prestazione.
- Dettagli: Ad esempio, un pezzo che richiede un'elevata resistenza all'usura può essere sottoposto a tempra e rinvenimento, mentre un pezzo che necessita di una migliore lavorabilità può essere ricotto. Il trattamento termico localizzato può essere applicato a zone specifiche di un pezzo per ottenere proprietà mirate.
- Considerazioni: La comprensione dell'applicazione finale aiuta a selezionare il metodo e i parametri di trattamento termico appropriati.
-
Manutenzione e prevenzione dei tempi morti:
- Importanza: Una manutenzione regolare e il monitoraggio del processo possono prevenire i difetti e ridurre i tempi di inattività.
- Dettagli: Anticipare potenziali problemi, come malfunzionamenti dei forni o perdite di gas, garantisce una produzione ininterrotta. Le strategie di manutenzione predittiva possono identificare i problemi prima che si aggravino.
- Considerazioni: Investire in attrezzature affidabili e formare il personale per monitorare e mantenere il processo di trattamento termico può migliorare l'efficienza complessiva e la qualità del prodotto.
Considerando attentamente questi fattori, i produttori possono ottimizzare il processo di trattamento termico per ottenere le proprietà desiderate del materiale, migliorare le prestazioni del prodotto e ridurre i costi.
Tabella riassuntiva:
Fattore chiave | Importanza | Dettagli |
---|---|---|
Controllo della temperatura | Determina le trasformazioni di fase e le proprietà meccaniche. | Richiede un riscaldamento preciso entro tolleranze ristrette per evitare difetti come cricche o rammollimenti. |
Tempo alla temperatura | Influenza i processi di trasformazione di fase e di diffusione. | Deve essere ottimizzato in base al tipo di materiale, alle dimensioni del pezzo e alle proprietà desiderate. |
Velocità e metodo di raffreddamento | Determina la microstruttura e la durezza finali. | Raffreddamento rapido (tempra) per la durezza; raffreddamento più lento (ricottura) per la duttilità. |
Tipo di materiale e dimensioni del pezzo | Materiali e dimensioni diverse richiedono parametri specifici. | Personalizzare il processo in base alla composizione, alla geometria e all'applicazione. |
Distribuzione uniforme della temperatura | Assicura proprietà uniformi in tutto il pezzo. | Un'adeguata progettazione del forno e la distribuzione del calore impediscono una trasformazione non uniforme. |
Circolazione del gas e controllo dell'atmosfera | Influenza la chimica superficiale e le proprietà. | Una precisa composizione del gas impedisce l'ossidazione o la contaminazione. |
Ottimizzazione del ciclo | Riduce il consumo di energia e i tempi di lavorazione. | I sistemi di controllo avanzati ottimizzano i cicli di riscaldamento, mantenimento e raffreddamento. |
Requisiti dell'applicazione finale e delle proprietà | Allinea il processo alle esigenze di prestazione del pezzo. | Tempra per la resistenza all'usura; ricottura per la lavorabilità. |
Manutenzione e prevenzione dei tempi morti | Previene i difetti e riduce i tempi di fermo. | Le strategie di manutenzione predittiva assicurano una produzione ininterrotta. |
Ottimizzate il vostro processo di trattamento termico oggi stesso contattate i nostri esperti per soluzioni su misura!