La porosità nella metallurgia delle polveri è un fattore critico che influisce sulle proprietà meccaniche e sulle prestazioni del prodotto finale.La riduzione della porosità può essere ottenuta ottimizzando diversi parametri chiave durante il processo di produzione.Questi includono l'aumento della pressione di compattazione, della temperatura di sinterizzazione e del tempo di sinterizzazione, che collettivamente contribuiscono a ridurre la porosità apparente e ad aumentare la densità apparente.Inoltre, il controllo delle dimensioni delle particelle è fondamentale, poiché le particelle più grandi tendono ad aumentare la porosità.Gestendo attentamente questi fattori, i produttori possono produrre componenti ad alta densità e bassa porosità con proprietà meccaniche migliori.
Spiegazione dei punti chiave:
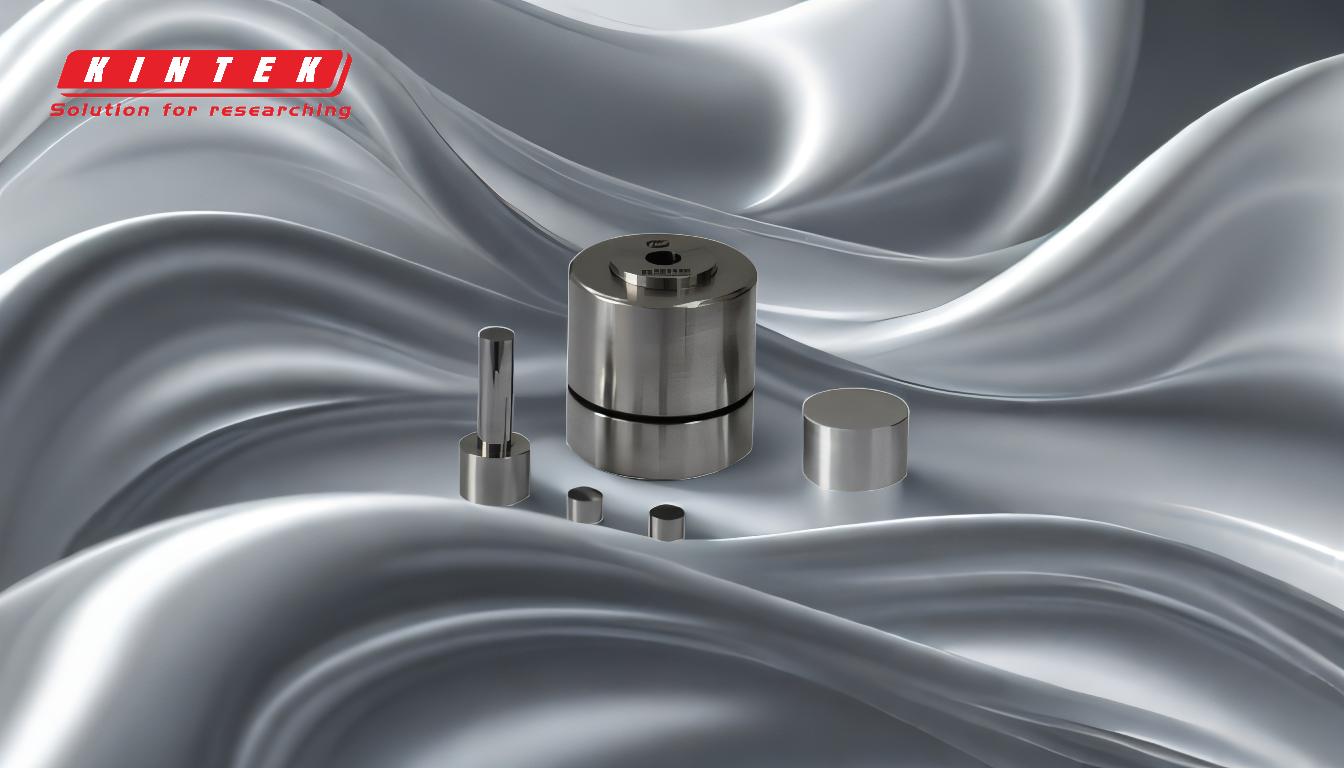
-
Aumento della pressione di compattazione:
- Impatto:Una maggiore pressione di compattazione riduce gli spazi tra le particelle di polvere, determinando un compatto più denso con una minore porosità.
- Meccanismo:Quando si applica la pressione durante la fase di compattazione, le particelle sono costrette ad avvicinarsi l'una all'altra, riducendo al minimo i vuoti e aumentando la densità apparente del compattato verde.
- Considerazioni pratiche:Sebbene una pressione più elevata sia vantaggiosa, deve essere bilanciata con il rischio di danneggiare lo stampo o di causare una distribuzione non uniforme della densità nel pezzo.
-
Ottimizzazione della temperatura e del tempo di sinterizzazione:
- Impatto:Temperature di sinterizzazione più elevate e tempi di sinterizzazione più lunghi favoriscono un migliore legame e diffusione delle particelle, riducendo la porosità e aumentando la densità.
- Meccanismo:La sinterizzazione comporta il riscaldamento della polvere compattata al di sotto del suo punto di fusione, consentendo agli atomi di diffondere attraverso i confini delle particelle, chiudendo i pori e rafforzando il materiale.
- Considerazioni pratiche:Una temperatura o un tempo eccessivi possono portare alla crescita o alla distorsione dei grani, pertanto è necessaria un'attenta ottimizzazione.
-
Controllo della dimensione delle particelle:
- Impatto:Le dimensioni delle particelle più piccole comportano generalmente una minore porosità perché si impacchettano in modo più efficiente, lasciando meno vuoti.
- Meccanismo:Le particelle fini hanno un rapporto superficie/volume più elevato, che favorisce la sinterizzazione e l'adesione.Le particelle più grandi, invece, creano più spazi vuoti e aumentano la porosità.
- Considerazioni pratiche:Sebbene le particelle più piccole siano preferibili, possono anche aumentare il rischio di agglomerazione, che deve essere gestito durante la lavorazione.
-
Metodi di produzione della polvere:
- Impatto:Il metodo utilizzato per produrre le polveri metalliche ne influenza le dimensioni, la forma e la distribuzione, che a loro volta influiscono sulla porosità.
- Meccanismo:Tecniche come l'atomizzazione producono polveri di dimensioni controllate, che possono essere adattate per ridurre al minimo la porosità.La frantumazione e la macinazione possono produrre particelle di forma irregolare che si impacchettano in modo meno efficiente.
- Considerazioni pratiche:La scelta del metodo di produzione delle polveri è essenziale per ottenere le caratteristiche desiderate delle particelle e ridurre al minimo la porosità.
-
Selezione del materiale:
- Impatto:La scelta del materiale di base (ad esempio, rame-base o ferro-base) può influenzare la porosità a causa delle differenze di forma, dimensione e comportamento di sinterizzazione delle particelle.
- Meccanismo:Alcuni materiali si sinterizzano più facilmente di altri, determinando una migliore densificazione e una minore porosità.
- Considerazioni pratiche:La scelta del materiale deve essere in linea con l'applicazione prevista e le proprietà meccaniche desiderate.
Prendendo in considerazione questi fattori chiave, i produttori possono ridurre efficacemente la porosità nella metallurgia delle polveri, ottenendo componenti con resistenza, durata e prestazioni migliori.
Tabella riassuntiva:
Fattore chiave | Impatto | Meccanismo | Considerazioni pratiche |
---|---|---|---|
Aumento della pressione di compattazione | Riduce gli spazi vuoti tra le particelle, dando luogo a compatti più densi e con minore porosità. | La pressione costringe le particelle ad avvicinarsi, riducendo al minimo i vuoti e aumentando la densità di massa. | Bilanciare la pressione per evitare danni allo stampo o una distribuzione non uniforme della densità. |
Ottimizzazione della temperatura e del tempo di sinterizzazione | Promuove il legame tra le particelle, riduce la porosità e aumenta la densità. | Il riscaldamento al di sotto del punto di fusione consente la diffusione degli atomi, chiudendo i pori e rafforzando il materiale. | Evitare temperature o tempi eccessivi per evitare la crescita o la distorsione dei grani. |
Controllo della dimensione delle particelle | Le particelle più piccole si impacchettano in modo efficiente, riducendo la porosità. | Le particelle fini hanno un rapporto superficie/volume più elevato, che favorisce la sinterizzazione e l'adesione. | Gestire i rischi di agglomerazione con particelle più piccole. |
Metodi di produzione della polvere | Influenza la dimensione, la forma e la distribuzione delle particelle, influenzando la porosità. | L'atomizzazione produce gamme di dimensioni controllate; la frantumazione/macinazione può creare particelle irregolari. | Selezionare il metodo giusto per ottenere le caratteristiche desiderate delle particelle. |
Selezione del materiale | Il materiale di base influisce sulla porosità a causa delle differenze nel comportamento di sinterizzazione. | Alcuni materiali sinterizzano più facilmente, determinando una migliore densificazione e una minore porosità. | Allineate la scelta del materiale all'applicazione e alle proprietà meccaniche desiderate. |
Siete pronti a ottimizzare il vostro processo di metallurgia delle polveri? Contattate oggi stesso i nostri esperti per soluzioni su misura!