Introduzione ai forni sottovuoto per molibdeno
I forni a vuoto per molibdenosono fondamentali nelle applicazioni ad alta temperatura e sfruttano le proprietà uniche del molibdeno per eccellere in ambienti difficili. Questi sistemi avanzati non sono solo essenziali per la sinterizzazione in atmosfera ad alta temperatura, ma anche per la sinterizzazione sottovuoto di vari materiali, dimostrando la loro versatilità e il ruolo critico nei moderni processi industriali. Questo articolo approfondisce le caratteristiche complesse, la costruzione e le applicazioni dei forni a vuoto per molibdeno, fornendo approfondimenti sui loro sistemi di controllo avanzati e sulle strategie di manutenzione, essenziali per garantire prestazioni ottimali e lunga durata.
Caratteristiche e scopi principali dei forni a vuoto per molibdeno
I forni sottovuoto per molibdeno sono apparecchiature specializzate progettate per la lavorazione ad alta temperatura in un ambiente controllato e sottovuoto. Questi forni sono particolarmente rinomati per il loro utilizzo nella sinterizzazione in atmosfera ad alta temperatura e nella sinterizzazione sotto vuoto di vari materiali, tra cui ceramiche, metalli e compositi. Le proprietà uniche del molibdeno, come l'elevato punto di fusione, l'eccellente conduttività termica e la resistenza agli shock termici, lo rendono un materiale ideale per gli elementi riscaldanti di questi forni.
Stabilità ed efficienza alle alte temperature
Una delle caratteristiche principali dei forni sottovuoto al molibdeno è la capacità di mantenere la stabilità alle alte temperature. Il molibdeno può operare a temperature fino a 1700°C, il che è fondamentale per processi come la sinterizzazione in cui è essenziale un controllo preciso della temperatura. L'elevata conducibilità termica del molibdeno assicura un trasferimento di calore efficiente, consentendo un riscaldamento rapido e una distribuzione uniforme della temperatura all'interno della camera del forno. Questa efficienza è particolarmente importante nelle applicazioni industriali, dove i tempi e i costi energetici sono fattori significativi.
Prestazioni sotto vuoto e controllo della contaminazione
I forni sottovuoto per molibdeno sono progettati per funzionare in un'atmosfera sottovuoto o controllata, essenziale per evitare la contaminazione dei materiali da lavorare. L'ambiente sottovuoto elimina la presenza di ossigeno e altri gas che potrebbero reagire con i materiali ad alte temperature, preservandone la purezza e l'integrità. Questa caratteristica è particolarmente vantaggiosa nella lavorazione di materiali di elevata purezza e nelle applicazioni in cui i livelli di contaminazione in tracce devono essere ridotti al minimo.
Versatilità nelle applicazioni
La versatilità dei forni sottovuoto per molibdeno si estende a un'ampia gamma di applicazioni oltre alla sinterizzazione. Tra queste, il trattamento termico, la brasatura, la ricottura e la lavorazione di materiali avanzati come la ceramica trasparente e i compositi a matrice metallica. Ognuna di queste applicazioni trae vantaggio dal controllo preciso della temperatura e dall'ambiente privo di contaminazione fornito dal forno.
Componenti strutturali e design
Il design di un forno a vuoto per molibdeno comprende diversi componenti chiave che ne garantiscono la funzionalità e l'efficienza. Questi includono:
- Corpo e coperchio del forno: Costruiti in acciaio inossidabile di alta qualità, il corpo e il coperchio del forno sono progettati per mantenere un vuoto elevato e sono spesso raffreddati ad acqua per gestire le alte temperature.
- Elementi di riscaldamento: Realizzati in molibdeno di elevata purezza, questi elementi sono fondamentali per raggiungere e mantenere le temperature richieste.
- Schermi isolanti: Sono utilizzati per ridurre al minimo le perdite di calore e garantire una distribuzione uniforme della temperatura all'interno della camera del forno.
- Sistema del vuoto: Composto da pompe, valvole e manometri, il sistema del vuoto è essenziale per mantenere l'ambiente sotto vuoto e controllare l'atmosfera all'interno del forno.
- Sistema di controllo: Sistemi di controllo avanzati, spesso con interfacce PLC e computer, consentono un controllo preciso dei parametri del forno, garantendo riproducibilità e sicurezza di funzionamento.
Manutenzione e precauzioni
Sebbene i forni sottovuoto per molibdeno offrano numerosi vantaggi, richiedono anche una manutenzione e un funzionamento accurati per garantire la longevità e le prestazioni. Il molibdeno è sensibile all'ossidazione e alla contaminazione, pertanto i forni devono funzionare in condizioni strettamente controllate. La manutenzione regolare, compresa l'ispezione e la sostituzione degli elementi riscaldanti e delle guarnizioni, è fondamentale per prevenire i guasti e garantire il funzionamento del forno al massimo dell'efficienza.
In conclusione, i forni sottovuoto per molibdeno sono strumenti indispensabili nella lavorazione ad alta temperatura, in quanto offrono stabilità alle alte temperature, trasferimento di calore efficiente e un ambiente privo di contaminazione. La loro versatilità e precisione li rende un componente chiave per il progresso della scienza dei materiali e delle tecnologie di lavorazione industriale.
Costruzione e composizione dei forni a vuoto per molibdeno
I forni a vuoto per molibdeno sono apparecchiature sofisticate progettate per applicazioni ad alta temperatura sotto vuoto o in atmosfera controllata. Questi forni sono fondamentali per processi come la sinterizzazione, il trattamento termico e la brasatura, in cui è essenziale mantenere un ambiente incontaminato. La costruzione di questi forni coinvolge diversi componenti chiave, ognuno dei quali è progettato per funzionare perfettamente in condizioni estreme.
Componenti strutturali
Corpo e coperchio del forno: Il corpo del forno è generalmente costruito in acciaio inossidabile, noto per la sua resistenza alla corrosione e alla deformazione ad alta temperatura. I gusci interni ed esterni sono spesso realizzati in acciaio inox 304, con la superficie esterna lucidata a specchio per migliorare la durata e l'estetica. Il coperchio, che è rimovibile, include un meccanismo di raffreddamento ad acqua nella sua sezione centrale per evitare il surriscaldamento e garantire una tenuta ermetica quando è chiuso.
Fondo e sistema di aspirazione: Il fondo del forno, simile al coperchio, incorpora il raffreddamento ad acqua e presenta porte per elettrodi, termocoppie e altri strumenti di monitoraggio. Il sistema del vuoto è parte integrante del funzionamento del forno e consiste in una combinazione di pompe del vuoto, valvole e manometri. Questi componenti lavorano insieme per raggiungere e mantenere i livelli di vuoto necessari, fondamentali per prevenire l'ossidazione e la contaminazione dei materiali in lavorazione.
Elementi di riscaldamento e schermo isolante: Il cuore del forno è costituito dagli elementi riscaldanti, spesso realizzati in molibdeno di elevata purezza. Il molibdeno è scelto per la sua eccellente resistenza alle alte temperature e per la sua capacità di mantenere l'integrità strutturale fino a 1700°C. Gli elementi riscaldanti sono progettati per funzionare ad alte densità di potenza, garantendo un riscaldamento rapido e uniforme. Lo schermo isolante, tipicamente realizzato con materiali come il tungsteno e l'acciaio inossidabile, contribuisce a mantenere la temperatura all'interno del forno e a ridurre la perdita di calore.
Considerazioni operative
Sistemi di movimentazione e controllo dei materiali: I forni sottovuoto per molibdeno sono dotati di sistemi di controllo avanzati che consentono una gestione precisa della temperatura e il controllo del processo. Questi sistemi possono essere automatizzati, utilizzando interfacce PLC e touch screen, consentendo agli operatori di monitorare e regolare i parametri in tempo reale. L'inclusione del controllo computerizzato non solo migliora l'efficienza, ma garantisce anche la ripetibilità e la sicurezza dei processi ad alta temperatura.
Caratteristiche di raffreddamento e sicurezza: Date le elevate temperature operative, i sistemi di raffreddamento sono fondamentali per la longevità dei componenti del forno. Le camicie raffreddate ad acqua attorno al corpo del forno, al coperchio e al fondo aiutano a dissipare il calore e a prevenire danni strutturali. Per proteggere l'apparecchiatura e gli operatori sono state integrate anche funzioni di sicurezza come le valvole di scarico della pressione e le funzioni di arresto di emergenza.
Applicazioni e vantaggi
I forni sottovuoto per molibdeno sono strumenti versatili, utilizzati in diversi settori, tra cui la metallurgia, la ceramica e l'elettronica. La loro capacità di operare sotto vuoto o in atmosfera controllata li rende ideali per i processi che richiedono un'elevata purezza e una contaminazione minima. L'uso di elementi riscaldanti in molibdeno garantisce un riscaldamento efficiente e affidabile, contribuendo alla qualità complessiva e alla consistenza dei prodotti finali.
In conclusione, la costruzione e la composizione dei forni sottovuoto al molibdeno sono meticolosamente progettate per soddisfare le esigenze delle applicazioni ad alta temperatura e purezza. Ogni componente, dal corpo del forno agli elementi riscaldanti, svolge un ruolo critico nel garantire un funzionamento efficiente e sicuro del forno, rendendolo uno strumento indispensabile in ambienti di produzione e ricerca avanzati.
Sistemi di controllo nei forni a vuoto per molibdeno
I forni a vuoto per molibdeno sono parte integrante dei processi di lavorazione ad alta temperatura e di sintesi dei materiali e utilizzano sistemi di controllo avanzati per garantire precisione ed efficienza. Questi sistemi di controllo, che comprendono sistemi di controllo automatico computerizzato e controllori logici programmabili (PLC), sono fondamentali per gestire processi complessi e mantenere un funzionamento ottimale del forno.
Sistemi di controllo automatico computerizzato
I sistemi di controllo automatico computerizzato nei forni a vuoto per molibdeno sono progettati per gestire funzioni di controllo logico complesse, il monitoraggio continuo dei parametri di processo e la gestione dei dati. Questi sistemi utilizzano hardware e software dedicati per supervisionare operazioni quali la velocità di rifusione, il controllo del gap dell'arco e l'acquisizione dei dati. Un PC di interfaccia operatore (OIP) funge da interfaccia principale tra l'operatore e il processo del forno, fornendo la visualizzazione del processo in tempo reale, la regolazione dei parametri e la gestione delle ricette. L'OIP può anche essere dotato di un'interfaccia di rete Ethernet per il trasferimento continuo dei dati ad altri computer collegati in rete, migliorando l'integrazione del sistema e l'accessibilità dei dati.
Controllori logici programmabili (PLC)
I PLC hanno rivoluzionato il controllo dei forni a vuoto, sostituendo i tradizionali sistemi a relè con controlli digitali più affidabili ed efficienti. Originariamente introdotti per semplificare la gestione di più strumenti di controllo, i PLC sono ora indispensabili nei moderni sistemi di forni a vuoto. Riducono il coinvolgimento dell'operatore, assicurano una qualità costante del prodotto e riducono al minimo i tempi di inattività del forno. Nei moderni forni a vuoto per molibdeno, i PLC sono in genere integrati con interfacce touch panel, che consentono agli operatori di caricare e scaricare il forno, selezionare le ricette di processo e avviare le operazioni con la semplice pressione di un pulsante.
Caratteristiche e vantaggi del sistema di controllo
L'integrazione di sistemi di controllo avanzati nei forni a vuoto per molibdeno offre diversi vantaggi chiave:
-
Precisione e coerenza: I sistemi di controllo avanzati consentono di regolare con precisione i parametri del forno, garantendo una distribuzione uniforme del calore e risultati di lavorazione uniformi. Questa precisione è fondamentale per le applicazioni di alto valore in cui le proprietà del materiale devono essere strettamente controllate.
-
Efficienza energetica: I moderni sistemi di controllo ottimizzano l'uso dell'energia regolando dinamicamente i cicli di riscaldamento e i tassi di raffreddamento in base ai dati in tempo reale. In questo modo non solo si riducono i costi operativi, ma si minimizza anche l'impatto ambientale.
-
Monitoraggio e controllo a distanza: Grazie alla possibilità di operare da postazioni remote, questi sistemi migliorano la flessibilità operativa e la sicurezza. L'accesso remoto consente il monitoraggio e le regolazioni in tempo reale, riducendo la necessità di personale in loco durante le fasi critiche del funzionamento.
-
Gestione e analisi dei dati: I sistemi di controllo avanzati facilitano la registrazione e l'analisi dei dati, essenziali per il miglioramento dei processi e la conformità agli standard di qualità. I dati storici possono essere utilizzati per perfezionare i processi e risolvere i problemi in modo proattivo.
-
Sicurezza migliorata: I sistemi di controllo automatizzati includono protocolli di sicurezza che prevengono gli errori dell'operatore e proteggono dai malfunzionamenti delle apparecchiature. Questo aspetto è particolarmente importante negli ambienti ad alta temperatura e sottovuoto, dove i rischi per la sicurezza sono elevati.
Applicazioni e tendenze future
I forni a vuoto per molibdeno dotati di sistemi di controllo avanzati sono utilizzati in una varietà di applicazioni ad alta temperatura, tra cui la sinterizzazione, il trattamento termico e la sintesi dei materiali. Con il progredire della tecnologia, le tendenze future dei sistemi di controllo si concentreranno probabilmente su un'ulteriore integrazione con l'intelligenza artificiale e gli algoritmi di apprendimento automatico per prevedere e ottimizzare le prestazioni del forno, migliorare la manutenzione predittiva e l'efficienza complessiva del processo.
In conclusione, i sistemi di controllo avanzati nei forni sottovuoto per molibdeno rappresentano un significativo balzo in avanti in termini di precisione, efficienza e sicurezza. Questi sistemi sono essenziali per soddisfare i severi requisiti della moderna lavorazione ad alta temperatura e della sintesi dei materiali, garantendo che i forni sottovuoto per molibdeno rimangano all'avanguardia delle tecnologie produttive avanzate.
Proprietà del materiale e prestazioni degli elementi riscaldanti in molibdeno
Il molibdeno, un metallo refrattario noto per la sua resistenza alle alte temperature e l'eccellente conduttività elettrica, è ampiamente utilizzato in vari elementi riscaldanti in ambito industriale e di laboratorio. La sua capacità di mantenere l'integrità strutturale e le prestazioni a temperature estreme lo rende una scelta preferenziale per le applicazioni che richiedono durata e affidabilità.
Proprietà materiali del molibdeno
Il molibdeno presenta diverse proprietà chiave che lo rendono adatto agli elementi riscaldanti:
- Punto di fusione elevato: Il molibdeno ha un punto di fusione di circa 2623°C (4753°F), notevolmente superiore a quello di molti altri metalli. Questo elevato punto di fusione consente agli elementi riscaldanti in molibdeno di operare a temperature fino a 1700°C (3100°F) senza cedimenti strutturali.
- Buona conducibilità elettrica: Il molibdeno è un ottimo conduttore di elettricità, fondamentale per un'efficiente generazione di calore negli elementi riscaldanti.
- Resistenza allo scorrimento: Alle alte temperature, il molibdeno presenta una deformazione minima nel tempo, nota come resistenza allo scorrimento. Questa proprietà garantisce che gli elementi riscaldanti mantengano la loro forma e le loro prestazioni in caso di esposizione prolungata alle alte temperature.
- Bassa espansione termica: Il molibdeno ha un coefficiente di espansione termica relativamente basso, che contribuisce a ridurre le sollecitazioni e le deformazioni durante i cicli di riscaldamento e raffreddamento rapidi.
Prestazioni in ambienti ad alta temperatura
In ambienti ad alta temperatura, gli elementi riscaldanti in molibdeno dimostrano prestazioni eccezionali:
- Resistenza all'ossidazione: Il molibdeno forma uno strato protettivo di triossido di molibdeno (MoO3) quando è esposto a temperature elevate in atmosfere ossidanti. Questo strato aiuta a prevenire l'ulteriore ossidazione e prolunga la durata degli elementi riscaldanti.
- Forza e durata: Nonostante il funzionamento ad alta temperatura, il molibdeno mantiene la sua resistenza e non diventa fragile se non esposto a temperature superiori a 1700°C (3100°F). Ciò garantisce che gli elementi riscaldanti possano resistere alle sollecitazioni meccaniche e agli shock termici.
- Distribuzione efficiente del calore: La buona conducibilità termica del molibdeno garantisce una distribuzione uniforme del calore, essenziale per un riscaldamento costante nei forni industriali e di laboratorio.
Effetti delle leghe sul molibdeno
La lega del molibdeno con altri elementi ne migliora le proprietà e ne estende la gamma operativa:
- Lega TZM: L'aggiunta di titanio e zirconio al molibdeno forma la lega TZM, che presenta una maggiore resistenza, una temperatura di ricristallizzazione più elevata e una migliore resistenza allo scorrimento. La TZM può operare a temperature dell'elemento fino a 1400°C (2552°F).
- Molibdeno lantanato (MoLa): Incorporando il triossido di lantanio nel molibdeno si ottiene una struttura a grani fini "a fibre sovrapposte" che aumenta notevolmente la resistenza alla ricristallizzazione e alla deformazione ad alta temperatura. Il MoLa può essere utilizzato a temperature dell'elemento fino a 2000°C (3632°F).
- Disiliciuro di molibdeno (MoSi2): Questo composto offre bassa resistività, caratteristiche positive di resistenza e temperatura ed eccellente resistenza all'ossidazione ad alta temperatura. Gli elementi riscaldanti in MoSi2 possono funzionare con carichi di watt molto elevati e mantenere prestazioni costanti per tutta la loro durata.
Applicazioni degli elementi riscaldanti in molibdeno
Gli elementi riscaldanti in molibdeno sono ampiamente utilizzati in varie applicazioni, tra cui:
- Forni a vuoto: Grazie alla sua resistenza all'ossidazione e all'elevato punto di fusione, il molibdeno è ideale per i forni a vuoto utilizzati nei processi di trattamento termico come la tempra e la brasatura.
- Forni industriali e da laboratorio: La capacità del molibdeno di resistere alle alte temperature e la distribuzione uniforme del calore lo rendono adatto a un'ampia gamma di forni industriali e di laboratorio.
- Ambienti di ossidazione ad alta temperatura: La formazione di uno strato di ossido protettivo sugli elementi riscaldanti in molibdeno ne garantisce la longevità e l'affidabilità in atmosfere ossidanti ad alta temperatura.
In conclusione, il molibdeno e le sue leghe sono materiali fondamentali per gli elementi riscaldanti, grazie alle loro eccezionali prestazioni ad alta temperatura, alla resistenza e alla durata. Grazie a un'attenta selezione e alle leghe, questi materiali possono essere adattati per soddisfare i requisiti specifici di varie applicazioni industriali e di laboratorio, garantendo processi di riscaldamento efficienti e affidabili.
Manutenzione e prestazioni a lungo termine dei forni a vuoto al molibdeno
Il mantenimento delle prestazioni a lungo termine dei forni a vuoto per molibdeno è fondamentale per garantire un funzionamento costante e affidabile. Questi forni sono progettati per operare in condizioni estreme e una corretta manutenzione può prevenire problemi come l'indurimento, il collasso e la perdita di resistenza degli elementi riscaldanti ad alte temperature. Ecco le linee guida dettagliate per preservare l'integrità e l'efficienza del vostro forno a vuoto per molibdeno.
Manutenzione degli elementi riscaldanti
Gli elementi riscaldanti in molibdeno sono componenti critici dei forni a vuoto. Devono essere sottoposti a un'accurata manutenzione per evitare danni e garantire una lunga durata. Dopo ogni utilizzo, ispezionare gli elementi riscaldanti per individuare eventuali segni di danneggiamento. Controllare la tenuta dei collegamenti per evitare problemi elettrici. Se un elemento riscaldante è danneggiato, può essere possibile ripararlo. Gli elementi in molibdeno possono essere riparati fino a tre volte per fascia di elementi, ma ciò richiede particolari precauzioni a causa della fragilità del molibdeno e del potenziale rilascio di vapori tossici di biossido di molibdeno durante il processo di riparazione.
Condizionamento di nuovi elementi riscaldanti
I nuovi elementi riscaldanti in molibdeno devono essere condizionati per migliorarne le prestazioni e la durata. Ciò comporta il riscaldamento del forno vuoto a 1550°C e il mantenimento di tale temperatura per un'ora. Questo processo contribuisce all'applicazione di un sottile strato protettivo di vetro sugli elementi, che può prevenire il degrado prematuro. Se il forno deve funzionare per periodi prolungati a temperature inferiori a 800°C, ricondizionare le superfici utilizzando la procedura di cottura iniziale per mantenerne l'integrità.
Controllo della velocità di riscaldamento
La velocità di riscaldamento è un fattore critico per mantenere l'integrità strutturale degli elementi riscaldanti. Un riscaldamento rapido può portare all'espansione termica e alla deformazione dello scudo termico. Si raccomanda di utilizzare una velocità di riscaldamento lenta, soprattutto nella fase ad alta temperatura. Ad esempio, riducendo la velocità di rampa per le temperature di 100-200°C al di sotto della temperatura nominale massima del forno a 60-100°C all'ora, si possono evitare sollecitazioni eccessive sugli elementi riscaldanti.
Controlli del vuoto e delle perdite
Prima di avviare il processo di riscaldamento, è essenziale verificare il tasso di perdita del vuoto e il grado di vuoto finale. Garantire un ambiente di vuoto adeguato è fondamentale per il funzionamento efficiente del forno. Quando l'apparecchiatura non è in uso, conservarla in condizioni di vuoto. Se all'interno del forno sono presenti sostanze volatili, è necessario asciugarlo per evitare contaminazioni e potenziali danni agli elementi riscaldanti.
Manipolazione dei prodotti e controllo delle impurità
Quando si maneggiano i prodotti, fare attenzione a non farli cadere sulla superficie degli elementi riscaldanti in molibdeno, perché potrebbero danneggiarsi. I prodotti contenenti elementi di ferro con punti di fusione più bassi non devono volatilizzarsi sul nastro di molibdeno nel forno, poiché ciò può portare alla fusione nel tempo. Tenere i prodotti saldamente con entrambe le mani o utilizzare oggetti meccanici per evitare cadute accidentali. Inoltre, controllare rigorosamente il contenuto di impurità dei prodotti per evitare la contaminazione degli elementi riscaldanti.
Collegamenti elettrici e sistemi di raffreddamento
Il collegamento elettrico agli elementi riscaldanti avviene in genere tramite un passante raffreddato ad acqua. Questa connessione sigillata contiene il conduttore che porta la corrente all'elemento riscaldante. I passanti sono disponibili in varie correnti nominali, anche ad alta capacità. Il raffreddamento ad acqua previene il surriscaldamento ed è essenziale utilizzare un sistema di raffreddamento a circuito chiuso e collegato a terra con refrigeranti non conduttivi come acqua deionizzata o glicole etilenico. Le linee di raffreddamento devono essere realizzate con materiali non conduttivi, come i tubi in polipropilene, per evitare che il refrigerante diventi parte del circuito.
Progettazione di elementi di riscaldamento resistenti
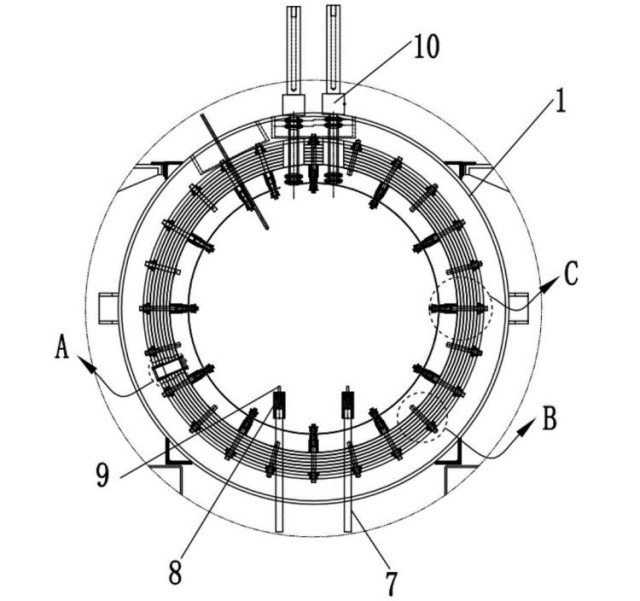
Per garantire che il filo di riscaldamento del forno a vuoto mantenga la resistenza necessaria alle alte temperature e impedisca l'indurimento, il collasso o l'abbassamento, è necessario progettare attentamente le dimensioni del filo di riscaldamento. A tal fine, è necessario utilizzare un filo di resistenza a spirale e prestare attenzione al diametro di curvatura, al passo e al diametro centrale dell'elemento riscaldante. Il corpo riscaldante deve essere fissato contro il rivestimento isolante del forno a vuoto, con 95 pezzi di ceramica posizionati nel rivestimento isolante per fornire uno spazio di espansione adeguato. Durante l'uso, posizionare gli elementi riscaldanti in modo appropriato, in genere a intervalli di 100-200 mm, e agganciarli saldamente per evitare che il filo della resistenza rimanga piatto. Inoltre, evitare il contatto diretto tra i fili del forno per prevenire i cortocircuiti, in genere utilizzando fogli di isolamento.
Seguendo queste linee guida complete per la manutenzione e la progettazione, è possibile garantire le prestazioni e l'affidabilità a lungo termine del forno a vuoto per molibdeno, prolungandone la durata e mantenendo un'efficienza operativa ottimale.
Applicazioni dei forni a vuoto per molibdeno nell'industria
I forni sottovuoto al molibdeno svolgono un ruolo cruciale in diversi settori industriali grazie alla loro capacità di operare a temperature elevate e in condizioni di vuoto, garantendo un controllo preciso del processo di riscaldamento senza ossidazione o contaminazione. Questa sezione esplora le diverse applicazioni dei forni a vuoto al molibdeno in settori quali la ceramica, la metallurgia, l'elettronica e i trattamenti di materiali speciali.
Industria della ceramica
Nell'industria della ceramica, i forni a vuoto al molibdeno sono essenziali per la produzione di ceramiche dense e di alta qualità con proprietà uniformi. Questi forni consentono la sinterizzazione di ceramiche avanzate a temperature fino a 2400°C, che sono fondamentali per ottenere le proprietà meccaniche, elettriche e termiche desiderate. L'ambiente sotto vuoto impedisce l'ossidazione delle polveri ceramiche, consentendo di ottenere prodotti con purezza e prestazioni migliori. Le applicazioni includono la produzione di ceramiche tecniche utilizzate nell'elettronica, nell'aerospaziale e nei dispositivi medici.
Metallurgia
Il settore della metallurgia utilizza ampiamente i forni sottovuoto al molibdeno per la fusione e il trattamento termico dei metalli. Questi forni sono ideali per la lavorazione di metalli refrattari come tungsteno, molibdeno e tantalio, che richiedono punti di fusione elevati e resistono all'ossidazione. La fusione sotto vuoto aiuta a rimuovere le impurità e i gas volatili, ottenendo metalli con purezza e proprietà meccaniche superiori. Inoltre, questi forni sono utilizzati per il trattamento termico di acciai ad alta resistenza, acciai inossidabili e acciai per utensili per ottenere la durezza, la tenacità e la resistenza all'usura desiderate.
Elettronica
Nell'industria elettronica, i forni a vuoto al molibdeno sono utilizzati per la produzione di dispositivi a semiconduttore e circuiti integrati. I forni sono utilizzati per processi come la sinterizzazione, la ricottura e la diffusione, che richiedono un controllo preciso della temperatura e un ambiente privo di contaminazione. Le capacità ad alta temperatura dei forni al molibdeno consentono la lavorazione di materiali avanzati come il carburo di silicio e il nitruro di gallio, fondamentali per i dispositivi elettronici di prossima generazione.
Trattamenti speciali dei materiali
I forni a vuoto al molibdeno sono utilizzati anche per trattamenti speciali dei materiali in vari settori. Questi includono:
- Brasatura e saldatura: I forni sottovuoto offrono un ambiente ideale per le operazioni di brasatura e saldatura, garantendo giunti di alta qualità con ossidazione e porosità minime. Questo aspetto è particolarmente importante nell'industria aerospaziale e automobilistica, dove affidabilità e prestazioni sono fondamentali.
- Trattamento del combustibile nucleare: I forni al molibdeno sono utilizzati per la produzione di pellet di combustibile nucleare, garantendo elevata purezza e densità. L'ambiente sottovuoto aiuta a rimuovere le impurità e i gas volatili, essenziali per la sicurezza e le prestazioni nucleari.
- Fusione del vetro: Nell'industria del vetro, i forni sottovuoto al molibdeno sono utilizzati per la fusione di vetri di elevata purezza e per la creazione di ceramiche tecniche. Le alte temperature e l'atmosfera controllata consentono di produrre vetri speciali con proprietà ottiche e meccaniche uniche.
Vantaggi dei forni sottovuoto al molibdeno
L'uso di forni sottovuoto al molibdeno offre diversi vantaggi, tra cui:
- Capacità di produrre ad alta temperatura: Gli elementi riscaldanti in molibdeno possono resistere a temperature fino a 2400°C, rendendoli adatti alla lavorazione di materiali ad alta temperatura.
- Atmosfera controllata: L'ambiente sotto vuoto impedisce l'ossidazione e la contaminazione, garantendo prodotti di alta qualità con proprietà costanti.
- Efficienza energetica: I forni sottovuoto sono progettati per essere efficienti dal punto di vista energetico, riducendo i costi operativi e l'impatto ambientale.
- Versatilità: I forni sottovuoto al molibdeno possono essere configurati per varie applicazioni, diventando così uno strumento versatile in diversi settori.
In conclusione, i forni sottovuoto al molibdeno sono indispensabili nell'industria moderna, in quanto consentono di produrre materiali e componenti di alta qualità con un controllo preciso e una contaminazione minima. Le loro applicazioni spaziano dalla ceramica alla metallurgia, dall'elettronica ai trattamenti di materiali speciali, evidenziando il loro ruolo critico nel progresso dei processi tecnologici e industriali.
Tendenze future e innovazioni nella tecnologia dei forni a vuoto per molibdeno
Il settore della tecnologia dei forni sottovuoto al molibdeno è pronto per significativi progressi e innovazioni che miglioreranno l'efficienza e amplieranno le applicazioni in vari settori. Con l'aumento della domanda di materiali di alta qualità e di processi di trattamento termico precisi, lo sviluppo di forni sottovuoto avanzati per il molibdeno sta diventando fondamentale.
Miglioramenti dell'efficienza
Uno degli obiettivi principali dell'evoluzione della tecnologia dei forni a vuoto al molibdeno è il miglioramento dell'efficienza operativa. Le innovazioni negli elementi riscaldanti, nei materiali isolanti e nei sistemi di controllo dovrebbero ridurre il consumo energetico e migliorare l'uniformità della temperatura. Ad esempio, l'integrazione di materiali isolanti avanzati come le fibre ceramiche e l'isolamento multistrato può ridurre significativamente le perdite di calore, migliorando così l'efficienza energetica complessiva del forno.
Inoltre, lo sviluppo di sistemi di controllo intelligenti che utilizzano l'intelligenza artificiale e gli algoritmi di apprendimento automatico può ottimizzare i cicli di riscaldamento, prevedere le esigenze di manutenzione e regolare i parametri operativi in tempo reale. Questi sistemi possono analizzare grandi quantità di dati raccolti dai sensori all'interno del forno per garantire prestazioni ottimali e tempi di inattività minimi.
Nuove applicazioni
La versatilità dei forni sottovuoto al molibdeno sta aprendo nuove strade per applicazioni in campi emergenti come la produzione additiva, la ceramica avanzata e la lavorazione dei semiconduttori. La capacità di controllare l'atmosfera e la temperatura con grande precisione rende questi forni ideali per la lavorazione di materiali avanzati che richiedono condizioni ambientali specifiche.
Nel campo della manifattura additiva, i forni sottovuoto al molibdeno possono essere utilizzati per la post-elaborazione di parti metalliche, assicurando che siano prive di impurità e abbiano le proprietà meccaniche desiderate. Allo stesso modo, nella produzione di ceramiche avanzate, questi forni possono facilitare la sinterizzazione di forme e composizioni complesse che non sono possibili con i metodi convenzionali.
Innovazioni nei materiali
Lo sviluppo di nuove leghe e compositi di molibdeno è un'altra area di innovazione. Incorporando elementi come il titanio, lo zirconio e i metalli delle terre rare, i ricercatori stanno creando leghe di molibdeno con una maggiore resistenza alle alte temperature, alla corrosione e alla conducibilità termica. Questi materiali avanzati possono estendere l'intervallo di temperatura operativa degli elementi riscaldanti in molibdeno e migliorarne la durata.
Inoltre, l'uso delle nanotecnologie nella produzione di elementi riscaldanti in molibdeno può portare a miglioramenti significativi delle loro prestazioni. I rivestimenti nanostrutturati possono migliorare l'emissività degli elementi, consentendo un trasferimento di calore più efficiente e un consumo energetico ridotto.
Considerazioni ambientali
Con l'inasprirsi delle normative ambientali, anche la progettazione dei forni sottovuoto per molibdeno si sta evolvendo per ridurre al minimo l'impronta ecologica. Si stanno studiando innovazioni nella progettazione dei forni che riducano la produzione di rifiuti e migliorino le capacità di riciclaggio. Inoltre, lo sviluppo di forni ad alta efficienza energetica, conformi agli standard internazionali di consumo energetico, sta diventando una priorità per i produttori.
Conclusione
Il futuro deiforni sottovuoto per molibdeno è luminoso, con numerose innovazioni all'orizzonte che porteranno a miglioramenti dell'efficienza e all'espansione delle applicazioni. Sfruttando i progressi nella scienza dei materiali, nei sistemi di controllo e nella sostenibilità ambientale, l'industria è pronta a soddisfare la crescente domanda di materiali di alta qualità e di precisione. Con la continua evoluzione di queste tecnologie, esse svolgeranno un ruolo cruciale nel plasmare il futuro di vari settori, da quello aerospaziale e automobilistico a quello elettronico e sanitario.
CONTATTATECI PER UNA CONSULENZA GRATUITA
I prodotti e i servizi di KINTEK LAB SOLUTION sono stati riconosciuti da clienti di tutto il mondo. Il nostro personale sarà lieto di assistervi per qualsiasi richiesta. Contattateci per una consulenza gratuita e parlate con uno specialista del prodotto per trovare la soluzione più adatta alle vostre esigenze applicative!