La sinterizzazione in un forno a induzione si riferisce al processo di compattazione e unione delle particelle di polvere in una massa solida mediante l'applicazione di calore, in genere al di sotto del punto di fusione del materiale.Questo processo è fondamentale per la formazione del rivestimento del forno, che deve resistere alle alte temperature e alle sollecitazioni meccaniche durante il funzionamento.Il processo di sinterizzazione in un forno a induzione prevede tre fasi fondamentali: cottura, semi-sinterizzazione e sinterizzazione completa.Ogni fase è attentamente controllata per garantire che il rivestimento raggiunga una microstruttura uniforme, durevole e ad alte prestazioni.I forni a induzione, grazie al controllo preciso della temperatura e alle capacità di riscaldamento uniforme, sono particolarmente adatti ai processi di sinterizzazione, garantendo l'integrità e la durata del rivestimento.
Punti chiave spiegati:
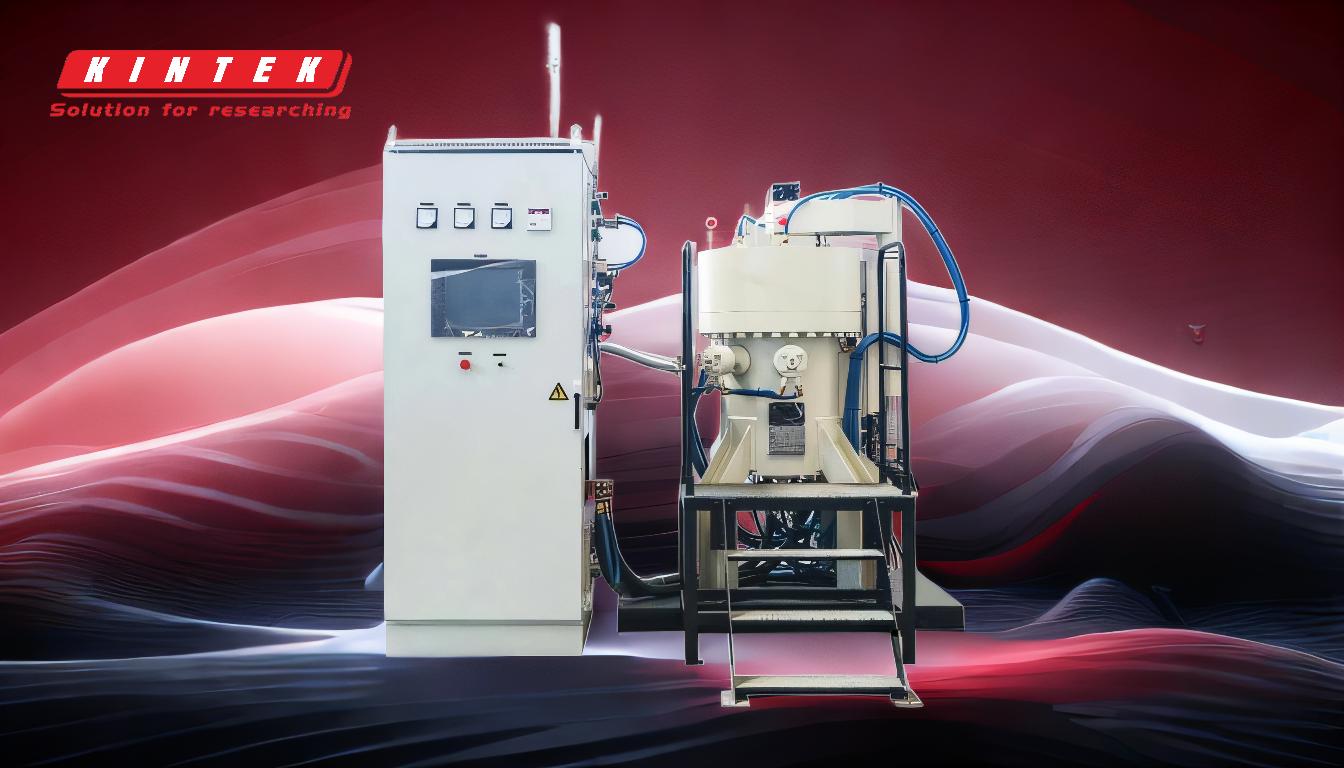
-
Definizione di sinterizzazione nei forni a induzione:
- La sinterizzazione è il processo di compattazione e unione di particelle di polvere in una massa solida utilizzando il calore, in genere al di sotto del punto di fusione del materiale.
- Nei forni a induzione, la sinterizzazione è utilizzata principalmente per formare il rivestimento refrattario, che deve sopportare temperature elevate e sollecitazioni meccaniche durante il funzionamento.
-
Fasi del processo di sinterizzazione:
-
Fase di cottura:
- Il rivestimento del forno viene riscaldato a circa 600°C a una velocità controllata.
- Questa fase rimuove l'umidità dal materiale refrattario, prevenendo le crepe e garantendo l'integrità strutturale.
-
Fase di semi-sinterizzazione:
- La temperatura viene portata a 900°C e mantenuta per un certo periodo.
- Successivamente, la temperatura viene portata a 1200°C a un ritmo più veloce e mantenuta nuovamente.
- Questa fase avvia l'unione delle particelle, formando una struttura semisolida.
-
Fase di sinterizzazione completa:
- La temperatura finale viene regolata in base alle proprietà del materiale e alle caratteristiche del rivestimento desiderate.
- Questa fase garantisce che il rivestimento raggiunga una microstruttura completamente legata, densa e durevole.
-
Fase di cottura:
-
Importanza della sinterizzazione per i rivestimenti dei forni:
- Un rivestimento ben sinterizzato ha una struttura a tre strati che garantisce proprietà termiche e meccaniche ottimali.
- Una sinterizzazione adeguata aumenta la resistenza del rivestimento agli shock termici, all'erosione e alle reazioni chimiche con i metalli fusi.
- Il processo di sinterizzazione influisce direttamente sulla durata del rivestimento e sulle prestazioni complessive del forno.
-
Ruolo dei forni a induzione nella sinterizzazione:
- I forni a induzione forniscono un controllo preciso della temperatura e un riscaldamento uniforme, essenziali per ottenere risultati di sinterizzazione uniformi.
- Il campo elettromagnetico dei forni a induzione genera correnti parassite, garantendo una composizione e una distribuzione uniforme della temperatura nel materiale di rivestimento.
- I forni a induzione possono raggiungere temperature fino a 1650°C, adatte alla sinterizzazione di un'ampia gamma di materiali refrattari.
-
Vantaggi dei forni a induzione per la sinterizzazione:
- Riscaldamento uniforme:Assicura una sinterizzazione uniforme su tutto il rivestimento, riducendo il rischio di punti deboli.
- Efficienza energetica:I forni a induzione sono altamente efficienti, con una potenza di uscita effettiva superiore al 95%.
- Automazione e controllo:I sistemi di controllo avanzati consentono di regolare con precisione le velocità di riscaldamento, le temperature e i tempi di mantenimento.
- Durata:I forni a induzione sono progettati per il funzionamento continuo 24 ore su 24 e sono quindi ideali per i processi di sinterizzazione industriale.
-
Parametri chiave del processo:
- Controllo della temperatura:La regolazione precisa delle velocità di riscaldamento e dei tempi di mantenimento è fondamentale per ottenere le proprietà di rivestimento desiderate.
- Composizione del materiale:La composizione chimica del materiale refrattario, in particolare gli elementi ad alta affinità con l'ossigeno, deve essere gestita con attenzione.
- Proprietà fisiche:Fattori come il punto di fusione, la bagnabilità e la tensione superficiale influenzano il processo di sinterizzazione.
- Purezza e fluidità:Garantire la purezza e la fluidità del materiale fuso durante la sinterizzazione migliora le prestazioni del rivestimento.
-
Considerazioni pratiche per la sinterizzazione nei forni a induzione:
- Design del forno:Il forno deve essere dotato di induttore, alimentazione e sistema di controllo di alta qualità per supportare il processo di sinterizzazione.
- Materiali di rivestimento:La scelta dei materiali refrattari e la loro compatibilità con il processo di sinterizzazione è fondamentale.
- Manutenzione:L'ispezione e la manutenzione regolari del rivestimento del forno sono necessarie per garantire prestazioni a lungo termine.
Comprendendo questi punti chiave, gli acquirenti di apparecchiature e materiali di consumo possono prendere decisioni informate sul processo di sinterizzazione nei forni a induzione, garantendo prestazioni ottimali e longevità del rivestimento del forno.
Tabella riassuntiva:
Aspetto | Dettagli |
---|---|
Definizione | Compattazione e unione di particelle di polvere utilizzando un calore inferiore al punto di fusione. |
Fasi chiave | Cottura (600°C), Semisinterizzazione (900°C-1200°C), Sinterizzazione completa. |
Importanza | Migliora la durata del rivestimento, la resistenza agli shock termici e la durata del forno. |
Vantaggi | Riscaldamento uniforme, efficienza energetica, controllo preciso e durata. |
Parametri chiave | Controllo della temperatura, composizione del materiale, proprietà fisiche, purezza. |
Considerazioni pratiche | Progettazione del forno, materiali di rivestimento e manutenzione regolare. |
Siete pronti a ottimizzare il vostro processo di sinterizzazione? Contattate oggi stesso i nostri esperti per soluzioni su misura!