La sinterizzazione al plasma di scintilla (SPS) è una moderna tecnica di sinterizzazione che combina pressione monoassiale e corrente continua pulsata (DC) per consolidare rapidamente le polveri in materiali densi e omogenei.Il processo è caratterizzato da velocità, efficienza e capacità di ottenere un'elevata densificazione a temperature inferiori rispetto ai metodi di sinterizzazione convenzionali.Le fasi principali del processo SPS comprendono la rimozione del gas e la creazione del vuoto, l'applicazione della pressione, il riscaldamento a resistenza e il raffreddamento.Ciascuna fase svolge un ruolo critico nel garantire il successo della densificazione e dell'adesione delle particelle di polvere.Il processo sfrutta la scarica al plasma, il riscaldamento joule e la deformazione plastica per ottenere un riscaldamento rapido, l'adesione delle particelle e il consolidamento del materiale.
Punti chiave spiegati:
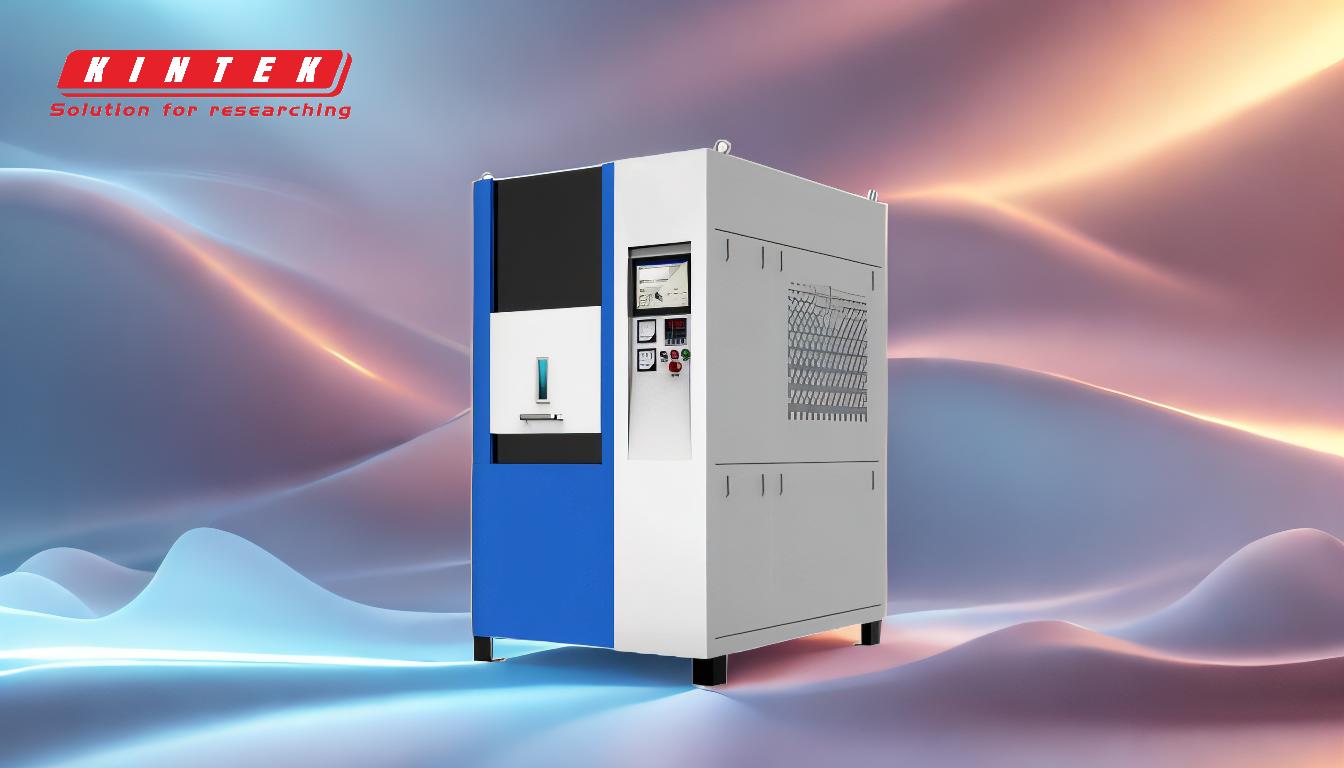
-
Rimozione dei gas e creazione del vuoto
- La prima fase del processo SPS prevede la rimozione dei gas dalla camera di sinterizzazione e la creazione di un vuoto o di un'atmosfera controllata.
- Questa operazione è fondamentale per prevenire l'ossidazione e la contaminazione del materiale in polvere, garantendo la purezza e la qualità del prodotto finale.
- A ambiente sotto vuoto facilita inoltre un migliore trasferimento di calore e la generazione di plasma durante le fasi successive.
-
Applicazione della pressione
- La pressione uniassiale viene applicata al materiale in polvere all'interno di uno stampo, tipicamente in grafite .
- La pressione aiuta a compattare le particelle di polvere, riducendo gli spazi tra di esse e favorendo un migliore contatto per la sinterizzazione.
- La pressione applicata favorisce anche la deformazione plastica delle particelle, essenziale per ottenere un'elevata densificazione.
-
Riscaldamento a resistenza
- La corrente continua pulsata viene fatta passare attraverso la matrice di grafite e, se conduttiva, attraverso il materiale in polvere stesso.
- Questo genera alte temperature localizzate e scariche di plasma tra le particelle, provocando un rapido riscaldamento.
-
Il processo prevede tre meccanismi di riscaldamento:
- Riscaldamento al plasma:La scarica tra le particelle crea un plasma che facilita la diffusione e il legame con la superficie.
- Riscaldamento Joule:La resistenza elettrica all'interno del materiale genera calore, favorendo ulteriormente la sinterizzazione.
- Deformazione plastica:La combinazione di calore e pressione provoca la deformazione delle particelle e il loro legame alle interfacce.
- Questi meccanismi consentono di sinterizzare a temperature molto più basse e in tempi più brevi rispetto ai metodi convenzionali.
-
Fase di raffreddamento
- Dopo il processo di sinterizzazione, il materiale viene raffreddato rapidamente a temperatura ambiente.
- Il raffreddamento rapido aiuta a preservare la microstruttura e le proprietà del materiale sinterizzato.
- La velocità di raffreddamento viene controllata per evitare tensioni termiche o cricche nel prodotto finale.
-
Vantaggi di SPS
- Velocità:L'SPS completa il processo di sinterizzazione in una frazione del tempo richiesto dai metodi convenzionali.
- Temperature più basse:L'SPS raggiunge la densificazione a temperature inferiori di diverse centinaia di gradi rispetto alla sinterizzazione tradizionale.
- Migliori proprietà del materiale:Le rapide velocità di riscaldamento e raffreddamento consentono di ottenere microstrutture più fini e proprietà meccaniche migliori.
- Versatilità:L'SPS può essere utilizzato per un'ampia gamma di materiali, tra cui ceramiche, metalli e compositi.
-
Applicazioni della SPS
- La SPS è ampiamente utilizzata nella fabbricazione di materiali avanzati, come ceramiche nanostrutturate, materiali a gradazione funzionale e compositi.
- È particolarmente utile nei settori che richiedono materiali ad alte prestazioni con un controllo preciso della microstruttura e delle proprietà, come quello aerospaziale, automobilistico ed elettronico.
Seguendo questi passaggi, la sinterizzazione al plasma di scintilla consente la produzione di materiali densi e di alta qualità con proprietà superiori, che la rendono una scelta preferenziale per la fabbricazione di materiali avanzati.
Tabella riassuntiva:
Fase | Dettagli chiave |
---|---|
Rimozione dei gas e vuoto | Rimuove i gas, previene l'ossidazione e garantisce un'atmosfera controllata. |
Applicazione della pressione | Compatta le particelle di polvere, riduce gli spazi vuoti e favorisce la deformazione plastica. |
Riscaldamento a resistenza | Utilizza la corrente continua pulsata per la scarica al plasma, il riscaldamento joule e l'incollaggio rapido delle particelle. |
Fase di raffreddamento | Il raffreddamento rapido preserva la microstruttura e previene le sollecitazioni termiche. |
Vantaggi | Velocità, temperature più basse, proprietà migliorate e versatilità dei materiali. |
Applicazioni | Aerospaziale, automobilistico, elettronico e fabbricazione di materiali avanzati. |
Scoprite come la sinterizzazione al plasma di scintilla può rivoluzionare il vostro processo di fabbricazione dei materiali... contattateci oggi stesso !