I forni per il trattamento termico sono classificati in base a diversi fattori chiave, tra cui la fonte di calore, la temperatura di lavoro e il tipo di trattamento termico che eseguono.Queste classificazioni aiutano a scegliere il forno giusto per specifiche applicazioni industriali.Le fonti di calore possono essere basate sulla resistenza o sui combustibili, ulteriormente suddivisi in solidi, liquidi e gassosi.La classificazione delle temperature comprende forni a bassa, media e alta temperatura, ciascuno adatto a diversi processi di trattamento termico.Inoltre, i forni sono classificati in base alla loro struttura e ai processi di trattamento termico specifici per cui sono progettati, come ricottura, rinvenimento, tempra e carburazione.
Punti chiave spiegati:
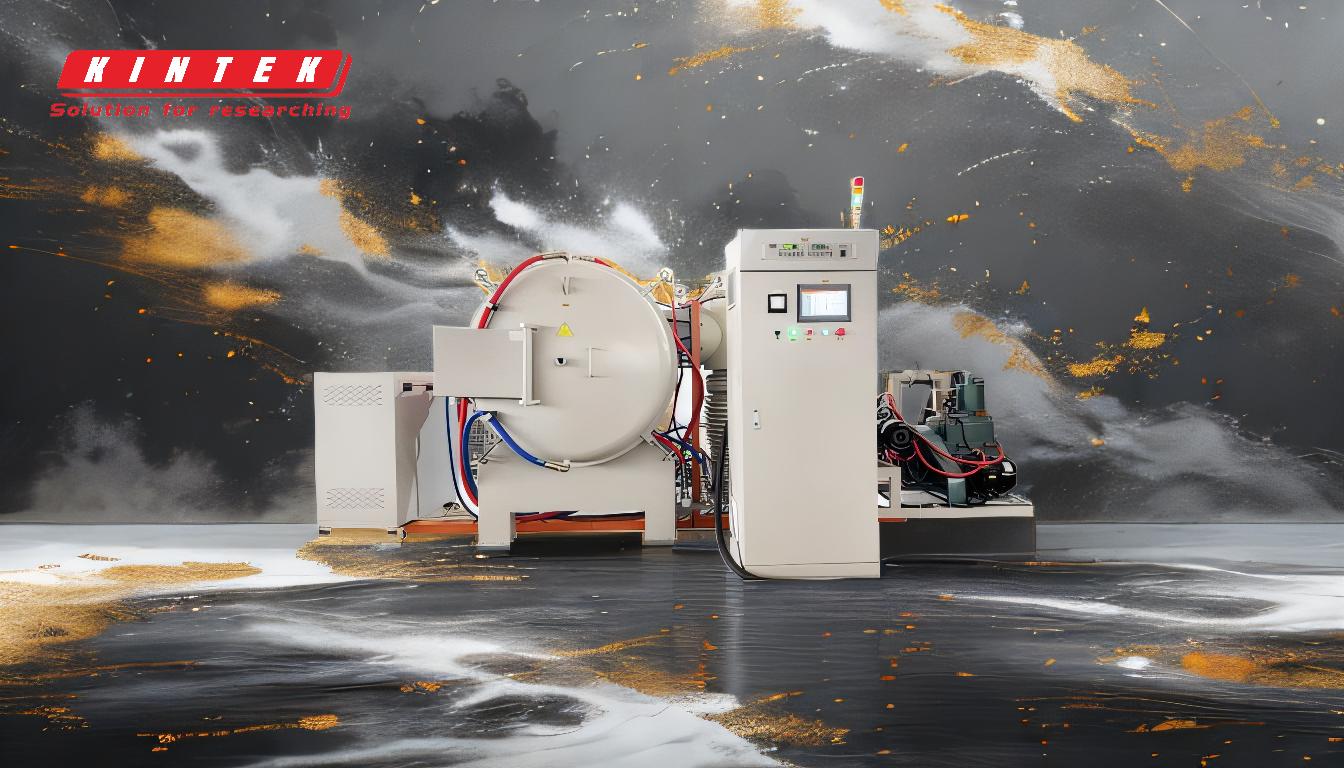
-
Classificazione per fonte di calore:
- Forni a resistenza:Utilizzano la resistenza elettrica per generare calore e sono noti per il controllo preciso della temperatura.Sono comunemente utilizzati in applicazioni che richiedono un riscaldamento uniforme.
-
Forni a combustibile:Si basano sulla combustione di combustibili per produrre calore.Sono ulteriormente classificati in base al tipo di combustibile utilizzato:
- Combustibili solidi:Include carbone, carbone polverizzato e coke.Sono efficaci dal punto di vista dei costi, ma possono produrre più emissioni.
- Combustibili liquidi:Come la benzina e il cherosene.Offrono un migliore controllo della combustione rispetto ai combustibili solidi.
- Combustibili gassosi:Include il gas di carbone e il gas di produzione.Sono più puliti e forniscono una distribuzione efficiente del calore.
-
Classificazione in base alla temperatura di lavoro:
- Forni a bassa temperatura (<650°C):Utilizzati per processi come il rinvenimento e la ricottura subcritica.Questi forni utilizzano spesso la circolazione forzata dell'aria o bagni liquidi (olio, piombo o sale) per ottenere un riscaldamento uniforme.
- Forni a media temperatura (650-1000°C):Adatti per processi quali tempra, normalizzazione e carburazione di acciai al carbonio e basso legati.Questi forni sono versatili e ampiamente utilizzati nel trattamento termico generale.
- Forni ad alta temperatura (>1000°C):Progettati per il trattamento termico di acciai ad alta velocità e altri cicli ad alta temperatura.Questi forni possono operare fino a 1400°C e sono essenziali per i trattamenti specializzati.
-
Classificazione per processo di trattamento termico:
- Forni di ricottura:I forni a rulli, i forni a spinta, i forni a cassetta, i forni a vaso/pozzo, i forni a nastro trasportatore e i forni a tempra integrale.Ogni tipo è progettato per gestire processi di ricottura specifici, garantendo un riscaldamento e un raffreddamento uniformi.
- Forni di tempra:Utilizzati per il rinvenimento o la ricottura subcritica, operano tipicamente a temperature comprese tra 0 e 700°C.Questi forni utilizzano spesso calore secco con circolazione forzata dell'aria o bagni liquidi.
- Forni di carburazione o carbonitrurazione:Sono forni specializzati utilizzati per i processi di tempra superficiale.Introducono carbonio o azoto nella superficie del metallo per aumentarne la durezza e la resistenza all'usura.
-
Classificazione per struttura:
- Forni verticali:Sono progettati con un orientamento verticale che li rende adatti a processi industriali specifici in cui lo spazio è limitato.
- Forni orizzontali:Hanno un orientamento orizzontale e sono comunemente utilizzati per i processi di trattamento termico continuo.
- Forni a camera singola:Questi forni hanno una camera per il riscaldamento e il raffreddamento e sono adatti per i processi a lotti.
- Forni a tre camere:Hanno camere separate per il riscaldamento, il raffreddamento e la tempra, consentendo cicli di trattamento termico più complessi.
-
Forni specializzati:
- Forni a resistenza sotto vuoto:Si tratta di forni moderni in cui l'intero involucro funge da contenitore del vuoto.Sono utilizzati per processi che richiedono un'atmosfera controllata, come i trattamenti endotermici.Possono essere di tipo verticale, orizzontale, a camera singola o a tre camere.
La comprensione di queste classificazioni aiuta a selezionare il forno appropriato in base ai requisiti specifici di trattamento termico, garantendo prestazioni ed efficienza ottimali nelle applicazioni industriali.
Tabella riassuntiva:
Classificazione | Caratteristiche principali | Applicazioni |
---|---|---|
Per fonte di calore | Resistenza (controllo preciso), combustibile (solido, liquido, gassoso) | Riscaldamento uniforme, distribuzione del calore economica o efficiente |
Per temperatura | Bassa (<650°C), Media (650-1000°C), Alta (>1000°C) | Trattamenti di rinvenimento, tempra, acciaio ad alta velocità |
Per processo di trattamento termico | Ricottura, rinvenimento, carburazione | Riscaldamento uniforme, indurimento superficiale, resistenza all'usura |
Per struttura | Verticale, orizzontale, a camera singola, a tre camere | Vincoli di spazio, processi continui, cicli batch o complessi |
Forni specializzati | Resistenza al vuoto (atmosfera controllata) | Trattamenti endotermici, processi di alta precisione |
Avete bisogno di aiuto per scegliere il forno di trattamento termico giusto? Contattate i nostri esperti oggi stesso per soluzioni su misura!