La forgiatura a pressione e la forgiatura a martello sono due metodi distinti utilizzati nella lavorazione dei metalli, ciascuno con una serie di vantaggi e svantaggi.La forgiatura a pressione, in particolare, offre diversi vantaggi rispetto alla forgiatura a martello, che la rendono una scelta preferenziale in molte applicazioni industriali.Di seguito, un'analisi dettagliata dei vantaggi della forgiatura a pressione rispetto alla forgiatura a martello.
Punti chiave spiegati:
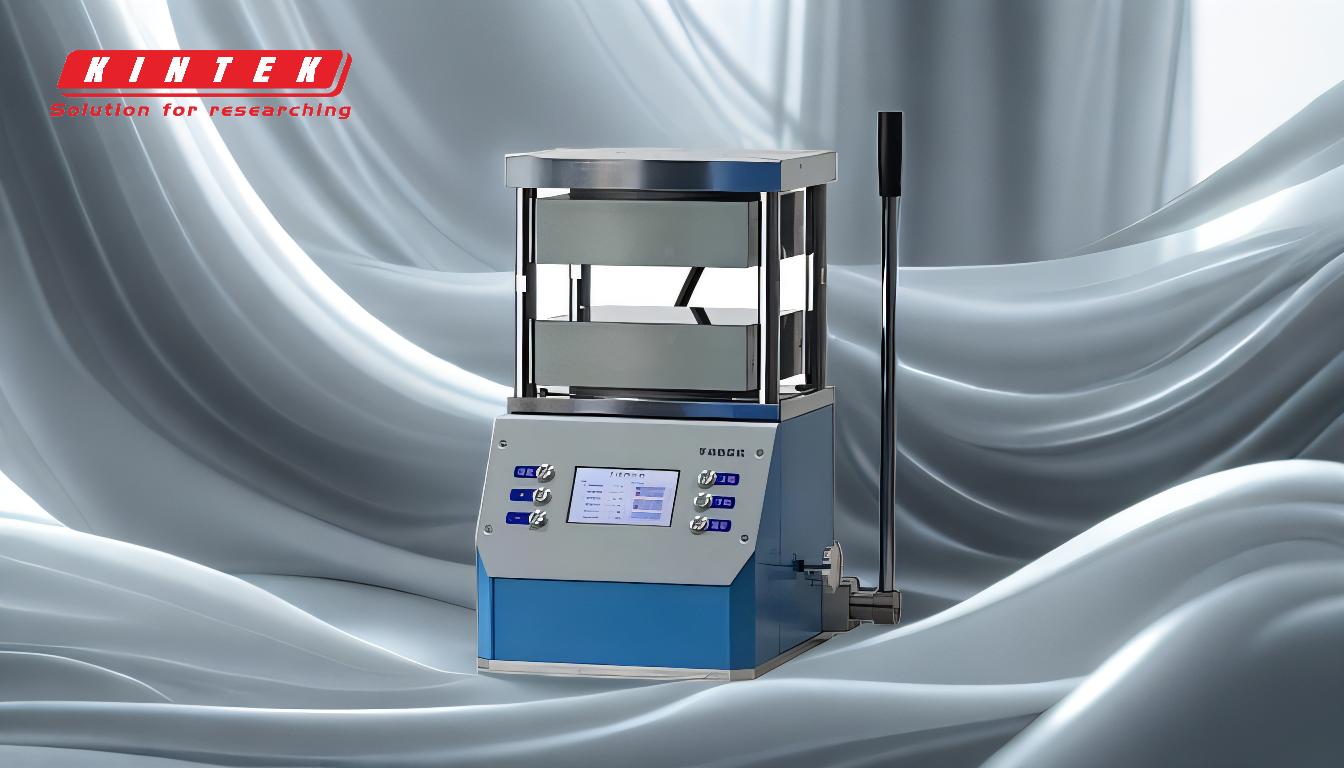
-
Velocità ed efficienza dei costi:
- Forgiatura a pressa:Il processo di forgiatura a pressione è generalmente più rapido e meno costoso rispetto alla forgiatura a martello.Questo perché la forgiatura a pressa comporta un'applicazione continua di pressione, che può essere controllata e automatizzata in modo più efficiente, con tempi di produzione più rapidi e costi di manodopera inferiori.
- Forgiatura a martello:Al contrario, la forgiatura a martello prevede colpi ripetuti per modellare il metallo, il che può richiedere più tempo e lavoro.
-
Flusso dei grani e forza:
- Forgiatura a pressa:Uno dei vantaggi significativi della forgiatura a pressione è il miglioramento del flusso dei grani all'interno del metallo.La pressione continua applicata durante la forgiatura a pressione comprime la struttura dei grani, determinando un flusso di grani più uniforme e allineato.Il risultato è un pezzo finale più resistente e durevole.
- Forgiatura a martello:Sebbene la forgiatura a martello influisca anche sul flusso dei grani, gli impatti ripetuti possono talvolta portare a strutture dei grani meno uniformi, compromettendo potenzialmente la resistenza del prodotto finale.
-
Riduzione dello stress:
- Forgiatura a pressa:Il processo di forgiatura a pressione riduce le sollecitazioni sugli angoli e sui filetti del pezzo forgiato.Ciò è dovuto alla distribuzione uniforme della pressione, che riduce al minimo il rischio di punti di concentrazione delle sollecitazioni che potrebbero portare a cedimenti sotto carico.
- Forgiatura a martello:Gli impatti ripetuti nella forgiatura a martello possono creare punti di stress localizzati, soprattutto in geometrie complesse, che potrebbero richiedere ulteriori trattamenti post-fusione per essere mitigati.
-
Difetti metallurgici:
- Forgiatura a pressa:La forgiatura a pressione riduce al minimo i difetti metallurgici, come la porosità e la segregazione della lega.L'applicazione controllata della pressione garantisce una struttura del materiale più omogenea, che migliora la risposta del pezzo al trattamento termico e riduce la probabilità di difetti.
- Forgiatura a martello:La natura d'impatto della forgiatura a martello può talvolta portare a difetti interni come la porosità, soprattutto se il processo di forgiatura non è controllato meticolosamente.
-
Tempo di lavorazione:
- Forgiatura a pressa:Grazie alla struttura superiore dei grani e alla riduzione dei difetti metallurgici, i pezzi stampati richiedono spesso meno tempo di lavorazione.La forma più precisa e uniforme ottenuta con la forgiatura a pressione significa che è necessario rimuovere meno materiale durante la lavorazione, risparmiando tempo e costi.
- Forgiatura a martello:I pezzi prodotti con la forgiatura a martello possono richiedere una lavorazione più approfondita per ottenere le dimensioni finali e la finitura superficiale desiderate, con conseguente aumento dei tempi e dei costi.
-
Precisione e coerenza:
- Forgiatura a pressa:La forgiatura a pressione consente una maggiore precisione e consistenza del prodotto finale.L'applicazione controllata della pressione assicura che ogni pezzo sia forgiato secondo le specifiche esatte, il che è particolarmente importante per i componenti di alta precisione.
- Forgiatura a martello:Anche se la forgiatura a martello può produrre pezzi precisi, la variabilità introdotta dagli impatti ripetuti può portare a leggere incongruenze tra i pezzi.
-
Automazione e scalabilità:
- Forgiatura a pressa:Il processo si presta maggiormente all'automazione, rendendo più facile l'aumento della produzione.Le linee di forgiatura automatizzate possono produrre grandi quantità di pezzi con un intervento umano minimo, con conseguente aumento dell'efficienza e riduzione dei costi.
- Forgiatura a martello:L'automazione è più impegnativa con la forgiatura a martello a causa della natura del processo, che si basa su impatti ripetuti.Questo può limitare la scalabilità delle operazioni di forgiatura a martello.
In sintesi, lo stampaggio a pressa offre diversi vantaggi rispetto allo stampaggio a percussione, tra cui velocità ed efficienza dei costi, maggiore flusso di grani e resistenza, riduzione delle sollecitazioni sul pezzo finale, minimizzazione dei difetti metallurgici, riduzione dei tempi di lavorazione, maggiore precisione e coerenza e migliore scalabilità grazie all'automazione.Questi vantaggi rendono la forgiatura a pressa il metodo preferito in molte applicazioni industriali in cui sono richiesti pezzi di alta qualità, durevoli e realizzati con precisione.
Tabella riassuntiva:
Aspetto | Forgiatura a pressa | Forgiatura a martello |
---|---|---|
Velocità e costi | Più veloce e meno costoso grazie alla pressione continua e all'automazione. | Richiede tempo e manodopera a causa dei colpi ripetuti. |
Flusso di grani e forza | Flusso della grana migliorato per pezzi più resistenti e durevoli. | Struttura della grana meno uniforme, che può compromettere la resistenza. |
Riduzione dello stress | La pressione uniforme riduce le sollecitazioni su angoli e filetti. | Gli impatti ripetuti creano punti di stress localizzati, che richiedono trattamenti post-forgiatura. |
Difetti metallurgici | Riduce al minimo difetti come porosità e segregazione della lega. | Rischio più elevato di difetti interni come la porosità. |
Tempo di lavorazione | Riduzione dei tempi di lavorazione grazie a forme precise e uniformi. | È necessaria una lavorazione più approfondita per ottenere le dimensioni e le finiture finali. |
**Precisione e coerenza | Maggiore precisione e coerenza nei prodotti finali. | Lievi incongruenze dovute a impatti ripetuti. |
**Automazione e scalabilità | Più facile da automatizzare e scalare per le grandi produzioni. | Scalabilità limitata a causa della dipendenza da impatti ripetuti. |
Siete pronti a ottimizzare il vostro processo di lavorazione dei metalli con la forgiatura a pressione? Contattateci oggi stesso per saperne di più!