Il metodo sputtering è una tecnica di deposizione fisica da vapore (PVD) utilizzata per depositare film sottili su substrati. Si tratta di bombardare un materiale bersaglio con ioni ad alta energia, provocando l'espulsione di atomi dalla superficie del bersaglio. Questi atomi espulsi viaggiano poi attraverso una camera a vuoto e si depositano su un substrato, formando un film sottile. Il processo è altamente preciso ed è ampiamente utilizzato in settori quali i semiconduttori, l'ottica e i rivestimenti. Le fasi principali comprendono la generazione di ioni, il bombardamento del bersaglio, l'espulsione degli atomi, il trasporto attraverso il vuoto e la deposizione sul substrato. Lo sputtering è favorito dalla capacità di produrre film uniformi e di alta qualità, anche su materiali sensibili al calore.
Punti chiave spiegati:
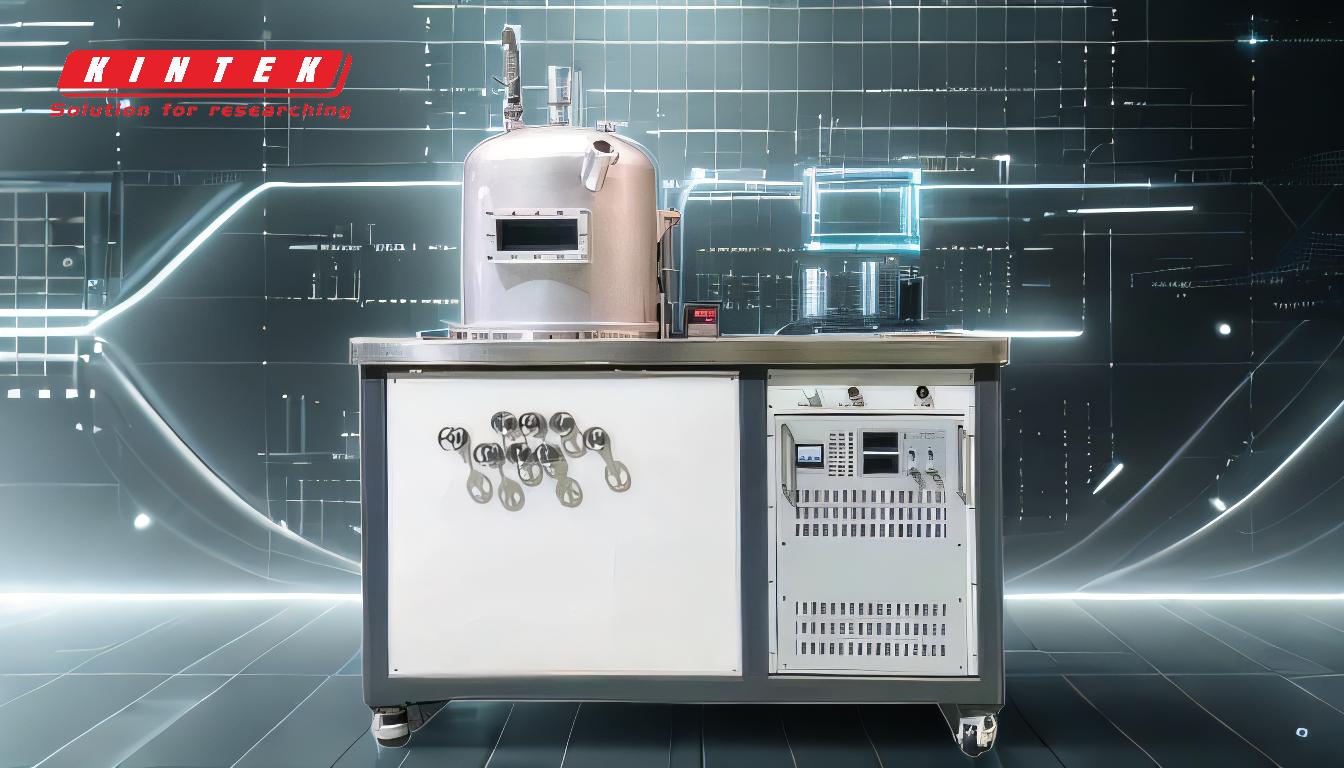
-
Generazione e accelerazione degli ioni:
- Nel processo di sputtering, gli ioni vengono generati ionizzando un gas di sputtering, in genere un gas inerte come l'argon o lo xenon. La ionizzazione avviene in un plasma creato all'interno di una camera a vuoto.
- Tra il target (catodo) e il substrato (anodo) viene applicata una tensione che accelera gli ioni con carica positiva verso il materiale target.
-
Bombardamento del bersaglio:
- Gli ioni accelerati colpiscono il materiale bersaglio con un'elevata energia cinetica. Questo trasferimento di energia fa sì che gli atomi o le molecole vicine alla superficie del bersaglio acquistino energia sufficiente per fuoriuscire dalla superficie.
- Il processo di espulsione degli atomi dal materiale bersaglio è noto come "sputtering"
-
Espulsione e trasporto di atomi:
- Gli atomi o le molecole espulsi dal materiale di destinazione formano un flusso di vapore. Queste particelle viaggiano attraverso la camera a vuoto verso il substrato.
- L'ambiente sotto vuoto è fondamentale perché impedisce le interazioni con l'aria o altri gas indesiderati, garantendo la purezza e la qualità del film depositato.
-
Deposizione su substrato:
- Gli atomi sputati si condensano sul substrato, formando un film sottile. Il substrato è tipicamente montato di fronte al bersaglio all'interno della camera da vuoto.
- La bassa temperatura delle particelle polverizzate consente di rivestire senza danni anche substrati sensibili al calore, come le materie plastiche.
-
Vantaggi dello sputtering:
- Precisione e uniformità: Lo sputtering produce film sottili altamente uniformi e precisi, rendendolo ideale per le applicazioni che richiedono un'elevata precisione, come la produzione di semiconduttori.
- Versatilità: Può depositare un'ampia gamma di materiali, tra cui metalli, leghe e ceramiche, su vari substrati.
- Bassa temperatura: Il processo può essere eseguito a temperature relativamente basse, consentendo il rivestimento di materiali sensibili al calore.
-
Applicazioni dello sputtering:
- Semiconduttori: Utilizzato per depositare film sottili nei circuiti integrati e in altri componenti elettronici.
- Ottica: Applicato nella produzione di rivestimenti antiriflesso, specchi e filtri ottici.
- Rivestimenti: Utilizzato per rivestimenti resistenti all'usura, alla corrosione e decorativi su vari materiali.
Comprendendo questi punti chiave, si può apprezzare l'efficienza e la versatilità del metodo sputtering nella produzione di film sottili di alta qualità per un'ampia gamma di applicazioni.
Tabella riassuntiva:
Passi chiave | Descrizione |
---|---|
Generazione di ioni | Gli ioni sono generati dalla ionizzazione di gas inerti come l'argon in un plasma. |
Bombardamento del bersaglio | Gli ioni ad alta energia colpiscono il bersaglio, espellendo gli atomi dalla sua superficie. |
Espulsione dell'atomo | Gli atomi espulsi formano un flusso di vapore e attraversano una camera a vuoto. |
Deposizione | Gli atomi si condensano sul substrato, formando un film sottile. |
Vantaggi | Precisione, uniformità, versatilità e lavorazione a bassa temperatura. |
Applicazioni | Semiconduttori, ottica, rivestimenti antiusura e altro ancora. |
Scoprite come lo sputtering può migliorare i vostri processi a film sottile.. contattate i nostri esperti oggi stesso !