Indice dei contenuti
Introduzione ai forni fusori sottovuoto
I forni fusori a induzione sottovuoto sono emersi come una tecnologia rivoluzionaria nella lavorazione dei metalli, in grado di soddisfare le esigenze uniche dei materiali avanzati. Questi forni operano in condizioni di vuoto, consentendo un controllo preciso della temperatura, la rimozione dei gas e la prevenzione dell'ossidazione, ottenendo leghe di elevata purezza e alte prestazioni. I forni di fusione a induzione sottovuoto hanno rivoluzionato la produzione di leghe di alta qualità con proprietà eccezionali, rendendoli strumenti indispensabili per la produzione avanzata e la ricerca.
Componenti di un forno di fusione a induzione sottovuoto
Il forno di fusione a induzione sottovuoto è un'apparecchiatura versatile in metallurgia, in grado di fondere un'ampia gamma di metalli e leghe, tra cui superleghe, alluminio, acciaio inossidabile e altro. Il suo funzionamento si basa sull'induzione elettromagnetica in condizioni di vuoto, evitando la contaminazione dei metalli fusi da parte di gas reattivi come ossigeno, azoto e idrogeno.
I componenti principali di un forno di fusione a induzione sottovuoto comprendono:
-
Corpo del forno: Il corpo del forno ospita gli altri componenti e fornisce un ambiente sigillato per il funzionamento sotto vuoto. In genere è costruito con materiali durevoli in grado di resistere alle alte temperature e di mantenere l'integrità del vuoto.
-
Alimentatore a media frequenza: Questa unità fornisce l'energia elettrica necessaria per generare il campo magnetico per il riscaldamento a induzione. È costituita da una fonte di alimentazione, da trasformatori e da circuiti di controllo per regolare la potenza in uscita.
-
Sistema del vuoto: Il sistema del vuoto è responsabile della creazione e del mantenimento del vuoto all'interno della camera del forno. Comprende una pompa per vuoto, manometri e valvole per controllare il livello di vuoto. La pompa del vuoto rimuove l'aria e altri gas dalla camera, ottenendo le condizioni di vuoto necessarie per la fusione.
-
Sistema di raffreddamento: Il sistema di raffreddamento impedisce il surriscaldamento dei componenti del forno, in particolare della bobina di induzione e del crogiolo. In genere utilizza una combinazione di canali raffreddati ad acqua e ventole per dissipare efficacemente il calore.
-
Sistema di controllo elettrico: Questo sistema monitora e controlla il funzionamento del forno, compresi la temperatura, il livello di vuoto e l'alimentazione. Assicura che il forno operi entro parametri sicuri ed efficienti.
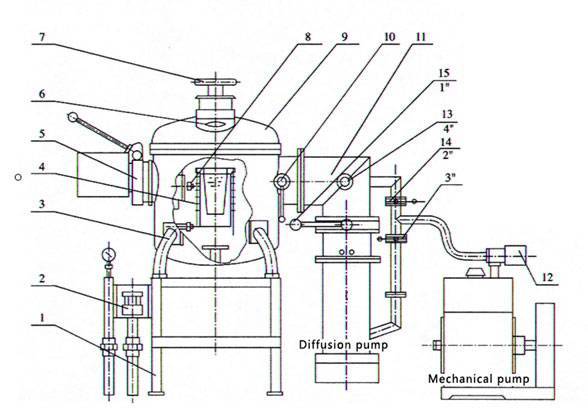
Oltre a questi componenti essenziali, i forni fusori a induzione sottovuoto possono essere dotati di componenti ausiliari in base ai requisiti specifici del processo. Questi possono includere:
- Carrello di trasmissione per facilitare lo spostamento del forno
- Meccanismi di apertura e chiusura della porta del forno
- Vasca di colata centrifuga per la colata del metallo fuso
- Finestra di osservazione per il monitoraggio del processo di fusione
- Sistema di filtraggio dei gas per la rimozione delle impurità nell'ambiente sotto vuoto.
La configurazione e la selezione dei componenti di un forno fusorio a induzione sottovuoto variano a seconda dell'applicazione specifica e dei materiali da fondere. Considerando attentamente i requisiti del processo di fusione, è possibile ottimizzare le prestazioni del forno e ottenere i risultati desiderati.
Funzionamento di un forno di fusione a induzione sottovuoto
La fusione a induzione sotto vuoto è una tecnica di fusione specializzata che prevede il riscaldamento e la fusione del metallo in condizioni di vuoto. Questo processo offre diversi vantaggi, tra cui la rimozione delle impurità, il controllo preciso della temperatura e la capacità di fondere un'ampia gamma di metalli.
Il forno di fusione a induzione sotto vuoto è costituito da diversi componenti chiave:
- Camera a vuoto: Questa camera ermetica ospita la bobina di induzione e il crogiolo.
- Bobina di induzione: Questa bobina genera campi elettromagnetici che inducono correnti parassite nel metallo, provocandone il riscaldamento e la fusione.
- Crogiolo: Questo contenitore contiene il metallo durante il processo di fusione.
- Sistema di vuoto: Questo sistema evacua l'aria dalla camera, creando il vuoto.
- Sistema di raffreddamento: Questo sistema fa circolare l'acqua nel forno per evitare il surriscaldamento.
Il funzionamento di un forno di fusione a induzione sottovuoto prevede le seguenti fasi:
- Caricamento del forno: Il metallo da fondere viene inserito nel crogiolo.
- Evacuazione della camera: Il sistema di vuoto viene attivato per rimuovere l'aria dalla camera.
- Applicazione dell'alimentazione: L'alimentazione viene applicata alla bobina di induzione, generando campi elettromagnetici che riscaldano il metallo.
- Fusione del metallo: Il metallo si scioglie gradualmente e forma una piscina fusa.
- Raffinazione del metallo: Le impurità vengono rimosse dal metallo fuso attraverso reazioni chimiche, dissociazione, flottazione e volatilizzazione.
- Regolazione della chimica: La composizione del metallo fuso viene regolata aggiungendo elementi di lega o rimuovendo le impurità.
- Colata del metallo: Una volta raggiunte la composizione e la temperatura desiderate, il metallo fuso viene versato in uno stampo o in un crogiolo.
La fusione a induzione sotto vuoto è una tecnica di fusione versatile ed efficiente, utilizzata per un'ampia gamma di applicazioni, tra cui:
- Produzione di metalli di elevata purezza: La fusione a induzione sotto vuoto può produrre metalli con livelli di impurità estremamente bassi.
- Fusione di metalli reattivi: I metalli reattivi all'ossigeno o ad altri gas possono essere fusi sotto vuoto per evitare la contaminazione.
- Produzione di leghe: La fusione a induzione sotto vuoto può essere utilizzata per produrre leghe con composizioni e proprietà precise.
- Riciclaggio dei metalli: La fusione a induzione sotto vuoto può essere utilizzata per riciclare i metalli e rimuovere le impurità.
Vantaggi dei forni fusori a induzione sottovuoto
I forni fusori a induzione sottovuoto (VIM) offrono una moltitudine di vantaggi che li rendono la scelta ideale per diverse applicazioni nell'industria metallurgica. Questi forni operano in condizioni di vuoto, consentendo un controllo preciso dei processi di fusione e solidificazione, ottenendo materiali di alta qualità con proprietà personalizzate. Esploriamo i principali vantaggi dei forni VIM:
Alta purezza e qualità
Uno dei vantaggi più significativi dei forni VIM è la capacità di produrre materiali di elevata purezza e qualità. L'ambiente sotto vuoto elimina il rischio di contaminazione da ossigeno, azoto e altri gas presenti nell'atmosfera. Il risultato è una fusione più pulita e omogenea, priva di inclusioni e impurità dannose che potrebbero influire sulle proprietà meccaniche del materiale.
Atmosfera controllata
Nella camera da vuoto, l'atmosfera è strettamente controllata. Vengono introdotti solo gas specifici a pressioni precise. Questo livello di controllo consente di controllare la composizione chimica del materiale fuso e l'eventuale reattività. Si evitano ossidazioni o reazioni indesiderate con i gas ambientali, garantendo la purezza e la qualità del prodotto finale.
Fusione e raffreddamento rapidi
I forni VIM consentono tassi di fusione e raffreddamento rapidi grazie all'assenza di resistenza dell'aria e all'uso del riscaldamento a induzione. Questo rapido processo di riscaldamento e raffreddamento si traduce in strutture granulari raffinate, proprietà meccaniche migliori e maggiore omogeneità del materiale.
Consumo energetico ridotto
I forni VIM sono altamente efficienti dal punto di vista energetico. L'ambiente sottovuoto riduce al minimo la perdita di calore per convezione e irraggiamento, consentendo un utilizzo più efficiente dell'energia. Inoltre, i rapidi cicli di fusione e raffreddamento riducono il tempo complessivo di lavorazione, riducendo ulteriormente il consumo energetico.
Scalabilità
I forni VIM possono essere progettati e scalati per adattarsi a diverse capacità e requisiti di produzione. Questa flessibilità li rende adatti sia per scopi di ricerca su piccola scala che per la produzione industriale su larga scala. I forni di piccole dimensioni possono essere utilizzati per esperimenti di laboratorio e studi pilota, mentre i forni più grandi possono gestire la produzione di grandi volumi per applicazioni commerciali.
Vantaggi ambientali
I forni VIM offrono alcuni vantaggi ambientali. L'ambiente sottovuoto elimina la necessità di agenti flussanti, riducendo la generazione di rifiuti pericolosi. Inoltre, l'assenza di inquinamento dell'aria e delle scorie durante il processo di fusione contribuisce a un funzionamento più pulito ed ecologico.
In conclusione, i forni fusori a induzione sottovuoto offrono numerosi vantaggi per la produzione di metalli e leghe di alta qualità e purezza. L'ambiente sottovuoto, l'atmosfera controllata, le rapide velocità di fusione e raffreddamento, il ridotto consumo energetico, la scalabilità e i vantaggi ambientali rendono i forni VIM la scelta preferita dell'industria metallurgica.
Applicazioni dei forni fusori a induzione sotto vuoto
I forni di fusione a induzione sottovuoto (VIM) sono strumenti versatili utilizzati in diversi settori, tra cui quello aerospaziale, medico e automobilistico. La loro funzione principale consiste nella lavorazione di leghe specializzate, come le superleghe, le leghe di titanio e gli acciai inossidabili, in cui è fondamentale ottenere prestazioni eccezionali.
Industria aerospaziale
I forni VIM svolgono un ruolo cruciale nell'industria aerospaziale, dove la produzione di componenti ad alte prestazioni per aerei, missili e satelliti richiede l'uso di leghe specializzate. Questi forni consentono la fusione e la colata precisa di superleghe e acciai ad alta resistenza, molti dei quali richiedono la lavorazione sottovuoto a causa della presenza di elementi reattivi come titanio, niobio e alluminio.
Industria medica
Nel settore medico, i forni VIM sono utilizzati per produrre impianti e strumenti chirurgici di alta qualità. La capacità di controllare con precisione il processo di fusione assicura la produzione di leghe con purezza e proprietà meccaniche ottimali, essenziali per garantire la sicurezza e l'efficacia dei dispositivi medici.
Industria automobilistica
L'industria automobilistica utilizza i forni VIM per produrre componenti ad alte prestazioni come ingranaggi, cuscinetti e parti del motore. Questi forni facilitano la produzione di leghe con maggiore durezza, resistenza all'usura e alla fatica, che sono fondamentali per la durata e l'affidabilità dei componenti automobilistici.
Altre applicazioni
Oltre a questi settori primari, i forni VIM trovano applicazione anche nell'industria nucleare per la fusione e la colata di uranio a basso arricchimento in barre di combustibile. Inoltre, sono utilizzati nella produzione di metalli come il titanio e l'alluminio.
Vantaggi dei forni VIM
L'uso dei forni VIM offre diversi vantaggi rispetto alle tecniche di fusione tradizionali:
- Controllo preciso della temperatura: I forni VIM consentono un controllo preciso della temperatura, essenziale per fondere e fondere leghe con proprietà specifiche.
- Ambiente sotto vuoto: L'ambiente sotto vuoto impedisce la contaminazione del metallo fuso e garantisce la produzione di leghe di elevata purezza.
- Migliori proprietà dei materiali: La combinazione di un controllo preciso della temperatura e dell'ambiente sottovuoto consente di ottenere leghe con proprietà meccaniche migliorate, come forza, tenacità e resistenza alla corrosione.
- Efficienza energetica: I forni VIM funzionano a temperature e pressioni inferiori rispetto alle tecniche di fusione tradizionali, con conseguente risparmio energetico.
Conclusioni
I forni di fusione a induzione sottovuoto sono strumenti indispensabili in diversi settori industriali, in quanto consentono la produzione di leghe ad alte prestazioni con proprietà materiali eccezionali. La loro versatilità e la capacità di controllare con precisione il processo di fusione li rendono ideali per le applicazioni in cui qualità e affidabilità sono fondamentali.
Conclusione
I forni fusori a induzione sottovuoto hanno trasformato la lavorazione dei metalli, consentendo la produzione di leghe di elevata purezza con proprietà eccezionali. La loro capacità di controllare le condizioni di vuoto, prevenire la contaminazione e ottenere una precisa regolazione della temperatura li rende strumenti indispensabili per la produzione avanzata e la ricerca. Liberando il potenziale dei materiali specializzati, i forni fusori sottovuoto continuano a guidare l'innovazione e a spingere i confini della scienza dei materiali.
CONTATTATECI PER UNA CONSULENZA GRATUITA
I prodotti e i servizi di KINTEK LAB SOLUTION sono stati riconosciuti da clienti di tutto il mondo. Il nostro personale sarà lieto di assistervi per qualsiasi richiesta. Contattateci per una consulenza gratuita e parlate con uno specialista del prodotto per trovare la soluzione più adatta alle vostre esigenze applicative!