Introduzione all'importanza delle atmosfere dei forni
Le atmosfere dei forni svolgono un ruolo cruciale in vari processi di trattamento termico, come la sinterizzazione e la ricottura. Sono essenziali per prevenire l'ossidazione, ridurre il rischio di contaminazione e migliorare le proprietà dei materiali trattati. Un forno ad atmosfera inerte, ad esempio, è progettato per mantenere un ambiente controllato privo di ossigeno, umidità e altre impurità. Questo tipo di forno è utilizzato in applicazioni che richiedono la lavorazione ad alta temperatura di materiali come ceramiche, metalli e compositi. L'uso di forni ad atmosfera controllata può migliorare la qualità dei materiali, aumentare l'efficienza e ridurre i costi.
Indice dei contenuti
- Introduzione all'importanza delle atmosfere dei forni
- Che cos'è un forno ad atmosfera inerte?
- Uso dei forni ad atmosfera inerte per la sinterizzazione e la ricottura
- Vantaggi dei forni ad atmosfera controllata
- Condizioni ambientali migliorate
- Migliore controllo del forno e produzione efficiente
- Due categorie principali: Forni batch e continui
- Forni ad atmosfera di KINTEK
- Conclusione
Che cos'è un forno ad atmosfera inerte?
Un forno ad atmosfera inerte è un tipo di apparecchiatura da laboratorio utilizzata per i processi di sinterizzazione e ricottura. Fornisce un ambiente controllato e privo di ossigeno, essenziale per alcune applicazioni ad alta temperatura. Inerte significa chimicamente inattivo, motivo per cui le atmosfere inerti sono necessarie per i processi chimici che non richiedono la contaminazione di gas reattivi.
Come funziona un forno ad atmosfera inerte?
I forni ad atmosfera inerte funzionano rimuovendo l'ossigeno e altri gas reattivi dall'ambiente. Ciò si ottiene spurgando il forno con un gas inerte, come azoto o argon. Il forno viene quindi riscaldato alla temperatura desiderata e il materiale da sinterizzare o ricuocere viene posto al suo interno. Il forno viene sigillato per mantenere l'atmosfera inerte, che consente al materiale di subire il processo di riscaldamento e raffreddamento senza ossidazione o altre reazioni chimiche.
Perché un processo richiede un forno ad atmosfera inerte?
Molti processi di trattamento termico richiedono un'atmosfera altamente controllata per ottenere il risultato desiderato. Ad esempio, la sinterizzazione, la ricottura lucida e la carbonitrurazione sono processi utilizzati per la produzione di parti per vari settori industriali. Questi processi richiedono atmosfere altamente controllate per garantire un risultato positivo. Le atmosfere inerti, come quelle create da un forno ad atmosfera inerte, sono necessarie per evitare reazioni chimiche come la decarburazione o l'ossidazione che potrebbero avere un impatto negativo sulla qualità e sulle prestazioni del prodotto finito.
L'importanza dei gas in atmosfera inerte
I gas in atmosfera inerte sono essenziali per creare l'ambiente controllato necessario per i processi di sinterizzazione e ricottura. L'azoto, l'elio e l'argon sono comunemente usati per creare atmosfere inerti perché sono chimicamente stabili e hanno una bassa reattività. Utilizzando questi gas, ricercatori e produttori possono creare un ambiente stabile e privo di ossigeno che consente un controllo preciso del riscaldamento e del raffreddamento dei materiali.
In conclusione, un forno ad atmosfera inerte è un'attrezzatura fondamentale per i ricercatori e i produttori che lavorano con materiali ad alta temperatura. Fornendo un ambiente stabile e privo di ossigeno per i processi di sinterizzazione e ricottura, i forni in atmosfera inerte possono contribuire a ottenere risultati migliori e una produzione più costante.
Uso dei forni ad atmosfera inerte per la sinterizzazione e la ricottura
I forni ad atmosfera inerte sono ampiamente utilizzati nei processi di sinterizzazione e ricottura per creare un ambiente privo di gas reattivi. L'uso di gas inerti, come argon o azoto, crea un'atmosfera stabile e costante che riduce la probabilità di reazioni indesiderate durante il processo di sinterizzazione o ricottura.
Vantaggi dell'utilizzo di forni ad atmosfera inerte
L'uso di forni ad atmosfera inerte offre diversi vantaggi. Uno dei vantaggi più significativi è il miglioramento della qualità del prodotto. Creando un'atmosfera stabile e costante, i forni ad atmosfera inerte possono contribuire a produrre prodotti finali di alta qualità con meno difetti.
Un altro vantaggio è l'aumento dell'efficienza produttiva. I forni in atmosfera inerte possono contribuire a ridurre i tempi di lavorazione e a migliorare la produttività. Ciò si ottiene riducendo al minimo la necessità di rilavorazioni e aumentando la resa di prodotti di alta qualità.
Riduzione della contaminazione e dell'ossidazione
I forni ad atmosfera inerte possono anche ridurre al minimo la contaminazione e l'ossidazione, che possono avere un impatto significativo sulle proprietà finali del prodotto. L'uso di un'atmosfera controllata aiuta a ridurre la probabilità di contaminazione da fonti esterne e previene l'ossidazione del prodotto durante il processo di sinterizzazione o ricottura.
Versatilità nei materiali
I forni ad atmosfera inerte possono essere utilizzati per un'ampia gamma di materiali, tra cui metalli, ceramiche e compositi, il che li rende uno strumento essenziale per molte industrie. La possibilità di utilizzare questi forni per materiali diversi offre ai produttori una maggiore flessibilità nella progettazione e produzione dei prodotti.
Vantaggi dei forni ad atmosfera controllata
I forni ad atmosfera controllata offrono diversi vantaggi ai tecnici di laboratorio, rendendoli uno strumento essenziale nei processi di sinterizzazione e ricottura.
Ambiente su misura per applicazioni specifiche
Uno dei vantaggi più significativi dei forni ad atmosfera controllata è la possibilità di creare un ambiente specifico che può essere adattato a una particolare applicazione. Controllando la composizione del gas, la temperatura e la pressione all'interno del forno, i tecnici di laboratorio possono manipolare le reazioni chimiche che si verificano durante la sinterizzazione e la ricottura, migliorando la qualità e la consistenza del prodotto finale.
Prevenzione dell'ossidazione
I forni ad atmosfera controllata possono essere utilizzati per prevenire l'ossidazione di materiali sensibili, eliminando l'ossigeno dall'ambiente. Ciò riduce il rischio di contaminazione e migliora la purezza del prodotto.
Lavorazione ad alta temperatura
Un altro vantaggio dei forni ad atmosfera controllata è la loro capacità di operare ad alte temperature, offrendo una maggiore flessibilità nei materiali che possono essere lavorati. Questi forni sono comunemente utilizzati nella produzione di ceramiche, metalli e semiconduttori, dove sono necessarie temperature elevate per ottenere le proprietà desiderate.
Controllo preciso per risultati accurati e riproducibili
Il controllo preciso offerto dai forni ad atmosfera controllata consente ai tecnici di laboratorio di ottenere risultati più accurati e riproducibili. Ciò riduce il rischio di errori e migliora la qualità complessiva della ricerca.
Superiore ai forni a cassetta e a bagno di sale
I forni ad atmosfera controllata hanno ormai ampiamente soppiantato i forni a cassetta (carburazione a pacchetto) e a bagno di sale, grazie al fatto che presentano un migliore controllo del forno, una produzione più efficiente e un minore impegno di manodopera. Offrono inoltre condizioni ambientali di funzionamento molto migliorate, senza i gravi problemi di contaminazione del terreno con sali tossici (cianuri) e le difficoltà di smaltimento dei sali di scarto, delle maschere e degli impianti contaminati e degli scarti della carburazione in cassetta.
Nel complesso, i vantaggi dei forni ad atmosfera controllata li rendono uno strumento indispensabile per i laboratori che si occupano di scienza dei materiali, chimica e ingegneria.
Migliori condizioni ambientali
I forni ad atmosfera controllata sono progettati per creare un ambiente in cui i materiali possono essere riscaldati con precisione e senza contaminazioni indesiderate. Uno dei principali vantaggi dell'utilizzo di un forno ad atmosfera controllata è il miglioramento delle condizioni ambientali. Controllando l'atmosfera all'interno del forno, è possibile ridurre la quantità di ossigeno e umidità presente, che può avere un impatto significativo sulla qualità del prodotto finito.
Riduzione dei livelli di ossigeno
Riducendo la quantità di ossigeno presente durante il processo di sinterizzazione o ricottura, è possibile prevenire l'ossidazione, che può portare a un prodotto finale più debole e meno durevole. Quando i livelli di ossigeno sono elevati, possono reagire con molti elementi chimici a temperature diverse, causando l'ossidazione. Con un forno ad atmosfera controllata, i livelli di ossigeno possono essere ridotti per evitare che ciò accada. L'azoto è considerato un gas vettore chimicamente inerte dell'aria e viene spesso utilizzato come gas riducente per evitare l'ossidazione dei materiali nei forni ad alta temperatura. Questo processo di copertura viene realizzato utilizzando ingressi per il gas, come i flussimetri per l'azoto, e una porta di scarico per espellere il gas esaurito dalla camera attraverso una cappa di aspirazione o una tubazione esterna del collettore.
Riduzione dei livelli di umidità
Analogamente, controllando la quantità di umidità presente, è possibile prevenire la formazione di composti chimici indesiderati, che possono influire sulla qualità del prodotto finito. L'umidità può causare reazioni chimiche indesiderate durante il processo di ricottura, che possono influire sulla qualità del prodotto finale. Utilizzando un forno ad atmosfera controllata, è possibile ridurre i livelli di umidità, garantendo un prodotto finale di alta qualità.
Maggiore efficienza e produttività
Oltre a questi vantaggi ambientali, i forni ad atmosfera controllata offrono anche una maggiore efficienza e produttività, oltre a una maggiore flessibilità e controllo sull'intero processo di sinterizzazione o ricottura. Utilizzando un forno ad atmosfera controllata, è possibile creare un ambiente più favorevole al processo di riscaldamento, che può portare a un riscaldamento più rapido ed efficiente. Questo, a sua volta, può contribuire ad aumentare la produttività e a ridurre i costi.
Migliore controllo del forno e produzione efficiente
I forni ad atmosfera controllata (CAF) offrono diversi vantaggi rispetto ai forni tradizionali, tra cui un migliore controllo dell'ambiente del forno e una produzione più efficiente. I CAF sono progettati per funzionare in ambienti con livelli controllati di ossigeno, azoto o altri gas, che possono essere regolati in base alle esigenze specifiche del processo.
Controllo preciso dell'ambiente del forno
Uno dei principali vantaggi dei CAF è la capacità di offrire un controllo preciso dell'ambiente del forno. Questo livello di controllo può portare a una migliore qualità del prodotto, in quanto consente un controllo più preciso del processo di sinterizzazione o ricottura. I CAF possono operare in ambienti con livelli controllati di ossigeno, azoto o altri gas. Questo livello di controllo può portare a una migliore qualità del prodotto, in quanto consente un controllo più preciso del processo di sinterizzazione o ricottura.
Efficienza migliorata
Un altro vantaggio dei CAF è la capacità di lavorare i materiali a temperature più elevate rispetto ai forni tradizionali, il che può portare a tempi di lavorazione più rapidi e a una maggiore efficienza. Un altro vantaggio dei CAF è la capacità di lavorare i materiali a temperature più elevate rispetto ai forni tradizionali, il che può portare a tempi di lavorazione più rapidi e a una maggiore efficienza. Ciò è particolarmente importante per i processi che richiedono una lavorazione ad alta temperatura, come la sinterizzazione e la ricottura.
Riduzione dell'ossidazione
I CAF hanno anche la capacità di ridurre la quantità di ossidazione che si verifica durante il processo di sinterizzazione o ricottura, contribuendo a preservare l'integrità del materiale in lavorazione. Ciò può essere particolarmente importante per i materiali sensibili all'ossidazione, come alcuni metalli o ceramiche.
Qualità costante della produzione
Il controllo preciso dell'ambiente del forno nei CAF consente di ottenere una qualità costante del prodotto, fondamentale per le applicazioni di ricerca e sviluppo e per la produzione industriale. La possibilità di controllare i livelli di ossigeno, azoto o altri gas durante il processo di sinterizzazione o ricottura garantisce che il prodotto finale soddisfi gli standard qualitativi desiderati.
Conclusioni
In conclusione, i CAF offrono una serie di vantaggi rispetto ai forni tradizionali per i processi di sinterizzazione e ricottura. Offrono un migliore controllo dell'ambiente del forno, una maggiore efficienza, una riduzione dell'ossidazione e una qualità costante del prodotto. Questi vantaggi rendono i CAF la scelta ideale per un'ampia gamma di applicazioni, dalla ricerca e sviluppo alla produzione industriale.
Due categorie principali: Forni batch e continui
I forni ad atmosfera controllata sono apparecchiature di laboratorio essenziali utilizzate per i processi di sinterizzazione e ricottura in molte industrie. Esistono due categorie principali di forni ad atmosfera controllata: i forni batch e i forni continui.
Forni batch
I forni a lotti sono adatti per piccole quantità di prodotti; il materiale viene caricato nel forno in un lotto e riscaldato alla temperatura desiderata per un periodo specifico. Il forno a lotti è un forno a camera singola che viene caricato, riscaldato e scaricato come un lotto. La temperatura, la composizione del gas e la pressione sono impostate per l'intero processo batch. Il forno batch è ideale per la produzione e la ricerca su piccola scala ed è anche adatto per materiali che richiedono una temperatura e un'atmosfera specifiche per un periodo specifico.
Forni continui
I forni continui sono invece adatti a grandi quantità di prodotti che richiedono un flusso continuo di materiale attraverso il forno. Nei forni continui, il materiale viene caricato a un'estremità e trasportato attraverso il forno da un sistema di trasporto. Il sistema di trasporto è progettato per fornire un flusso continuo di materiale attraverso il forno. La temperatura, la composizione del gas e la pressione sono controllate durante l'intero processo. I forni continui sono ideali per la produzione di grandi volumi e sono comunemente utilizzati nell'industria automobilistica, aerospaziale ed elettronica.
Sia i forni discontinui che quelli continui offrono diversi vantaggi. I forni ad atmosfera controllata possono migliorare notevolmente la qualità del prodotto finale. I vantaggi derivanti dall'utilizzo di questi forni includono la riduzione dell'ossidazione, il miglioramento delle proprietà dei materiali e l'aumento della resa dei prodotti. I forni ad atmosfera controllata possono anche migliorare l'uniformità del prodotto, ridurre il consumo energetico e minimizzare la contaminazione e gli scarti.
In conclusione, i forni ad atmosfera controllata svolgono un ruolo fondamentale in diversi settori industriali e offrono una serie di vantaggi per i processi di sinterizzazione e ricottura. La scelta tra forni batch e forni continui dipende dalle esigenze specifiche dell'industria o del laboratorio. Il forno batch è adatto alla produzione su piccola scala e alla ricerca, mentre il forno continuo è ideale per la produzione di grandi volumi. Entrambi i tipi di forno sono progettati per fornire un ambiente controllato che migliora le proprietà dei materiali e riduce al minimo l'ossidazione.
Forni ad atmosfera di KINTEK
I forni ad atmosfera sono essenziali per i processi di sinterizzazione e ricottura in laboratorio. KINTEK, produttore leader di attrezzature da laboratorio, offre forni ad atmosfera che forniscono un ambiente controllato con precisione per i processi di sinterizzazione e ricottura, per garantire risultati della massima qualità possibile.
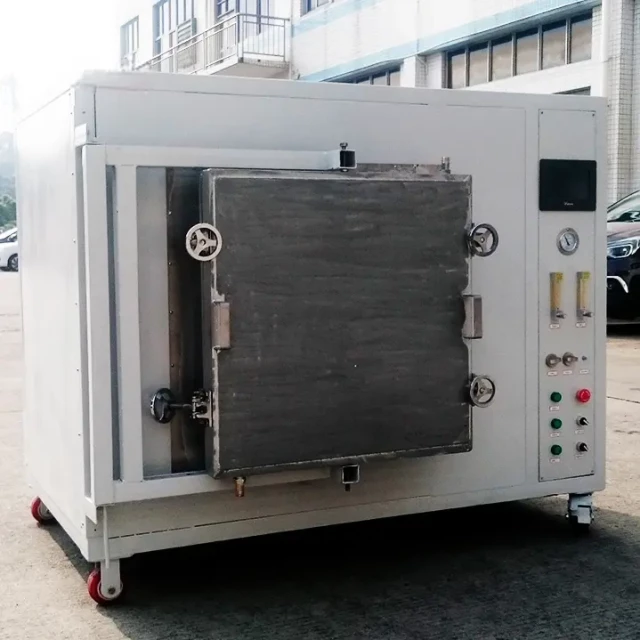
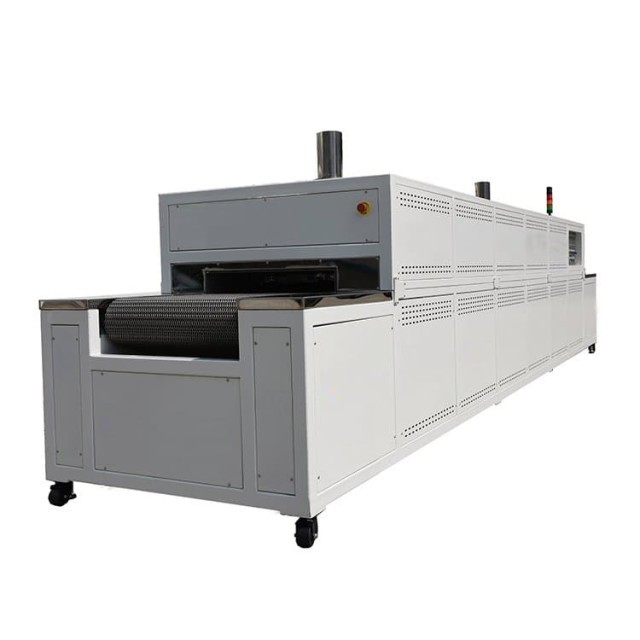
Caratteristiche dei forni ad atmosfera KINTEK
I forni ad atmosfera KINTEK sono progettati per soddisfare le specifiche del cliente. Questi forni hanno una gamma di dimensioni delle zone di riscaldamento e di intervalli di temperatura di lavoro (1100°C, 1300°C e 1600°C), che li rendono ideali per l'uso in una vasta gamma di applicazioni, dalla metallurgia e dalla scienza dei materiali alla lavorazione dei semiconduttori e alla produzione di elettronica.
Atmosfera controllata
I forni ad atmosfera funzionano controllando l'ambiente in cui i campioni vengono riscaldati, creando un'atmosfera specifica che può influenzare in modo significativo le proprietà finali del materiale in lavorazione. I forni ad atmosfera di KINTEK sono dotati di diverse caratteristiche brevettate che consentono una migliore miscelazione, con conseguente miglioramento del trasferimento di calore e di massa. L'assenza di parti mobili nel sistema di supporto del tubo offre un design semplice, affidabile e robusto che migliora la scalabilità. Inoltre, l'azione di rotolamento del prodotto all'interno del tubo determina un elevato grado di uniformità della temperatura e di contatto gas-solido, producendo un prodotto più omogeneo, riducendo i tempi di lavorazione e aumentando i tassi di produzione.
Atmosfere di processo
I forni ad atmosfera di KINTEK possono adattarsi a una varietà di atmosfere di processo. Gli eccellenti progetti di tenuta e l'attenzione al controllo dell'atmosfera includono l'integrazione di sistemi di riciclo dell'atmosfera, sistemi di abbattimento dei gas di scarico e miscelazione controllata dell'atmosfera per un controllo di processo personalizzato. Queste atmosfere includono gas infiammabili e tossici come idrogeno, azoto, argon, aria, ossigeno, etilene, metano, CO2, CO e cloro gassoso.
Personalizzazione
KINTEK affronta la progettazione di un forno ad atmosfera come un sistema completo, con la possibilità di incorporare sistemi di controllo del processo, trattamento e gestione dei gas, installazione chiavi in mano e messa in funzione completa sul campo. L'azienda offre anche forni da laboratorio ad alta temperatura personalizzati, che garantiscono un eccellente controllo e uniformità della temperatura e un'ottima efficienza energetica. Questi forni possono essere modificati a partire da un modello standard o costruiti secondo le specifiche del cliente.
In conclusione, i forni ad atmosfera di KINTEK sono una scelta eccellente per qualsiasi laboratorio che voglia migliorare la qualità e la coerenza del proprio lavoro. Questi forni offrono un ambiente controllato con precisione per i processi di sinterizzazione e ricottura, riducendo l'ossidazione, controllando la formazione di fasi e migliorando la qualità complessiva e la coerenza del prodotto finale.
Conclusioni
In conclusione, i forni ad atmosfera controllata sono diventati parte integrante dei processi di sinterizzazione e ricottura grazie alla loro capacità di creare un ambiente inerte che previene l'ossidazione, riduce la contaminazione e migliora la qualità del prodotto finale. Offrono condizioni ambientali migliori, un migliore controllo del forno, una produttività efficiente e un livello di sicurezza più elevato rispetto ai forni tradizionali. KINTEK offre un'ampia gamma di forni ad atmosfera controllata, progettati per soddisfare le esigenze di diversi settori industriali. Investire in un forno ad atmosfera controllata può aiutare le aziende a risparmiare tempo, ridurre i costi e produrre prodotti di alta qualità conformi agli standard industriali.
CONTATTATECI PER UNA CONSULENZA GRATUITA
I prodotti e i servizi di KINTEK LAB SOLUTION sono stati riconosciuti da clienti di tutto il mondo. Il nostro personale sarà lieto di assistervi per qualsiasi richiesta. Contattateci per una consulenza gratuita e parlate con uno specialista del prodotto per trovare la soluzione più adatta alle vostre esigenze applicative!