La temperatura di cottura dell'allumina, un parametro chiave nella sua lavorazione, è tipicamente intorno a 1350°C per ottenere strutture ad alta densità e a grana fine, come dimostra il riferimento che afferma che i compatti di polvere di allumina pura cotti a questa temperatura per 20 minuti raggiungono il 99% della densità teorica con una dimensione dei grani di 1,2 μm.L'allumina, o ossido di alluminio (Al2O3), è un materiale ceramico versatile noto per la sua resistenza alle alte temperature, la forza meccanica e la stabilità chimica, che lo rendono adatto alle applicazioni industriali più esigenti.Il suo punto di fusione è di circa 2000°C, ma la temperatura di cottura è inferiore, in quanto è ottimizzata per la sinterizzazione e la densificazione durante la lavorazione.Questa temperatura garantisce l'integrità strutturale del materiale e le proprietà desiderate, come la resistenza all'usura, la conduttività termica e la resistenza alla corrosione, che sono fondamentali per applicazioni come crogioli, isolanti elettrici e componenti ad alta temperatura.
Punti chiave spiegati:
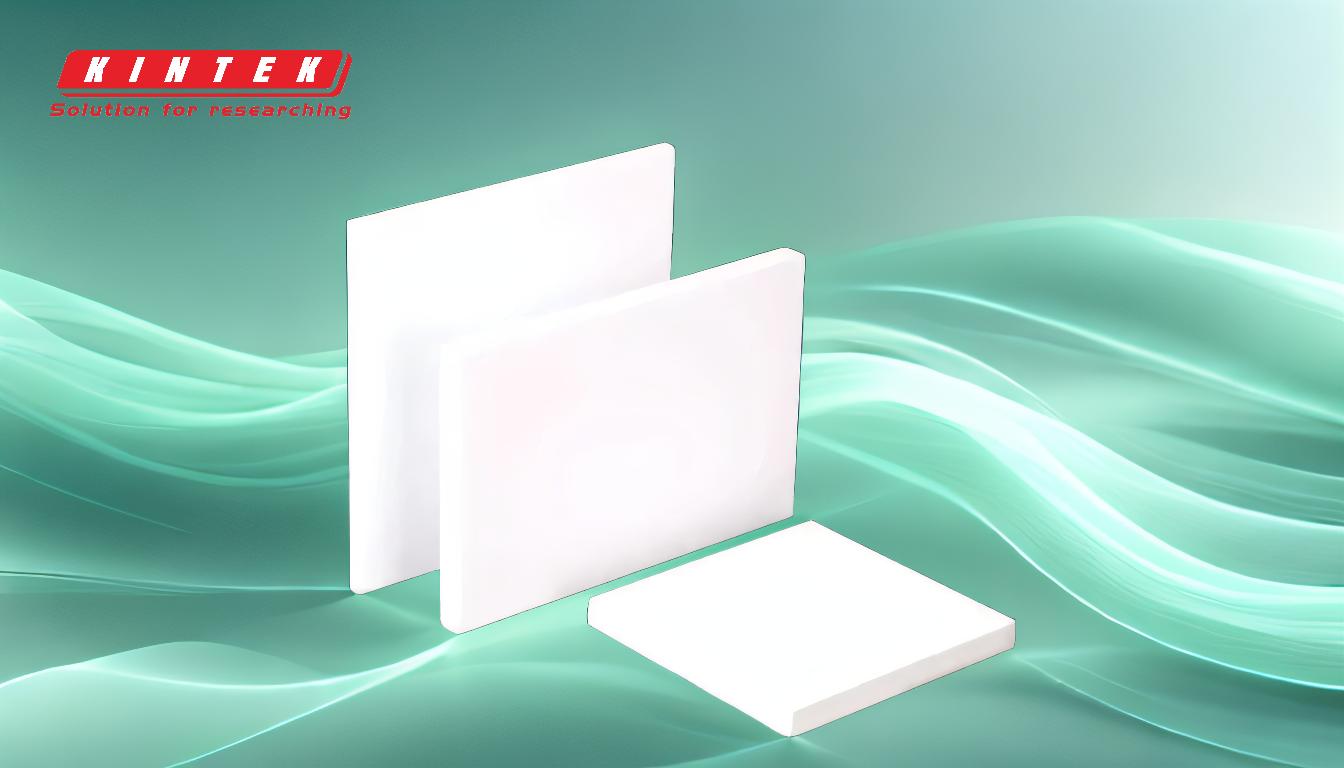
-
Temperatura di cottura dell'allumina:
- La temperatura di cottura dell'allumina è tipicamente di 1350°C come dimostrato nella referenza in cui i compatti di polvere di allumina pura raggiungono il 99% della densità teorica e una dimensione dei grani di 1,2 μm quando vengono cotti a questa temperatura per 20 minuti.
- Questa temperatura è fondamentale per la sinterizzazione, un processo che densifica il materiale legando le particelle tra loro senza fonderle completamente.
-
Proprietà dell'allumina alle alte temperature:
- L'allumina è nota per la sua stabilità alle alte temperature con un punto di fusione di circa 2000°C .Questo lo rende adatto alle applicazioni che richiedono una resistenza al calore estremo.
- La sua conducibilità termica (circa 3000 W/m-K) e il coefficiente di espansione termica gli consentono di sopportare elevate pressioni interne e shock termici, rendendolo ideale per l'uso in crogioli e altri ambienti ad alta temperatura.
-
Importanza della temperatura di cottura nella lavorazione:
- La temperatura di cottura è inferiore al punto di fusione per garantire una sinterizzazione e una densificazione adeguate.A 1350°C, l'allumina raggiunge una densità e una struttura dei grani ottimali, fondamentali per le sue proprietà meccaniche e termiche.
- Un surriscaldamento o un surriscaldamento insufficiente durante la cottura può portare a difetti come porosità o densificazione incompleta, compromettendo le prestazioni del materiale.
-
Applicazioni dell'allumina:
- La resistenza alle alte temperature e la forza meccanica dell'allumina la rendono adatta a crogioli , isolanti elettrici e componenti in forni ad alta temperatura .
- La sua resistenza chimica e l'inerzia biologica lo rendono ideale anche per l'impiego in ambienti corrosivi e in applicazioni mediche.
-
Confronto con altri materiali:
- L'allumina è più dura di materiali come il ferro o la grafite, con una resistenza all'usura e una conducibilità termica superiori.Questo la rende una scelta preferenziale per le applicazioni industriali più impegnative.
- Il suo elevato coefficiente di espansione termica gli consente di gestire meglio le sollecitazioni termiche rispetto a molte altre ceramiche.
-
Presenza naturale e lavorazione:
- L'allumina deriva dall'ossido di alluminio, che costituisce circa il 15% della crosta terrestre.Viene estratto dai minerali presenti in natura e raffinato in materiali ceramici attraverso processi come la sinterizzazione a temperature controllate.
Conoscendo la temperatura di cottura e il suo ruolo nella lavorazione dell'allumina, i produttori possono ottimizzare le proprietà del materiale per applicazioni specifiche, garantendo durata e prestazioni in ambienti corrosivi e ad alta temperatura.
Tabella riassuntiva:
Aspetto chiave | Dettagli |
---|---|
Temperatura di cottura | 1350°C per 20 minuti per ottenere una densità teorica del 99% e una granulometria di 1,2 μm. |
Punto di fusione | ~2000°C |
Proprietà chiave | Stabilità alle alte temperature, resistenza all'usura, conducibilità termica |
Applicazioni | Crogioli, isolanti elettrici, componenti ad alta temperatura |
Importanza della lavorazione | Assicura sinterizzazione, densificazione e integrità strutturale |
Ottimizzate la lavorazione dell'allumina contattate i nostri esperti oggi stesso !