La calcinazione e la sinterizzazione sono entrambi processi termici utilizzati in metallurgia e nella scienza dei materiali, ma hanno scopi diversi e operano in condizioni diverse.La calcinazione comporta il riscaldamento di un materiale, tipicamente un minerale metallico, in presenza di aria o ossigeno per rimuovere impurità come carbonio, acqua o altre sostanze volatili.La sinterizzazione, invece, prevede il riscaldamento di materiali metallici o ceramici in polvere al di sotto del loro punto di fusione per fondere insieme le particelle, creando un oggetto solido con proprietà meccaniche migliorate.Sebbene entrambi i processi avvengano a temperature inferiori al punto di fusione del materiale, i loro obiettivi e risultati differiscono notevolmente.La calcinazione è principalmente un processo di purificazione, mentre la sinterizzazione è un processo di consolidamento volto a migliorare la resistenza e l'integrità del materiale.
Punti chiave spiegati:
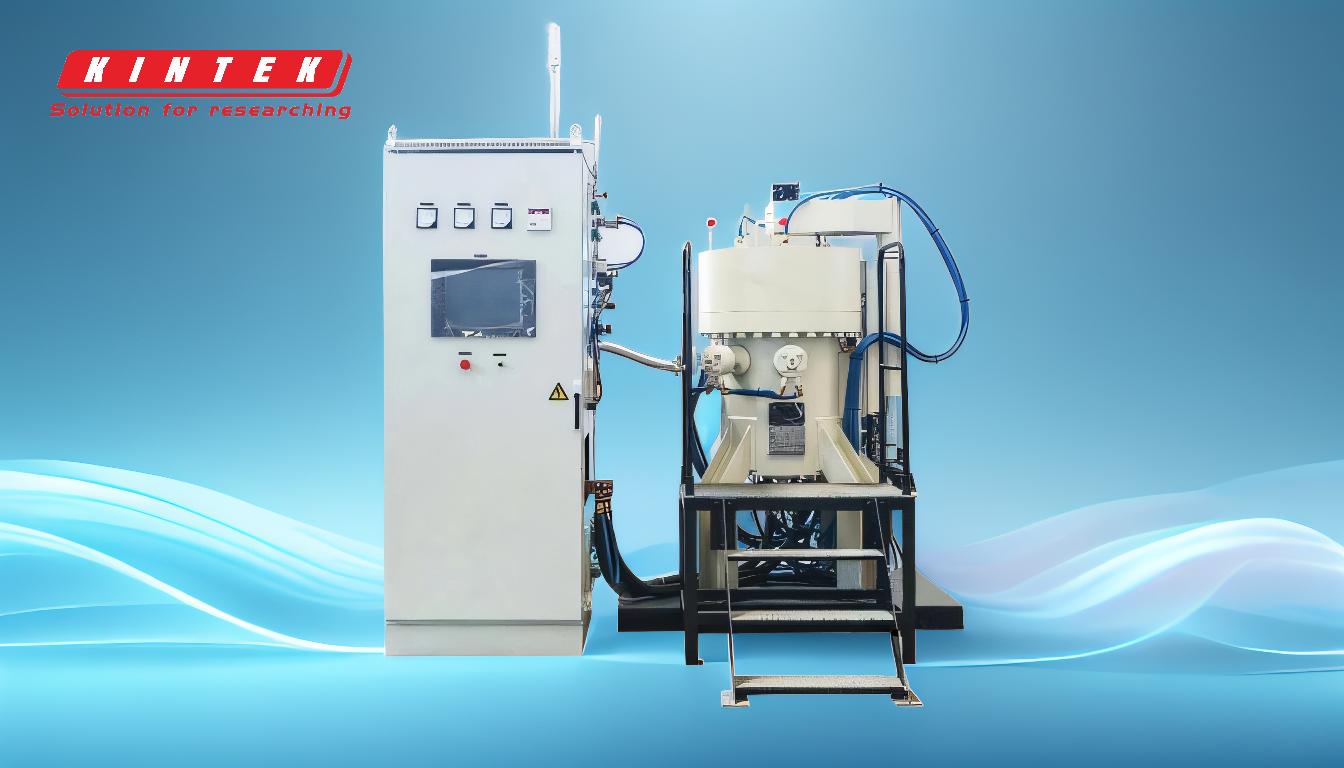
-
Definizione e scopo:
- Calcinazione:Processo termico in cui un materiale (solitamente un minerale metallico) viene riscaldato in presenza di aria o ossigeno per rimuovere impurità come carbonio, acqua o altri composti volatili.L'obiettivo è la purificazione.
- Sinterizzazione:Un processo termico in cui i materiali metallici o ceramici in polvere vengono riscaldati al di sotto del loro punto di fusione per fondere insieme le particelle, formando un oggetto solido.L'obiettivo è il consolidamento e il miglioramento delle proprietà del materiale.
-
Intervallo di temperatura:
- Entrambi i processi avvengono a temperature inferiori al punto di fusione del materiale da lavorare.
- La calcinazione comporta in genere temperature più basse rispetto alla sinterizzazione, poiché il suo obiettivo principale è quello di eliminare le impurità piuttosto che fondere le particelle.
-
Cambiamenti chimici e fisici:
- Calcinazione:Comporta principalmente cambiamenti chimici, come la decomposizione dei carbonati o l'ossidazione delle impurità.
- Sinterizzazione:Comporta principalmente cambiamenti fisici, in cui le particelle si legano tra loro attraverso la diffusione e la crescita dei grani senza fusione.
-
Applicazioni:
- Calcinazione:Comunemente utilizzata nella produzione di cemento, calce e allumina, dove è necessario rimuovere le impurità per ottenere la composizione chimica desiderata.
- Sinterizzazione:Ampiamente utilizzato nella metallurgia delle polveri e nella ceramica per produrre componenti ad alta resistenza, densità e precisione dimensionale.
-
Attrezzatura:
- Forno di calcinazione:Progettato per fornire un riscaldamento controllato in un'atmosfera ossidante, spesso con funzioni di gestione dei gas di scarico e delle impurità.
- Forno di sinterizzazione:Progettati per fornire un riscaldamento uniforme e un raffreddamento controllato, spesso con funzioni per mantenere un'atmosfera specifica (ad esempio, gas inerte) per prevenire l'ossidazione o la contaminazione.
-
Risultato:
- Calcinazione:Si ottiene un materiale purificato con un contenuto ridotto di impurità, spesso in uno stato più friabile o poroso.
- Sinterizzazione:Si ottiene un oggetto denso e solido con proprietà meccaniche migliorate, come forza, durezza e resistenza all'usura.
-
Stato del materiale:
- Calcinazione:In genere si parte da un materiale sfuso o da un minerale, che può essere frantumato o macinato prima del riscaldamento.
- Sinterizzazione:Inizia con materiale in polvere, che viene compattato nella forma desiderata prima del riscaldamento.
-
Controllo dell'atmosfera:
- Calcinazione:Spesso richiede un'atmosfera ossidante per facilitare la rimozione delle impurità.
- Sinterizzazione:Può richiedere un'atmosfera controllata (ad esempio, gas inerte o vuoto) per evitare l'ossidazione o la contaminazione durante il processo di incollaggio.
-
Post-lavorazione:
- Calcinazione:Il materiale ottenuto può richiedere ulteriori lavorazioni, come la macinazione o l'ulteriore raffinazione, a seconda dell'applicazione.
- Sinterizzazione:Il prodotto sinterizzato ha spesso una forma quasi netta e può richiedere una post-lavorazione minima, come la lavorazione o la finitura superficiale.
-
Rilevanza per l'industria:
- Calcinazione:Critica in settori quali la produzione di cemento, la raffinazione dei metalli e la produzione chimica.
- Sinterizzazione:Essenziale in settori come quello automobilistico, aerospaziale ed elettronico per la produzione di componenti ad alte prestazioni.
La comprensione di queste differenze chiave aiuta a selezionare il processo e l'apparecchiatura appropriati per le specifiche esigenze di lavorazione dei materiali, garantendo risultati ottimali in termini di purezza, resistenza e funzionalità.
Tabella riassuntiva:
Aspetto | Calcinazione | Sinterizzazione |
---|---|---|
Scopo | Purificazione dei materiali attraverso la rimozione delle impurità. | Consolidamento di materiali in polvere per migliorarne la resistenza e l'integrità. |
Intervallo di temperatura | Temperature inferiori, al di sotto del punto di fusione del materiale. | Temperature più elevate, sempre al di sotto del punto di fusione del materiale. |
Cambiamenti | Principalmente cambiamenti chimici (ad esempio, decomposizione, ossidazione). | Principalmente cambiamenti fisici (ad esempio, legame delle particelle attraverso la diffusione). |
Applicazioni | Produzione di cemento, calce e allumina. | Metallurgia delle polveri, ceramica, industria automobilistica, aerospaziale ed elettronica. |
Apparecchiatura | Forno di calcinazione con atmosfera ossidante. | Forno di sinterizzazione con atmosfera controllata (ad esempio, gas inerte o vuoto). |
Risultato | Materiale purificato con impurità ridotte, spesso poroso. | Oggetto denso e solido con proprietà meccaniche migliorate. |
Stato del materiale | Inizia con materiale sfuso o minerale. | Inizia con materiale in polvere, compattato prima del riscaldamento. |
Controllo dell'atmosfera | Atmosfera ossidante per rimuovere le impurità. | Atmosfera controllata per prevenire l'ossidazione o la contaminazione. |
Post-lavorazione | Può richiedere una rettifica o un'ulteriore rifinitura. | Spesso la forma è quasi a rete e la post-elaborazione è minima. |
Rilevanza industriale | Produzione di cemento, raffinazione dei metalli, produzione chimica. | Industria automobilistica, aerospaziale, elettronica per componenti ad alte prestazioni. |
Avete bisogno di aiuto per scegliere il processo o l'apparecchiatura giusta per la vostra lavorazione dei materiali? Contattate oggi stesso i nostri esperti per una guida personalizzata!