Nel contesto dei forni, una storta si riferisce a una camera o recipiente sigillato utilizzato in ambienti industriali o di laboratorio per eseguire processi che richiedono ambienti controllati, come il trattamento termico, le reazioni chimiche o la lavorazione dei materiali. La storta è progettata per isolare il materiale in lavorazione da contaminanti esterni, garantendo un controllo preciso su temperatura, pressione e atmosfera. Questa configurazione è particolarmente utile in applicazioni come ricottura, brasatura, sinterizzazione o altri processi termici in cui è necessario evitare contaminazione o ossidazione. Le storte sono comunemente utilizzate in settori quali la metallurgia, la ceramica e la produzione di semiconduttori.
Punti chiave spiegati:
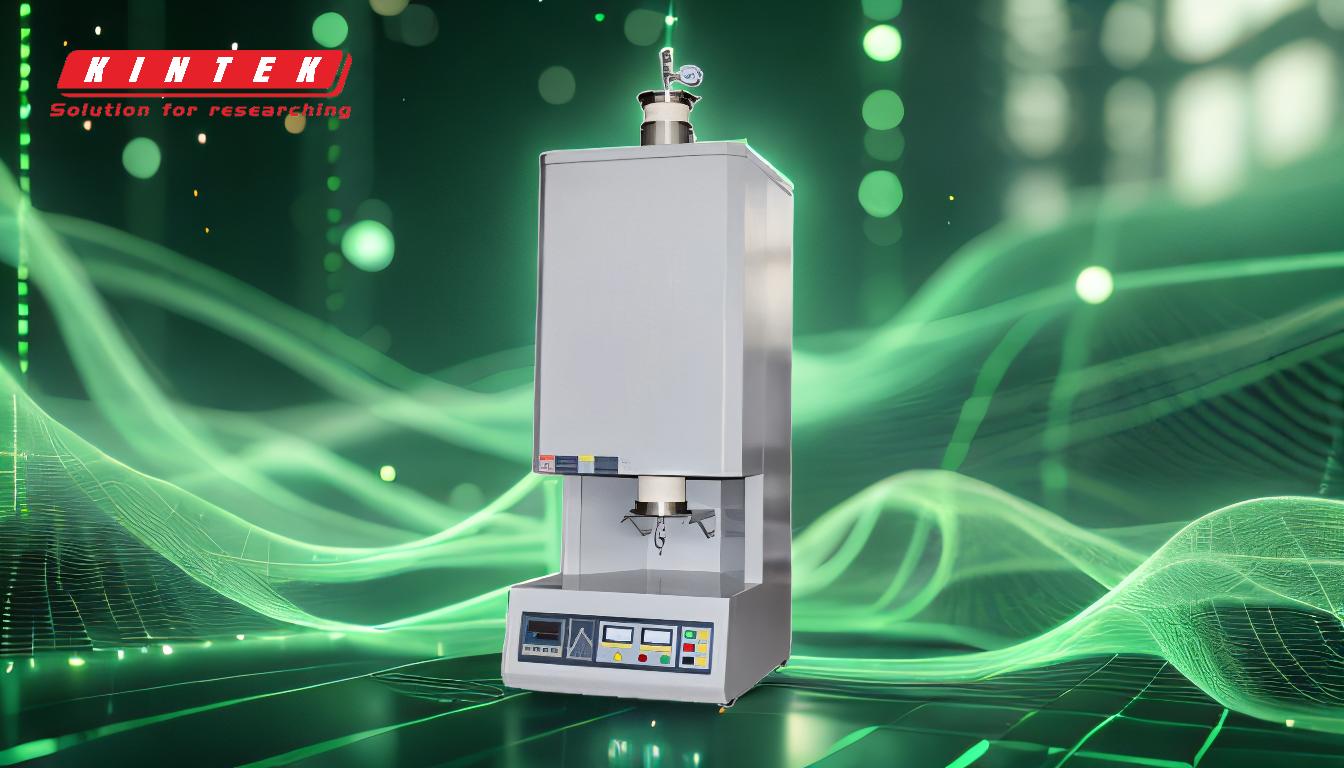
-
Definizione di storta nei forni:
- Una storta è una camera o recipiente sigillato integrato in un forno per creare un ambiente isolato per la lavorazione dei materiali. È spesso realizzato con materiali come acciaio inossidabile, ceramica o altre leghe che possono resistere alle alte temperature e alle atmosfere corrosive. La storta garantisce che il materiale all'interno sia protetto da contaminanti esterni, come ossigeno o umidità, che potrebbero interferire con il processo.
-
Scopo di una replica:
-
Lo scopo principale di una storta è fornire un ambiente controllato per i processi che richiedono condizioni atmosferiche specifiche. Per esempio:
- Trattamento termico: Le storte vengono utilizzate in processi come la ricottura, in cui i metalli vengono riscaldati e raffreddati per alterarne le proprietà senza ossidazione.
- Brasatura: Un forno a storta può creare un ambiente privo di ossigeno per prevenire l'ossidazione durante l'unione dei metalli.
- Sinterizzazione: Nella metallurgia delle polveri, le storte vengono utilizzate per compattare e fondere materiali in polvere senza contaminazione.
-
Lo scopo principale di una storta è fornire un ambiente controllato per i processi che richiedono condizioni atmosferiche specifiche. Per esempio:
-
Tipi di storte:
-
Le storte possono variare nel design e nel materiale a seconda dell'applicazione:
- Repliche batch: Utilizzato per la lavorazione di materiali in lotti discreti, spesso in operazioni su scala ridotta.
- Repliche continue: Progettato per la lavorazione continua, in cui i materiali si muovono attraverso la storta in modo controllato, ideale per applicazioni industriali su larga scala.
- Storte specifiche per il materiale: Alcune storte sono realizzate su misura per materiali specifici, come quelli utilizzati nell'industria dei semiconduttori per la lavorazione dei wafer di silicio.
-
Le storte possono variare nel design e nel materiale a seconda dell'applicazione:
-
Controllo dell'atmosfera nelle storte:
-
Le storte sono spesso dotate di sistemi per il controllo dell'atmosfera interna. Ciò può includere:
- Gas Inerti: L'azoto o l'argon vengono utilizzati per creare un ambiente privo di ossigeno.
- Sistemi di vuoto: Alcune storte funzionano in condizioni di vuoto per eliminare eventuali contaminanti gassosi.
- Gas reattivi: In alcuni processi vengono introdotti gas come l'idrogeno o l'anidride carbonica per facilitare reazioni chimiche specifiche.
-
Le storte sono spesso dotate di sistemi per il controllo dell'atmosfera interna. Ciò può includere:
-
Applicazioni dei forni a storte:
-
I forni a storta sono ampiamente utilizzati in vari settori:
- Metallurgia: Per processi come l'indurimento, il rinvenimento e la ricottura dei metalli.
- Ceramica: Per la sinterizzazione di materiali ceramici per ottenere elevata resistenza e densità.
- Produzione di semiconduttori: Per processi come la diffusione e l'ossidazione dei wafer di silicio.
- Elaborazione chimica: Per reazioni che richiedono un controllo preciso della temperatura e dell'atmosfera.
-
I forni a storta sono ampiamente utilizzati in vari settori:
-
Vantaggi dell'utilizzo di una storta:
- Prevenzione della contaminazione: L'ambiente sigillato previene l'ossidazione e la contaminazione, garantendo risultati di alta qualità.
- Controllo di precisione: Le storte consentono un controllo preciso della temperatura, della pressione e dell'atmosfera, che è fondamentale per molti processi industriali.
- Versatilità: Le storte possono essere adattate per un'ampia gamma di applicazioni, rendendole uno strumento prezioso in molti settori.
-
Sfide e considerazioni:
-
Sebbene le storte offrano molti vantaggi, ci sono anche delle sfide:
- Costo: I forni a storte possono essere costosi a causa dei materiali e dei sistemi specializzati richiesti.
- Manutenzione: La natura sigillata delle storte implica che richiedono una manutenzione regolare per garantirne l'integrità e le prestazioni.
- Consumo energetico: I forni a storte spesso consumano una quantità significativa di energia, soprattutto nelle applicazioni ad alta temperatura.
-
Sebbene le storte offrano molti vantaggi, ci sono anche delle sfide:
Comprendendo il ruolo e la funzionalità di una storta nei forni, le industrie possono sfruttare meglio questa tecnologia per ottenere una lavorazione dei materiali precisa e priva di contaminazioni.
Tabella riassuntiva:
Aspetto | Dettagli |
---|---|
Definizione | Camera stagna per l'isolamento di materiali in ambienti controllati. |
Scopo | Previene la contaminazione, garantisce un controllo preciso della temperatura e dell'atmosfera. |
Tipi | Batch, continuo, specifico per il materiale. |
Controllo dell'atmosfera | Gas inerti, sistemi da vuoto, gas reattivi. |
Applicazioni | Metallurgia, ceramica, produzione di semiconduttori, lavorazione chimica. |
Vantaggi | Prevenzione della contaminazione, controllo di precisione, versatilità. |
Sfide | Costi elevati, esigenze di manutenzione, consumo di energia. |
Pronti a potenziare i vostri processi industriali con i forni a storte? Contattaci oggi per saperne di più!