Il magnetron sputtering è una tecnica di deposizione di film sottili ampiamente utilizzata e il suo successo dipende dall'ottimizzazione di diversi parametri critici.Questi parametri includono la densità di potenza del target, la pressione del gas, la temperatura del substrato, la velocità di deposizione e fattori geometrici come la distanza target-substrato.Inoltre, i parametri del plasma, come l'energia degli ioni e il riscaldamento degli elettroni, svolgono un ruolo significativo nel determinare la qualità e l'uniformità del film.Anche la scelta del sistema di erogazione della potenza (CC, RF o CC pulsata) influenza il processo.Regolando attentamente questi parametri, è possibile ottenere le proprietà desiderate del film, come uniformità, adesione e densità, riducendo al minimo difetti e danni.
Spiegazione dei punti chiave:
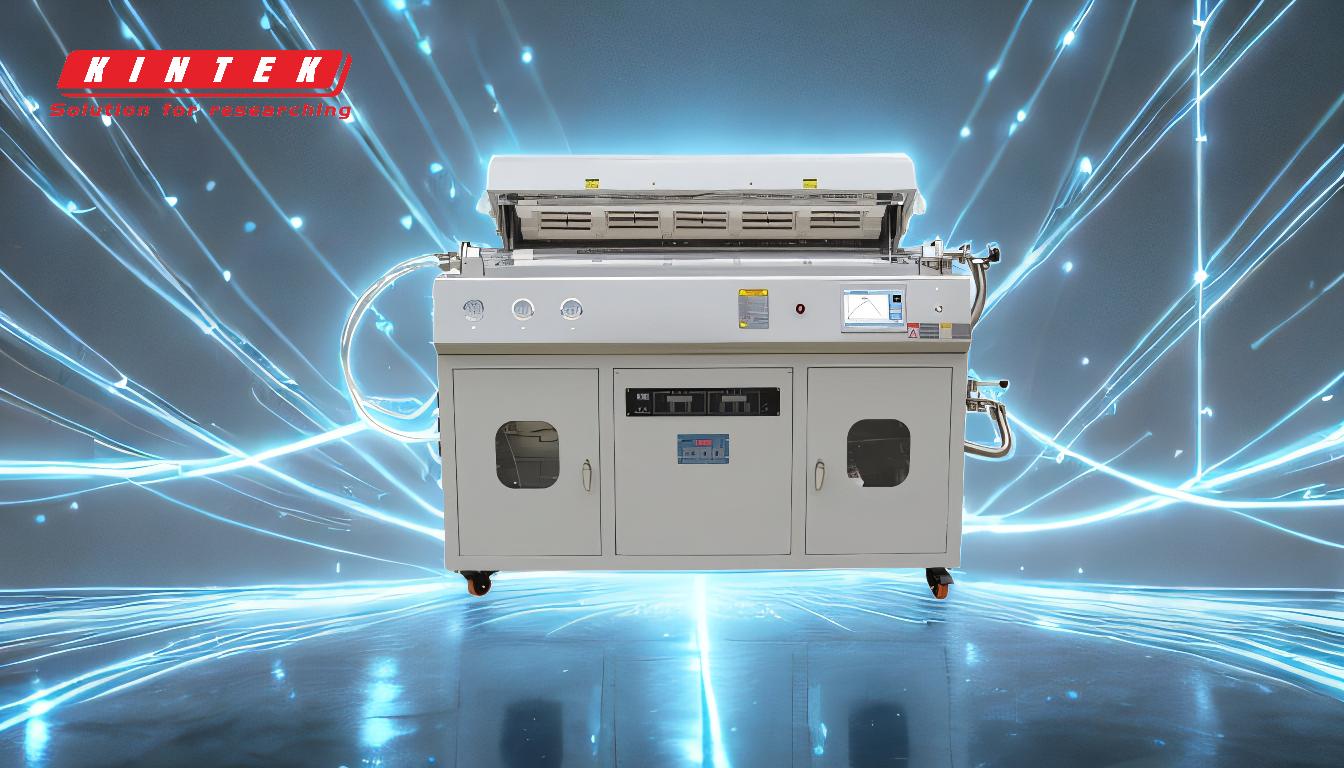
-
Densità di potenza target:
- La densità di potenza del target influisce direttamente sulla velocità di sputtering e sull'energia degli atomi espulsi.Densità di potenza più elevate aumentano il numero di ioni nel plasma, portando a un tasso di deposizione più elevato.
- Tuttavia, una densità di potenza eccessiva può causare il surriscaldamento o il danneggiamento del materiale bersaglio, quindi deve essere ottimizzata per bilanciare la velocità di deposizione e la qualità del film.
-
Pressione del gas:
- La pressione del gas influisce sul percorso libero medio degli atomi e degli ioni polverizzati.Le pressioni più basse determinano un minor numero di collisioni, consentendo agli atomi di raggiungere il substrato con una maggiore energia, il che migliora la densità e l'adesione del film.
- Pressioni più elevate possono migliorare l'uniformità, ma possono ridurre la densità del film a causa dell'aumento della dispersione delle particelle polverizzate.
-
Temperatura del substrato:
- La temperatura del substrato influisce sulla microstruttura del film, sull'adesione e sulle sollecitazioni.Le temperature più elevate favoriscono una migliore mobilità atomica, che porta a film più densi e uniformi.
- Tuttavia, temperature eccessive possono causare diffusione indesiderata o cambiamenti di fase nel film o nel substrato.
-
Velocità di deposizione:
- La velocità di deposizione è influenzata dalla densità di potenza del target, dalla pressione del gas e dal materiale del target.Una velocità di deposizione più elevata è auspicabile per la produttività, ma deve essere bilanciata con la qualità del film.
- Se non viene controllata correttamente, una velocità di deposizione elevata può portare a difetti o a una scarsa adesione.
-
Parametri geometrici:
- Distanza bersaglio-substrato:Questa distanza influisce sull'uniformità del film e sull'energia degli atomi depositati.Una distanza inferiore può aumentare la velocità di deposizione, ma può portare a film non uniformi a causa di effetti di ombreggiamento.
- Area di erosione target:Il profilo di erosione del bersaglio influisce sulla distribuzione del materiale polverizzato.Un profilo di erosione uniforme garantisce proprietà uniformi del film.
-
Parametri del plasma:
- Energia ionica:Le energie ioniche più elevate migliorano la densità e l'adesione del film, ma possono anche causare danni al substrato se troppo elevate.
- Riscaldamento degli elettroni e creazione di elettroni secondari:Questi processi sostengono il plasma e influenzano la generazione di ioni, che è fondamentale per uno sputtering efficiente.
-
Sistema di alimentazione:
-
La scelta del sistema di erogazione dell'energia (CC, RF o CC pulsata) influisce sulla stabilità del plasma, sull'energia degli ioni e sulla velocità di deposizione.Ad esempio:
- Sputtering Magnetron DC:Adatto per bersagli conduttivi ma non per materiali isolanti.
- RF Magnetron Sputtering:Ideale per bersagli isolanti grazie alla sua capacità di prevenire l'accumulo di carica.
- Sputtering DC pulsato:Riduce gli archi e migliora la qualità del film nei processi di sputtering reattivo.
-
La scelta del sistema di erogazione dell'energia (CC, RF o CC pulsata) influisce sulla stabilità del plasma, sull'energia degli ioni e sulla velocità di deposizione.Ad esempio:
-
Vuoto di base e pressione del gas di sputtering:
- Un alto vuoto di base garantisce un ambiente pulito, riducendo al minimo la contaminazione.
- La pressione del gas di sputtering (solitamente argon) deve essere ottimizzata per bilanciare la densità del plasma e l'efficienza dello sputtering.
-
Uniformità e qualità del film:
- L'uniformità è influenzata dalla distanza target-substrato, dalla pressione del gas e dall'area di erosione del target.
- La qualità del film può essere migliorata ottimizzando l'energia degli ioni, la temperatura del substrato e la velocità di deposizione per ridurre al minimo i difetti e migliorare l'adesione.
Controllando attentamente questi parametri, la deposizione di film sottili tramite sputtering magnetronico permette di ottenere film uniformi e di alta qualità con proprietà personalizzate per varie applicazioni.
Tabella riassuntiva:
Parametro | Impatto sulla qualità della pellicola |
---|---|
Densità di potenza del target | Influisce sulla velocità di sputtering e sull'energia degli atomi espulsi; un'alta densità aumenta la velocità di deposizione. |
Pressione del gas | Influenza il percorso libero medio degli atomi; una pressione più bassa migliora la densità e l'adesione. |
Temperatura del substrato | Le temperature più elevate aumentano la mobilità atomica, dando luogo a film più densi e uniformi. |
Velocità di deposizione | Tassi più elevati aumentano la produttività, ma devono essere bilanciati per evitare difetti. |
Distanza target-substrato | Distanze più brevi aumentano la velocità di deposizione ma possono ridurre l'uniformità. |
Energia ionica | Migliora la densità del film e l'adesione, ma può danneggiare i substrati se troppo elevata. |
Sistema di alimentazione | DC, RF o DC pulsata influisce sulla stabilità del plasma e sulla velocità di deposizione. |
Vuoto di base | Garantisce un ambiente pulito, riducendo al minimo la contaminazione. |
Uniformità del film | Influenzata dalla distanza target-substrato, dalla pressione del gas e dall'area di erosione del target. |
Ottimizzate il vostro processo di sputtering magnetronico per ottenere risultati superiori. contattate i nostri esperti oggi stesso !