La calcinazione non avviene in genere in un altoforno. Viene invece effettuata principalmente in forni specializzati come i forni a riverbero o i forni rotativi, progettati per fornire condizioni di riscaldamento controllate al di sotto del punto di fusione del materiale. La calcinazione prevede il riscaldamento dei materiali in assenza o con un apporto limitato di aria per indurre la decomposizione termica, rimuovere le sostanze volatili o provocare transizioni di fase. Mentre la torrefazione su piccola scala, che richiede un apporto minimo di ossigeno, può avvenire in un altoforno, la calcinazione è un processo diverso e di solito richiede attrezzature diverse. L'altoforno è più comunemente associato ai processi di fusione, in cui si utilizzano temperature elevate e reazioni chimiche specifiche per estrarre i metalli dai minerali.
Punti chiave spiegati:
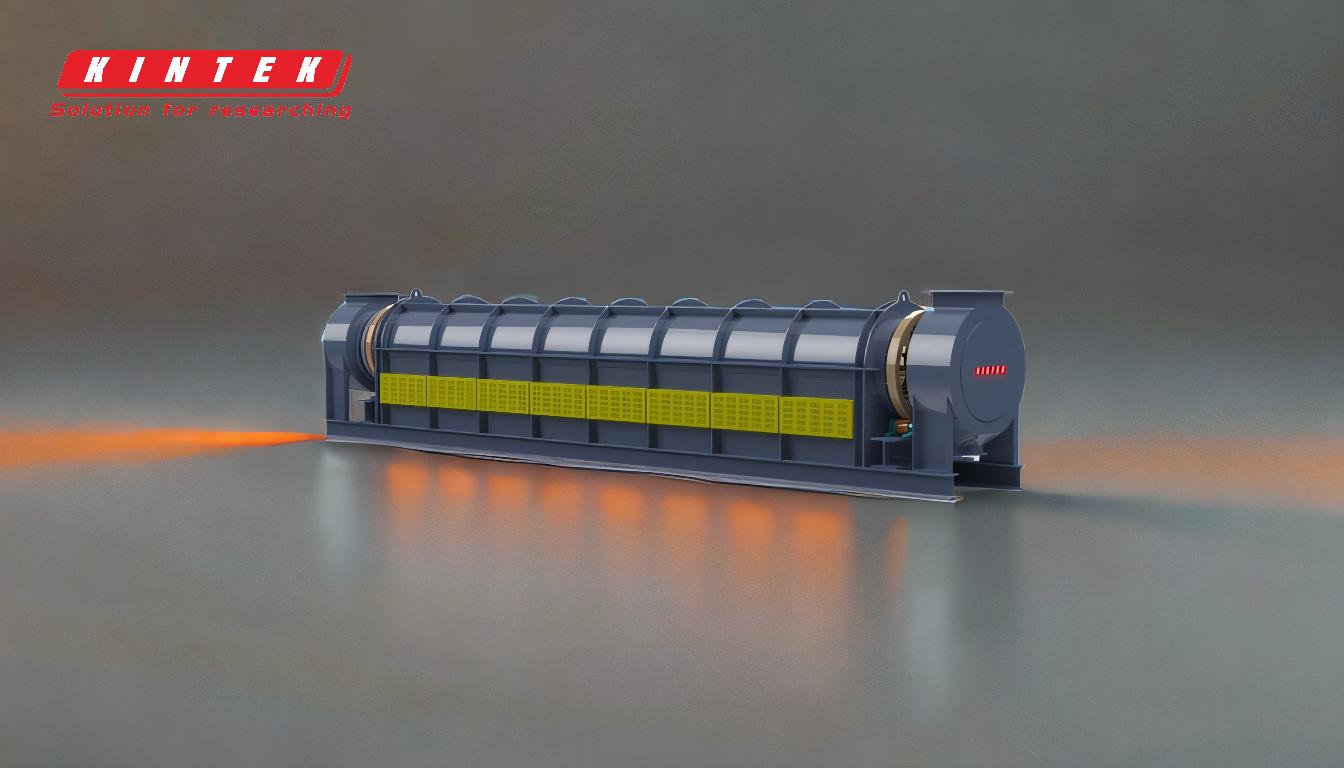
-
Definizione di calcinazione:
- La calcinazione è un processo di trattamento termico che prevede il riscaldamento di materiali solidi, come i minerali, al di sotto del loro punto di fusione in assenza o in presenza limitata di aria o ossigeno. Questo processo induce la decomposizione termica, rimuove le frazioni volatili o provoca transizioni di fase.
-
Apparecchiature tipiche per la calcinazione:
- La calcinazione viene solitamente eseguita in apparecchiature specializzate come forni a riverbero o forni rotativi . Questi forni sono progettati per fornire condizioni di riscaldamento controllate e sono adatti a processi che richiedono una precisa regolazione della temperatura.
- I forni a riverbero, ad esempio, hanno una forma a "S" orizzontale e possono funzionare con o senza ossigeno, a seconda dei requisiti specifici del processo.
-
Altoforno e calcinazione:
- A altoforno è utilizzato principalmente per fusione un processo che prevede alte temperature e reazioni chimiche per estrarre i metalli dai minerali. In genere non viene utilizzato per la calcinazione.
- Mentre la torrefazione su piccola scala (un processo simile alla calcinazione, ma che richiede una quantità minima di ossigeno) può avvenire in un altoforno, la calcinazione vera e propria è un processo distinto e generalmente richiede attrezzature diverse.
-
Scopo della calcinazione:
- Lo scopo principale della calcinazione è rimuovere le impurità volatili o indurre la dissociazione chimica nei materiali. Ad esempio, nella produzione di calce dal calcare, la calcinazione allontana l'anidride carbonica, lasciando la calce in polvere.
-
Esempi di calcinazione:
- Un classico esempio di calcinazione è la conversione di calcare (CaCO₃) a calce (CaO) . Quando il calcare viene riscaldato, subisce una decomposizione termica, rilasciando anidride carbonica (CO₂) e formando calce.
- Anche altri materiali, come la dolomite e la magnesite, vengono calcinati per ottenere specifiche proprietà chimiche o fisiche.
-
Forni rotativi per la calcinazione:
- I forni rotativi sono comunemente utilizzati per la calcinazione, soprattutto per i materiali con dimensioni delle particelle pari o inferiori a 60 mm. Questi forni forniscono un riscaldamento uniforme e sono efficienti per la produzione di prodotti coerenti e di alta qualità.
-
Contrasto con la torrefazione:
- La torrefazione è un processo simile, ma in genere prevede il riscaldamento dei minerali in presenza di aria o ossigeno in eccesso. Viene spesso utilizzata per ossidare i minerali solforati, mentre la calcinazione si concentra sulla decomposizione termica o sulla rimozione delle sostanze volatili.
-
Principali differenze tra i processi di calcinazione e di altoforno:
- La calcinazione è un processo di decomposizione termica che avviene al di sotto del punto di fusione del materiale, mentre i processi di altoforno prevedono la fusione che avviene a temperature molto più elevate e spesso comporta una riduzione chimica.
- La calcinazione viene tipicamente effettuata in forni a riverbero o forni rotativi mentre gli altiforni sono utilizzati per produzione di ferro e altri processi di estrazione dei metalli.
In sintesi, la calcinazione non viene eseguita in un altoforno. Viene invece condotta in apparecchiature specializzate progettate per il riscaldamento controllato e la decomposizione termica. L'altoforno è riservato alla fusione e ad altri processi ad alta temperatura, il che lo rende inadatto ai requisiti precisi della calcinazione.
Tabella riassuntiva:
Punto chiave | Dettagli |
---|---|
Definizione di calcinazione | Decomposizione termica al di sotto del punto di fusione, spesso in assenza di aria/ossigeno. |
Apparecchiature tipiche | Forni a riverbero, forni rotativi. |
Uso dell'altoforno | Principalmente per la fusione, non per la calcinazione. |
Scopo della calcinazione | Rimuovere le impurità volatili o indurre la dissociazione chimica. |
Esempio | Conversione del calcare (CaCO₃) in calce (CaO). |
Forni rotativi | Ideale per il riscaldamento uniforme di materiali ≤60 mm. |
Contrasto con la torrefazione | La torrefazione utilizza l'aria in eccesso; la calcinazione si concentra sulla decomposizione termica. |
Avete bisogno del forno giusto per il vostro processo di calcinazione? Contattate i nostri esperti oggi stesso per trovare la soluzione perfetta!