La riduzione della porosità durante la sinterizzazione è un obiettivo critico nella lavorazione dei materiali per ottenere prodotti più densi, resistenti e affidabili.La porosità di un materiale sinterizzato è influenzata da diversi fattori, tra cui la porosità iniziale del compatto verde, la temperatura di sinterizzazione, il tempo di sinterizzazione, l'atmosfera, la dimensione delle particelle e la pressione applicata.Ottimizzando queste variabili, è possibile ridurre al minimo la porosità e migliorare le proprietà meccaniche e fisiche del materiale.Le strategie chiave includono il controllo della porosità iniziale del compatto verde, la selezione di temperature e tempi di sinterizzazione appropriati, l'uso di particelle di dimensioni ridotte e l'applicazione di una pressione esterna durante la sinterizzazione.Inoltre, l'atmosfera di sinterizzazione e la velocità di riscaldamento svolgono un ruolo importante nell'eliminazione dei pori e nella densificazione.
Spiegazione dei punti chiave:
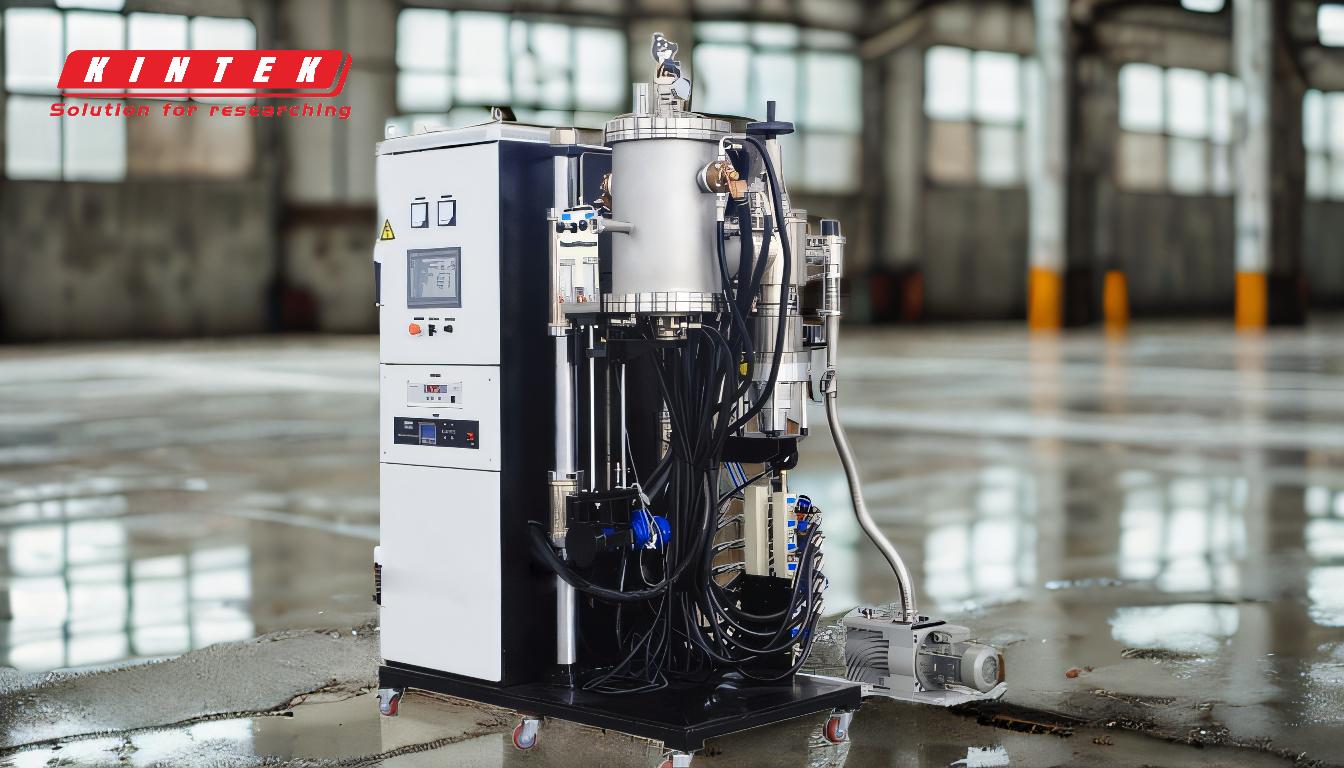
-
Controllo della porosità iniziale del compattamento del verde:
- La porosità iniziale del compatto verde (il materiale non sinterizzato) è un fattore critico nel determinare la porosità finale dopo la sinterizzazione.Una porosità iniziale più bassa porta generalmente a un prodotto finale più denso.
- Per ridurre la porosità iniziale, è necessario adottare tecniche di compattazione adeguate, ad esempio utilizzando pressioni di compattazione più elevate o ottimizzando la distribuzione delle dimensioni delle particelle nel compattato verde.L'impacchettamento uniforme delle particelle riduce al minimo i vuoti di grandi dimensioni e favorisce una migliore densificazione durante la sinterizzazione.
-
Ottimizzazione della temperatura di sinterizzazione:
- La temperatura di sinterizzazione influisce significativamente sulla riduzione della porosità.Le temperature più elevate aumentano la diffusione atomica, che aiuta a eliminare i pori promuovendo il legame delle particelle e la crescita dei grani.
- Tuttavia, temperature troppo elevate possono portare a una crescita indesiderata dei grani o alla decomposizione del materiale.Pertanto, è essenziale identificare la temperatura di sinterizzazione ottimale per il materiale specifico, per bilanciare la riduzione della porosità e l'integrità del materiale.
-
Regolazione del tempo di sinterizzazione:
- Tempi di sinterizzazione più lunghi consentono di eliminare i pori attraverso meccanismi come la diffusione al limite e la diffusione reticolare.Ciò è particolarmente importante per i materiali con un'elevata porosità iniziale o per quelli che richiedono una diffusione allo stato solido, come le ceramiche di ossido puro.
- Tuttavia, tempi di sinterizzazione troppo lunghi possono portare a una sinterizzazione eccessiva, che può degradare le proprietà del materiale.Il tempo di sinterizzazione deve essere ottimizzato in base al materiale e alla porosità finale desiderata.
-
Utilizzare particelle di dimensioni ridotte:
- Le particelle più piccole hanno un rapporto superficie/volume più elevato, che aumenta la forza motrice della sinterizzazione e migliora la densificazione.Le particelle più piccole riducono inoltre le distanze di diffusione, rendendo più efficiente l'eliminazione dei pori.
- Assicurare una distribuzione uniforme delle dimensioni delle particelle per evitare problemi di densificazione localizzata e promuovere una sinterizzazione omogenea.
-
Applicare una pressione esterna (pressatura a caldo o pressatura isostatica a caldo):
- L'applicazione di pressione durante la sinterizzazione (ad esempio, la pressatura a caldo o la pressatura isostatica a caldo) può ridurre significativamente la porosità, favorendo il riarrangiamento delle particelle ed eliminando i vuoti.La sinterizzazione assistita da pressione è particolarmente efficace per i materiali difficili da densificare con i metodi di sinterizzazione convenzionali.
- Questo metodo riduce il tempo di sinterizzazione e la temperatura di sinterizzazione richiesta, rendendolo uno strumento potente per ottenere materiali a bassa porosità.
-
Controllo dell'atmosfera di sinterizzazione:
- L'atmosfera di sinterizzazione (ad esempio, aria, vuoto o gas inerti come argon o azoto) influisce sulla cinetica di sinterizzazione e sulla porosità finale.Ad esempio, un'atmosfera sottovuoto o inerte può prevenire l'ossidazione e promuovere una migliore densificazione in alcuni materiali.
- La scelta dell'atmosfera dipende dalla reattività del materiale e dalle proprietà desiderate del prodotto finale.
-
Ottimizzare la velocità di riscaldamento:
- La velocità di riscaldamento influenza il processo di densificazione.Una velocità di riscaldamento più lenta consente una distribuzione più uniforme della temperatura e una migliore eliminazione dei pori, mentre una velocità di riscaldamento più elevata può portare a gradienti termici e a una densificazione incompleta.
- La velocità di riscaldamento ottimale dipende dal materiale e dall'apparecchiatura di sinterizzazione utilizzata.
-
Migliorare la composizione e l'omogeneità:
- Una composizione omogenea con impurità minime favorisce una migliore sinterizzazione e riduce la porosità.Le impurità possono agire come barriere alla diffusione e ostacolare l'eliminazione dei pori.
- A volte si possono usare additivi o droganti per migliorare il comportamento di sinterizzazione e ridurre la porosità.
Controllando attentamente questi fattori, è possibile ridurre al minimo la porosità durante la sinterizzazione e produrre materiali con proprietà meccaniche, termiche ed elettriche superiori.Ogni sistema di materiali può richiedere regolazioni specifiche per ottenere i risultati desiderati, ma i principi sopra descritti forniscono una solida base per ridurre la porosità nei materiali sinterizzati.
Tabella riassuntiva:
Fattore | Impatto sulla riduzione della porosità |
---|---|
Porosità iniziale | Una minore porosità iniziale nel compatto verde porta a un prodotto finale più denso. |
Temperatura di sinterizzazione | Le temperature più elevate favoriscono la diffusione atomica, ma devono evitare una crescita eccessiva dei grani. |
Tempo di sinterizzazione | Tempi più lunghi consentono l'eliminazione dei pori, ma evitano una sinterizzazione eccessiva. |
Dimensione delle particelle | Le particelle più piccole aumentano la densificazione e riducono le distanze di diffusione. |
Pressione esterna | La sinterizzazione assistita da pressione (ad esempio, la pressatura a caldo) riduce significativamente la porosità. |
Atmosfera di sinterizzazione | Il vuoto o i gas inerti impediscono l'ossidazione e favoriscono la densificazione. |
Velocità di riscaldamento | Le velocità più basse garantiscono una distribuzione uniforme della temperatura e una migliore eliminazione dei pori. |
Composizione e omogeneità | Materiali omogenei con impurità minime migliorano la sinterizzazione e riducono la porosità. |
Siete pronti a ottimizzare il vostro processo di sinterizzazione per ottenere materiali più densi e resistenti? Contattate oggi stesso i nostri esperti per soluzioni su misura!