I componenti metallici sinterizzati sono prodotti attraverso una serie di fasi ben definite che trasformano i metalli in polvere in componenti solidi e durevoli.Il processo prevede in genere la preparazione delle polveri, la compattazione e la sinterizzazione, seguite da fasi di post-trattamento opzionali per migliorare le proprietà del prodotto finale.Selezionando accuratamente le polveri metalliche, applicando precise tecniche di compattazione e controllando l'ambiente di sinterizzazione, i produttori possono produrre pezzi con specifiche proprietà meccaniche, termiche e chimiche.Questo metodo è ampiamente utilizzato in settori come quello automobilistico, aerospaziale ed elettronico, grazie alla sua capacità di creare forme complesse con elevata precisione ed efficienza dei materiali.
Punti chiave spiegati:
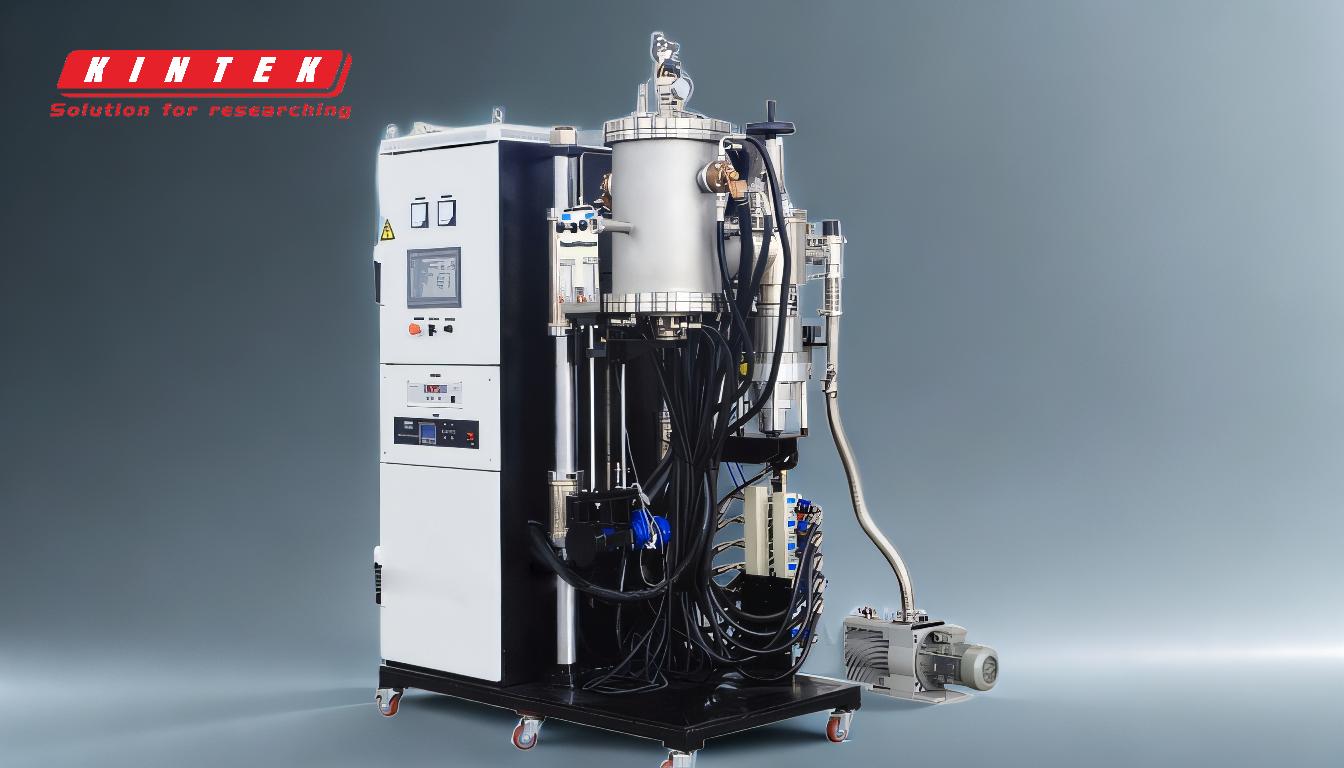
-
Preparazione della polvere
- Scopo:La prima fase prevede la creazione o la selezione della composizione appropriata della polvere metallica, che determina le proprietà finali del pezzo sinterizzato.
- Processo:Le polveri metalliche, come ferro, nichel, molibdeno o rame, sono spesso miscelate con elementi di lega, lubrificanti o additivi per ottenere le caratteristiche desiderate, come la forza, la durezza o la resistenza alla corrosione.
- Considerazioni:Le dimensioni, la forma e la distribuzione delle particelle della polvere sono fondamentali, in quanto influenzano il comportamento di compattazione e sinterizzazione.
-
Miscelazione e miscelazione
- Scopo:Assicura l'uniformità della miscela di polveri, essenziale per ottenere proprietà uniformi dei pezzi.
- Processo:Le polveri vengono miscelate con additivi come i lubrificanti (ad esempio, cera o acido stearico) per migliorare la fluidità e ridurre l'attrito durante la compattazione.
- Considerazioni:Una corretta miscelazione impedisce la segregazione delle particelle e garantisce una distribuzione uniforme degli elementi di lega.
-
Compattazione
- Scopo:Trasforma la polvere sfusa in un pezzo "verde" con una forma specifica e una resistenza iniziale.
- Processo:La polvere viene pressata in uno stampo ad alta pressione (in genere 20-50 tonnellate per pollice quadrato) per formare una forma coerente.
- Considerazioni:La forza di compattazione deve essere attentamente controllata per evitare difetti come crepe o densità non uniforme.Spesso si utilizzano lubrificanti per facilitare l'espulsione dallo stampo.
-
Sinterizzazione
- Scopo:Lega le particelle tra loro per creare un pezzo solido e durevole con proprietà meccaniche ottimali.
- Processo:La parte verde viene riscaldata in un'atmosfera controllata (ad esempio, idrogeno, azoto o vuoto) a una temperatura appena inferiore al punto di fusione del metallo.In questo modo le particelle si legano per diffusione, riducendo la porosità e aumentando la resistenza.
- Considerazioni:La temperatura, il tempo e l'atmosfera di sinterizzazione devono essere controllati con precisione per ottenere la densità, la durezza e la microstruttura desiderate.
-
Post-trattamento
- Scopo:Migliora le proprietà del pezzo sinterizzato per soddisfare i requisiti specifici dell'applicazione.
-
Processo:Le fasi di post-trattamento più comuni includono:
- Lavorazione:Lavorazione di precisione con utensili diamantati o a ultrasuoni per ottenere tolleranze ristrette.
- Trattamento termico:Processi come la tempra e il rinvenimento per migliorare la durezza e la resistenza.
- Trattamento della superficie:Rivestimenti o placcature per migliorare la resistenza all'usura o alla corrosione.
- Montaggio:Giunzione di parti sinterizzate con altri componenti mediante brasatura o metallizzazione.
- Considerazioni:Le fasi di post-trattamento sono adattate all'uso previsto del pezzo, garantendo la conformità agli standard di prestazione.
-
Vantaggi delle parti in metallo sinterizzato
- Efficienza del materiale:Scarti minimi rispetto alla lavorazione tradizionale.
- Forme complesse:Capacità di produrre geometrie complesse, difficili o impossibili da realizzare con altri metodi.
- Costo-efficacia:Costi di produzione ridotti per la produzione di grandi volumi.
- Personalizzabilità:Proprietà del materiale personalizzate grazie al controllo preciso della composizione della polvere e dei parametri di lavorazione.
Seguendo questi passaggi, i produttori possono produrre parti metalliche sinterizzate con precisione, durata e prestazioni eccezionali, che le rendono ideali per un'ampia gamma di applicazioni industriali.
Tabella riassuntiva:
Passo | Scopo | Considerazioni chiave |
---|---|---|
Preparazione della polvere | Selezionare la composizione della polvere metallica per le proprietà desiderate | Le dimensioni, la forma e la distribuzione delle particelle influenzano la compattazione e la sinterizzazione. |
Miscelazione | Garantire l'uniformità della miscela di polveri per ottenere proprietà uniformi dei pezzi | Una corretta miscelazione previene la segregazione e assicura una distribuzione uniforme degli additivi. |
Compattazione | Trasforma la polvere sciolta in una forma coerente con la forza iniziale. | Controllare la forza di compattazione per evitare difetti come crepe o densità non uniforme. |
Sinterizzazione | Legare le particelle per creare un pezzo solido e durevole con proprietà ottimali | Il controllo preciso di temperatura, tempo e atmosfera è fondamentale. |
Post-trattamento | Migliorare le proprietà per soddisfare i requisiti di applicazioni specifiche | Include lavorazione, trattamento termico, trattamento superficiale e assemblaggio. |
Avete bisogno di parti metalliche sinterizzate personalizzate per il vostro settore? Contattateci oggi stesso per soluzioni esperte!