Introduzione
Indice dei contenuti
Quando si tratta di produrre componenti ceramici di alta qualità, uno dei processi più importanti è la pressatura isostatica. Questa tecnica garantisce l'uniformità e la precisione necessarie per la produzione di ceramiche utilizzate in vari settori industriali. La pressatura isostatica prevede un'attenta selezione delle polveri da pressare e il controllo degli strumenti per ottenere l'uniformità desiderata. Un altro fattore chiave in questo processo è l'ottimizzazione del processo di sinterizzazione, che influenza notevolmente le proprietà fisiche della ceramica. Conoscendo il processo di pressatura isostatica, i produttori possono garantire la produzione di ceramiche che soddisfano i rigorosi standard di precisione dimensionale e di prestazioni.
Il processo di pressatura semi-isostatica
Importanza dell'uniformità di pressatura
Nellapressatura semi-isostatica i prodotti vengono posti in un contenitore chiuso riempito di liquido e sottoposti a una pressione uguale su tutte le superfici. Questo ambiente ad alta pressione aumenta la densità dei prodotti e conferisce loro le forme richieste. Le presse semi-isostatiche sono ampiamente utilizzate per la formatura di refrattari ad alta temperatura, ceramiche, carburo cementato, magneti permanenti al lantanio, materiali al carbonio e polveri di metalli rari.
Ruolo di un'attenta selezione delle polveri di pressatura e dei controlli degli utensili
La pressatura semi-isostatica si basa su un'attenta selezione delle polveri di pressatura e dei controlli degli utensili per garantire il risultato desiderato. A differenza di altri processi di metallurgia delle polveri, la pressatura semi-isostatica offre diversi vantaggi, tra cui una compattazione uguale in tutte le direzioni e una densità finale del componente più uniforme. Tuttavia, i produttori devono caratterizzare attentamente le proprietà della polvere metallica utilizzata nel processo per ottenere le proprietà ottimali del componente finale. La caratterizzazione del materiale è fondamentale per garantire la qualità e le prestazioni desiderate del prodotto finale.
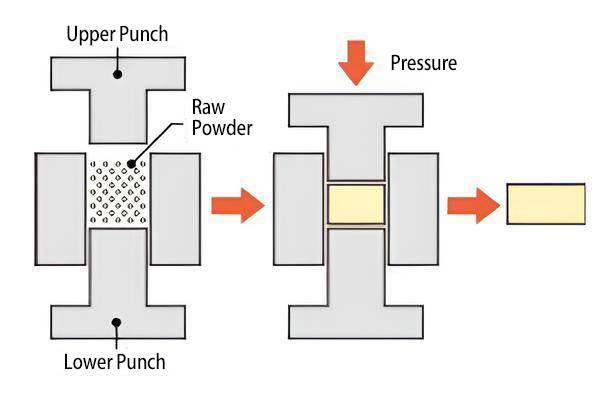
Influenza del processo di sinterizzazione ottimizzato sulle proprietà fisiche
Il processo di sinterizzazione ottimizzato svolge un ruolo significativo nel determinare le proprietà fisiche dei componenti pressati semi-isostaticamente. La pressatura isostatica consente di produrre vari tipi di materiali da polveri compatte riducendo la porosità della miscela di polveri. La miscela di polveri viene compattata e incapsulata utilizzando la pressione isostatica, che applica una pressione uguale da tutte le direzioni. Il confinamento della polvere metallica all'interno di una membrana flessibile o di un contenitore ermetico assicura una compattazione e una densità uniformi all'interno della parte compattata.
Il processo di pressatura isostatica si è evoluto nel corso degli anni ed è oggi ampiamente utilizzato in vari settori, tra cui ceramica, metalli, compositi, plastica e carbonio. Offre vantaggi unici per le applicazioni ceramiche e refrattarie, consentendo di modellare con precisione i prodotti e riducendo la necessità di costose lavorazioni meccaniche. La pressione esercitata a 360° durante la pressatura isostatica assicura una compattazione e una densità uniformi, risolvendo i problemi di variazione della densità nei metodi di lavorazione convenzionali. La pressatura isostatica è particolarmente adatta per la produzione di pezzi di grandi dimensioni, di pezzi con un elevato rapporto spessore/diametro e di pezzi che richiedono proprietà superiori del materiale.
Esistono due categorie principali di pressatura isostatica: la pressatura isostatica a freddo (CIP) e la pressatura isostatica a caldo (HIP). La CIP prevede l'applicazione di una pressione isostatica alla polvere sfusa a temperatura ambiente, mentre la HIP applica una pressione isostatica alla polvere quando viene riscaldata in una confezione. L'HIP utilizza un gas inerte come mezzo di trasferimento della pressione. Il processo di pressatura isostatica a caldo consiste nel collocare la polvere in un recipiente ad alta pressione, sottoporla a temperatura elevata e pressione bilanciata e sinterizzarla in parti compatte. Rispetto ad altri metodi come la pressatura a caldo, la pressatura isostatica a caldo offre temperature di sinterizzazione più basse e una maggiore densità del prodotto.
In conclusione, il processo di pressatura semi-isostatica offre vantaggi unici in termini di uniformità di pressatura e densità finale dei componenti. Un'attenta selezione delle polveri di pressatura e dei controlli degli utensili, nonché l'ottimizzazione del processo di sinterizzazione, sono fondamentali per ottenere le proprietà fisiche desiderate. Il processo di pressatura isostatica è diventato uno strumento prezioso in diversi settori industriali, consentendo la produzione di componenti di alta qualità con forme precise e proprietà materiali superiori.
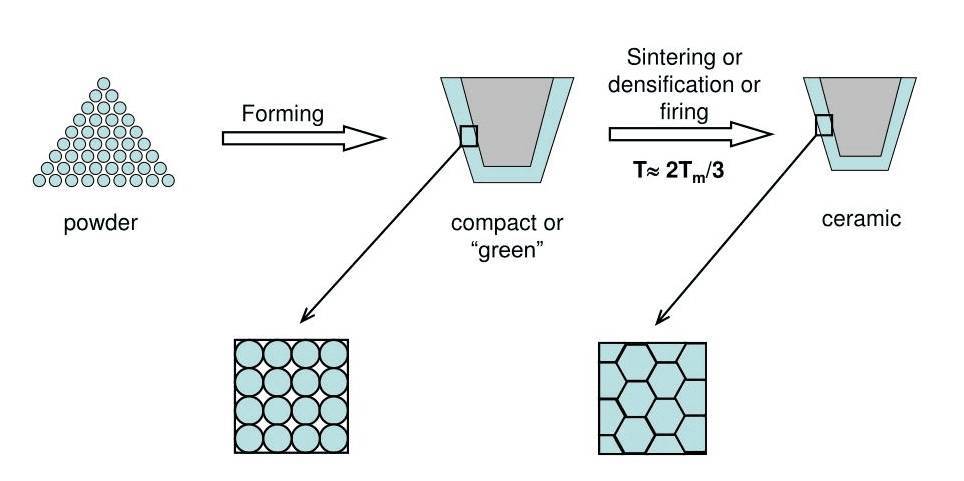
Ruolo delle tecniche di sinterizzazione su misura
Ottenere linearità e concentricità
La sinterizzazione è un processo cruciale nella produzione di componenti ceramici. Le tecniche di sinterizzazione su misura svolgono un ruolo fondamentale per ottenere linearità e concentricità in questi componenti.
Un vantaggio della sinterizzazione a temperatura ambiente è che consente di produrre target di grandi dimensioni senza essere limitati dalle dimensioni delle apparecchiature. Questo metodo offre inoltre un basso investimento in attrezzature, un basso costo di produzione, un'elevata efficienza produttiva, eccellenti prestazioni del target e una facile produzione industriale. È particolarmente adatto ai requisiti di prestazione dei target rivestiti per display di fascia alta.
Tuttavia, la sinterizzazione a temperatura ambiente ha i suoi punti deboli. È considerato il metodo di sinterizzazione più difficile rispetto ad altri. Per ottenere un corpo sinterizzato denso, spesso viene aggiunto un coadiuvante di sinterizzazione. Ma la rimozione del coadiuvante di sinterizzazione dal corpo sinterizzato può essere difficile, con conseguente riduzione della purezza del prodotto. Inoltre, è necessario soddisfare requisiti rigorosi per quanto riguarda la forma, la dimensione delle particelle e la distribuzione granulometrica della polvere. Per soddisfare questi requisiti vengono comunemente utilizzate tecniche di lavorazione delle polveri come la macinazione a sfere, la macinazione a getto e la classificazione per sedimentazione. Infine, i target prodotti attraverso la sinterizzazione a temperatura ambiente sono generalmente sottili.
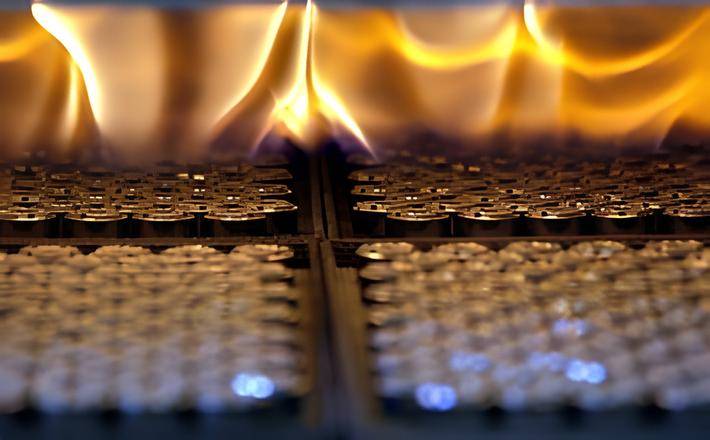
Idoneità alla produzione di vari componenti ceramici
La sinterizzazione è un processo versatile che offre diversi vantaggi nella produzione di componenti ceramici. Ecco alcuni vantaggi chiave:
-
Forme complesse: La sinterizzazione dei metalli consente di creare forme complesse che sarebbero difficili o impossibili da produrre con altri metodi. Questa capacità apre la strada a design innovativi e componenti funzionali.
-
Alta precisione dimensionale: La sinterizzazione offre un'elevata precisione dimensionale, garantendo che il prodotto finito corrisponda perfettamente alla forma desiderata. Questa precisione è fondamentale nelle applicazioni in cui sono richieste tolleranze ristrette.
-
Affidabilità e ripetibilità della produzione su larga scala: La sinterizzazione è un processo affidabile, che produce prodotti finiti uniformi. Questo lo rende ideale per le produzioni su larga scala, dove la coerenza e l'uniformità sono essenziali.
-
Autolubrificazione: La sinterizzazione può creare pezzi con proprietà autolubrificanti. La polvere compattata forma un legame denso tra le particelle, riducendo l'attrito e l'usura. Questa proprietà è preziosa nelle applicazioni in cui la lubrificazione è difficile o indesiderata.
-
Materiali unici e isotropi: La sinterizzazione viene utilizzata per creare materiali unici e isotropi, ovvero con le stesse proprietà in tutte le direzioni. Questi materiali sono altamente durevoli e presentano un'eccellente resistenza, rendendoli adatti ad applicazioni che richiedono robustezza.
-
Tecnologia verde: La sinterizzazione è considerata una tecnologia verde in quanto non produce emissioni nocive. Questo la rende una scelta ecologica per le aziende che vogliono ridurre il loro impatto ambientale.
-
Smorzamento delle vibrazioni: La sinterizzazione può produrre pezzi con proprietà di smorzamento delle vibrazioni. La polvere compattata forma un legame denso, riducendo vibrazioni e rumore. Questo attributo è vantaggioso nelle applicazioni in cui il controllo delle vibrazioni è fondamentale.
Varie parti in ceramica
La sinterizzazione dei metalli trova applicazione in diversi settori, tra cui componenti elettrici, semiconduttori e fibre ottiche. Migliora la resistenza, la conduttività e la traslucenza dei metalli, rendendoli adatti a questi settori.
Nella sinterizzazione della ceramica, il processo è utilizzato per produrre oggetti in ceramica, tra cui le ceramiche. Comporta il consolidamento del materiale, riducendo la porosità e aumentando la densità. Le materie prime ceramiche spesso richiedono additivi organici prima della sinterizzazione per migliorare la plasticità. Il processo di sinterizzazione è guidato da alte temperature, pressione o correnti elettriche.
I moderni metodi di formatura delle polveri, come la pressatura isostatica, lo slipcasting, l'estrusione, la tapecasting e la stampa 3D, sono stati sviluppati per realizzare corpi verdi di ceramica e metalli. Il corpo verde viene poi riscaldato attraverso un processo di sinterizzazione, che riduce la porosità e aumenta la densità.
I processi di sinterizzazione sono controllati da meccanismi di diffusione allo stato solido attivati termicamente. Questi meccanismi possono essere quantificati sviluppando modelli di sinterizzazione utilizzando strumenti come i dilatometri a spinta.
Le apparecchiature di sinterizzazione a microonde sono ampiamente utilizzate nelle applicazioni industriali per sinterizzare varie ceramiche di alta qualità, tra cui l'ossido di cobalto e litio, il nitruro di silicio, il carburo di silicio, l'ossido di alluminio, il nitruro di alluminio, l'ossido di zirconio, l'idrossido di magnesio, l'alluminio, lo zinco, il caolino, il solfato di cobalto, l'ossalato di cobalto e l'ossido di vanadio. Viene anche utilizzato per sinterizzare dispositivi elettronici in ceramica come le ceramiche piezoelettriche PZT e i varistori.
In generale, le tecniche di sinterizzazione su misura svolgono un ruolo cruciale nell'ottenere linearità e concentricità nei componenti ceramici. Offrono numerosi vantaggi, tra cui la capacità di produrre forme complesse, l'elevata precisione dimensionale, l'affidabilità nella produzione su larga scala, l'autolubrificazione, i materiali isotropi unici, la tecnologia verde e lo smorzamento delle vibrazioni. La sinterizzazione dei metalli trova applicazione in diversi settori industriali, mentre la sinterizzazione della ceramica è utilizzata nella produzione di ceramiche e in altri processi di produzione di ceramica. Le apparecchiature di sinterizzazione a microonde sono ampiamente utilizzate nelle applicazioni industriali per sinterizzare varie ceramiche e dispositivi elettronici in ceramica.
Capacità dimensionali e precisione
Gamma standard di capacità dimensionali
Le capacità dimensionali di un sistema di deposizione svolgono un ruolo cruciale nel determinare la sua idoneità per varie applicazioni. Negli ambienti di ricerca e sviluppo, la flessibilità è un fattore chiave. Il sistema deve essere in grado di gestire diversi materiali, dimensioni del substrato, intervalli di temperatura, flusso di ioni, velocità di deposizione, frequenze, punti finali e regimi operativi di pressione. Ciò consente di sperimentare e di adattarsi alle mutevoli priorità. Inoltre, entrano in gioco anche considerazioni di budget, poiché il costo dei sistemi può variare in modo significativo a seconda delle opzioni tecnologiche.
Precisione in condizioni di combustione
La precisione è un fattore critico quando si parla di sistemi di deposizione. Ad esempio, nel caso di applicazioni di microlavorazione o di ultraprecisione, il diamante viene spesso utilizzato come materiale per utensili grazie alla sua estrema durezza e stabilità dimensionale. Se si considera la precisione in condizioni di cottura, è importante notare che il diametro interno può avere una tolleranza di +/- 0,02 mm con una ripetibilità inferiore a 10 µm all'interno dello stesso lotto di produzione.
Precisione dopo la rettifica al diamante
La rettifica al diamante è un processo che può migliorare notevolmente la precisione nelle applicazioni di lavorazione. Dopo la diamantatura, la lunghezza del pezzo può avere una tolleranza di +/- 0,03 mm, mentre il diametro esterno può avere una tolleranza di +/- 0,01 mm. Inoltre, lo spessore minimo della parete ottenibile è di 0,3 µm. Questi livelli di precisione garantiscono risultati di alta qualità del pezzo.
Gli utensili diamantati possono essere realizzati con diamante massiccio (monocristallo, diamante CVD, PCD) o con rivestimenti diamantati. Gli utensili abrasivi diamantati standard sono realizzati incollando monocristalli di diamante su un corpo di base. In alternativa, esiste una nuova tecnologia di strati abrasivi che prevede strati di diamante microcristallino depositati in fase di vapore chimico con punte di cristalli affilate. Queste punte taglienti contribuiscono all'efficacia del processo di rettifica.
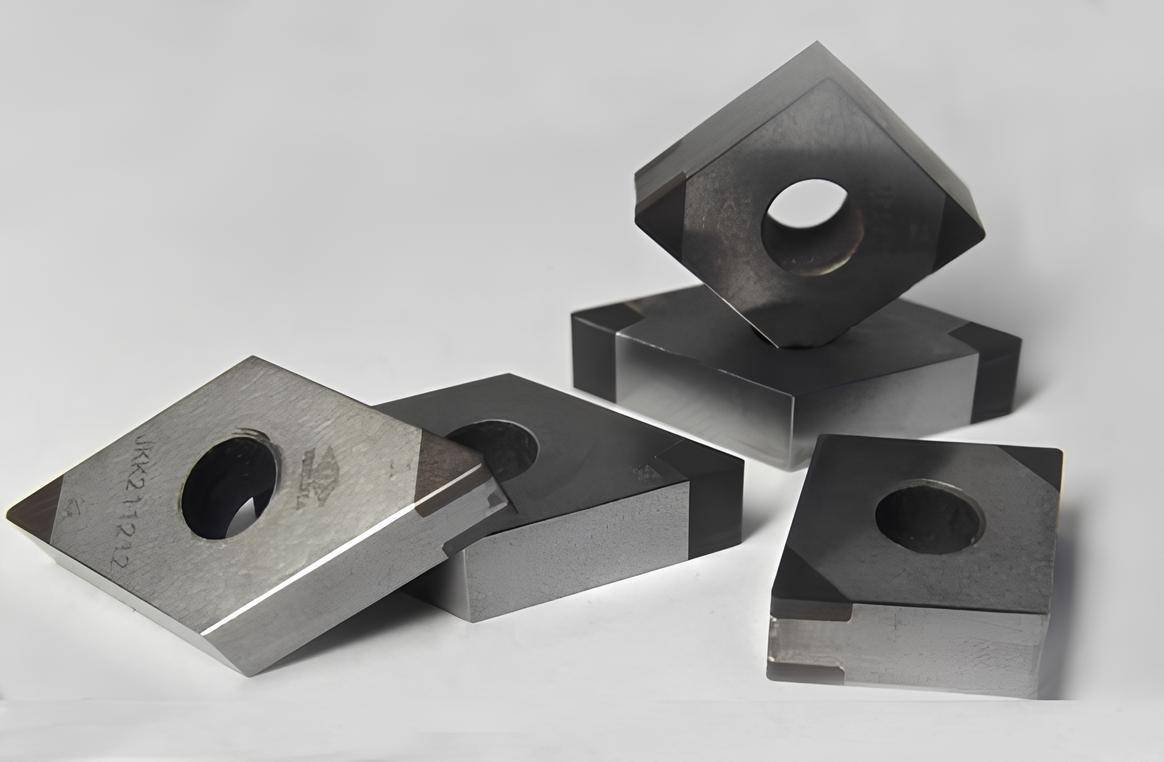
Anche i microutensili di rettifica, come le matite abrasive e le frese, possono essere prodotti con la stessa tecnologia di rivestimento. Sono stati testati con successo anche utensili molto piccoli, con diametri di 50 mm.
In conclusione, le capacità dimensionali e la precisione di un sistema di deposizione sono fattori cruciali da considerare negli ambienti di ricerca e sviluppo. Il sistema deve offrire flessibilità, consentendo la sperimentazione e l'adattamento alle mutevoli priorità. La rettifica diamantata può migliorare notevolmente la precisione nelle applicazioni di lavorazione, garantendo risultati di alta qualità. Che si tratti di una gamma standard di capacità dimensionali o di precisione dopo la rettifica al diamante, questi fattori contribuiscono all'efficacia e all'efficienza complessiva del sistema di deposizione.
Conclusione
In conclusione,la pressatura isostatica è un processo cruciale nella produzione di ceramica che garantisce l'uniformità e la precisione dei componenti ceramici. Selezionando con cura le polveri di pressatura e controllando gli strumenti, i produttori possono ottenere l'uniformità desiderata nelle ceramiche pressate. Inoltre, l'ottimizzazione del processo di sinterizzazione migliora ulteriormente le proprietà fisiche della ceramica. Le tecniche di sinterizzazione su misura svolgono un ruolo fondamentale nell'ottenere linearità e concentricità nel prodotto finale, rendendolo adatto a varie applicazioni. Inoltre, le capacità dimensionali e la precisione delle ceramiche possono essere standardizzate e gli eventuali aggiustamenti necessari possono essere apportati attraverso la rettifica al diamante. In generale, la pressatura isostatica e le tecniche di sinterizzazione su misura sono essenziali per produrre componenti ceramici di alta qualità e precisione.
Se siete interessati ai nostri prodotti, visitate il nostro sito web aziendale:https://kindle-tech.com/product-categories/isostatic-pressdove l'innovazione è sempre stata una priorità. Il nostro team di ricerca e sviluppo è composto da ingegneri e scienziati esperti che seguono da vicino le tendenze del settore e si spingono costantemente oltre i confini del possibile. Le nostre apparecchiature di laboratorio incorporano la tecnologia più avanzata per garantire risultati accurati e ripetibili durante i vostri esperimenti. Dagli strumenti di alta precisione ai sistemi di controllo intelligenti, i nostri prodotti vi offriranno possibilità illimitate per il vostro lavoro sperimentale.
CONTATTATECI PER UNA CONSULENZA GRATUITA
I prodotti e i servizi di KINTEK LAB SOLUTION sono stati riconosciuti da clienti di tutto il mondo. Il nostro personale sarà lieto di assistervi per qualsiasi richiesta. Contattateci per una consulenza gratuita e parlate con uno specialista del prodotto per trovare la soluzione più adatta alle vostre esigenze applicative!