Il processo di sinterizzazione è un metodo fondamentale nella scienza dei materiali e nella produzione, utilizzato per trasformare i materiali in polvere in strutture solide e coese senza raggiungere il punto di fusione del materiale.Questo processo prevede diverse fasi, tra cui la preparazione della polvere, la compattazione, il riscaldamento controllato e il raffreddamento.La sinterizzazione è ampiamente utilizzata per creare componenti di elevata precisione, durezza e tenacità, ed è quindi ideale per produrre forme e geometrie complesse, difficili da ottenere con i metodi di produzione tradizionali.Il processo è anche economicamente vantaggioso, in quanto consente una rapida produzione di massa mantenendo precisione e ripetibilità.Di seguito illustriamo le fasi principali e i vantaggi della sinterizzazione.
Punti chiave spiegati:
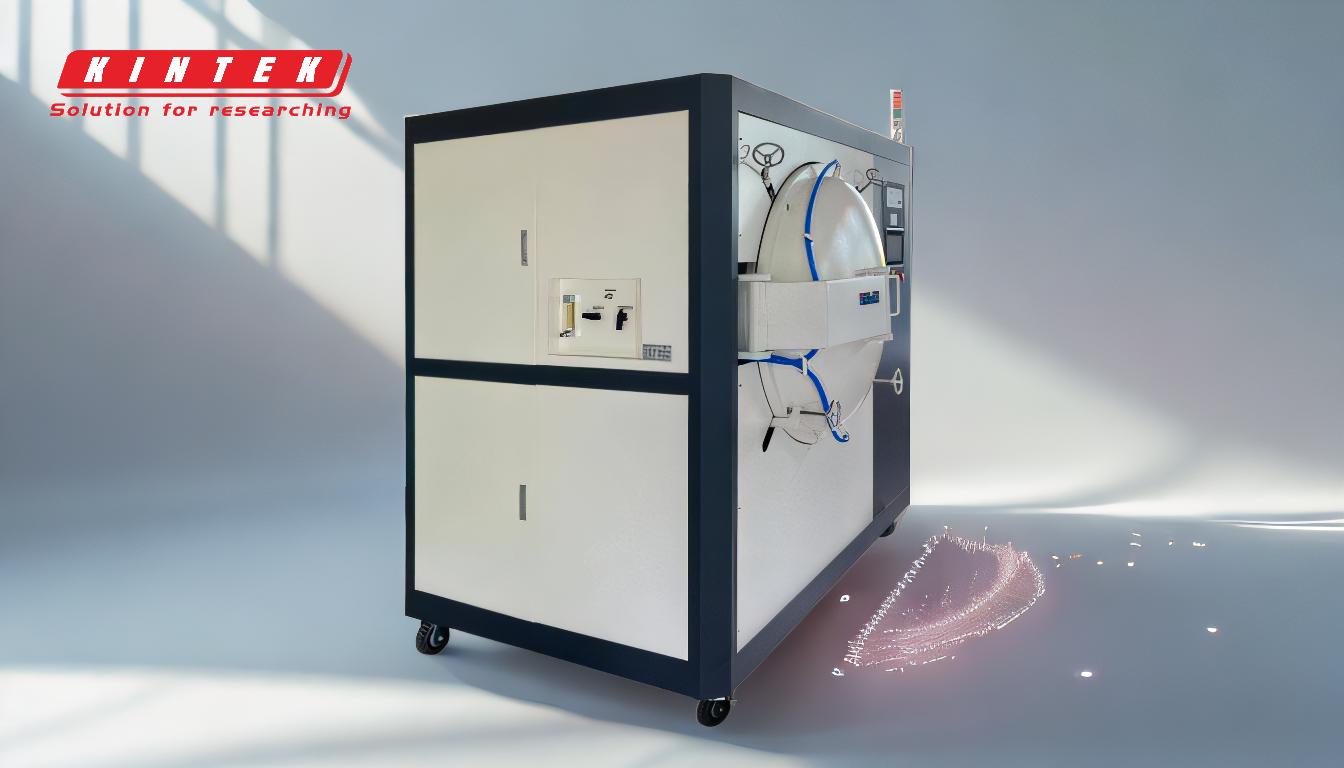
-
Preparazione della polvere compatta
- Il processo inizia con la preparazione delle materie prime, in genere in polvere.La polvere viene mescolata con agenti leganti come acqua, cera o polimeri per favorire l'adesione.
- La polvere viene poi compattata con metodi come la saldatura a freddo, gli strumenti di pressatura o i laser stampati in 3D per formare un "pezzo verde".Questa fase garantisce l'uniformità ed elimina i vuoti nel materiale.
-
Riscaldamento e consolidamento
- La polvere compattata viene posta in un forno di sinterizzazione, dove viene riscaldata a una temperatura appena inferiore al suo punto di fusione.Questo riscaldamento controllato attiva i processi di diffusione tra le particelle, portando alla formazione del collo e alla densificazione.
- In questa fase, l'agente legante evapora o brucia e le particelle primarie iniziano a fondersi in superficie.In alcuni casi, gli agenti leganti intermedi come il bronzo si fondono e si accoppiano tra le particelle, lasciando inalterato il materiale primario.
-
Fusione e densificazione delle particelle
- Con l'aumento della temperatura, le particelle subiscono una diffusione che le porta a fondersi e a densificarsi.Questa fase può essere accelerata utilizzando tecniche come la sinterizzazione in fase liquida (LPS), in cui si forma una fase liquida che migliora il legame tra le particelle.
- Il materiale passa da una struttura porosa a una massa densa e solida, con una porosità ridotta e proprietà meccaniche migliorate.
-
Raffreddamento e solidificazione
- Dopo la fase di riscaldamento, il materiale viene lasciato raffreddare gradualmente.Questo processo di raffreddamento solidifica il prodotto sinterizzato in una struttura rigida e coesa.
- Il prodotto finale mantiene la forma desiderata e presenta proprietà migliorate come durezza, tenacità e resistenza all'abrasione.
-
Vantaggi della sinterizzazione
- Geometrie complesse:La sinterizzazione consente di produrre forme e geometrie complesse, difficili da realizzare con i metodi di produzione tradizionali.
- Proprietà dei materiali:Permette di combinare più materiali, unendo proprietà come la tenacità e la resistenza all'abrasione.
- Costo-efficacia:La sinterizzazione riduce i costi di attrezzaggio e consente una rapida produzione di massa, mantenendo precisione e ripetibilità.
- Materiali ad alto punto di fusione:Il processo è particolarmente utile per i materiali con punti di fusione estremamente elevati, come il tungsteno e il molibdeno, dove i metodi di fusione tradizionali non sono praticabili.
-
Applicazioni della sinterizzazione
- La sinterizzazione è ampiamente utilizzata in settori come quello automobilistico, aerospaziale ed elettronico per produrre componenti come ingranaggi, cuscinetti, filtri e parti strutturali.
- Viene impiegata anche nella produzione di ceramiche, metalli e materiali compositi, il che la rende una tecnica di produzione versatile.
Conoscendo il processo di sinterizzazione, i produttori possono sfruttarne i vantaggi per produrre componenti durevoli e di alta qualità in modo efficiente ed economico.La capacità di creare forme complesse e di combinare le proprietà dei materiali rende la sinterizzazione una tecnica indispensabile nella produzione moderna.
Tabella riassuntiva:
Fase | Descrizione |
---|---|
Preparazione della polvere | Le materie prime vengono preparate in polvere e miscelate con agenti leganti. |
Compattazione | La polvere viene compattata per formare una "parte verde", garantendo l'uniformità ed eliminando i vuoti. |
Riscaldamento e consolidamento | La polvere compattata viene riscaldata al di sotto del punto di fusione, attivando la diffusione e il legame. |
Fusione delle particelle | Le particelle si fondono e si densificano, passando da strutture porose a strutture solide dense. |
Raffreddamento e solidificazione | Il raffreddamento graduale solidifica il materiale in un prodotto finale rigido e coeso. |
Vantaggi | - Geometrie complesse |
- Proprietà del materiale migliorate
- Produzione di massa a costi contenuti
- Ideale per materiali ad alto punto di fusione. | Applicazioni
| Automotive, aerospaziale, elettronica, ceramica, metalli e compositi.| Scoprite come la sinterizzazione può rivoluzionare il vostro processo di produzione... contattate i nostri esperti oggi stesso