I forni batch e i forni a colata continua differiscono in modo significativo nella progettazione, nel funzionamento e nell’applicazione. I forni batch trattano una quantità specifica di materiale in un unico ciclo, rendendoli ideali per operazioni su scala ridotta e ambienti cleanroom. Sono più semplici, economici e di facile manutenzione, ma richiedono una maggiore movimentazione manuale e il raggruppamento dei materiali. I forni a colata continua, invece, trattano i materiali in un flusso continuo, offrendo maggiore produttività ed efficienza per operazioni su larga scala. Sono più complessi, costosi e richiedono una manutenzione frequente, ma eliminano la necessità di movimentazione manuale e riducono il consumo energetico. La scelta tra i due dipende dai requisiti specifici dell'applicazione, come la scala di produzione, il tipo di materiale e l'efficienza operativa.
Punti chiave spiegati:
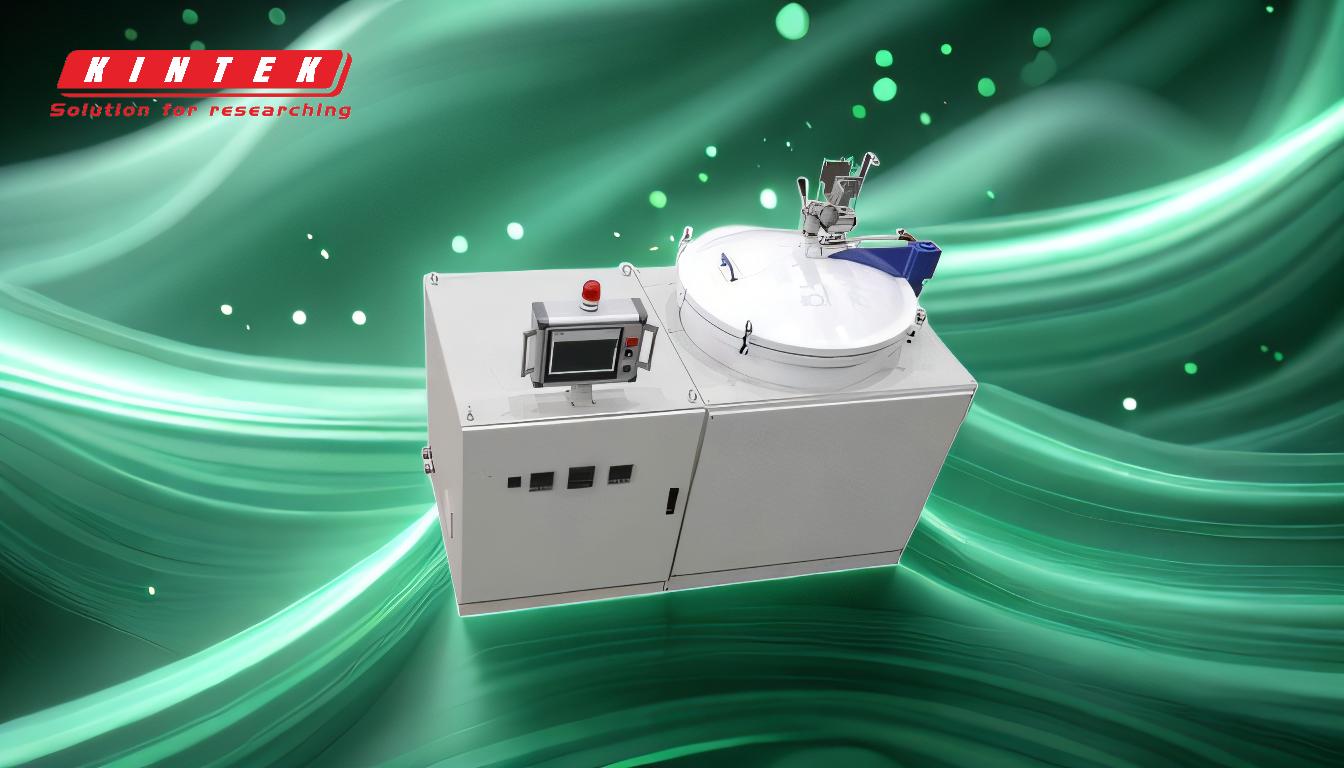
-
Modalità operativa:
- Forni batch: Questi forni trattano una determinata quantità di materiale in un unico passaggio. Il materiale viene caricato, lavorato e quindi scaricato prima dell'inizio del lotto successivo. Ciò li rende adatti per operazioni su scala ridotta in cui è richiesto un controllo preciso su ciascun lotto.
- Forni a colata continua: Questi forni trattano il materiale in continuo senza interruzioni. Il materiale viene immesso nel forno da un'estremità ed esce dall'altra estremità dopo la lavorazione. Questo flusso continuo consente una maggiore produttività ed è ideale per operazioni su larga scala.
-
Capacità:
- Forni batch: Tipicamente hanno capacità che vanno da 620 a 2320 ml. La capacità limitata li rende adatti alla lavorazione di minori quantità di materiale alla volta.
- Forni a colata continua: Hanno capacità limitate dalla dimensione della tramoggia di alimentazione o di raccolta, che può variare da pochi litri a diverse centinaia di litri o più. Ciò consente la lavorazione continua di grandi quantità di materiale.
-
Design e complessità:
- Forni batch: Si tratta di macchine a processo chiuso, spesso progettate per soddisfare gli standard delle camere bianche e le applicazioni in atmosfera inerte. Sono meno complessi, più facili da mantenere e generalmente meno costosi sia inizialmente che nel tempo.
- Forni a colata continua: Questi sono più complessi e costosi. Sono costituiti da più moduli come camere di carico/evacuazione, camere di preriscaldamento e ad alto calore, camere a posizione di calore multipla e camere di raffreddamento. Questa complessità consente un'elaborazione continua ma richiede una manutenzione più frequente.
-
Manutenzione e costi:
- Forni batch: Più facile e meno costoso da mantenere. Richiedono più lavoro manuale durante il processo per formare gruppi per il caricamento e necessitano di attrezzature come cestelli o scaffalature.
- Forni a colata continua: Più costosi da mantenere a causa della loro complessità. Funzionano a temperatura costante, con gli articoli che viaggiano attraverso il forno a velocità costante, eliminando la necessità di rastrelliere o cestelli e riducendo il consumo energetico complessivo.
-
Applicazioni:
- Forni batch: Adatto per applicazioni che richiedono un controllo preciso su ciascun lotto, come in ambienti cleanroom o dove sono necessarie atmosfere inerti. Sono ideali per operazioni su scala ridotta e processi specializzati.
- Forni a colata continua: Ideale per processi di produzione su larga scala come ricottura, brasatura, cementazione, sinterizzazione e tempra. Il funzionamento continuo consente elevata produttività ed efficienza, rendendoli adatti alle industrie che richiedono grandi volumi di materiale lavorato.
-
Efficienza energetica:
- Forni batch: Generalmente meno efficiente dal punto di vista energetico per operazioni su larga scala a causa della necessità di ripetuti cicli di riscaldamento e raffreddamento per ciascun lotto.
- Forni a colata continua: Maggiore efficienza energetica per operazioni su larga scala poiché mantengono una temperatura costante e trattano il materiale in modo continuo, riducendo la necessità di cicli ripetuti di riscaldamento e raffreddamento.
In sintesi, la scelta tra un forno batch e un forno a colata continua dipende dai requisiti specifici dell’applicazione, tra cui la scala di produzione, il tipo di materiale e l’efficienza operativa. I forni batch sono più adatti per operazioni precise e su piccola scala, mentre i forni a colata continua sono ideali per processi su larga scala e ad alta produttività.
Tabella riassuntiva:
Caratteristica | Forno batch | Forno di colata continua |
---|---|---|
Modalità operativa | Elabora il materiale in lotti specifici | Elabora il materiale in modo continuo |
Capacità | 620–2320 ml (su piccola scala) | Capacità maggiori, da litri a centinaia di litri |
Design e complessità | Processo più semplice e chiuso, compatibile con le camere bianche | Complessità, moduli multipli, manutenzione più elevata |
Manutenzione e costi | Più facile e meno costoso da mantenere | È necessaria una manutenzione più costosa e frequente |
Applicazioni | Ideale per operazioni precise e su piccola scala (camere bianche, atmosfere inerti) | Adatto per processi su larga scala (ricottura, brasatura, sinterizzazione, tempra) |
Efficienza energetica | Meno efficiente per operazioni su larga scala | Maggiore efficienza energetica per la lavorazione continua e su larga scala |
Hai bisogno di aiuto per scegliere il forno giusto per la tua applicazione? Contatta i nostri esperti oggi stesso per una consulenza personalizzata!