Introduzione
Indice dei contenuti
- Introduzione
- Panoramica della pressatura isostatica a freddo
- Tipi di pressatura isostatica a freddo
- Vantaggi della pressatura isostatica a freddo rispetto alla pressatura con stampo monoassiale
- La pressatura isostatica a freddo nella produzione di componenti di forma complessa
- Confronto tra CIP e stampaggio a iniezione per la produzione di grandi volumi
- Panoramica storica dell'uso del CIP nella produzione di ceramiche di allumina
- Uso del CIP nella produzione di isolatori per candele di accensione
- Presse isostatiche a freddo
- Pressatura isostatica a freddo
- COS'È LA PRESSATURA ISOSTATICA A FREDDO DESCRIZIONE
- Pressatura isostatica a freddo
- Processo di pressatura isostatica a freddo
- Vantaggi della pressatura isostatica a freddo per la ceramica allumina
- Svantaggi della pressatura isostatica a freddo per la ceramica
- Applicazioni della pressatura isostatica a freddo
- Tecnologie di compressione alternative
- Conclusione
La pressatura isostatica a freddo (CIP)è un processo di produzione ampiamente utilizzato in vari settori, tra cui quello ceramico, metallurgico e farmaceutico. Consiste nell'applicare una pressione uguale in tutte le direzioni a un materiale collocato all'interno di uno stampo flessibile o di un sacchetto. Questo processo consente di ottenere una densità uniforme e di modellare componenti complessi con geometrie intricate. Il CIP offre diversi vantaggi rispetto alla tradizionale pressatura monoassiale, come la capacità di formare forme più complesse e di ridurre le distorsioni e le fessurazioni dovute all'impacchettamento uniforme delle particelle. In questo post approfondiremo l'applicazione, i vantaggi e i limiti della pressatura isostatica a freddo.
Panoramica della pressatura isostatica a freddo
Spiegazione della pressatura isostatica a freddo
La pressatura isostatica a freddo (CIP) è una tecnica di lavorazione dei materiali che prevede l'applicazione di una pressione uguale in tutte le direzioni a un materiale in polvere. Questo processo viene utilizzato per comprimere la polvere in una massa solida, creando un pezzo grezzo con una resistenza sufficiente per la manipolazione e la successiva lavorazione.
Differenziazione tra pressatura isostatica a sacco umido e a sacco secco
Una variante della pressatura isostatica a freddo è la tecnologia del sacco umido. In questo processo, la polvere viene riempita in uno stampo e sigillata ermeticamente all'esterno del recipiente in pressione. Lo stampo viene quindi immerso in un fluido ad alta pressione all'interno del recipiente e viene applicata una pressione isostatica per comprimere la polvere in una forma. La tecnologia a sacchi umidi è ideale per la produzione di più forme e di piccole e grandi quantità.
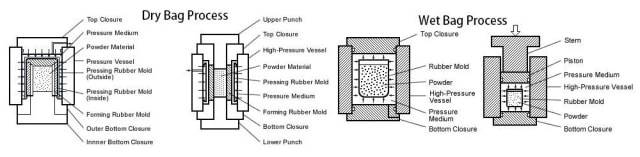
La pressatura isostatica a secco, invece, prevede la creazione di uno stampo integrato nel recipiente in pressione. La polvere viene aggiunta allo stampo, questo viene sigillato e la pressione viene applicata per comprimere la polvere. Questo processo elimina la necessità di immergere lo stampo in un fluido separato, facilitando l'automazione.
Ruolo della qualità della polvere e della progettazione degli stampi nel processo
La qualità della polvere utilizzata nella pressatura isostatica a freddo gioca un ruolo cruciale nel prodotto finale. La polvere deve avere una distribuzione granulometrica, una fluidità e una densità adeguate per garantire una compressione efficiente e uniforme. Inoltre, il design dell'attrezzatura, compreso lo stampo o il sacchetto utilizzato, deve essere attentamente progettato per soddisfare i requisiti specifici del materiale della polvere e della forma desiderata.
Un'adeguata progettazione degli utensili e la qualità della polvere sono essenziali per ottenere la densità e la resistenza desiderate nel prodotto finale. Questo aspetto è particolarmente importante in settori come quello aerospaziale, automobilistico e medicale, in cui sono fondamentali componenti affidabili e di alta qualità.
In sintesi, la pressatura isostatica a freddo è una tecnica versatile di lavorazione dei materiali che consente di comprimere i materiali in polvere in parti solide. La scelta tra la tecnologia wet bag e quella dry bag dipende dai requisiti di produzione specifici. Inoltre, la qualità della polvere e la progettazione degli utensili giocano un ruolo importante nel garantire i risultati desiderati nel prodotto finale.
Tipi di pressatura isostatica a freddo
Descrizione dettagliata della tecnica wet bag
Nella tecnica del sacco umido della pressatura isostatica a freddo, il materiale in polvere viene riempito in uno stampo e sigillato ermeticamente all'esterno del recipiente in pressione. Lo stampo riempito viene quindi immerso in un fluido in pressione all'interno del recipiente in pressione. La pressione isostatica viene applicata alla superficie esterna dello stampo, comprimendo la polvere in una massa solida.
Questo metodo non è così comune come l'altro tipo di pressatura isostatica a freddo, ma esistono oltre 3000 presse per sacchi umidi utilizzate in tutto il mondo. I sacchi a umido sono disponibili in varie dimensioni, da 50 mm a 2000 mm di diametro.
La lavorazione del materiale con la tecnologia dei sacchi a umido può durare da 5 a 30 minuti, il che la rende un processo relativamente lento. Tuttavia, l'uso di pompe ad alto volume e di meccanismi di caricamento migliorati può contribuire a velocizzare il processo.
Spiegazione della tecnica di pressatura con sacchi a secco
La tecnica di pressatura a secco, invece, prevede la creazione di uno stampo integrato nel recipiente a pressione. In questo processo, la polvere viene aggiunta allo stampo, che viene poi sigillato. Si applica la pressione e il pezzo risultante viene espulso.
Rispetto alla tecnica a sacchi umidi, il processo a sacchi secchi si presta all'automazione ed è adatto allo stampaggio di lunghe serie di compatti ad alti ritmi di produzione. L'integrazione dello stampo nel recipiente di pressione elimina la necessità della fase di immersione, rendendolo un metodo più efficiente.
Confronto tra le applicazioni delle due tecniche
La scelta tra le tecniche wet bag e dry bag dipende dai requisiti specifici dell'applicazione. La tecnologia wet bag è ideale per la produzione di più forme e di piccole e grandi quantità, nonché per la pressatura di prodotti di grandi dimensioni. Consente di creare forme complesse e di ottenere un'elevata densità di verde.
D'altra parte, la pressatura con sacchi a secco è più adatta all'automazione e ad alti tassi di produzione. Offre una più facile integrazione nel processo di produzione ed elimina la fase di immersione, con conseguenti tempi di produzione più rapidi.
In sintesi, sia la tecnica del sacco umido che quella del sacco a secco hanno i loro vantaggi e sono utilizzate in diverse applicazioni. La scelta tra le due tecniche dipende da fattori quali la forma desiderata, la quantità di produzione e il livello di automazione richiesto.
Vantaggi della pressatura isostatica a freddo rispetto alla pressatura con stampo monoassiale
Capacità di formare forme più complesse
La pressatura isostatica a freddo (CIP) offre il vantaggio di poter formare forme più complesse rispetto alla pressatura monoassiale. Con il CIP, la pressione viene applicata uniformemente su tutta la superficie dello stampo, consentendo la compattazione di forme complesse e dettagliate. Ciò è particolarmente vantaggioso quando si producono componenti con geometrie o design intricati che potrebbero essere difficili da ottenere con la pressatura monoassiale.

Riduzione delle distorsioni e delle cricche grazie all'impacchettamento uniforme delle particelle
Uno dei principali vantaggi della pressatura isostatica a freddo rispetto alla pressatura monoassiale è la riduzione delle distorsioni e delle cricche nel prodotto finale. Nel CIP, la pressione viene applicata in modo uniforme, con conseguente impacchettamento più uniforme delle particelle e riduzione dei gradienti di pressione. Ciò determina una distribuzione più omogenea della densità e riduce la probabilità di distorsioni e cricche nel componente finito. Questo vantaggio è particolarmente critico quando si tratta di componenti di forma complessa.
Secondo le considerazioni tecniche, il CIP fornisce una densità maggiore e più uniforme a una determinata pressione di compattazione, rendendolo particolarmente adatto alle polveri fragili o fini. Inoltre, l'assenza di attrito sulle pareti dello stampo nel CIP elimina i problemi associati alla rimozione del lubrificante e consente di ottenere densità di pressatura più elevate.
Inoltre, il CIP offre il vantaggio di un ritiro più uniforme durante la sinterizzazione, grazie alla densità verde uniforme. Ciò è essenziale per mantenere un buon controllo della forma e ottenere proprietà uniformi nel prodotto finale. Inoltre, il CIP non richiede un legante a base di cera come la pressatura uniassiale, eliminando la necessità di operazioni di deceratura.
In sintesi, i vantaggi della pressatura isostatica a freddo rispetto alla pressatura monoassiale includono la capacità di formare forme più complesse e la riduzione delle distorsioni e delle fessurazioni grazie all'impacchettamento uniforme delle particelle. Questi vantaggi rendono il CIP il metodo preferito per la produzione di componenti con geometrie complesse e per ottenere prodotti omogenei e di alta qualità.
La pressatura isostatica a freddo nella produzione di componenti di forma complessa
Confronto tra CIP e stampaggio a iniezione per la produzione di grandi volumi
Quando sono richiesti componenti di forma complessa, al di là delle capacità di forma dello stampaggio monoassiale, e si necessita di una produzione in grandi volumi, il CIP e lo stampaggio a iniezione sono le due opzioni principali utilizzate. Il CIP è stato il primo metodo high-tech riportato in letteratura per la produzione di ceramiche di allumina, da Daubenmeyer nel 1934. In effetti, gli isolatori per candele di accensione sono probabilmente il componente ceramico CIP con il maggior volume di produzione a livello globale. Una percentuale significativa dei 3 miliardi di isolatori per candele prodotti ogni anno è sottoposta a CIP. Come per la pressatura uniassiale, il materiale di partenza del CIP è generalmente semplice allumina Bayer macinata, allumina Bayer macinata ed essiccata a spruzzo o, in rari casi, nanopolveri SolGel essiccate a spruzzo ad alta tecnologia. Tuttavia, in generale, il CIP non è così comune a livello industriale come lo stampaggio a iniezione. Il CIP viene generalmente utilizzato solo quando sono richieste forme molto complesse e lo stampaggio a iniezione non è praticabile per qualsiasi motivo.
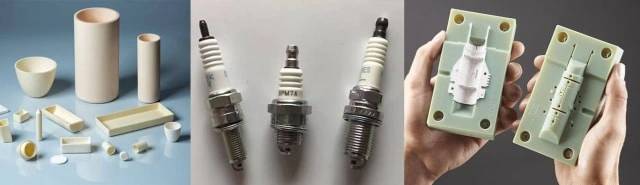
Panoramica storica dell'uso del CIP nella produzione di ceramica di allumina
La pressatura isostatica a freddo (CIP) è una tecnologia a base di polveri, quasi a forma di rete, per la produzione di componenti in metallo e ceramica. Il CIP è stato comunemente utilizzato per la lavorazione della ceramica, ma non altrettanto per i metalli. I recenti sviluppi nella capacità di processo e nella metallurgia delle polveri, tuttavia, hanno permesso di utilizzare sempre più il CIP nella produzione di componenti metallici ad alte prestazioni. Vantaggi quali la lavorazione allo stato solido, la microstruttura uniforme, la complessità della forma, i bassi costi di attrezzaggio e la scalabilità del processo hanno reso il CIP una via di lavorazione praticabile per i metalli. Inoltre, la possibilità di produrre pezzi di forma quasi netta con uno scarto minimo di materiale ha reso il processo più ampiamente accettabile in applicazioni di nicchia, come quelle aerospaziali e automobilistiche.
Uso del CIP nella produzione di isolatori per candele di accensione
Per decenni, la pressatura isostatica a freddo (CIP) è stata utilizzata con successo dai produttori di tutto il mondo. Il CIP viene utilizzato per consolidare le polveri metalliche e ceramiche per ottenere un pezzo "verde" che può essere sottoposto a ulteriori trattamenti, come la laminazione, la lavorazione o la sinterizzazione.
Con pressioni tipiche da 1.035 a 4.138 bar (da 15.000 a 60.000 psi) e temperature ambiente fino a 93°C (200°F), il CIP può raggiungere il 95% della densità teorica per la ceramica.
Un processo collaudato per parti ad alte prestazioni Le applicazioni comuni della pressatura isostatica a freddo comprendono il consolidamento di polveri ceramiche, la compressione di grafite, refrattari e isolanti elettrici e altre ceramiche fini per applicazioni dentali e mediche.
La tecnologia si sta espandendo in nuove applicazioni, come la pressatura di bersagli per lo sputtering, il rivestimento di parti di valvole in un motore per ridurre al minimo l'usura delle testate, le telecomunicazioni, l'elettronica, il settore aerospaziale e automobilistico.
Presse isostatiche a freddo
Le presse isostatiche a freddo (CIP) EPSI sono utilizzate per produrre componenti in polvere metallica non sinterizzati o compattati con coloranti verdi in una fase preliminare di densificazione prima della laminazione, della lavorazione o della sinterizzazione. I nostri sistemi CIP sono utilizzati da aziende di tutto il mondo per produrre efficacemente componenti impeccabili per l'industria aerospaziale, militare, industriale e medica. I leader tecnologici di tutto il mondo sanno che le nostre presse isostatiche a freddo sono progettate in modo tale che i pezzi possano essere facilmente rimossi con una resistenza verde sufficiente per la successiva manipolazione e sinterizzazione.
Pressatura isostatica a freddo
La pressatura isostatica a freddo offre il vantaggio di produrre pezzi per i quali l'elevato costo iniziale degli stampi di pressatura non può essere giustificato o quando sono necessarie compattezze molto grandi o complesse. È possibile pressare isostaticamente su scala commerciale una varietà di polveri, tra cui metalli, ceramiche, plastiche e compositi. Le pressioni richieste per la compattazione vanno da meno di 5.000 psi a più di 100.000 psi (da 34,5 a 690 MPa). Le polveri vengono compattate in stampi elastomerici con un processo a umido o a secco.
Le capacità dei materiali sono importanti da considerare quando si scelgono i servizi di pressatura isostatica a freddo. Le leghe di alluminio e magnesio, i carburi e gli utensili da taglio, il carbonio e la grafite, le ceramiche e i compositi sono solo alcuni dei materiali e dei componenti che vengono prodotti con il CIP. Alcuni servizi di pressatura isostatica a freddo sono specializzati in rivestimenti e depositi di spray termici, leghe di rame, diamanti e materiali simili ai diamanti. Altri lavorano con materiali elettronici o elettrici, esplosivi o pirotecnici, o materiali speciali e proprietari.
DESCRIZIONE DELLA PRESSATURA ISOSTATICA A FREDDO
La pressatura isostatica a freddo (CIP) è un processo utilizzato per modellare e compattare le polveri in componenti di dimensioni e forme diverse. Nella pressatura isostatica a freddo (CIP) a sacchi umidi, il materiale viene preformato e poi sigillato in un sacco flessibile o in uno stampo. Il sacco viene posto all'interno di un fluido idraulico (ad esempio, olio o acqua) in un recipiente a pressione. Al fluido viene applicata una pressione, solitamente compresa tra 10.000 e 60.000 psi, che viene distribuita uniformemente sul materiale. Questo metodo contribuisce a ridurre la distorsione, a migliorare la precisione e a ridurre il rischio di intrappolamento di aria e di vuoti. È ampiamente utilizzato nella produzione di componenti per applicazioni mediche, aerospaziali e automobilistiche.
Il controllo dimensionale con il CIP è minore rispetto alla pressatura uniassiale. Ad esempio, se si desidera un diametro di 5 mm esatti, è necessario procedere per tentativi, errori e calcoli nella procedura di stampaggio e riempimento. Ma una volta che si è arrivati a questo punto, si tratta di un processo molto ripetibile che offre alcuni vantaggi distinti. Tra cui la possibilità di stampare pellet con un rapporto d'aspetto molto lungo. Le candele di accensione sono un esempio di un articolo comune che viene pressato isostaticamente a freddo su scala industriale.
Pressatura isostatica a freddo
La pressatura isostatica a freddo (CIP) viene eseguita a temperatura ambiente e utilizza uno stampo in materiale elastomerico come uretano, gomma o cloruro di polivinile. Il fluido nella pressatura isostatica a freddo è solitamente olio o acqua. La pressione del fluido durante l'operazione è in genere compresa tra 60.000 lbs/in2 (400 MPa) e 150.000 lbs/in2 (1000 MPa). Uno svantaggio di questo processo di produzione è la bassa precisione geometrica dovuta alla flessibilità dello stampo. Per prima cosa la polvere viene compattata a una densità molto uniforme mediante pressatura isostatica a freddo. Quindi il compatto verde viene solitamente sinterizzato in modo convenzionale, per produrre il pezzo desiderato.
Processo di pressatura isostatica a freddo
Spiegazione del processo CIP
La pressatura isostatica a freddo (CIP) è un metodo di lavorazione dei materiali che consiste nel compattare le polveri racchiudendole in uno stampo in elastomero. Lo stampo è realizzato con materiali come l'uretano, la gomma o il cloruro di polivinile, che hanno una bassa resistenza alla deformazione. Una pressione liquida viene quindi applicata uniformemente allo stampo per comprimerlo. Questo processo si basa sulla legge di Pascal, secondo la quale la pressione applicata a un fluido chiuso si trasmette in tutte le direzioni senza alcuna variazione di grandezza.
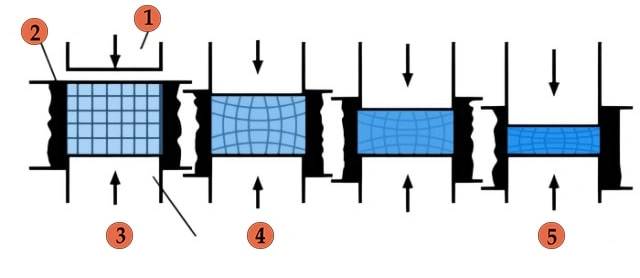
La CIP può essere utilizzata per vari materiali come plastica, grafite, polvere metallurgica, ceramica e obiettivi di sputtering. Viene comunemente utilizzato per ottenere un pezzo "grezzo" con una resistenza sufficiente per la manipolazione e la lavorazione, che può poi essere ulteriormente sinterizzato per ottenere la resistenza finale.
Automazione del processo CIP
Il processo CIP può essere automatizzato utilizzando apparecchiature specializzate. Il materiale da lavorare viene sigillato in uno stampo in elastomero e posto in una camera di pressione. Un mezzo liquido, come acqua o olio, viene pompato nella camera e lo stampo viene sottoposto uniformemente ad alta pressione da tutti i lati. L'automazione garantisce un'applicazione costante e precisa della pressione, che si traduce in prodotti finiti di alta qualità.
L'automazione del processo CIP offre diversi vantaggi. Migliora l'efficienza riducendo il lavoro manuale e aumentando i tassi di produzione. Inoltre, garantisce un'applicazione costante della pressione, migliorando la qualità e l'affidabilità dei prodotti finiti. Inoltre, l'automazione consente un migliore controllo e monitoraggio dei parametri di processo, con conseguente ottimizzazione del processo e risparmio sui costi.
Cicli di pressurizzazione e depressurizzazione nel CIP
Il processo CIP prevede cicli di pressurizzazione e depressurizzazione per ottenere la compattazione desiderata delle polveri. Durante il ciclo di pressurizzazione, il mezzo liquido viene pompato nella camera di pressione, applicando una pressione uniforme allo stampo in elastomero. Questa pressione compatta le polveri e forma un solido altamente compatto.
Una volta ottenuta la compattazione desiderata, inizia il ciclo di depressurizzazione. La pressione nella camera viene gradualmente rilasciata, consentendo allo stampo di rilassarsi e al materiale compattato di essere rimosso. Questo ciclo assicura che il materiale compattato possa essere facilmente estratto dallo stampo senza deformazioni o danni.
I cicli di pressurizzazione e depressurizzazione sono attentamente controllati per ottenere la densità e la resistenza desiderate del materiale compattato. I parametri, come l'entità della pressione, la durata e la velocità di variazione, possono essere regolati in base ai requisiti specifici del materiale da lavorare.
In conclusione, la pressatura isostatica a freddo (CIP) è un metodo versatile per compattare le polveri e modellare i materiali. Racchiudendo le polveri in uno stampo in elastomero e applicando una pressione uniforme, il CIP può produrre solidi altamente compatti per diverse applicazioni. L'automazione del processo CIP offre maggiore efficienza e controllo, mentre i cicli di pressurizzazione e depressurizzazione garantiscono la densità e la resistenza desiderate del materiale compattato.
Vantaggi della pressatura isostatica a freddo per la ceramica di allumina
Confronto tra il CIP e la pressatura monoassiale e altri metodi di formatura della ceramica
La pressatura isostatica a freddo (CIP) è una tecnologia a base di polveri, quasi a forma di rete, per la produzione di componenti in metallo e ceramica. Il CIP è stato comunemente utilizzato per la lavorazione della ceramica, ma non altrettanto per i metalli. I recenti sviluppi nella capacità di processo e nella metallurgia delle polveri, tuttavia, hanno permesso di utilizzare sempre più il CIP nella produzione di componenti metallici ad alte prestazioni. Vantaggi quali la lavorazione allo stato solido, la microstruttura uniforme, la complessità della forma, i bassi costi di attrezzaggio e la scalabilità del processo hanno reso il CIP una via di lavorazione praticabile per i metalli.
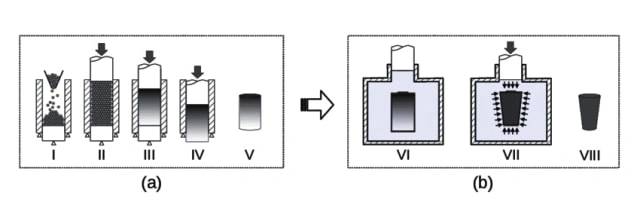
Alcuni dei principali vantaggi del CIP per le ceramiche di allumina rispetto allo stampaggio monoassiale sono i seguenti:
-
Sono possibili forme più complesse: Il CIP consente di produrre forme più complesse rispetto alla pressatura monoassiale. Ciò è dovuto al fatto che il CIP utilizza stampi flessibili che possono accogliere disegni e forme complesse.
-
Gradienti di pressione di pressatura notevolmente ridotti: Il CIP riduce in modo significativo i gradienti di pressione di pressatura, contribuendo a minimizzare la distorsione e la fessurazione durante il processo di formatura. Ciò garantisce che i componenti ceramici finali abbiano una maggiore precisione dimensionale e integrità strutturale.
Vantaggi del CIP per pezzi complessi con piccole tirature
Il CIP offre diversi vantaggi per la produzione di pezzi complessi con piccole tirature. Questi vantaggi includono:
-
Basso costo dello stampo: Il CIP richiede un basso costo dello stampo, che lo rende ideale per la produzione di pezzi complessi con piccole tirature. A differenza di altri metodi di formatura della ceramica, il CIP non richiede stampi costosi, il che contribuisce a ridurre i costi di produzione.
-
Nessun costo di stampo per il post-CIP: Oltre al basso costo degli stampi, il CIP elimina anche la necessità di stampi nei processi post-CIP. Ciò riduce ulteriormente i costi di produzione e consente una maggiore flessibilità nella produzione di pezzi complessi.
-
Nessuna limitazione di dimensioni: Il CIP non ha limiti di dimensioni, ad eccezione dei limiti della camera di pressatura. Questo lo rende adatto alla produzione di componenti molto grandi, soprattutto di forme complesse. Infatti, con il CIP sono stati prodotti con successo componenti di peso superiore a 1 tonnellata.
-
Tempi di ciclo di lavorazione brevi: Il CIP ha tempi di lavorazione brevi perché non richiede l'essiccazione o la combustione del legante. Ciò significa che i componenti ceramici formati possono essere sinterizzati più rapidamente rispetto ad altri metodi, con conseguente aumento dell'efficienza produttiva.
Sebbene il CIP offra numerosi vantaggi per le ceramiche di allumina, è importante notare alcuni dei suoi limiti. Tra questi, il controllo dimensionale limitato, la complessità della forma inferiore a quella dello stampaggio a iniezione di polveri (PIM) e la necessità di polveri con un'eccellente fluidità.
Nel complesso, la pressatura isostatica a freddo è un metodo versatile ed economico per la produzione di ceramica di allumina con forme complesse e piccole tirature. I suoi vantaggi in termini di complessità della forma, gradienti di pressione ridotti, basso costo dello stampo e tempi di lavorazione più rapidi ne fanno una scelta popolare in vari settori come quello automobilistico, aerospaziale e delle telecomunicazioni.
Svantaggi della pressatura isostatica a freddo per la ceramica
Problemi di controllo dimensionale e complessità della forma
La pressatura isostatica a freddo (CIP) è un processo di compattazione delle polveri utilizzato per ottenere pezzi pronti per la sinterizzazione. Tuttavia, l'uso del CIP per la ceramica presenta alcune sfide legate al controllo dimensionale e alla complessità della forma.
La minore precisione delle superfici pressate adiacenti al sacco flessibile rispetto alla pressatura meccanica o all'estrusione richiede spesso una lavorazione successiva. Ciò significa che possono essere necessari ulteriori passaggi per ottenere le dimensioni e la forma desiderate delle parti in ceramica.
Requisiti delle polveri utilizzate nel CIP
Uno degli svantaggi della pressatura isostatica a freddo è che per le presse a sacchi a secco completamente automatiche è normalmente necessaria una polvere essiccata a spruzzo relativamente costosa. Ciò può aumentare il costo complessivo del processo, poiché è necessario utilizzare polveri specializzate.
Inoltre, i tassi di produzione per il CIP sono inferiori rispetto all'estrusione o alla compattazione in stampo. Ciò significa che il processo potrebbe non essere altrettanto efficiente in termini di produzione di volumi.
In sintesi, se da un lato la pressatura isostatica a freddo offre dei vantaggi, come la capacità di produrre compatti grandi o complessi e l'uso di una varietà di polveri, dall'altro presenta alcuni svantaggi. Tra questi, le difficoltà legate al controllo dimensionale e alla complessità della forma, i requisiti per le polveri speciali e i tassi di produzione inferiori rispetto ad altri metodi di formatura.
Applicazioni della pressatura isostatica a freddo
Uso comune del CIP nella produzione di massa di ceramiche avanzate
La pressatura isostatica a freddo (CIP) è una tecnologia a base di polveri, quasi a forma di rete, comunemente utilizzata per la lavorazione della ceramica. Ha il vantaggio di poter produrre pezzi in cui l'elevato costo iniziale degli stampi di pressatura non è giustificato o quando sono necessari compatti molto grandi o complessi.

È possibile pressare isostaticamente su scala commerciale una varietà di polveri, tra cui metalli, ceramiche, plastiche e compositi. Le pressioni richieste per la compattazione variano da meno di 5.000 psi a più di 100.000 psi. Le polveri vengono compattate in stampi elastomerici con un processo a sacchi umidi o a secco.
Il CIP è stato ampiamente utilizzato per il consolidamento di polveri ceramiche, grafite, materiali refrattari, isolanti elettrici e per la compressione di ceramiche avanzate. Materiali come nitruro di silicio, carburo di silicio, nitruro di boro, carburo di boro, boruro di titanio e spinello possono essere lavorati con il CIP.
La tecnologia si sta espandendo in nuove applicazioni, come la compressione di bersagli per sputtering, il rivestimento di componenti di valvole utilizzate per ridurre l'usura dei cilindri nei motori e varie applicazioni nelle telecomunicazioni, nell'elettronica, nell'industria aerospaziale e automobilistica.
Esempi di componenti prodotti da CIP
Il CIP è comunemente utilizzato per il consolidamento di polveri ceramiche, la compressione di grafite, refrattari e isolanti elettrici, nonché di altre ceramiche fini per applicazioni dentali e mediche. Viene utilizzato anche per la pressatura di bersagli sputtering, per il rivestimento di parti di valvole nei motori per ridurre al minimo l'usura delle testate e in varie applicazioni nei settori delle telecomunicazioni, dell'elettronica, dell'aerospaziale e dell'industria automobilistica.
Le apparecchiature CIP sono utilizzate per comprimere i costi di produzione e sono essenziali per la produzione di prodotti finiti a partire dalle materie prime. Il processo prevede il confinamento delle polveri in uno stampo in elastomero, il posizionamento dello stampo in una camera di pressione, il pompaggio di un mezzo liquido e l'applicazione uniforme di un'elevata pressione su tutti i lati dello stampo. Il CIP può essere utilizzato con polveri metallurgiche, carburi cementati, materiali refrattari, grafite, ceramica, plastica e altri materiali.
Le capacità dei materiali sono importanti da considerare quando si scelgono i servizi di pressatura isostatica a freddo. Leghe di alluminio e magnesio, carburi e utensili da taglio, carbonio e grafite, ceramiche, compositi e altri materiali possono essere prodotti con la CIP. Alcuni servizi di pressatura isostatica a freddo sono specializzati in rivestimenti e depositi a spruzzo termico, leghe di rame, diamanti e materiali simili ai diamanti, materiali elettronici o elettrici, esplosivi o pirotecnici, o materiali speciali e proprietari.
La pressatura isostatica a freddo viene eseguita a temperatura ambiente e utilizza uno stampo in materiale elastomerico come uretano, gomma o cloruro di polivinile. Il fluido utilizzato nella pressatura isostatica a freddo è solitamente olio o acqua e la pressione del fluido durante l'operazione varia tipicamente da 60.000 lbs/in2 a 150.000 lbs/in2. Uno svantaggio di questo processo produttivo è la bassa precisione geometrica dovuta alla flessibilità dello stampo.
In sintesi, la pressatura isostatica a freddo (CIP) è una tecnica preziosa per la produzione di massa di ceramiche avanzate e altri materiali. Offre vantaggi quali la lavorazione allo stato solido, la microstruttura uniforme, la complessità della forma, il basso costo degli utensili e la scalabilità del processo. Il CIP è ampiamente utilizzato in vari settori industriali e continua ad espandersi in nuove applicazioni.
Tecnologie di compressione alternative
Panoramica delle altre tecnologie di compressione
Nel campo della lavorazione dei materiali, sono disponibili diverse tecniche di compressione potenti. Due di queste tecniche, la pressatura isostatica a freddo (CIP) e la pressatura isostatica a caldo (HIP), sono ampiamente utilizzate in vari settori. Entrambi i metodi mirano a migliorare le proprietà dei materiali, ma si differenziano per le condizioni operative e offrono vantaggi unici.
Introduzione della compattazione a onde d'urto come alternativa
Sebbene CIP e HIP siano tecniche di compressione efficaci, sono state sviluppate tecnologie alternative per affrontare sfide specifiche. Una di queste alternative è la compattazione a onde d'urto, nota anche come compressione d'urto.
La compattazione a onde d'urto comporta la generazione di un'onda d'urto breve e ad alta pressione che può deformare gravemente le particelle o addirittura causare una fusione locale. Questo processo può portare il materiale a diventare completamente denso e compatto senza una crescita significativa dei grani. Le onde d'urto sono caratterizzate da pressioni molto elevate, temperature medie, tempi di reazione molto brevi e tassi di deformazione molto elevati.
Diversi metodi, come le pistole ad aria compressa e le onde d'urto esplosive, precedentemente utilizzati per la compressione di polveri di dimensioni micrometriche, vengono ora impiegati per comprimere le nanopolveri. Queste tecnologie di compressione alternative, con tempi di riscaldamento molto brevi, hanno dimostrato di riuscire a ottenere materiali completamente densi e compatti, senza la formazione di grani nanometrici.
Un esempio di compattazione a onde d'urto è l'uso di un dispositivo di compattazione a onde d'urto piane dotato di una pistola ad aria compressa. Questo dispositivo genera un'onda d'urto breve e ad alta pressione in grado di deformare le particelle e di ottenere una densità e una compattazione complete. Queste tecnologie di compressione alternative offrono un modo efficiente di lavorare i materiali con una crescita minima dei grani e un miglioramento delle proprietà del materiale.
Nell'industria della gomma, le presse a compressione avanzate sono utilizzate per una vulcanizzazione efficiente della gomma. Applicando una forza di pressione controllata sui materiali in gomma, queste macchine testano le caratteristiche fisiche dei prodotti in gomma, come la resistenza, la resilienza e la durata, assicurando che siano conformi agli standard ASTM e di alta qualità.
Nel complesso, le tecnologie di compressione alternative, come la compattazione a onde d'urto, forniscono soluzioni innovative per ottenere materiali completamente densi e compatti con proprietà migliorate. Queste tecnologie offrono vantaggi unici e possono essere utilizzate in vari settori per migliorare le capacità di lavorazione dei materiali.
Conclusioni
In conclusione,la pressatura isostatica a freddo (CIP) è una tecnica molto versatile ed efficiente per la produzione di componenti di forma complessa, in particolare nella produzione di ceramiche avanzate. A differenza della tradizionale pressatura monoassiale, la CIP consente la formazione di forme più complesse e riduce il rischio di distorsioni e fessurazioni grazie all'impacchettamento uniforme delle particelle. Nonostante le difficoltà legate al controllo dimensionale e ai requisiti della polvere, il CIP offre vantaggi significativi per le piccole serie ed è ampiamente utilizzato nella produzione di massa di ceramiche avanzate. In alternativa al CIP, vale la pena considerare anche la compattazione a onde d'urto per alcune applicazioni di compressione.
CONTATTATECI PER UNA CONSULENZA GRATUITA
I prodotti e i servizi di KINTEK LAB SOLUTION sono stati riconosciuti da clienti di tutto il mondo. Il nostro personale sarà lieto di assistervi per qualsiasi richiesta. Contattateci per una consulenza gratuita e parlate con uno specialista del prodotto per trovare la soluzione più adatta alle vostre esigenze applicative!