Introduzione alla tecnologia di pressatura isostatica a caldo (HIP)
Definizione e principi di base
La pressatura isostatica a caldo (HIP) è una tecnologia sofisticata che impiega gas inerti come azoto e argon come mezzo di trasmissione della pressione. Questo metodo sottopone un prodotto a una pressione uniforme da tutte le direzioni in condizioni di alta temperatura e pressione. Il processo prevede la pressatura e la sinterizzazione del prodotto, con significativi miglioramenti in termini di densità, uniformità e prestazioni complessive.
Il principio fondamentale dell'HIP risiede nella capacità di applicare una pressione isotropa, garantendo che il materiale subisca una deformazione e una densificazione uniformi. Questa uniformità è fondamentale per migliorare le proprietà meccaniche e l'integrità microstrutturale del materiale. I gas inerti utilizzati nel processo non solo facilitano la trasmissione della pressione, ma prevengono anche eventuali reazioni chimiche che potrebbero compromettere l'integrità del materiale.
Il processo HIP può essere suddiviso in diverse fasi chiave:
- Avvicinamento e riarrangiamento delle particelle: Inizialmente, le particelle all'interno del materiale si avvicinano l'una all'altra e si riorganizzano per riempire vuoti e spazi vuoti.
- Deformazione plastica: Con l'aumento della pressione, le particelle subiscono una deformazione plastica, riducendo ulteriormente il volume dei vuoti.
- Diffusione Creep: Infine, entrano in gioco i meccanismi di diffusione, che permettono alle particelle di legarsi a livello atomico, dando vita a un prodotto completamente densificato e sinterizzato.
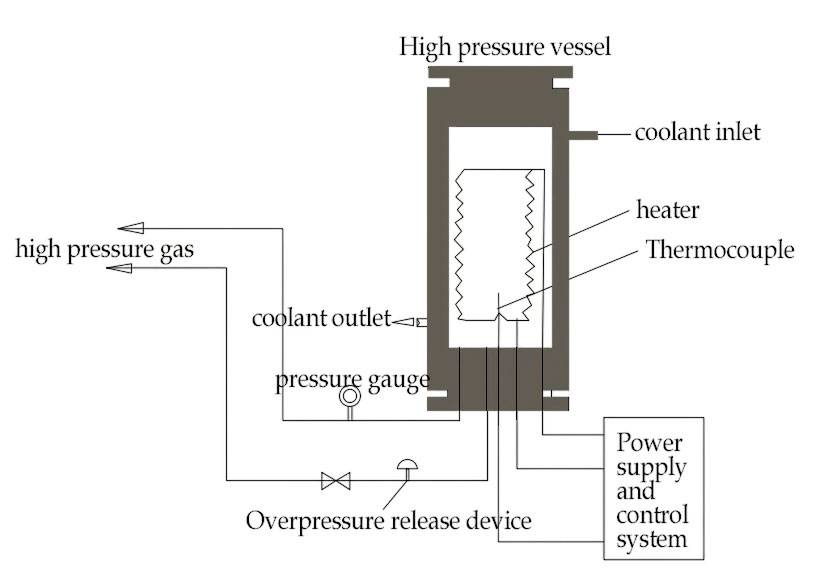
Questo processo a più fasi garantisce che il prodotto finale non solo soddisfi, ma spesso superi gli standard di prestazione stabiliti dai metodi di produzione tradizionali. La combinazione di alta temperatura e pressione uniforme crea un effetto sinergico che migliora le proprietà del materiale, rendendo l'HIP una tecnologia indispensabile in diverse applicazioni ad alte prestazioni.
Sviluppo storico e applicazioni attuali
La tecnologia della pressatura isostatica a caldo (HIP) è stata ampiamente adottata in diversi settori, contribuendo in modo significativo alla produzione di prodotti di alta qualità e allo sviluppo di nuovi materiali. Inizialmente, la sua applicazione si concentrava principalmente nell'industria aerospaziale e aeronautica, dove la necessità di materiali con proprietà meccaniche superiori e alta affidabilità era fondamentale. Nel corso del tempo, la tecnologia HIP si è estesa ai settori dell'energia, dei trasporti, dell'ingegneria elettrica, dell'elettronica, dell'industria chimica e della metallurgia.
Nell'industria aerospaziale, l'HIP viene utilizzato per produrre componenti con geometrie complesse che richiedono elevata resistenza e peso ridotto, come le pale delle turbine e le parti strutturali. Il settore energetico trae vantaggio dall'HIP attraverso la creazione di componenti per reattori nucleari e turbine a gas, che richiedono un'eccezionale durata e resistenza a temperature e pressioni elevate. Le applicazioni nel settore dei trasporti includono la produzione di componenti per sistemi automobilistici e ferroviari, che migliorano le prestazioni e la sicurezza.
Anche l'ingegneria elettrica e l'elettronica hanno sfruttato la tecnologia HIP per sviluppare materiali ad alte prestazioni per dispositivi elettronici e sistemi di alimentazione. Nell'industria chimica, l'HIP viene impiegato per produrre componenti e catalizzatori resistenti alla corrosione, mentre in metallurgia contribuisce alla produzione di leghe ad alta resistenza e alla riparazione di parti metalliche.
La versatilità della tecnologia HIP è ulteriormente dimostrata dalle sue applicazioni emergenti in nuovi campi. Ad esempio, se ne sta studiando l'utilizzo nei materiali porosi, nei trattamenti superficiali, nella preparazione di materiali ad alta purezza e persino nell'industria alimentare a scopo di sterilizzazione. Queste diverse applicazioni sottolineano l'ampio impatto e il potenziale della tecnologia HIP nei moderni processi industriali.
Componenti e principi di funzionamento delle apparecchiature HIP
Componenti chiave delle apparecchiature HIP
L'attrezzatura essenziale per la tecnologia HIP (Hot Isostatic Pressing) comprende diversi componenti critici, ognuno dei quali svolge un ruolo vitale nel processo. Questi componenti comprendono un recipiente ad alta pressione, un forno di riscaldamento, un compressore, una pompa a vuoto, un serbatoio di stoccaggio del gas, un sistema di raffreddamento e un sistema di controllo computerizzato.
- Recipiente ad alta pressione: È il componente principale del sistema HIP. È progettato per resistere a pressioni e temperature estreme, garantendo il contenimento sicuro dei materiali sottoposti a trattamento.
- Forno di riscaldamento: Responsabile del riscaldamento dei materiali alla temperatura richiesta, il forno è fondamentale per avviare il processo di sinterizzazione.
- Compressore: Questo componente genera la pressione necessaria per compattare i materiali, garantendo uniformità e densità.
- Pompa del vuoto: Prima dell'applicazione della pressione, la pompa del vuoto rimuove l'aria e altri gas dal sistema, creando un ambiente controllato per il processo HIP.
- Serbatoio di stoccaggio del gas: Immagazzina il gas inerte utilizzato come mezzo di pressione, garantendo una fornitura costante durante il processo di pressatura.
- Sistema di raffreddamento: Dopo la pressatura e la sinterizzazione, il sistema di raffreddamento raffredda rapidamente i materiali per evitare reazioni indesiderate e stabilizzare il prodotto finale.
- Sistema di controllo computerizzato: Gestisce e monitora tutti gli aspetti del processo HIP, dal controllo della temperatura e della pressione alla raccolta e all'analisi dei dati, garantendo precisione ed efficienza.
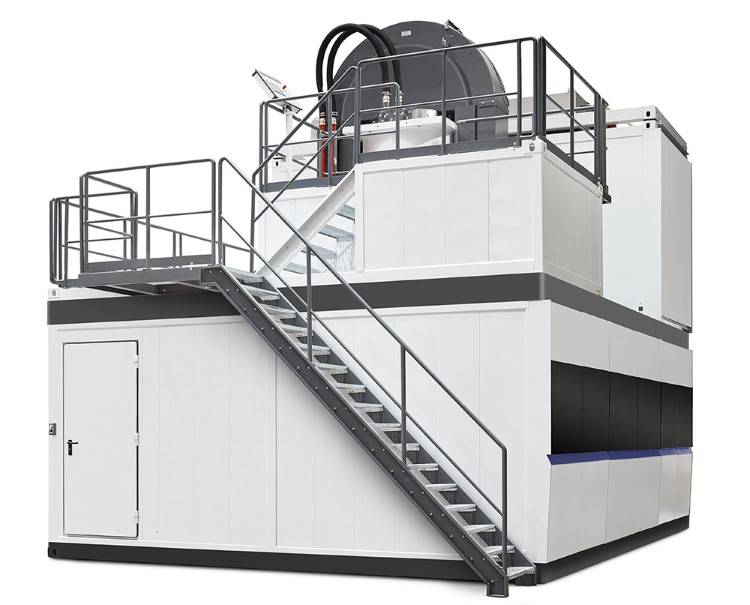
Ciascuno di questi componenti è stato meticolosamente progettato per funzionare in armonia, consentendo alla tecnologia HIP di fornire prodotti di alta qualità, densi e uniformi in diversi settori industriali.
Flusso di processo e meccanismi di densificazione
Il processo di pressatura isostatica a caldo (HIP) è una sequenza meticolosamente orchestrata di fasi che contribuiscono collettivamente alla densificazione dei materiali in polvere. Questo processo può essere suddiviso in tre fasi principali: avvicinamento e riarrangiamento delle particelle, deformazione plastica e scorrimento per diffusione. Ognuna di queste fasi svolge un ruolo cruciale nel raggiungimento del livello di densificazione desiderato e spesso operano in tandem piuttosto che in sequenza.
Nella fase iniziale,avvicinamento e riarrangiamento delle particellele particelle di polvere vengono avvicinate e riorganizzate per ottimizzare la loro densità di impaccamento. Questa fase è fondamentale per gettare le basi dei successivi processi di densificazione. Le particelle si muovono e si allineano in modo da ridurre al minimo i vuoti e massimizzare i punti di contatto, creando una struttura più coesa.
La seconda fase,deformazione plasticaprevede l'applicazione di uno stress meccanico che provoca la deformazione plastica delle particelle di polvere. Questa deformazione è facilitata dalle condizioni di alta pressione e temperatura mantenute durante il processo HIP. Man mano che le particelle si deformano, riempiono i vuoti lasciati dalla fase di riarrangiamento, riducendo ulteriormente la porosità complessiva del materiale.
Lo stadio finale,diffusione striscianteè il momento in cui il processo di densificazione raggiunge il suo apice. In presenza di temperature e pressioni elevate, la diffusione atomica diventa significativa. Questa diffusione consente di eliminare i vuoti residui e le microfessure, ottenendo un materiale quasi completamente denso e privo di difetti interni significativi. Il funzionamento simultaneo di queste fasi garantisce la trasformazione della polvere in un prodotto finale ad alta densità, omogeneo e meccanicamente robusto.
Fase | Descrizione |
---|---|
Avvicinamento e riorganizzazione delle particelle | Le particelle di polvere vengono avvicinate e riorganizzate per ottimizzare l'impacchettamento. |
Deformazione plastica | Le particelle si deformano plasticamente sotto pressione e temperatura elevate. |
Diffusione Creep | La diffusione atomica elimina vuoti e microfessure, ottenendo una densificazione completa. |
Questo processo a più stadi non solo migliora le proprietà meccaniche del materiale, ma garantisce anche l'uniformità dell'intero prodotto, rendendolo adatto ad applicazioni impegnative in settori come quello aerospaziale, automobilistico ed energetico.
Applicazioni della tecnologia HIP
Trattamento di densificazione dei getti
La tecnologia di pressatura isostatica a caldo (HIP) è fondamentale sia per la densificazione di nuove fusioni che per la riparazione di quelle usate, ripristinando efficacemente le loro prestazioni a livelli incontaminati. Eliminando i difetti interni, come microporosità e microfratture, l'HIP assicura che i getti soddisfino i più alti standard di prestazioni del materiale. Questo processo è particolarmente importante per materiali come l'alluminio, il titanio e le leghe ad alta temperatura, dove le velocità di raffreddamento durante il processo di formatura possono portare a strutture interne non uniformi.
Nel caso delle leghe di titanio, ad esempio, nonostante i significativi progressi nelle tecniche di colata di precisione, l'HIP rimane un passaggio indispensabile nella fase di post-lavorazione. L'applicazione di una pressione gassosa a temperature elevate induce una deformazione plastica e un legame per diffusione, eliminando così la microporosità interna e migliorando le proprietà meccaniche complessive dei getti.
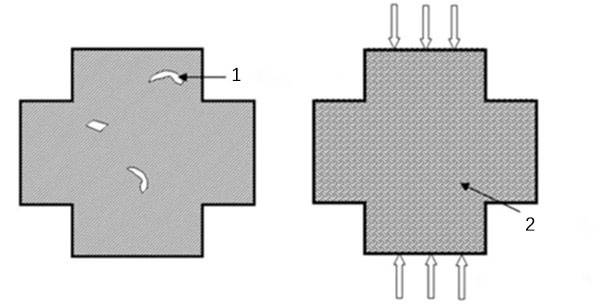
I vantaggi della HIP nella densificazione dei getti sono molteplici. Non solo migliora la consistenza del prodotto riducendo le variazioni delle proprietà meccaniche, ma migliora anche in modo significativo i parametri di prestazione chiave. Ad esempio, le resistenze alla trazione e alla prova aumentano in genere di circa il 5%, mentre la duttilità può migliorare fino al 50%. Inoltre, le proprietà di fatica dei getti trattati con HIP possono migliorare fino a dieci volte, raggiungendo una durata a fatica paragonabile a quella delle leghe battute. Questo miglioramento si estende ad altre proprietà critiche come la resistenza all'urto, la tenacità e la finitura superficiale lavorata.
In sintesi, il ruolo dell'HIP nella densificazione dei getti è fondamentale e offre un percorso per ottimizzare le prestazioni dei getti ed estenderne l'applicabilità a nuove e più impegnative applicazioni.
Rivestimento e incollaggio per diffusione dei compositi
La tecnologia di pressatura isostatica a caldo (HIP) offre metodi avanzati per migliorare le prestazioni dei materiali attraverso processi come il rivestimento e l'incollaggio per diffusione dei compositi. Queste tecniche sono particolarmente utili per l'incollaggio di materiali dissimili, che possono migliorare significativamente la resistenza e la durata complessiva dei componenti.
Incollaggio per diffusione: Un processo versatile
L'incollaggio per diffusione, un aspetto chiave della tecnologia HIP, consente di unire senza soluzione di continuità materiali simili e dissimili, sia in polvere che in forma solida. Questo processo elimina la necessità di ricorrere ai metodi di saldatura tradizionali, riducendo il numero di saldature e le relative ispezioni. Il risultato è un processo produttivo più affidabile ed economico.
Rivestimento: Ottimizzazione dell'uso del materiale
Il rivestimento tramite HIP consente di formare componenti con materiali pregiati o costosi solo nelle aree critiche. Questo uso strategico dei materiali non solo riduce i costi complessivi, ma garantisce anche che le aree più esigenti del componente ricevano i materiali della migliore qualità. Ad esempio, nelle applicazioni aerospaziali, ciò può significare l'utilizzo di leghe leggere in aree non critiche e di leghe ad alta resistenza in aree soggette a sollecitazioni estreme.
Vantaggi del rivestimento HIP e dell'incollaggio per diffusione
Benefici | Descrizione |
---|---|
Riduzione delle saldature | Elimina o riduce il numero di saldature, minimizzando i potenziali punti di rottura. |
Efficienza dei costi | Ottimizza l'uso dei materiali, riducendo la necessità di leghe costose. |
Prestazioni migliorate | Migliora la resistenza e la durata complessiva dei componenti grazie all'incollaggio senza saldature. |
Versatilità | Adatto a un'ampia gamma di materiali, comprese le leghe refrattarie e ad alta resistenza. |
In sintesi, il rivestimento HIP e l'incollaggio per diffusione dei compositi sono processi trasformativi che non solo migliorano le prestazioni dei materiali, ma offrono anche significativi vantaggi economici e operativi. Applicate per incollare due parti o per creare strutture stratificate, queste tecniche sono essenziali per far progredire le capacità dell'ingegneria e della produzione moderna.
Consolidamento della polvere in vari materiali
La pressatura isostatica a caldo (HIP) è una tecnica versatile utilizzata per consolidare un'ampia gamma di materiali, tra cui leghe ad alta temperatura, carburo cementato, acciaio ad alta velocità, materiali ceramici e leghe di titanio. Questo processo migliora significativamente le prestazioni di questi materiali e riduce i costi di produzione, rendendolo un'alternativa interessante ai tradizionali metodi di fusione o di deformazione.
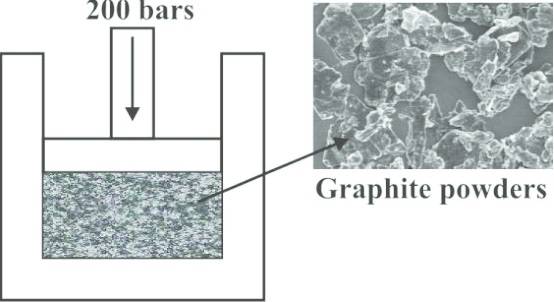
Materiali chiave che beneficiano dell'HIP
Tipo di materiale | Aree di applicazione | Miglioramenti delle prestazioni |
---|---|---|
Leghe ad alta temperatura | Aerospaziale, energia, trasporti | Maggiore resistenza e durata |
Carburo cementato | Utensili da taglio, attrezzature per l'industria mineraria | Maggiore durezza e resistenza all'usura |
Acciaio ad alta velocità | Macchine utensili, strumenti da taglio | Maggiore efficienza di taglio |
Materiali ceramici | Elettronica, automotive, dispositivi medici | Migliori proprietà termiche ed elettriche |
Leghe di titanio | Aerospaziale, impianti medici | Peso ridotto e migliore biocompatibilità |
Fasi del processo di consolidamento HIP
- Preparazione: La polvere viene mescolata con un legante fuggitivo e modellata nella forma desiderata mediante pressione a temperatura ambiente. Per questa fase è essenziale un'atmosfera controllata con gas protettivi.
- Riscaldamento e consolidamento: Il materiale viene riscaldato fino a poco meno del suo punto di fusione, attivando la formazione di microstrutture cristalline martensitiche.
- Fusione delle particelle: Le particelle diventano più dense e alla fine si fondono insieme, un processo che può essere accelerato utilizzando la sinterizzazione in fase liquida (LPS).
- Solidificazione: Il materiale si raffredda e si solidifica, creando una massa unica con proprietà migliorate.
Consolidando questi materiali attraverso l'HIP, le industrie possono ottenere componenti di qualità superiore con prestazioni superiori, rendendo l'HIP una tecnologia indispensabile nella produzione moderna.
Applicazioni emergenti in nuovi settori
La tecnologia della pressatura isostatica a caldo (HIP) non si limita alle applicazioni industriali tradizionali, ma viene esplorata attivamente anche in campi emergenti, ampliandone la portata e l'utilità. Una delle aree più promettenti è l'uso dell'HIP nel trattamento dei materiali porosi. Applicando una pressione uniforme e alte temperature, l'HIP può chiudere efficacemente pori e microfessure, migliorando l'integrità strutturale e le prestazioni di questi materiali.
Nel trattamento delle superfici, HIP offre una soluzione unica per migliorarne la durata e la funzionalità. Questa tecnologia può essere impiegata per creare rivestimenti duri e resistenti all'usura sui componenti, prolungandone significativamente la durata in ambienti difficili. Inoltre, l'HIP viene utilizzato nella preparazione di materiali di elevata purezza, dove la sua capacità di ottenere una densificazione uniforme è fondamentale per produrre materiali con purezza e omogeneità eccezionali.
Un'altra interessante applicazione dell'HIP è nell'industria alimentare, dove viene studiata per la sterilizzazione. Le condizioni di alta pressione e alta temperatura fornite dall'HIP possono uccidere efficacemente i microrganismi, rendendolo una potenziale alternativa ai metodi di sterilizzazione tradizionali. Questa applicazione non solo evidenzia la versatilità della tecnologia HIP, ma apre anche nuove strade al suo utilizzo per garantire la sicurezza e la qualità degli alimenti.
Campo di applicazione | Uso specifico di HIP |
---|---|
Materiali porosi | Chiusura di pori e microfessure, miglioramento dell'integrità strutturale |
Trattamenti di superficie | Creazione di rivestimenti duri e resistenti all'usura, per prolungare la durata di vita. |
Preparazione di materiali di elevata purezza. | Ottenere una densificazione uniforme, produrre materiali di elevata purezza |
Industria alimentare | Sterilizzazione, garanzia di sicurezza e qualità degli alimenti |
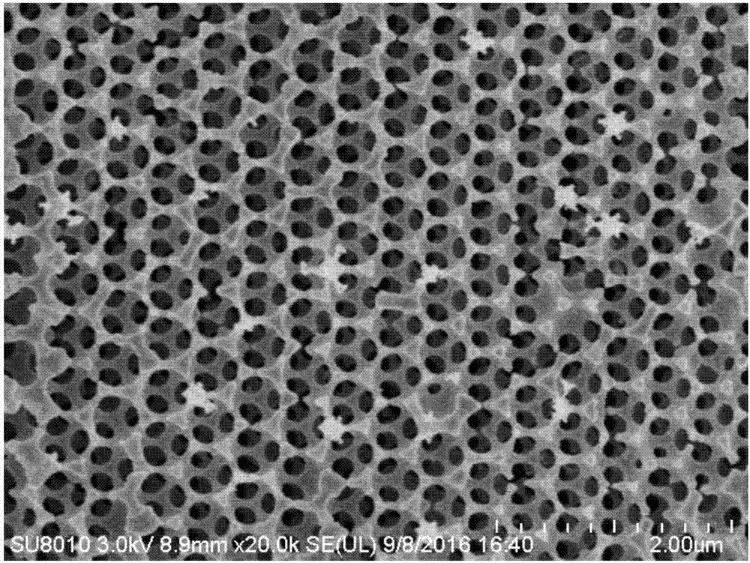
Queste applicazioni emergenti dimostrano l'adattabilità e il potenziale innovativo della tecnologia HIP, suggerendo che la sua influenza continuerà ad espandersi in vari settori.
Conclusioni e prospettive future
Impatto sulla moderna tecnologia di produzione
La tecnologia di pressatura isostatica a caldo (HIP) ha avuto un impatto significativo sulla produzione moderna, favorendo la creazione di materiali innovativi e ampliando la sua influenza in numerosi settori tecnici. Questa tecnologia, che utilizza gas inerti come l'azoto e l'argon per applicare una pressione uniforme ad alte temperature, ha rivoluzionato i processi di densificazione dei materiali. I materiali ottenuti presentano densità, uniformità e prestazioni eccezionali, fondamentali per le applicazioni avanzate in settori quali l'aerospaziale, l'energia e l'elettronica.
Uno dei contributi chiave della tecnologia HIP è la sua capacità di consolidare le polveri in materiali completamente densi senza la necessità di leganti o ausiliari di sinterizzazione aggiuntivi. Questa capacità è particolarmente preziosa nella produzione di leghe ad alta temperatura, carburi cementati e materiali ceramici, dove è essenziale ottenere densità e resistenza elevate. Il processo prevede tre fasi principali: l'avvicinamento e il riarrangiamento delle particelle, la deformazione plastica e lo scorrimento per diffusione, che operano tutte contemporaneamente per ottenere una densificazione ottimale.
Inoltre, la tecnologia HIP ha trovato nuove applicazioni in campi emergenti, come il trattamento di materiali porosi e la preparazione di materiali di elevata purezza. Ad esempio, si sta studiando la possibilità di utilizzarla per la sterilizzazione dei prodotti alimentari, dimostrando la sua versatilità e il suo potenziale al di là delle tradizionali applicazioni industriali. La capacità dell'HIP di riparare e densificare i getti usati, riportandoli a livelli di prestazioni quasi nuovi, sottolinea ulteriormente il suo valore nella produzione moderna.
In sintesi, il ruolo della tecnologia HIP nella produzione moderna è multiforme, in quanto guida i progressi della scienza dei materiali e ne espande l'utilità in una vasta gamma di settori. La sua continua evoluzione e la sua adattabilità promettono di sbloccare applicazioni ancora più innovative in futuro.
CONTATTATECI PER UNA CONSULENZA GRATUITA
I prodotti e i servizi di KINTEK LAB SOLUTION sono stati riconosciuti da clienti di tutto il mondo. Il nostro personale sarà lieto di assistervi per qualsiasi richiesta. Contattateci per una consulenza gratuita e parlate con uno specialista del prodotto per trovare la soluzione più adatta alle vostre esigenze applicative!