Il rivestimento sputter è una tecnica ampiamente utilizzata in vari settori, tra cui l'elettronica, l'ottica e la scienza dei materiali, per depositare film sottili su substrati.La necessità del vuoto nel rivestimento sputter è fondamentale per il successo del processo.Un ambiente sotto vuoto garantisce che gli atomi espulsi dal materiale di destinazione possano viaggiare senza ostacoli verso il substrato, riducendo al minimo le collisioni con le molecole di gas che potrebbero altrimenti disperdere gli atomi e degradare la qualità del rivestimento.Inoltre, il mantenimento della pressione corretta è fondamentale per sostenere il plasma necessario per lo sputtering.Una pressione troppo bassa provoca collisioni insufficienti a sostenere il plasma, mentre una pressione troppo alta causa collisioni eccessive, impedendo agli elettroni di acquisire energia sufficiente per ionizzare efficacemente gli atomi.Questo equilibrio è essenziale per ottenere rivestimenti uniformi e di alta qualità.
Spiegazione dei punti chiave:
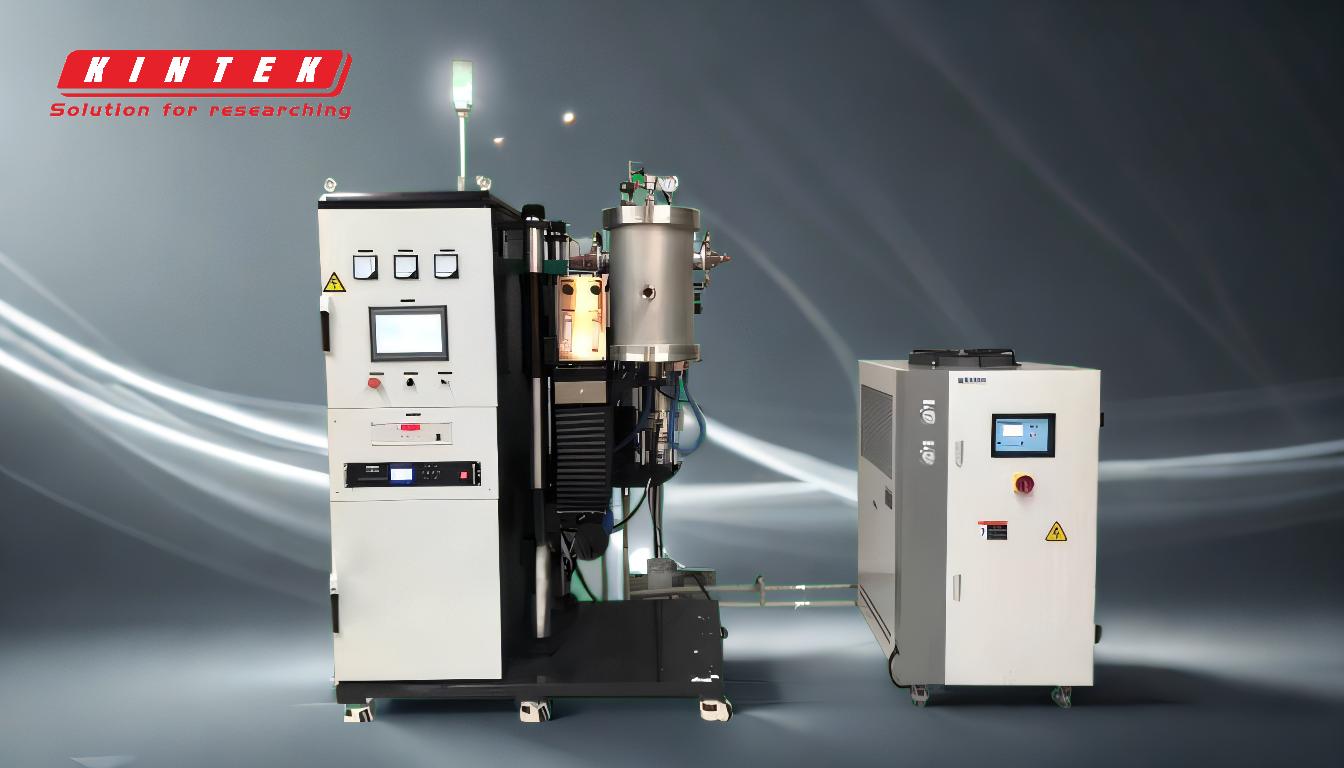
-
Riduzione al minimo della dispersione atomica:
- Nel vuoto, il percorso libero medio degli atomi espulsi dal bersaglio di sputtering è notevolmente aumentato.Ciò significa che gli atomi possono raggiungere direttamente il substrato senza essere dispersi dalle molecole di gas.In un ambiente non sottovuoto, le frequenti collisioni con le molecole d'aria farebbero deviare gli atomi dal percorso previsto, portando a rivestimenti non uniformi o di scarsa qualità.
-
Sostenere il plasma:
- Il rivestimento sputter si basa sulla generazione di un plasma, che è un gas altamente ionizzato contenente elettroni e ioni liberi.Il plasma è essenziale per bombardare il materiale bersaglio con gli ioni, provocando l'espulsione degli atomi.Un ambiente sottovuoto aiuta a mantenere il plasma garantendo che gli elettroni possano ottenere un'energia sufficiente per ionizzare gli atomi del gas.Se la pressione è troppo alta, gli elettroni perdono energia a causa di collisioni eccessive, rendendo difficile il mantenimento del plasma.
-
Prevenzione della contaminazione:
- Un ambiente sottovuoto riduce notevolmente la presenza di contaminanti come ossigeno, vapore acqueo e altri gas reattivi.Questi contaminanti possono reagire con gli atomi sputati, formando ossidi o altri composti che degradano la qualità del film sottile.Operando sotto vuoto, la purezza del materiale depositato viene preservata, con conseguenti migliori prestazioni del prodotto rivestito.
-
Controllo della velocità di deposizione:
- L'ambiente sotto vuoto consente un controllo preciso della velocità di deposizione del film sottile.Regolando la pressione e la potenza applicata al bersaglio, gli operatori possono regolare con precisione la velocità con cui gli atomi vengono depositati sul substrato.Questo controllo è fondamentale per le applicazioni che richiedono spessori o proprietà specifiche del rivestimento.
-
Miglioramento dell'uniformità del film:
- L'uniformità è fondamentale in molte applicazioni del rivestimento sputter, ad esempio nella produzione di rivestimenti ottici o di dispositivi a semiconduttore.Il vuoto garantisce che gli atomi spruzzati siano distribuiti in modo uniforme sul substrato, dando vita a un film coerente e uniforme.Questa uniformità è difficile da ottenere in un ambiente non sotto vuoto a causa della dispersione imprevedibile degli atomi.
-
Migliorare l'adesione:
- L'adesione del film sottile al substrato è un altro fattore critico influenzato dall'ambiente del vuoto.Nel vuoto, la superficie del substrato può essere pulita più efficacemente, spesso attraverso il bombardamento ionico, che rimuove eventuali contaminanti o ossidi.Questa superficie pulita consente un migliore legame tra il substrato e il film depositato, migliorando la durata complessiva e le prestazioni del rivestimento.
In sintesi, l'ambiente sotto vuoto nel rivestimento sputter è essenziale per garantire la qualità, l'uniformità e le prestazioni dei film sottili depositati.Riduce al minimo la dispersione atomica, sostiene il plasma, previene la contaminazione, controlla la velocità di deposizione, aumenta l'uniformità del film e migliora l'adesione.L'insieme di questi fattori rende il vuoto un componente critico del processo di sputter coating.
Tabella riassuntiva:
Fattore chiave | Ruolo nel rivestimento sputter |
---|---|
Riduzione al minimo della dispersione atomica | Assicura che gli atomi arrivino direttamente al substrato, riducendo le collisioni per ottenere rivestimenti uniformi. |
Sostenere il plasma | Mantiene la stabilità del plasma consentendo agli elettroni di ionizzare efficacemente gli atomi del gas. |
Prevenzione della contaminazione | Riduce i gas reattivi, preservando la purezza e le prestazioni del film sottile. |
Controllo della velocità di deposizione | Consente di regolare con precisione lo spessore e le proprietà del rivestimento. |
Miglioramento dell'uniformità del film | Assicura una distribuzione uniforme degli atomi per rivestimenti uniformi e di alta qualità. |
Miglioramento dell'adesione | Fornisce una superficie pulita del substrato per una migliore adesione e durata. |
Volete ottenere rivestimenti sputter di alta qualità? Contattate oggi stesso i nostri esperti per soluzioni su misura!