La sinterizzazione al plasma scintillante (SPS) è una tecnica di sinterizzazione avanzata che combina corrente elettrica diretta pulsata e pressione uniassiale per produrre materiali densi con proprietà uniche.Il processo prevede quattro fasi principali: creazione del vuoto, applicazione della pressione, riscaldamento resistivo e raffreddamento.Funziona sotto vuoto o in atmosfera controllata per prevenire l'ossidazione e garantire la purezza del materiale.L'SPS è caratterizzato da elevate velocità di riscaldamento, tempi di lavorazione brevi e controllo preciso di temperatura, pressione e velocità di riscaldamento, che consentono di creare materiali con microstrutture e proprietà personalizzate.Il processo è facilitato da un'interfaccia touchscreen per la programmazione e il controllo.
Punti chiave spiegati:
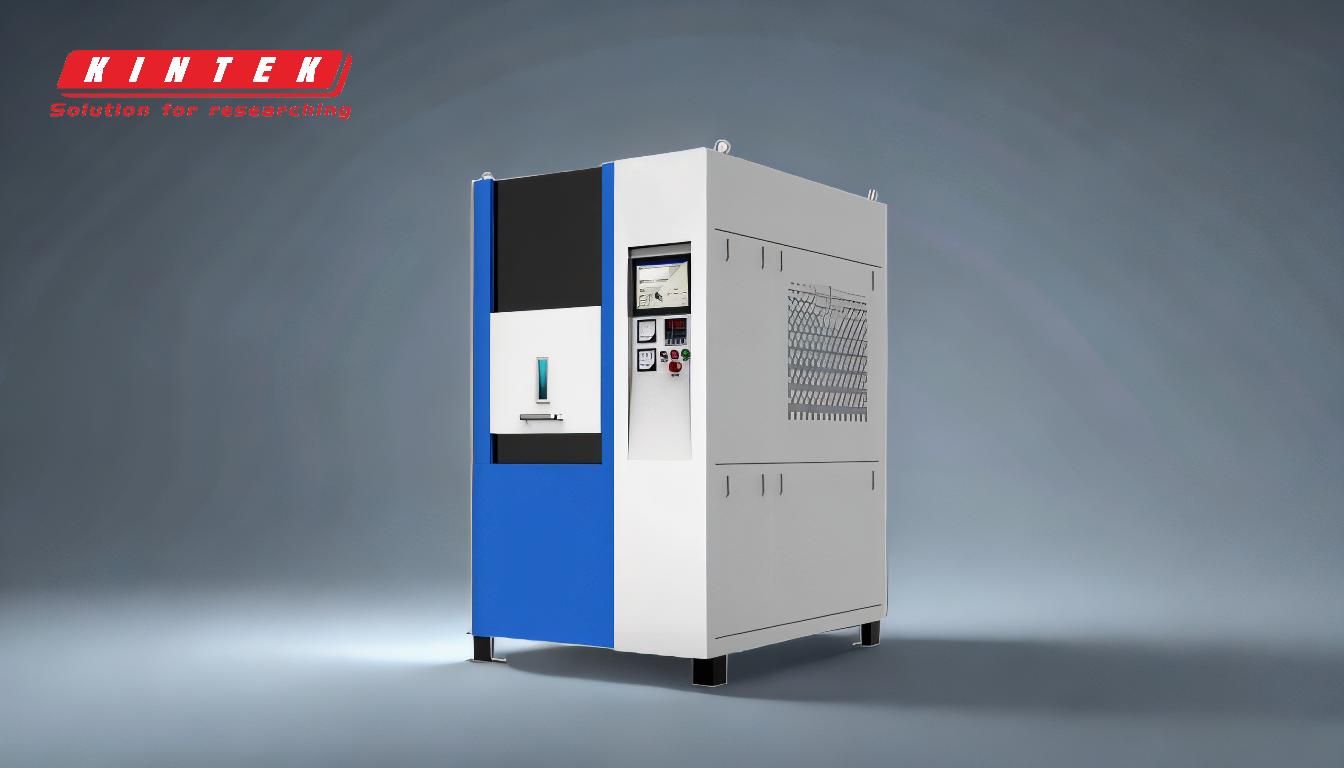
-
Panoramica dell'SPS:
- SPS è una tecnica di sinterizzazione avanzata che utilizza corrente elettrica diretta pulsata e pressione monoassiale.
- Si basa su una configurazione modificata di pressatura a caldo, in cui una corrente elettrica scorre direttamente attraverso la matrice di grafite e il componente.
- Il processo consente di ottenere tempi di riscaldamento molto rapidi e cicli di processo brevi grazie alle correnti pulsate e all'effetto "spark plasma".
-
Fasi chiave del processo SPS:
-
Fase 1:Rimozione del gas e creazione del vuoto:
- Il processo inizia con la rimozione del gas dalla camera per creare il vuoto o un'atmosfera controllata.
- Questa fase previene l'ossidazione e garantisce la purezza del materiale.
-
Fase 2: Applicazione della pressione:
- La pressione uniassiale viene applicata alla polvere compatta mediante punzoni superiori e inferiori.
- La pressione aiuta a densificare il materiale durante la sinterizzazione.
-
Fase 3: Riscaldamento resistivo:
- La corrente elettrica continua pulsata viene fatta passare attraverso la matrice di grafite e la polvere compatta.
- La scarica di scintille genera alte temperature localizzate, causando l'evaporazione superficiale e la fusione delle particelle di polvere.
- Si formano colli intorno alle aree di contatto tra le particelle, con conseguente densificazione.
-
Fase 4: raffreddamento:
- Dopo la sinterizzazione, il materiale viene raffreddato in condizioni controllate per ottenere la microstruttura e le proprietà desiderate.
-
Fase 1:Rimozione del gas e creazione del vuoto:
-
Caratteristiche uniche di SPS:
-
Alti tassi di riscaldamento:
- L'SPS raggiunge tassi di riscaldamento rapidi, riducendo significativamente i tempi di lavorazione rispetto ai metodi di sinterizzazione convenzionali.
-
Controllo preciso:
- Il processo consente un controllo preciso della temperatura, della pressione e della velocità di riscaldamento, consentendo la fabbricazione di materiali con proprietà personalizzate.
-
Basse temperature di sinterizzazione:
- L'SPS opera a temperature di sinterizzazione inferiori rispetto ai metodi tradizionali, riducendo al minimo la crescita dei grani e preservando le proprietà del materiale.
-
Alti tassi di riscaldamento:
-
Vantaggi di SPS:
-
Tempi di elaborazione brevi:
- La combinazione di elevate velocità di riscaldamento e correnti pulsate consente di ridurre i cicli di processo.
-
Proprietà uniche del materiale:
- L'"effetto plasma a scintilla" inibisce la crescita delle particelle, consentendo la creazione di materiali con composizioni e microstrutture uniche.
-
Atmosfera controllata:
- Il funzionamento sotto vuoto o in atmosfera controllata garantisce la purezza del materiale e ne previene l'ossidazione.
-
Tempi di elaborazione brevi:
-
Applicazioni di SPS:
- L'SPS è ampiamente utilizzato nella fabbricazione di ceramiche avanzate, metalli, compositi e materiali a gradazione funzionale.
- È particolarmente utile per produrre materiali con proprietà meccaniche, termiche ed elettriche migliorate.
-
Controllo e programmazione dei processi:
- Il processo SPS è controllato e programmato mediante un'interfaccia touchscreen.
- Ciò facilita il controllo preciso dei parametri di sinterizzazione e garantisce la riproducibilità del processo.
Comprendendo questi punti chiave, l'acquirente di attrezzature o materiali di consumo può apprezzare le capacità uniche dell'SPS e il suo potenziale per la produzione di materiali ad alte prestazioni con proprietà personalizzate.
Tabella riassuntiva:
Aspetto chiave | Dettagli |
---|---|
Panoramica del processo | Combina corrente elettrica pulsata e pressione monoassiale per la sinterizzazione. |
Fasi chiave | 1.Creazione del vuoto 2.Applicazione della pressione 3.Riscaldamento resistivo 4.Raffreddamento. |
Caratteristiche uniche | Elevate velocità di riscaldamento, controllo preciso, basse temperature di sinterizzazione. |
Vantaggi | Tempi di lavorazione brevi, proprietà uniche del materiale, atmosfera controllata. |
Applicazioni | Ceramica avanzata, metalli, compositi, materiali classificati funzionalmente. |
Controllo del processo | Interfaccia touchscreen per una programmazione precisa e riproducibile. |
Siete pronti a scoprire come la sinterizzazione al plasma di scintilla può rivoluzionare la vostra produzione di materiali? Contattateci oggi stesso per una guida esperta!