La sinterizzazione è un processo termico critico utilizzato per trasformare materiali in polvere in strutture solide e coese senza fondere il materiale primario.Comporta tre fasi principali: la modellazione della polvere in un pezzo "verde", il riscaldamento per rimuovere i leganti e fondere le particelle e il raffreddamento per ottenere il prodotto finale.Il processo avviene in apparecchiature specializzate come un forno di sinterizzazione dove il controllo della temperatura è fondamentale per garantire l'adesione delle particelle attraverso la diffusione.La sinterizzazione migliora le proprietà del materiale, riduce la porosità e consente di ottenere la resistenza meccanica e la precisione dimensionale desiderate.Il processo è ampiamente utilizzato in settori come la metallurgia, la ceramica e la produzione per produrre componenti complessi e ad alte prestazioni.
Punti chiave spiegati:
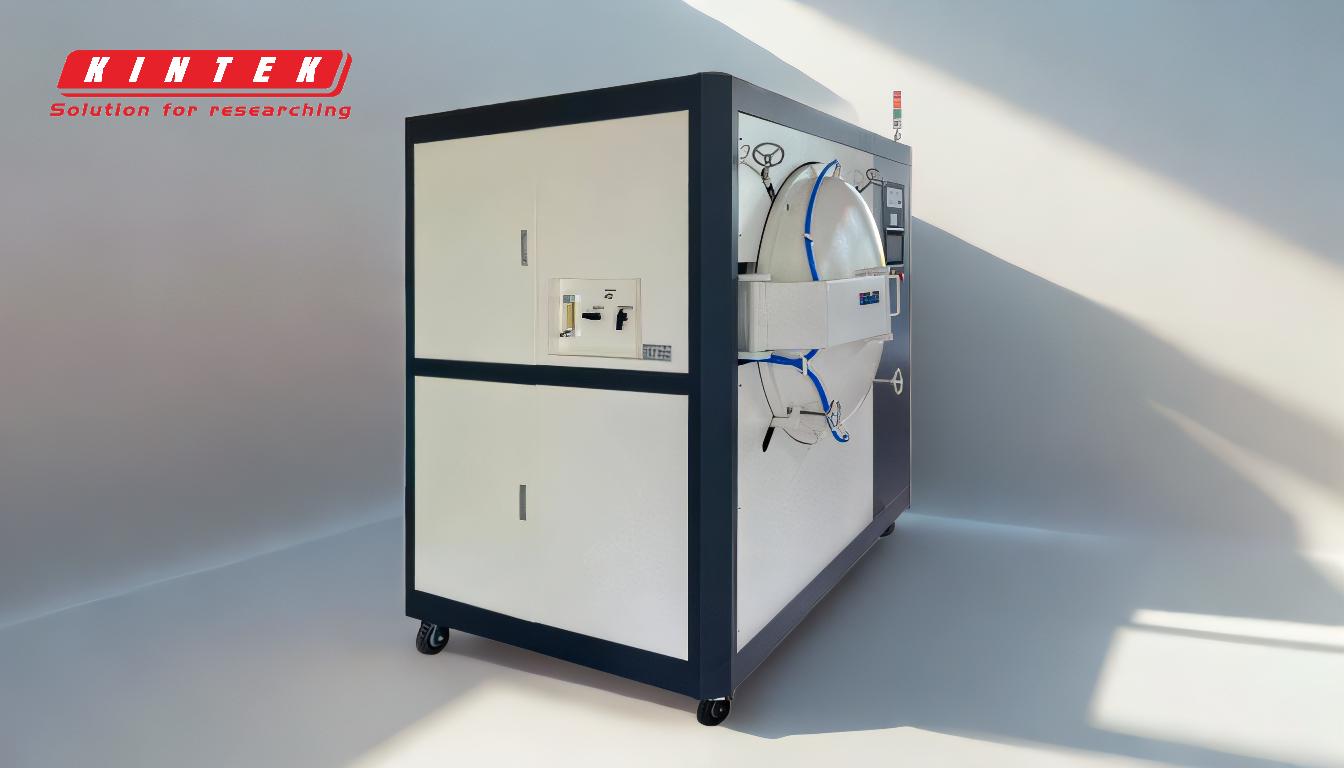
-
Formazione della parte verde:
- Il processo inizia con una miscela di polveri, spesso mescolata con un agente legante (ad esempio, acqua, cera o polimero), che viene compattata in una forma specifica.Questa parte "verde" è debole e sovradimensionata, ma mantiene la forma desiderata.
- Il legante assicura l'adesione delle particelle di polvere durante questa fase iniziale.
-
Riscaldamento e rimozione del legante:
- La parte verde viene posta in un forno di sinterizzazione e riscaldato per rimuovere il legante.Ciò avviene nella zona di preriscaldamento del forno, dove le temperature sono sufficientemente elevate da far evaporare o bruciare il legante.
- Questa fase è fondamentale per eliminare i materiali organici e i lubrificanti, garantendo che il pezzo sia pronto per la fusione delle particelle.
-
Fusione e densificazione delle particelle:
- Nella zona di sinterizzazione, la temperatura viene portata a un livello appena inferiore al punto di fusione del materiale primario.Ciò consente alle particelle di legarsi attraverso la diffusione allo stato solido, formando colli tra di esse.
- Le particelle si fondono in superficie, riducendo la porosità e aumentando la densità.In alcuni casi, un agente legante intermedio (ad esempio, il bronzo) può fondere e legare le particelle senza alterare il materiale primario.
-
Raffreddamento e proprietà finali:
- Dopo la sinterizzazione, il pezzo entra nella zona di raffreddamento, dove un raffreddamento controllato solidifica la struttura e migliora le proprietà meccaniche.
- In questa fase si verifica il ritiro, che conferisce al pezzo le dimensioni finali.La velocità di raffreddamento può essere regolata per regolare con precisione proprietà come la durezza e la resistenza.
-
Tipi di forni di sinterizzazione:
- Forni periodici:Questi forni lavorano i pezzi in lotti, con cicli di riscaldamento e raffreddamento controllati.
- Forni a tunnel:I pezzi passano attraverso diverse zone di temperatura (preriscaldamento, sinterizzazione e raffreddamento) in modo continuo, rendendoli adatti alla produzione di grandi volumi.
-
Vantaggi della sinterizzazione:
- Produce pezzi complessi e ad alta resistenza con uno scarto minimo di materiale.
- Migliora le proprietà del materiale, come la densità, la forza e la resistenza all'usura.
- Consente un controllo preciso delle dimensioni e delle caratteristiche meccaniche.
-
Applicazioni della sinterizzazione:
- Ampiamente utilizzato in metallurgia per la produzione di componenti metallici come ingranaggi, cuscinetti e filtri.
- Essenziale nella produzione di ceramiche per creare prodotti durevoli e resistenti al calore.
- Applicato nella metallurgia delle polveri per fabbricare parti intricate con proprietà personalizzate.
Grazie alla comprensione di queste fasi e dei meccanismi, i produttori possono ottimizzare il processo di sinterizzazione per produrre componenti di alta qualità ed economici per varie applicazioni industriali.
Tabella riassuntiva:
Fase | Descrizione |
---|---|
Formazione della parte verde | La miscela di polveri viene compattata in una forma con un legante. |
Riscaldamento e rimozione dei leganti | La parte verde viene riscaldata per rimuovere i leganti e prepararla alla fusione delle particelle. |
Fusione delle particelle | Le particelle si legano per diffusione, riducendo la porosità e aumentando la densità. |
Raffreddamento e finalizzazione | Il raffreddamento controllato solidifica la struttura, ottenendo le dimensioni finali. |
Tipi di forni | Descrizione |
Forni periodici | Lavorazione a lotti con cicli di riscaldamento e raffreddamento controllati. |
Forni a tunnel | Processo continuo attraverso zone di preriscaldamento, sinterizzazione e raffreddamento. |
Vantaggi | Descrizione |
Proprietà migliorate | Densità, forza e resistenza all'usura migliorate. |
Controllo di precisione | Dimensioni e caratteristiche meccaniche su misura. |
Applicazioni | Descrizione |
Metallurgia | Produzione di ingranaggi, cuscinetti e filtri. |
Ceramica | Creazione di prodotti durevoli e resistenti al calore. |
Metallurgia delle polveri | Realizzazione di parti complesse con proprietà personalizzate. |
Ottimizzate il vostro processo di sinterizzazione con una guida esperta... contattateci oggi stesso !