La tempra in aria, sebbene comunemente utilizzata nei processi di trattamento termico, presenta diversi svantaggi, in particolare se applicata a materiali come wafer di vetro sodo-calcico . Questi inconvenienti includono velocità di raffreddamento non uniformi, potenziale di stress termico e limitazioni nel raggiungimento di proprietà specifiche del materiale. Di seguito esploriamo questi svantaggi in dettaglio, concentrandoci sulle loro implicazioni per materiali e processi.
Punti chiave spiegati:
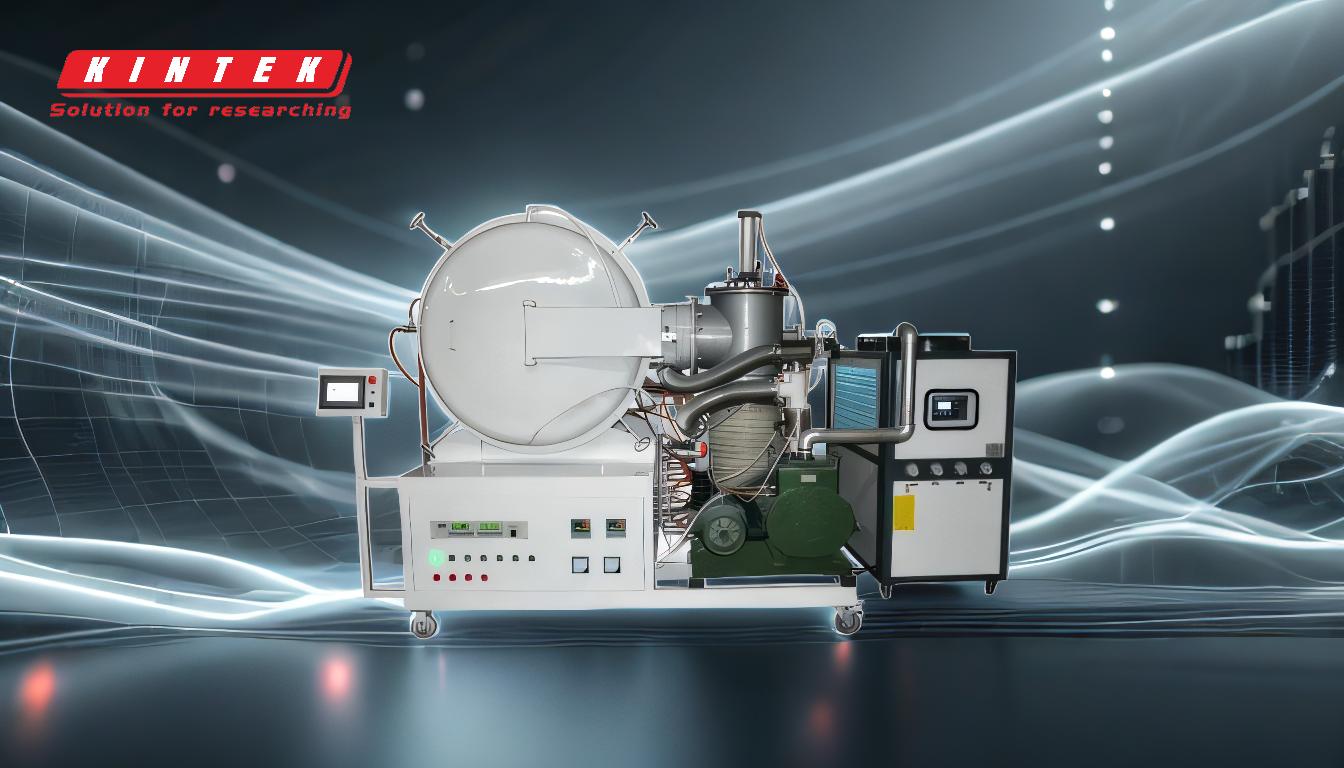
-
Velocità di raffreddamento irregolari:
- La tempra in aria si basa sulla circolazione dell'aria per rimuovere il calore dal materiale. Tuttavia, l’aria è un cattivo conduttore di calore rispetto ai liquidi o ai gas come l’azoto. Ciò si traduce in velocità di raffreddamento non uniformi nel materiale, in particolare per geometrie complesse o sezioni sottili wafer di vetro sodo-calcico .
- Un raffreddamento non uniforme può portare a proprietà del materiale incoerenti, come durezza o resistenza, che sono fondamentali per le applicazioni che richiedono precisione e uniformità.
-
Stress Termico e Cracking:
- Le velocità di raffreddamento più lente e irregolari nella tempra in aria possono indurre stress termico all'interno del materiale. Ciò è particolarmente problematico per materiali fragili come wafer di vetro sodo-calcico , che tendono a rompersi sotto stress.
- Lo stress termico può anche portare a deformazioni o distorsioni, rendendo il materiale inadatto per applicazioni che richiedono un'elevata precisione dimensionale.
-
Controllo limitato sulle velocità di raffreddamento:
- A differenza della tempra liquida o della tempra con gas ad alta pressione, la tempra in aria offre un controllo limitato sulle velocità di raffreddamento. Ciò rende difficile ottenere microstrutture o proprietà dei materiali specifiche che sono fondamentali per le applicazioni avanzate.
- Ad esempio, alcune leghe o materiali di vetro possono richiedere un raffreddamento rapido per ottenere la durezza o la trasparenza desiderate, che la tempra in aria non può fornire in modo affidabile.
-
Rischi ambientali e di contaminazione:
- La tempra in aria espone il materiale all'aria ambiente, che può contenere contaminanti come umidità, polvere o ossigeno. Questi contaminanti possono reagire con la superficie del materiale, provocando ossidazione o altre reazioni chimiche indesiderate.
- In caso di wafer di vetro sodo-calcico , l'esposizione all'umidità o all'ossigeno può compromettere le proprietà ottiche o l'integrità strutturale del materiale.
-
Inefficienza energetica:
- La tempra in aria spesso richiede tempi di raffreddamento più lunghi rispetto ad altri metodi, con conseguente maggiore consumo energetico e maggiori costi di lavorazione.
- L’inefficienza dell’aria come mezzo di raffreddamento ne limita inoltre l’applicabilità nei processi industriali ad alto rendimento in cui il risparmio di tempo ed energia è fondamentale.
-
Incompatibilità con i Materiali Avanzati:
- Materiali moderni, tra cui ceramiche avanzate, compositi e vetro specializzato wafer di vetro sodo-calcico , spesso richiedono una gestione termica precisa durante il raffreddamento. La tempra in aria potrebbe non fornire il controllo o la consistenza necessari per questi materiali.
- Ad esempio, per ottenere la chiarezza ottica o la resistenza meccanica desiderate wafer di vetro sodo-calcico potrebbero richiedere tecniche di raffreddamento più avanzate di quelle offerte dalla tempra in aria.
In sintesi, sebbene la tempra in aria sia un metodo semplice ed economico per alcune applicazioni, i suoi svantaggi, come il raffreddamento non uniforme, lo stress termico, il controllo limitato, i rischi di contaminazione, l’inefficienza energetica e l’incompatibilità con materiali avanzati, lo rendono meno adatto per applicazioni di precisione. applicazioni che coinvolgono materiali come wafer di vetro sodo-calcico . Metodi di raffreddamento alternativi, come la tempra liquida o con gas ad alta pressione, potrebbero essere più appropriati per ottenere le proprietà e le prestazioni desiderate del materiale.
Tabella riassuntiva:
Svantaggio | Impatto sui materiali |
---|---|
Velocità di raffreddamento irregolari | Durezza, resistenza e proprietà del materiale incoerenti. |
Stress Termico e Cracking | Rischio di crepe, deformazioni o distorsioni in materiali fragili. |
Controllo limitato sul raffreddamento | Difficoltà nel raggiungimento di microstrutture o proprietà specifiche. |
Contaminazione ambientale | Ossidazione o reazioni chimiche dovute all'esposizione a umidità, polvere o ossigeno. |
Inefficienza energetica | Tempi di raffreddamento più lunghi, maggiore consumo energetico e maggiori costi. |
Incompatibilità con i Materiali Avanzati | Idoneità limitata per materiali moderni che richiedono una gestione termica precisa. |
Scopri le migliori soluzioni di raffreddamento per i tuoi materiali— contatta i nostri esperti oggi stesso !