La sinterizzazione allo stato solido e la sinterizzazione in fase liquida sono due processi distinti utilizzati per la densificazione di ceramiche e altri materiali, che si differenziano principalmente per i meccanismi di legame delle particelle e per le temperature richieste.La sinterizzazione allo stato solido si basa su meccanismi di diffusione per trasportare il materiale e ottenere la densificazione, in genere a temperature più elevate, ed è adatta a materiali come la zirconia e l'allumina.La sinterizzazione in fase liquida, invece, prevede l'introduzione di una fase liquida a basso punto di fusione, che facilita il riarrangiamento e il legame delle particelle a temperature più basse, rendendola ideale per materiali più difficili da densificare come il nitruro di silicio e il carburo di silicio.La presenza della fase liquida accelera la densificazione e influenza la chiusura dei pori, la dimensione dei grani e le proprietà meccaniche.
Punti chiave spiegati:
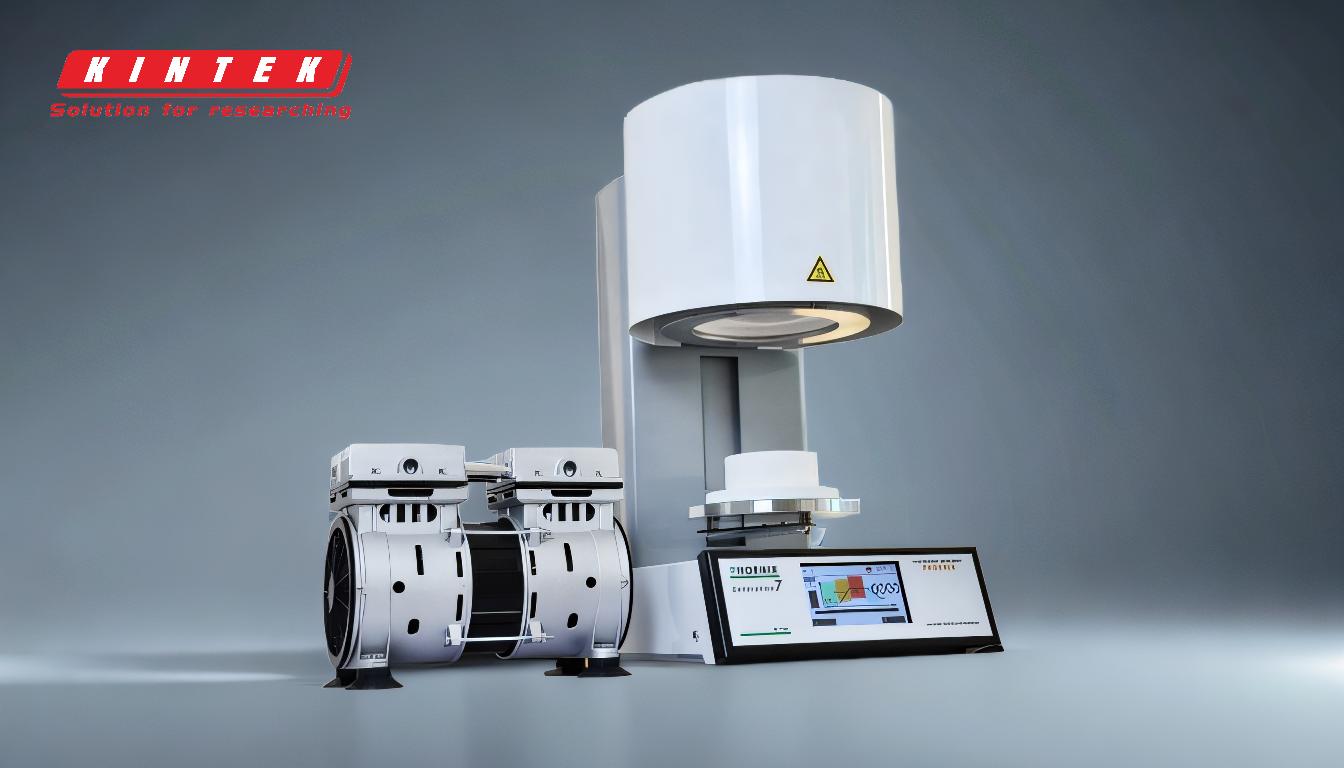
-
Temperatura di sinterizzazione:
- Sinterizzazione allo stato solido:Questo processo avviene a temperature relativamente elevate, spesso vicine al punto di fusione del materiale primario.Ad esempio, l'ossido di zirconio e l'allumina vengono sinterizzati a temperature intorno ai 1600°C.Le alte temperature sono necessarie per attivare i meccanismi di diffusione, che sono il mezzo principale per il trasporto e l'adesione del materiale.
- Sinterizzazione in fase liquida:Questo metodo opera a temperature inferiori rispetto alla sinterizzazione allo stato solido.L'aggiunta di una fase liquida a basso punto di fusione riduce la temperatura di sinterizzazione complessiva necessaria per la densificazione.La fase liquida si forma alla temperatura di sinterizzazione, consentendo alle forze capillari di riorganizzare le particelle in modo più efficiente.
-
Meccanismi di densificazione:
- Sinterizzazione allo stato solido:La densificazione si ottiene attraverso la diffusione allo stato solido.Gli atomi si spostano da aree ad alto potenziale chimico (ad esempio, le superfici delle particelle) ad aree a basso potenziale chimico (ad esempio, i colli tra le particelle).Questo processo è più lento e richiede temperature più elevate per superare le barriere dell'energia di attivazione per la diffusione.
- Sinterizzazione in fase liquida:La fase liquida migliora la densificazione fornendo un percorso ad alta diffusività per gli atomi.Le forze capillari guidano il riarrangiamento delle particelle e la fase liquida riempie gli spazi tra le particelle, favorendo un legame e una densificazione più rapidi.Questo processo è particolarmente efficace per i materiali difficili da densificare attraverso meccanismi allo stato solido.
-
Chiusura dei pori:
- Sinterizzazione allo stato solido:La chiusura dei pori nella sinterizzazione allo stato solido è un processo graduale che si basa sulla lenta diffusione degli atomi.Con il progredire della sinterizzazione, i pori si restringono e alla fine si chiudono, ma questo processo può richiedere molto tempo, soprattutto alle basse temperature.La microstruttura finale può ancora contenere una certa porosità residua, a seconda delle condizioni di sinterizzazione.
- Sinterizzazione in fase liquida:La presenza della fase liquida accelera la chiusura dei pori.Il liquido riempie i pori e gli spazi tra le particelle, accelerando la densificazione.La fase liquida aiuta anche a ridistribuire il materiale, riducendo la porosità complessiva in modo più efficace rispetto alla sinterizzazione allo stato solido.Il risultato è un prodotto finale più denso e con meno pori residui.
-
Granulometria e microstruttura:
- Sinterizzazione allo stato solido:Questo processo può portare a una crescita significativa dei grani, soprattutto alle alte temperature.I grani più grandi possono avere un impatto negativo sulle proprietà meccaniche, come la resistenza e la tenacità.La microstruttura è tipicamente caratterizzata da grani più grandi e uniformi.
- Sinterizzazione in fase liquida:La sinterizzazione in fase liquida tende a produrre grani di dimensioni minori grazie alle temperature di sinterizzazione più basse e alla presenza della fase liquida, che può inibire la crescita dei grani.La microstruttura risultante è più fine e può migliorare le proprietà meccaniche, come la resistenza alla flessione e la tenacità alla frattura.Inoltre, la modalità di frattura può passare da transgranulare (attraverso i grani) a intergranulare (lungo i confini dei grani), migliorando ulteriormente la tenacità.
-
Idoneità del materiale:
- Sinterizzazione allo stato solido:Questo metodo è adatto ai materiali che possono essere densificati attraverso meccanismi di diffusione, come la zirconia e l'allumina.Questi materiali hanno in genere punti di fusione elevati e non richiedono l'aggiunta di una fase liquida per la densificazione.
- Sinterizzazione in fase liquida:Questo metodo è ideale per i materiali difficili da densificare attraverso meccanismi allo stato solido, come il nitruro di silicio e il carburo di silicio.L'aggiunta di una fase liquida facilita la densificazione a temperature più basse e migliora la cinetica di sinterizzazione complessiva.
-
Proprietà meccaniche:
- Sinterizzazione allo stato solido:Le proprietà meccaniche dei materiali sinterizzati con metodi allo stato solido sono generalmente buone, con un'elevata densità ed eccellenti prestazioni ad alta temperatura.Tuttavia, il potenziale di crescita dei grani alle alte temperature può portare a una riduzione della resistenza e della tenacità.
- Sinterizzazione in fase liquida:I materiali sinterizzati con metodi in fase liquida presentano spesso proprietà meccaniche migliori, tra cui una maggiore resistenza alla flessione e tenacità alla frattura.La granulometria più fine e la modalità di frattura intergranulare contribuiscono a questi miglioramenti.Inoltre, le temperature di sinterizzazione più basse possono contribuire a preservare le proprietà intrinseche del materiale.
In sintesi, la scelta tra sinterizzazione allo stato solido e in fase liquida dipende dalle proprietà del materiale, dalla microstruttura desiderata e dalle prestazioni meccaniche.La sinterizzazione allo stato solido è adatta ai materiali che possono essere densificati per diffusione, mentre la sinterizzazione in fase liquida è vantaggiosa per i materiali più difficili da densificare, in quanto offre temperature di sinterizzazione più basse, una densificazione più rapida e proprietà meccaniche migliori.
Tabella riassuntiva:
Aspetto | Sinterizzazione allo stato solido | Sinterizzazione in fase liquida |
---|---|---|
Temperatura di esercizio | Temperature elevate (ad esempio, 1600°C per la zirconia/allumina) | Temperature più basse dovute alla presenza di una fase liquida a basso punto di fusione |
Meccanismo di densificazione | Si basa sulla diffusione allo stato solido, processo più lento | La fase liquida aumenta la diffusione, più veloce il riarrangiamento e il legame delle particelle |
Chiusura dei pori | Graduale, si basa su una lenta diffusione; è possibile la presenza di porosità residua. | Accelerata dalla fase liquida, meno pori residui |
Dimensione dei grani | Grani più grandi a causa delle alte temperature | Grani più piccoli, microstruttura più fine |
Idoneità del materiale | Adatto per zirconia, allumina e altri materiali che favoriscono la diffusione | Ideale per nitruro di silicio, carburo di silicio e materiali più difficili da densificare |
Proprietà meccaniche | Buona densità e prestazioni ad alta temperatura; la crescita potenziale dei grani riduce la tenacità | Migliore resistenza alla flessione, tenacità alla frattura e microstruttura più fine |
Avete bisogno di aiuto per scegliere il metodo di sinterizzazione giusto per i vostri materiali? Contattate i nostri esperti oggi stesso !