Introduzione alla sinterizzazione al plasma scintillante (SPS)
La sinterizzazione al plasma di scintilla (SPS) rappresenta un approccio innovativo nelle moderne tecnologie di lavorazione dei materiali, rivoluzionando il modo di sinterizzare i materiali. Questo metodo innovativo si distingue per l'impiego di impulsi di corrente continua per ottenere un riscaldamento e una sinterizzazione rapidi, con una differenza significativa rispetto alle tecniche tradizionali. Il processo unico di SPS prevede la generazione di un plasma di scintille attraverso correnti pulsate, facilitando la creazione di materiali con proprietà superiori. Approfondendo questa guida completa, esploreremo le complessità dell'SPS, la sua miriade di applicazioni in vari settori e i vantaggi sostanziali che offre rispetto ai metodi di sinterizzazione tradizionali. Unitevi a noi per scoprire il potenziale di trasformazione dell'SPS nel plasmare il futuro della scienza dei materiali.
Come funziona il forno di sinterizzazione al plasma scintillante
La sinterizzazione al plasma a scintilla (SPS), nota anche come sinterizzazione a corrente elettrica pulsata (PECS), sinterizzazione attivata dal plasma (PAS) o tecnologia di sinterizzazione assistita dal campo (FAST), è una sofisticata tecnica di sinterizzazione che sfrutta elevate correnti continue pulsate per riscaldare una polvere compatta all'interno di una configurazione di stampo/punzone. Questo metodo consente di applicare forze di compressione fino a 250 kN, con uscite del trasformatore in grado di raggiungere 10 V e correnti fino a 10 kA. Gli schemi di corrente continua pulsata possono essere regolati con segmenti ON e OFF che vanno da 0 a 255 ms, consentendo un controllo preciso del processo di sinterizzazione.
Il processo SPS si caratterizza per la velocità di riscaldamento e raffreddamento, che può superare rispettivamente i 1000°C/min e i 400°C/min, a seconda delle dimensioni e del design dell'utensile. Questo rapido ciclo termico riduce al minimo i processi di coartazione a basse temperature e preserva le nanostrutture intrinseche anche dopo la completa densificazione. La temperatura all'interno del forno SPS viene monitorata mediante un pirometro centrale che si concentra sul fondo di un foro nel punzone superiore, garantendo una misurazione accurata della temperatura indipendentemente dalle proprietà o dalle dimensioni del campione. Un ulteriore monitoraggio della temperatura può essere ottenuto utilizzando un pirometro esterno e termocoppie flessibili posizionate in vari punti.
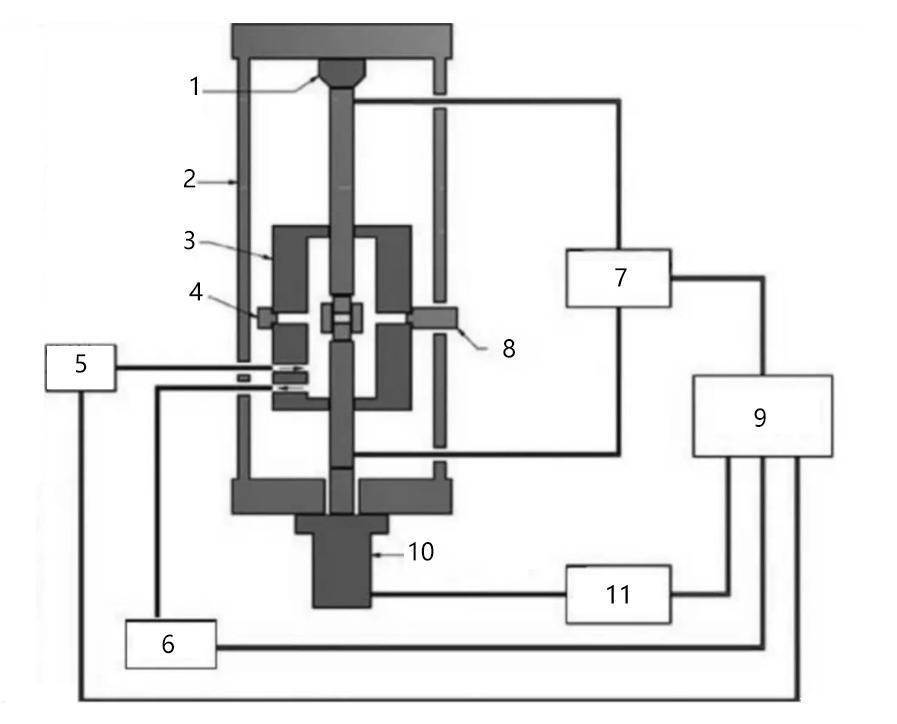
1. Unità di carico 2. Telaio di carico 3. Camera a vuoto 4. Finestra di osservazione 5. Canale del gas inerte 6. Pompa del vuoto 7. Interruttore a impulsi 8. Misuratore di temperatura 9. Sistema di controllo 10. Cilindro idraulico 11. Sistema idraulico
I componenti chiave di un forno SPS sono il dispositivo di pressione assiale, l'elettrodo di punzonatura raffreddato ad acqua e la camera a vuoto. Il dispositivo di pressione assiale applica la forza di compressione necessaria, mentre gli elettrodi di punzonatura raffreddati ad acqua aiutano a gestire il calore generato durante il processo. La camera a vuoto, abbinata a un sistema di controllo dell'atmosfera in grado di passare dal vuoto all'argon, garantisce condizioni di sinterizzazione ottimali. L'alimentazione a impulsi CC, insieme al sistema di raffreddamento ad acqua, alla misurazione dello spostamento, alla misurazione della temperatura e alle unità di controllo di sicurezza, completano la configurazione dell'SPS, facilitando il controllo completo del processo e la programmazione del ciclo di sinterizzazione attraverso un'interfaccia touch screen di facile utilizzo.
Il forno SPS è ampiamente utilizzato per la sinterizzazione di un'ampia gamma di materiali, tra cui ceramiche, cermet e metalli. I suoi principali vantaggi tecnici risiedono nelle elevate velocità di riscaldamento e raffreddamento, che riducono significativamente i tempi di lavorazione. L'elevata corrente pulsata non solo migliora la densificazione dei materiali elettricamente conduttivi, ma attiva anche molteplici meccanismi di sinterizzazione, come la rimozione dell'ossido superficiale, l'elettromigrazione e l'elettroplasticità. Questa combinazione di pressione meccanica, campo elettrico e campo termico migliora significativamente il legame e la densificazione tra le particelle, rendendo l'SPS un metodo preferibile per la preparazione di materiali ad alte prestazioni.
In sintesi, il processo di sinterizzazione al plasma di scintilla è un metodo altamente efficiente e controllato per la densificazione dei materiali, che offre tempi di lavorazione rapidi e la capacità di mantenere microstrutture fini. Le sue applicazioni spaziano in vari campi, dalla ceramica avanzata ai compositi metallici, evidenziando la sua versatilità e importanza nella moderna scienza e ingegneria dei materiali.
Vantaggi dell'uso di SPS nella lavorazione dei materiali
La sinterizzazione al plasma di scintilla (SPS) ha rivoluzionato il campo della lavorazione dei materiali, offrendo vantaggi significativi rispetto alle tecniche di sinterizzazione tradizionali. L'SPS è una tecnica di sinterizzazione assistita dal campo che utilizza sia la temperatura che la pressione per ottenere una rapida densificazione dei materiali. Questo metodo è particolarmente efficace per sinterizzare un'ampia gamma di materiali, tra cui ceramiche, metalli e compositi, con notevole efficienza e precisione.
Velocità di sinterizzazione rapida
Uno dei vantaggi più evidenti dell'SPS è la capacità di raggiungere tassi di sinterizzazione rapidi. I metodi di sinterizzazione tradizionali, come la pressatura a caldo e la sinterizzazione senza pressione, possono richiedere diverse ore per ottenere la densificazione desiderata. Al contrario, SPS può densificare i materiali in pochi minuti. Questa sinterizzazione rapida è resa possibile dalle elevate velocità di riscaldamento, che possono superare i 500°C al minuto. Ad esempio, il raggiungimento di una temperatura di 1200°C può essere raggiunto in soli 4 minuti con SPS, rispetto alle 2-4 ore dei metodi tradizionali. Questa velocità non solo aumenta la produttività, ma riduce anche il consumo energetico e i costi operativi.
Sinterizzazione a grana fine
L'SPS facilita la sinterizzazione a grana fine, fondamentale per migliorare le proprietà meccaniche e fisiche dei materiali sinterizzati. Le rapide velocità di riscaldamento inibiscono la crescita dei grani, consentendo la creazione di materiali con microstrutture controllate. Ciò è particolarmente vantaggioso per la produzione di materiali nanocristallini, dove il mantenimento di piccole dimensioni dei grani è essenziale per ottenere proprietà superiori. La sinterizzazione a grana fine migliora anche l'omogeneità dei prodotti sinterizzati, garantendo prestazioni più costanti e affidabili.
Capacità di controllare la densità e i gradienti di temperatura
L'SPS offre un eccellente controllo della densità e dei gradienti di temperatura all'interno dei materiali sinterizzati. Questo livello di controllo si ottiene grazie all'applicazione simultanea di temperatura e pressione, che consente di regolare con precisione il processo di sinterizzazione. Il controllo della densità è particolarmente importante per creare materiali con livelli di porosità specifici o per ottenere una densificazione completa. Inoltre, l'SPS può creare gradienti di temperatura all'interno dello stampo, consentendo la sinterizzazione simultanea di materiali con punti di fusione diversi. Questa capacità è preziosa per la produzione di materiali a gradazione funzionale (FGM), in cui la composizione e le proprietà variano spazialmente.
Efficienza e compattezza dei forni SPS
I forni SPS sono progettati per essere altamente efficienti e compatti, il che li rende ideali sia per la ricerca che per le applicazioni industriali. Il design compatto dei forni SPS riduce lo spazio richiesto e consente una facile integrazione nelle linee di produzione esistenti. Inoltre, l'efficienza dei forni SPS è rafforzata dalla loro capacità di raggiungere velocità di riscaldamento e raffreddamento rapide, che contribuiscono ulteriormente al risparmio energetico e alla riduzione dei costi operativi. Il meccanismo di riscaldamento interno, che prevede il riscaldamento Joule dello stampo in grafite e della bricchetta di polvere, assicura una distribuzione uniforme del calore e riduce al minimo le perdite di calore, ottimizzando così il processo di sinterizzazione.
Sinterizzazione di purificazione e attivazione
L'SPS offre anche vantaggi unici in termini di sinterizzazione di purificazione e attivazione. Il processo è in grado di rimuovere i gas adsorbiti e le pellicole di ossido dalle superfici delle particelle, con conseguente pulizia delle interfacce e miglioramento del legame. Questo effetto di purificazione, combinato con l'attivazione delle superfici delle particelle, consente di sinterizzare materiali altrimenti difficili da lavorare. Questa capacità amplia la gamma di materiali che possono essere efficacemente sinterizzati con SPS, tra cui ceramiche e compositi avanzati.
In conclusione, la sinterizzazione al plasma di scintilla (SPS) offre una moltitudine di vantaggi che la rendono una scelta superiore per la lavorazione dei materiali. La velocità di sinterizzazione, la capacità di sinterizzazione a grana fine, il controllo della densità e del gradiente di temperatura, l'efficienza e la compattezza ne fanno uno strumento prezioso sia per la ricerca che per le applicazioni industriali. Sfruttando questi vantaggi, l'SPS continua a spingersi oltre i confini della scienza e dell'ingegneria dei materiali, consentendo lo sviluppo di materiali innovativi e ad alte prestazioni.
Applicazioni della SPS in vari settori industriali
La tecnologia di sinterizzazione al plasma di scintilla (SPS) ha rivoluzionato i processi di produzione in diversi settori, consentendo la creazione di materiali avanzati con proprietà uniche. La tecnologia SPS è particolarmente rinomata per la sua capacità di produrre materiali ad alta densità e a grana fine in modo rapido e a temperature relativamente basse, il che la rende un metodo preferito per la sintesi di nanomateriali, ceramiche, compositi e impianti medici.
Nanomateriali
Una delle applicazioni più significative della SPS è la preparazione di nanomateriali. I nanomateriali presentano eccezionali proprietà meccaniche e fisiche grazie alla loro piccola dimensione dei grani, che ne aumenta la resistenza e la plasticità. La SPS facilita la sintesi di questi materiali inibendo la crescita dei grani durante il processo di sinterizzazione. Il riscaldamento rapido e i brevi tempi di sinterizzazione inerenti alla SPS contribuiscono a mantenere la dimensione dei grani su scala nanometrica, che è fondamentale per le prestazioni dei nanomateriali. Questa tecnica è particolarmente efficace per la sinterizzazione di polveri ottenute con metodi come la legatura meccanica, che spesso sono difficili da consolidare con i metodi tradizionali.
Ceramica e cermet
L'SPS è ampiamente utilizzato anche nella produzione di ceramiche e cermet a grana fine e ad alta densità. L'esclusivo meccanismo di riscaldamento dell'SPS, in cui ogni particella di polvere e i pori tra di esse agiscono come fonti di calore, consente una rapida densificazione e una significativa riduzione dei tempi e delle temperature di sinterizzazione. Questo metodo è molto vantaggioso per la produzione industriale, in quanto consente di risparmiare energia e di migliorare l'efficienza produttiva. La capacità di produrre ceramiche ad alta densità e con una struttura a grana fine ne aumenta la resistenza meccanica e la durata, rendendole adatte a varie applicazioni ingegneristiche.
Materiali funzionali a gradiente
I materiali funzionali a gradiente, che presentano una distribuzione a gradiente in determinate direzioni, sono un'altra area in cui l'SPS ha apportato contributi significativi. I metodi di sinterizzazione tradizionali hanno difficoltà a gestire le diverse temperature di sinterizzazione richieste per ogni strato nei materiali a gradiente. L'SPS, invece, è in grado di gestire efficacemente questo gradiente, consentendo la produzione su scala industriale di questi materiali complessi. Il processo di sinterizzazione controllata di SPS garantisce che ogni strato raggiunga le proprietà desiderate senza compromettere l'integrità della struttura complessiva.
Impianti medici
In campo medico, l'SPS viene utilizzato per produrre impianti con proprietà meccaniche e biocompatibilità personalizzate. La capacità di controllare con precisione le condizioni di sinterizzazione consente di creare impianti con proprietà meccaniche specifiche che corrispondono all'osso umano, migliorandone la funzionalità e la longevità. Inoltre, le SPS possono essere utilizzate per produrre strutture porose che facilitano la crescita dell'osso, migliorando l'integrazione degli impianti con il tessuto circostante.
Materiali compositi e nanostrutturati
La SPS è fondamentale per la fabbricazione di materiali compositi e nanostrutturati con proprietà migliorate, come quelle magnetiche, piezoelettriche, termoelettriche e ottiche. Il processo di sinterizzazione rapida in SPS aiuta a mantenere la nanostruttura dei materiali, che è fondamentale per le loro prestazioni. Ad esempio, l'SPS viene utilizzato per la sinterizzazione di nanotubi di carbonio per sviluppare elettrodi a emissione di elettroni di campo, dimostrando la sua versatilità nel trattare diversi tipi di materiali.
In conclusione, la sinterizzazione al plasma di scintilla è emersa come una tecnica versatile e potente con applicazioni che spaziano in diversi settori. La sua capacità di produrre materiali avanzati di alta qualità con proprietà uniche la rende uno strumento indispensabile nella produzione moderna. Con l'avanzare della ricerca e dello sviluppo in questo campo, si prevede che le potenziali applicazioni della sinterizzazione a plasma incandescente si espanderanno ulteriormente, promuovendo l'innovazione nella scienza e nell'ingegneria dei materiali.
Casi di studio: Implementazioni di successo di SPS
La tecnologia di sinterizzazione al plasma di scintilla (SPS) ha rivoluzionato il campo della scienza dei materiali, consentendo la sinterizzazione e la densificazione rapida di un'ampia gamma di materiali con proprietà migliorate. Questa sezione presenta diversi casi di studio che evidenziano il successo delle applicazioni di SPS sia in ambito di ricerca che industriale, dimostrando la sua versatilità ed efficacia.
Materiali per l'accumulo di energia
Una delle applicazioni più significative della SPS è lo sviluppo di materiali avanzati per l'accumulo di energia. Ad esempio, la SPS è stata utilizzata per produrre batterie agli ioni di litio ad alta capacità con prestazioni migliorate. Controllando con precisione i parametri di sinterizzazione, i ricercatori sono riusciti a creare materiali per batterie con densità energetiche più elevate e una migliore durata dei cicli. Secondo alcuni studi, le batterie agli ioni di litio trattate con SPS hanno mostrato un aumento del 20% della capacità di immagazzinare energia rispetto ai metodi convenzionali, rendendole ideali per l'uso nei veicoli elettrici e nell'elettronica portatile.
Ingegneria biomedica
Nel campo dell'ingegneria biomedica, SPS è stata determinante nella creazione di ceramiche porose per la somministrazione di farmaci e di impalcature per l'ingegneria dei tessuti. Questi materiali richiedono un controllo preciso della loro microstruttura per garantire la compatibilità con i sistemi biologici. L'SPS consente la fabbricazione di strutture altamente porose con dimensioni dei pori controllate, che sono cruciali per la somministrazione efficace di farmaci e la crescita dei tessuti. Ad esempio, gli scaffold di idrossiapatite lavorati con SPS sono stati utilizzati nell'ingegneria del tessuto osseo, dimostrando una biocompatibilità e una resistenza meccanica superiori rispetto ai metodi tradizionali.
Ceramica avanzata
La tecnologia SPS è stata ampiamente utilizzata anche nella produzione di ceramiche avanzate, come i superconduttori ad alta temperatura e le ceramiche piezoelettriche ad alte prestazioni. Questi materiali sono fondamentali per applicazioni che vanno dalla trasmissione di energia ai sensori e agli attuatori. L'SPS consente di densificare queste ceramiche a temperature più basse e in tempi più brevi, preservandone le proprietà uniche. Ad esempio, la SPS è stata utilizzata per produrre superconduttori di ittrio-bario-rame (YBCO) con densità vicine a quelle teoriche, migliorando significativamente le loro temperature di transizione superconduttiva.
Intermetallici e compositi
La versatilità dell'SPS è ulteriormente dimostrata dalla lavorazione di intermetallici e compositi. La SPS è stata utilizzata per creare leghe avanzate con proprietà meccaniche, termiche ed elettriche migliorate. Ad esempio, la SPS è stata impiegata per sintetizzare leghe intermetalliche di alluminuro di titanio (TiAl), che presentano una resistenza superiore alle alte temperature e all'ossidazione. Inoltre, la SPS ha permesso la produzione di ceramiche e metalli rinforzati con proprietà meccaniche migliorate, come i compositi a matrice di titanio con particelle ceramiche incorporate, che danno origine a materiali con elevata resistenza e resistenza all'usura.
Applicazioni industriali
In ambito industriale, la tecnologia SPS è stata adottata per la produzione di vari materiali, tra cui materiali magnetici, materiali duri e materiali funzionali a gradiente. Ad esempio, aziende giapponesi come Ohta Seiki hanno implementato con successo l'SPS per la produzione di massa di materiali superduri al 100% in WC, fornendo oltre 40 produttori in Giappone e all'estero. Questi materiali sono utilizzati in un'ampia gamma di applicazioni, dagli utensili da taglio ai componenti elettronici, dimostrando la scalabilità industriale di SPS.
Conclusioni
I casi di studio qui presentati illustrano l'ampia applicabilità di SPS in vari campi, dall'accumulo di energia all'ingegneria biomedica e ai materiali avanzati. La capacità di SPS di sinterizzare e densificare rapidamente i materiali a basse temperature, unita al preciso controllo del processo, lo rende uno strumento prezioso per gli scienziati e gli ingegneri dei materiali. Con l'avanzare della ricerca e dello sviluppo, si prevede che le potenziali applicazioni dell'SPS si espanderanno ulteriormente, consolidando la sua posizione di tecnologia leader nella lavorazione dei materiali.
Sfide e considerazioni sulla SPS
L'implementazione della tecnologia di sinterizzazione al plasma di scintilla (SPS) presenta diverse sfide e considerazioni che le organizzazioni devono affrontare per sfruttarne appieno i vantaggi. Tra queste, i costi elevati delle apparecchiature, le complessità operative e la necessità di una formazione specializzata. Comprendere queste sfide e sviluppare strategie per superarle è fondamentale per integrare e utilizzare con successo la tecnologia SPS.
Costi delle attrezzature
Uno dei principali ostacoli all'adozione della tecnologia SPS è l'elevato investimento iniziale richiesto per le attrezzature. I sistemi SPS sono sofisticati e includono funzioni avanzate come il controllo preciso della temperatura e della pressione, sistemi di vuoto e alimentatori specializzati. Questi componenti non solo aumentano il costo iniziale, ma richiedono anche una manutenzione e una calibrazione regolari per garantire prestazioni ottimali.
Complessità operative
Le operazioni di SPS prevedono più fasi, tra cui la creazione del vuoto, l'applicazione della pressione, il riscaldamento a resistenza e il raffreddamento controllato. Ogni fase richiede un monitoraggio e una regolazione accurati per evitare difetti e garantire le proprietà desiderate del materiale. La complessità di queste operazioni richiede un alto livello di competenza tecnica e un'attenzione meticolosa ai dettagli, che può essere impegnativa per le organizzazioni che non hanno esperienza di tecniche di sinterizzazione avanzate.
Formazione specializzata
Data la natura tecnica dell'SPS, il personale coinvolto nel funzionamento e nella manutenzione delle apparecchiature deve seguire una formazione specializzata. Questa formazione deve riguardare non solo il funzionamento di base del sistema SPS, ma anche argomenti avanzati come l'ottimizzazione del processo, la risoluzione dei problemi e i protocolli di sicurezza. Il costo e il tempo richiesti per questa formazione possono essere significativi, ritardando potenzialmente l'implementazione della tecnologia SPS.
Strategie per superare le sfide
Per superare queste sfide, le organizzazioni possono adottare diverse strategie:
-
Investimento in attrezzature di alta qualità: Sebbene il costo iniziale sia elevato, investire in apparecchiature SPS affidabili e di alta qualità può ridurre i costi operativi e di manutenzione a lungo termine. La scelta di apparecchiature di produttori affidabili con una solida rete di supporto e assistenza può contribuire a ridurre i problemi che si presentano durante il funzionamento.
-
Collaborazione e partnership: La collaborazione con istituti di ricerca o altre aziende che hanno esperienza in materia di SPS può fornire preziose intuizioni e supporto. I progetti di collaborazione possono aiutare a condividere i costi e le competenze necessarie per un'implementazione di successo.
-
Formazione e sviluppo continui: Investire nella formazione continua del personale può garantire l'aggiornamento sulle ultime tecniche e sulle migliori pratiche in materia di SPS. Questo obiettivo può essere raggiunto attraverso workshop, corsi online e sessioni di formazione pratica.
-
Ottimizzazione dei processi: Lo sviluppo di processi solidi, ben documentati e standardizzati può contribuire a ridurre la variabilità e a migliorare la coerenza dei risultati. Ciò comporta un'attenta sperimentazione e validazione per identificare le condizioni ottimali per ogni materiale e applicazione.
-
Focus su ricerca e sviluppo: Impegnarsi in attività di ricerca e sviluppo continue può aiutare le aziende a rimanere all'avanguardia nella tecnologia SPS. Ciò può comportare l'esplorazione di nuovi materiali, l'ottimizzazione dei processi esistenti e lo sviluppo di applicazioni innovative per i componenti prodotti con SPS.
Conclusioni
Sebbene l'implementazione della tecnologia SPS presenti diverse sfide, queste possono essere gestite efficacemente con le giuste strategie e investimenti. Affrontando i costi elevati, le complessità operative e i requisiti di formazione, le organizzazioni possono sbloccare il pieno potenziale di SPS, portando a significativi progressi nella scienza dei materiali e nella produzione.
Tendenze future della sinterizzazione al plasma scintillante
La tecnologia di sinterizzazione al plasma scintillante (SPS), nota per le sue capacità di sinterizzazione rapida a temperature relativamente basse, continua a evolversi, offrendo progressi significativi in termini di efficienza, scalabilità e varietà di applicazioni. Con l'aumento della domanda di nuovi materiali e di processi produttivi efficienti, la tecnologia SPS è all'avanguardia nell'innovazione tecnologica della scienza dei materiali.
Miglioramenti dell'efficienza
Una delle principali aree di interesse della tecnologia SPS è il miglioramento dell'efficienza. I metodi di sinterizzazione tradizionali possono richiedere molto tempo e molta energia, mentre l'SPS riduce significativamente sia il tempo di lavorazione che il consumo energetico. Gli sviluppi futuri mirano a ottimizzare ulteriormente questi aspetti affinando le tecniche di corrente d'impulso e migliorando i sistemi di controllo dei dispositivi SPS. Ad esempio, i progressi nei sistemi di alimentazione e controllo potrebbero consentire un controllo più preciso della temperatura e della pressione, portando a processi di sinterizzazione più efficienti.
Miglioramenti della scalabilità
La scalabilità è un altro aspetto critico della tecnologia SPS. Attualmente, la tecnologia SPS è utilizzata prevalentemente in laboratorio e per produzioni su piccola scala. Tuttavia, per soddisfare la domanda industriale, i futuri sistemi SPS dovranno gestire volumi maggiori e forme più complesse. I ricercatori stanno esplorando nuovi materiali e progetti di stampi in grado di resistere a pressioni e temperature più elevate, garantendo l'integrità e la riutilizzabilità degli stampi. Inoltre, l'integrazione di robotica e automazione avanzata nelle apparecchiature SPS potrebbe facilitare la produzione di pezzi più grandi e intricati, rendendo le SPS un'opzione valida per la produzione di grandi volumi.
Espansione verso nuovi tipi di materiali e industrie
La tecnologia SPS è stata tradizionalmente utilizzata per la sinterizzazione di metalli e ceramiche. Tuttavia, le sue capacità uniche offrono un potenziale di espansione verso nuovi tipi di materiali e industrie. La ricerca futura si concentrerà probabilmente sull'applicazione della tecnologia SPS a una gamma più ampia di materiali, tra cui polimeri, compositi e nanomateriali. Questa espansione potrebbe aprire nuove applicazioni in settori come l'elettronica, l'aerospaziale e l'ingegneria biomedica, dove il controllo preciso delle proprietà dei materiali è fondamentale.
Vantaggi ambientali ed economici
Anche i vantaggi ambientali ed economici di SPS sono alla base del suo sviluppo futuro. Il processo produttivo di SPS, efficiente dal punto di vista energetico e con pochi rifiuti, è in linea con gli obiettivi globali di sostenibilità. Poiché le industrie sono sempre più alla ricerca di soluzioni produttive ecocompatibili, la SPS potrebbe diventare il metodo preferito per la produzione di materiali ad alte prestazioni. Inoltre, i tempi di lavorazione ridotti e i minori costi energetici associati alla SPS possono portare a significativi risparmi economici, rendendola un'opzione interessante per i produttori.
Integrazione tecnologica e collaborazione
Infine, il futuro della tecnologia SPS comporterà probabilmente una maggiore integrazione con altre tecnologie di produzione avanzate e collaborazioni tra diversi settori. Ad esempio, la combinazione di SPS con le tecniche di produzione additiva potrebbe portare alla creazione di processi di produzione ibridi che sfruttano i punti di forza di entrambe le tecnologie. Inoltre, la ricerca interdisciplinare che coinvolge la scienza dei materiali, l'ingegneria elettrica e l'ingegneria meccanica potrebbe portare a progressi nella comprensione e nell'ottimizzazione del processo SPS.
In conclusione, il futuro della sinterizzazione al plasma di scintilla è promettente, con potenziali progressi pronti a renderla una tecnologia più efficiente, scalabile e versatile. Con il proseguimento della ricerca e dello sviluppo, la sinterizzazione al plasma potrebbe rivoluzionare il modo in cui produciamo materiali avanzati, contribuendo all'innovazione in vari settori e promuovendo pratiche di produzione sostenibili.
Conclusioni: Il ruolo delle SPS nella scienza dei materiali
In conclusione, lasinterizzazione al plasma di scintilla (SPS) si distingue come tecnologia trasformativa nel campo della scienza dei materiali. La sua capacità di sinterizzare rapidamente i materiali a livelli di grana fine, unita alla sua efficienza e versatilità, fa dell'SPS una pietra miliare nella moderna lavorazione dei materiali. Guardando al futuro, la SPS è pronta a promuovere innovazioni significative, espandendo le sue applicazioni in vari settori e aprendo la strada allo sviluppo di materiali avanzati ad alte prestazioni. La continua evoluzione e l'adozione della tecnologia SPS plasmerà senza dubbio il futuro della scienza dei materiali, offrendo nuove possibilità e soluzioni alle complesse sfide dei materiali.
CONTATTATECI PER UNA CONSULENZA GRATUITA
I prodotti e i servizi di KINTEK LAB SOLUTION sono stati riconosciuti da clienti di tutto il mondo. Il nostro personale sarà lieto di assistervi per qualsiasi richiesta. Contattateci per una consulenza gratuita e parlate con uno specialista del prodotto per trovare la soluzione più adatta alle vostre esigenze applicative!