Introduzione ai forni di sinterizzazione al plasma scintillante (SPS)
I forni di sinterizzazione al plasma scintillante (SPS) rappresentano una tecnologia all'avanguardia nel campo della scienza dei materiali, in quanto offrono un approccio unico alla sinterizzazione attraverso l'uso di corrente continua ad impulsi on-off per la generazione del plasma. Questa guida completa approfondisce le complessità della tecnologia SPS, esplorando i suoi componenti come il dispositivo di pressione assiale, l'elettrodo di punzonatura raffreddato ad acqua e la camera a vuoto. Comprendendo le caratteristiche principali e le applicazioni versatili dell'SPS, possiamo apprezzare come questa tecnologia rivoluziona la sinterizzazione rapida, efficiente e di alta qualità di vari materiali, dai metalli e dalle ceramiche ai nanomateriali e ai compositi.
Caratteristiche principali dei forni di sinterizzazione al plasma scintillante
I forni di sinterizzazione al plasma di scintilla (SPS) hanno rivoluzionato il campo della scienza dei materiali grazie alle loro capacità uniche e ai tempi di lavorazione rapidi. Questi forni utilizzano un'elevata corrente continua pulsata per riscaldare e sinterizzare polveri compatte, offrendo diversi vantaggi rispetto ai metodi di sinterizzazione tradizionali. Qui approfondiamo le caratteristiche principali dei forni SPS, tra cui la sinterizzazione rapida, la sinterizzazione di purificazione e attivazione, la sinterizzazione a grana fine, la sinterizzazione ad ampio raggio di temperatura, la sinterizzazione a controllo di densità e la sinterizzazione a gradiente di temperatura.
Sinterizzazione rapida
Uno dei vantaggi più significativi dei forni SPS è la capacità di ottenere una sinterizzazione rapida. La velocità di riscaldamento può superare i 500°C/min, una velocità nettamente superiore a quella dei metodi tradizionali come la pressatura a caldo, la pressatura isostatica a caldo (HIP) e la sinterizzazione senza pressione. Questa rapida velocità di riscaldamento consente tempi di sinterizzazione molto più brevi, spesso riducendo il processo da ore a pochi minuti. La velocità di riscaldamento e raffreddamento minimizza inoltre i processi di coartazione e aiuta a mantenere le nanostrutture intrinseche del materiale dopo la completa densificazione.
Sinterizzazione di purificazione e attivazione
I forni SPS offrono un esclusivo processo di sinterizzazione di purificazione e attivazione. L'elevata corrente continua pulsata induce un effetto di purificazione della superficie delle particelle, che rimuove i gas adsorbiti e le pellicole di ossido. Questo processo di purificazione, combinato con l'effetto di attivazione della superficie delle particelle, consente la sinterizzazione di materiali tradizionalmente difficili da sinterizzare. Questa caratteristica è particolarmente vantaggiosa per i materiali con requisiti di purezza elevati o sensibili ai contaminanti superficiali.
Sinterizzazione a grana fine
Il rapido aumento della temperatura nei forni SPS inibisce la crescita dei grani, consentendo la regolazione della microstruttura e la preparazione di corpi sinterizzati a grana fine. Questa caratteristica rende l'SPS un metodo eccellente per la preparazione di materiali nanocristallini. Controllando i parametri di sinterizzazione, i ricercatori possono ottenere la dimensione dei grani e la microstruttura desiderate, fondamentali per ottimizzare le proprietà meccaniche, elettriche e termiche del materiale.
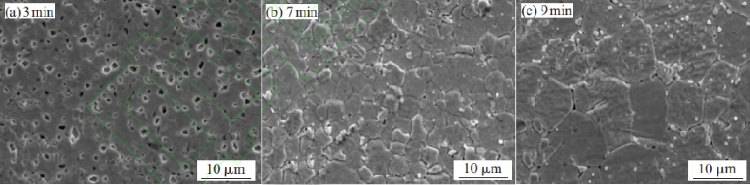
Sinterizzazione ad ampia gamma di temperature
I forni SPS possono operare in un'ampia gamma di temperature, da quelle più basse fino a 2300°C. Questo ampio intervallo di temperature rende i forni SPS versatili per la sinterizzazione di una varietà di materiali, tra cui ceramiche, metalli e compositi. La capacità di raggiungere temperature elevate in modo rapido ed efficiente è particolarmente utile per i materiali che richiedono una lavorazione ad alta temperatura per ottenere una densificazione completa e proprietà ottimali.
Sinterizzazione a controllo di densità
Un'altra caratteristica notevole dei forni SPS è la capacità di controllare la densità del corpo sinterizzato. Dai corpi porosi ai corpi sinterizzati completamente densi, i forni SPS offrono un controllo flessibile della densità. Questo si ottiene regolando i parametri di sinterizzazione, come la forza applicata, la corsa del pistone e la corrente. Il controllo preciso della densità è essenziale per adattare le proprietà del materiale a specifiche applicazioni, ad esempio nei settori aerospaziale, automobilistico e medico.
Sinterizzazione a gradiente di temperatura
I forni SPS possono creare un gradiente di temperatura all'interno dello stampo, consentendo la sinterizzazione simultanea di materiali con punti di fusione diversi. Questa caratteristica è particolarmente utile per la preparazione di materiali a gradazione funzionale (FGM), in cui diversi strati o regioni del materiale richiedono condizioni di lavorazione diverse. La capacità di creare un gradiente di temperatura (centinaia di °C/mm) all'interno dello stampo consente di produrre materiali complessi e multistrato con proprietà e funzionalità personalizzate.
In conclusione, i forni SPS offrono una serie di caratteristiche avanzate che li rendono uno strumento potente nel campo della scienza dei materiali. La loro capacità di ottenere sinterizzazione rapida, sinterizzazione di purificazione e attivazione, sinterizzazione a grana fine, sinterizzazione a temperatura ampia, sinterizzazione a controllo di densità e sinterizzazione a gradiente di temperatura li rende versatili ed efficienti per un'ampia gamma di applicazioni. Con l'avanzare della ricerca e dello sviluppo in questo campo, i forni SPS sono destinati a svolgere un ruolo sempre più importante nella produzione di materiali ad alte prestazioni.
Versatilità nella lavorazione dei materiali con SPS
La sinterizzazione al plasma di scintille (SPS) è una tecnica altamente efficiente e versatile utilizzata per la sinterizzazione di un'ampia gamma di materiali, tra cui metalli, ceramiche, nanomateriali e materiali compositi. Questo metodo sfrutta impulsi di corrente continua per generare scintille di plasma tra le particelle, favorendo processi di riscaldamento e densificazione rapidi. L'SPS è rinomato per la sua capacità di ottenere una preparazione dei materiali di alta qualità con vantaggi significativi rispetto ai metodi di sinterizzazione tradizionali.
Ampia applicabilità della SPS
Nanomateriali
La tecnologia SPS è particolarmente efficace nella preparazione dei nanomateriali. I metodi di sinterizzazione tradizionali spesso faticano a mantenere la dimensione dei grani su scala nanometrica e a raggiungere una densità completa. La tecnologia SPS, con il suo riscaldamento rapido e i brevi tempi di sintesi, sopprime efficacemente la coartazione dei grani. Questo processo rapido consente anche di mantenere difetti e sottostrutture nella polvere, il che può essere vantaggioso per la sintesi di materiali metastabili e nanomateriali.
Materiali funzionali a gradiente
I materiali funzionali a gradiente (FGM) sono compositi con una distribuzione a gradiente in una certa direzione, che spesso richiedono temperature di sinterizzazione diverse per ogni strato. I metodi tradizionali, come la deposizione chimica da vapore (CVD) e la deposizione fisica da vapore (PVD), sono costosi e impegnativi per la produzione industriale. SPS supera queste sfide consentendo la sinterizzazione di materiali con gradienti di resistenza al calore, resistenza all'usura, durezza, conduttività e porosità, con la possibilità di gestire più strati.
Materiali elettromagnetici
L'SPS viene utilizzato anche per la produzione di vari materiali elettromagnetici, tra cui elementi di conversione termoelettrica e materiali utilizzati nel campo dell'elettronica come materiali superconduttori, materiali magnetici, materiali dielettrici e altro ancora. Questi materiali sono fondamentali per applicazioni che vanno dall'accumulo di energia all'ingegneria biomedica.
Composti intermetallici
I composti intermetallici, noti per la loro fragilità e gli elevati punti di fusione, richiedono processi di preparazione specializzati. SPS offre un metodo efficiente per la preparazione di questi composti, sfruttando l'autoriscaldamento e l'attivazione superficiale tra le particelle, consentendo una sinterizzazione rapida e a bassa temperatura.
Ceramiche e cermet a grana fine e ad alta densità
Il processo SPS accorcia notevolmente i tempi di sinterizzazione e riduce le temperature sfruttando il calore generato all'interno di ogni particella di polvere e gli spazi tra di esse. Ciò rende l'SPS un metodo eccellente per la preparazione di ceramiche e cermet a grana fine e ad alta densità, essenziali per diverse applicazioni industriali.
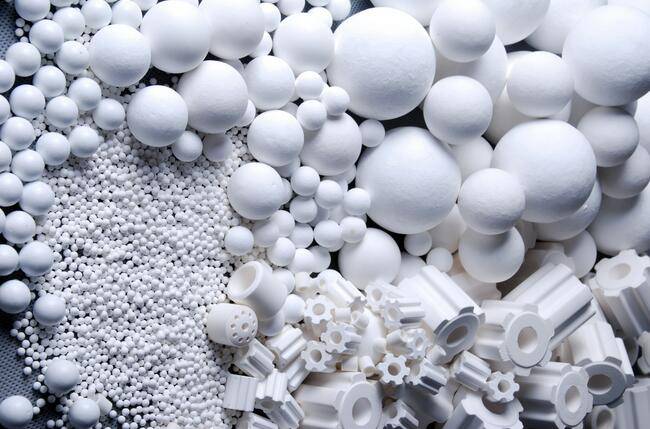
Vantaggi della SPS
- Tempi di ciclo più brevi: L'SPS riduce significativamente i cicli di sinterizzazione da ore o giorni a pochi minuti, aumentando la produttività e le capacità di sviluppo rapido dei materiali.
- Temperature di sinterizzazione più basse: Consente di sinterizzare a temperature più basse rispetto ai processi convenzionali, il che è particolarmente vantaggioso per i materiali sensibili al calore.
- Controllo del processo ad alta precisione: L'SPS offre un controllo preciso dei parametri di sinterizzazione, come la temperatura e la pressione, garantendo risultati ottimali e consentendo la creazione di prodotti chimici unici, non realizzabili con i metodi tradizionali.
- Versatilità: Può densificare un'ampia gamma di materiali, dai metalli a basso punto di fusione alle ceramiche ad altissima temperatura, e persino legare materiali dissimili che richiedono distribuzioni di temperatura non uniformi.
Applicazioni di SPS
La tecnologia SPS trova applicazione in diversi campi, tra cui:
- Accumulo di energia: Batterie agli ioni di litio ad alta capacità e altri materiali avanzati per l'accumulo di energia.
- Ingegneria biomedica: Ceramiche porose per la somministrazione di farmaci e impalcature per l'ingegneria dei tessuti.
- Ceramica avanzata: Superconduttori ad alta temperatura e ceramiche piezoelettriche ad alte prestazioni.
- Intermetallica: Leghe avanzate con proprietà meccaniche, termiche ed elettriche migliorate.
- Compositi: Ceramiche e metalli rinforzati con proprietà meccaniche migliorate.
In conclusione, la sinterizzazione al plasma di scintilla si distingue come metodo altamente versatile ed efficiente per la sinterizzazione di diversi materiali, offrendo vantaggi significativi in termini di controllo del processo, efficienza energetica e capacità di produrre materiali di alta qualità per un'ampia gamma di applicazioni.
Facilità operativa e caratteristiche di sicurezza dei forni SPS
I forni di sinterizzazione al plasma di scintilla (SPS) sono rinomati per la loro avanzata facilità operativa e le robuste caratteristiche di sicurezza, che li rendono una scelta privilegiata in varie applicazioni industriali. Questi forni sono progettati con un'attenzione particolare alle interfacce di facile utilizzo e ai meccanismi di sicurezza completi per garantire operazioni efficienti e sicure.
Design e sistemi di controllo di facile utilizzo
I forni SPS sono dotati di sistemi di controllo all'avanguardia che migliorano la facilità di funzionamento. Una caratteristica notevole è l'integrazione di interfacce touch screen e controllori logici programmabili (PLC) per il controllo centrale. Questa configurazione consente agli operatori di monitorare e regolare facilmente i parametri del forno, riducendo la complessità del funzionamento e il potenziale di errore umano. Il sistema PLC Allen-Bradley, ad esempio, è noto per la sua facilità di programmazione e modifica, che semplifica ulteriormente la gestione delle operazioni del forno.
L'armadio di controllo di questi forni è progettato per ospitare tutti i controlli elettrici in un armadio standard NEMA 12, assicurando la conformità agli standard di sicurezza come NFPA 70. Questo controllo centralizzato non solo aumenta la sicurezza, ma rende anche più semplice la manutenzione e la risoluzione dei problemi. L'inclusione di un interblocco integrato dell'interruttore elettrico principale aggiunge un ulteriore livello di sicurezza, impedendo operazioni non autorizzate o accidentali.
Meccanismi di sicurezza avanzati
La sicurezza è una preoccupazione fondamentale nel funzionamento dei forni SPS e questi sistemi sono dotati di diversi livelli di protezione. Tra le principali caratteristiche di sicurezza vi sono gli allarmi di malfunzionamento per sovratemperatura e sovrapressione, che segnalano agli operatori i potenziali pericoli in tempo reale. Inoltre, sono presenti sistemi meccanici di protezione automatica della pressione per salvaguardare i problemi legati alla pressione, garantendo l'integrità del forno e dei materiali in lavorazione.
I forni dispongono anche di funzioni di interblocco che impediscono il funzionamento in condizioni non sicure. Ad esempio, gli interblocchi vengono utilizzati per disattivare il forno in caso di mancanza di elettricità o acqua, pressione insufficiente o condizioni di sovratemperatura. Questi interblocchi sono fondamentali per prevenire gli incidenti e proteggere sia l'apparecchiatura che gli operatori.
Le funzionalità di controllo remoto sono un'altra importante caratteristica di sicurezza, in quanto consentono di diagnosticare a distanza i malfunzionamenti e di aggiornare i programmi. Questo non solo migliora l'efficienza della manutenzione, ma riduce anche il rischio di esposizione a condizioni pericolose per i tecnici.
Integrazione della termocoppia
Il controllo accurato della temperatura è essenziale nei processi di sinterizzazione e i forni SPS utilizzano termocoppie di alta qualità, come quelle di tipo "S" e "K", per il monitoraggio e il controllo precisi della temperatura. Queste termocoppie sono integrate con pannelli jack appropriati per il monitoraggio e il controllo del lavoro, assicurando che il processo di sinterizzazione rimanga entro intervalli di temperatura sicuri e ottimali.
Conclusioni
In sintesi, la facilità operativa e le caratteristiche di sicurezza dei forni SPS sono progettate per fornire un'esperienza di sinterizzazione sicura e senza interruzioni. Grazie ai sistemi di controllo di facile utilizzo, ai meccanismi di sicurezza avanzati e al controllo preciso della temperatura, questi forni sono ideali per un'ampia gamma di applicazioni nella lavorazione di metalli, ceramiche, nanomateriali e altro ancora. L'integrazione di tecnologie moderne e solidi protocolli di sicurezza assicura che gli operatori possano lavorare in modo efficiente riducendo al minimo i rischi.
Sistemi avanzati di controllo e monitoraggio in SPS
I sistemi avanzati di controllo e monitoraggio sono parte integrante del processo di sinterizzazione al plasma di scintilla (SPS) e consentono di regolare con precisione la temperatura, la pressione e la corrente, oltre all'acquisizione completa dei dati per tracciare e analizzare i parametri di sinterizzazione. Questi sistemi sono fondamentali per garantire la qualità e la riproducibilità dei materiali sinterizzati.
Controllo automatico del programma
Il processo SPS inizia con il caricamento di una quantità nota di campione di polvere essiccata e macinata in uno stampo cilindrico rivestito con un foglio di grafite, che facilita la rimozione del compatto sinterizzato. Lo stampo viene quindi posizionato all'interno della camera SPS e viene impostato il profilo tempo-temperatura specifico richiesto per l'esperimento. L'atmosfera all'interno della camera viene mantenuta secondo le necessità, che si tratti di vuoto, argon o altri ambienti controllati. La potenza è impostata al massimo in modalità Auto e il carico richiesto viene applicato allo stampo. La posizione dell'asse z è impostata a zero e il timer viene attivato prima di premere SINTER per avviare il processo di sinterizzazione.
Per la misurazione della temperatura, SPS utilizza due tipi di strumenti: le termocoppie per le temperature di sinterizzazione inferiori a 1000°C e i pirometri per le temperature superiori a 1000°C. Un impulso elevato di corrente continua viene fatto passare tra gli elettrodi di grafite e contemporaneamente viene applicata una pressione assiale dall'inizio del ciclo di sinterizzazione. Il campione viene riscaldato per effetto del riscaldamento Joule e delle scintille tra le particelle, con conseguente trasferimento istantaneo di calore e massa. Dopo la sinterizzazione, l'alimentazione viene spenta e il campione viene lasciato raffreddare.
Sistemi di controllo computerizzati
Il sistema di controllo in SPS è tipicamente computerizzato, con un sistema di controllo automatico PLC a schermo piatto e touch computer che consente la commutazione manuale in modalità automatica. Il software del sistema di controllo è sviluppato internamente e offre un'interfaccia di facile utilizzo con monitoraggio in tempo reale delle condizioni del forno. Il sistema è stabile e affidabile, con una risposta rapida e una forte capacità anti-interferenza. Il software visualizza una schermata di simulazione a colori, integrando la visualizzazione della temperatura e il controllo della valvola del vuoto per un funzionamento intuitivo.
Il dispositivo può adottare diverse curve per l'analisi, come le curve di temperatura, potenza, vuoto, temperatura dell'acqua, pressione dell'aria e tempo di sinterizzazione. Queste curve forniscono un modo semplice per analizzare il processo di sinterizzazione sulla base dei dati storici. Il sistema può generare automaticamente file Excel attraverso l'interfaccia USB per ulteriori analisi.
Il metodo di controllo della temperatura utilizza una termocoppia per temperature fino a 1700°C, mentre per temperature superiori a 1700°C subentrano strumenti a infrarossi. Il sistema supporta diverse interfacce di comunicazione come RS232, RS422, CAN, LAN e USB, facilitando il collegamento in rete con altre apparecchiature. L'interfaccia di controllo del software è visualizzata e mostra dinamicamente il flusso di lavoro per comodità e intuitività. Il software è inoltre aggiornabile gratuitamente a vita.
Controllori e acquisizione dati
Come per altre camere di prova, SPS offre diverse scelte di controllori, che vanno da sistemi completamente manuali a sistemi completamente automatizzati. I controllori automatici consentono agli utenti di impostare i parametri del processo e, man mano che la procedura si svolge, il sistema effettua le regolazioni di pressione, temperatura e altri fattori programmati. Questi sistemi di controllo sono configurabili con software personalizzabili e una varietà di metodi di raccolta dei dati. La scelta del controllore dipende dalla criticità dell'applicazione e dalle dimensioni della camera da vuoto. Le camere più piccole possono necessitare di un semplice manometro per monitorare il pompaggio e la pressione, mentre le camere più grandi possono richiedere un sistema più aggressivo e sofisticato.
Componenti della macchina di sinterizzazione
La macchina SPS è assistita da diversi componenti, tra cui una pressa monoassiale, elettrodi di punzonatura, camera a vuoto, atmosfera controllata, generatore di impulsi CC e unità di misura di posizione, temperatura e pressione. Il controllo della temperatura di sinterizzazione si ottiene impostando parametri quali il tempo di mantenimento, la velocità di rampa, la durata dell'impulso, la corrente e la tensione dell'impulso. La scarica a impulsi in corrente continua genera un plasma di scintille, una pressione d'impatto della scintilla, un riscaldamento Joule e un effetto di diffusione del campo elettrico. Nell'SPS, la sinterizzazione è assistita dalla tensione dell'impulso CC on-off, che è diversa dalla pressatura a caldo convenzionale. L'applicazione della pressione favorisce il flusso plastico del materiale e il flusso di corrente a impulsi CC attraverso le particelle è illustrato in diagrammi dettagliati.
In conclusione, i sistemi di controllo e monitoraggio avanzati negli SPS sono essenziali per ottenere risultati di sinterizzazione precisi e riproducibili. Questi sistemi consentono regolazioni in tempo reale e l'acquisizione di dati completi, garantendo la qualità e la coerenza dei materiali sinterizzati. Grazie all'integrazione di controllo computerizzato, software personalizzabile e metodi avanzati di raccolta dati, la tecnologia SPS continua a spingersi oltre i confini della scienza e dell'ingegneria dei materiali.
Applicazioni della sinterizzazione al plasma di scintilla nella scienza dei materiali
La sinterizzazione al plasma scintillante (SPS) è una tecnica di sinterizzazione versatile e avanzata che ha rivoluzionato il campo della scienza dei materiali. Combinando pressione monoassiale, corrente continua pulsata e riscaldamento rapido, l'SPS consente di sintetizzare un'ampia gamma di materiali con proprietà e strutture uniche. Questa sezione approfondisce le molteplici applicazioni della SPS, tra cui la sinterizzazione, la giunzione, la formatura, la modifica della superficie e la sintesi di materiali come gli elettroliti solidi e i materiali termici elettrici.
Sinterizzazione di materiali avanzati
L'SPS è particolarmente rinomato per la sua capacità di sinterizzare in modo efficiente materiali ad alto punto di fusione e nanomateriali. Le rapide velocità di riscaldamento (fino a 1000°C/min) e i brevi tempi di lavorazione propri dell'SPS contribuiscono a mantenere la nanostruttura delle polveri, evitando la crescita dei grani e preservando le proprietà intrinseche delle particelle di dimensioni nanometriche. Ciò rende l'SPS un metodo ideale per la produzione di ceramiche e cermet a grana fine e ad alta densità. Ad esempio, il nitruro di titanio, un materiale noto per le sue scarse proprietà di sinterizzazione e per la sua fragilità, può essere densificato ad alti livelli con la SPS, raggiungendo densità vicine ai valori teorici a pressioni di 1-5 GPa.
Giunzione e formatura
Oltre che per la sinterizzazione, la SPS viene impiegata anche per unire materiali dissimili e formare forme complesse. La corrente continua applicata durante il processo non solo riscalda il materiale, ma aumenta anche il legame di diffusione tra le particelle, facilitando l'unione di materiali tradizionalmente difficili da unire, come la ceramica ai metalli. Questa capacità è particolarmente utile nell'industria aerospaziale e automobilistica, dove la richiesta di compositi leggeri e ad alta resistenza è elevata.
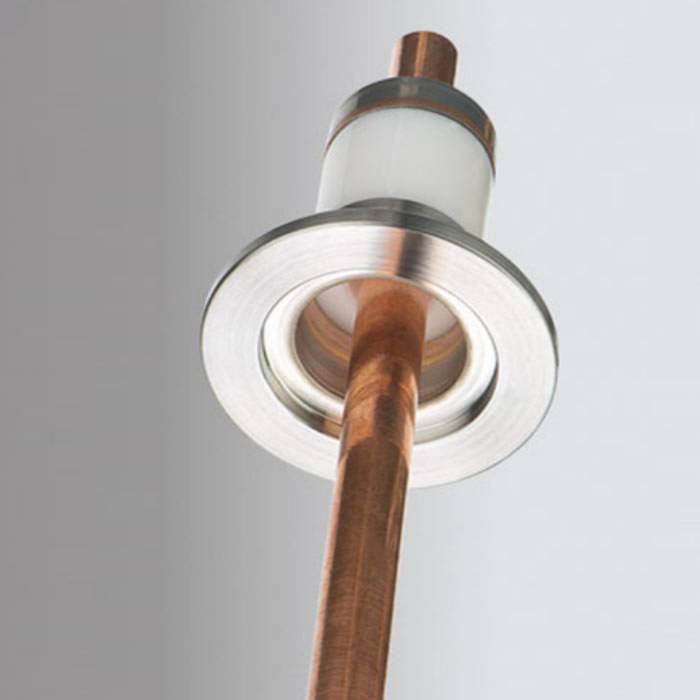
Modifica della superficie
L'SPS può essere utilizzato anche per la modifica della superficie, migliorando le proprietà superficiali dei materiali senza alterarne le caratteristiche di base. Controllando la densità di corrente e la pressione, è possibile personalizzare specifici strati superficiali per ottenere le proprietà desiderate, come una maggiore durezza, resistenza all'usura o alla corrosione. Questa applicazione è particolarmente vantaggiosa per i materiali degli utensili e per i componenti esposti ad ambienti difficili.
Sintesi di materiali funzionali
Una delle applicazioni più significative di SPS è la sintesi di materiali funzionali, tra cui elettroliti solidi e materiali elettrici termici. Gli elettroliti solidi, fondamentali per le applicazioni nelle batterie a stato solido e nelle celle a combustibile, richiedono un elevato grado di densificazione e purezza. L'SPS facilita la sintesi di questi materiali con una segregazione minima dei bordi dei grani e un'eccellente conduttività ionica. Allo stesso modo, i materiali termici elettrici, utilizzati in varie applicazioni di riscaldamento, possono essere sintetizzati con conducibilità termica e resistività elettrica controllate grazie a precisi parametri di lavorazione SPS.
Importanza industriale e prospettive future
L'importanza industriale della SPS risiede nella sua capacità di produrre materiali ad alte prestazioni con un consumo energetico ridotto e tempi di lavorazione più brevi. La tecnologia è particolarmente adatta alla produzione di nanomateriali, leghe amorfe in massa e materiali funzionali a gradiente, che sono difficili da sintetizzare con i metodi tradizionali. Mentre la ricerca continua a scoprire nuove applicazioni e a ottimizzare i parametri di lavorazione, la sinterizzazione al plasma scintillante è destinata a svolgere un ruolo cruciale nel futuro della scienza dei materiali, guidando i progressi in varie industrie high-tech.
In conclusione, la sinterizzazione al plasma di scintilla si distingue come tecnologia trasformativa nella scienza dei materiali, offrendo un ampio spettro di applicazioni, dalla sinterizzazione e giunzione alla modifica delle superfici e alla sintesi di materiali funzionali avanzati. La sua capacità di processare i materiali con elevata efficienza e precisione la rende uno strumento indispensabile sia per i ricercatori che per gli operatori industriali.
Sfide e considerazioni sull'utilizzo della tecnologia SPS
La tecnologia SPS (Spark Plasma Sintering) ha rivoluzionato il campo della scienza dei materiali, consentendo la sintesi di materiali avanzati con proprietà uniche. Tuttavia, l'implementazione di SPS comporta una serie di sfide e considerazioni che devono essere affrontate per ottenere risultati di sinterizzazione ottimali. Questa sezione approfondisce gli aspetti critici della selezione e della manutenzione degli stampi, nonché le considerazioni più ampie per operazioni SPS efficaci.
Selezione e manutenzione degli stampi
La scelta del materiale dello stampo è un fattore cruciale nella tecnologia SPS. Tradizionalmente, la grafite è il materiale preferito per la sua resistenza alle alte temperature, l'eccellente conducibilità elettrica e termica e la stabilità chimica. Tuttavia, gli stampi in grafite presentano limiti quali la bassa resistenza meccanica, la breve durata e la potenziale contaminazione dei materiali sinterizzati. Questi problemi rendono necessaria l'esplorazione di materiali di stampo alternativi.
I recenti progressi hanno portato allo sviluppo di materiali di stampo alternativi come il carburo cementato, la ceramica conduttiva e la grafite in fibra di carbonio. Ognuno di questi materiali offre vantaggi unici, ma presenta anche delle sfide. Ad esempio, gli stampi in carburo cementato offrono una maggiore resistenza, ma possono essere soggetti a deformazioni ad alte temperature. Le ceramiche conduttive offrono un equilibrio di proprietà, ma sono spesso costose. Gli stampi in fibra di carbonio e grafite combinano i vantaggi della grafite con proprietà meccaniche superiori, ma richiedono una manipolazione accurata per evitare danni.
Il mantenimento dell'integrità dello stampo è fondamentale per ottenere risultati di sinterizzazione costanti. L'ispezione e la sostituzione regolare degli stampi usurati sono essenziali per evitare incongruenze nel processo di sinterizzazione. Inoltre, una pulizia e un condizionamento adeguati degli stampi tra un utilizzo e l'altro possono prolungarne la durata e mantenere la qualità dei materiali sinterizzati.
Ottenere risultati ottimali di sinterizzazione
Per ottenere risultati ottimali di sinterizzazione, è necessario tenere conto di diverse considerazioni. Queste includono la selezione di parametri di sinterizzazione appropriati, il controllo dell'ambiente di sinterizzazione e la comprensione del meccanismo di sinterizzazione.
Parametri di sinterizzazione
I parametri di sinterizzazione, come la temperatura, la pressione e il tempo di permanenza, svolgono un ruolo fondamentale nel determinare le proprietà finali del materiale sinterizzato. Le rapide velocità di riscaldamento e raffreddamento ottenibili con l'SPS possono portare a microstrutture non in equilibrio, che possono essere vantaggiose per ottenere proprietà uniche del materiale. Tuttavia, queste velocità devono essere attentamente controllate per evitare una crescita eccessiva dei grani o altri difetti.
Ambiente di sinterizzazione
L'ambiente di sinterizzazione, compresi l'atmosfera e i gradienti di temperatura, può influenzare significativamente il processo di sinterizzazione. Il controllo dell'atmosfera può prevenire l'ossidazione e altre reazioni chimiche che possono degradare il materiale. I gradienti di temperatura all'interno dello stampo possono portare a una densificazione non uniforme, il che richiede un'attenta progettazione e ottimizzazione dell'impianto di sinterizzazione.
Comprendere il meccanismo di sinterizzazione
Il meccanismo di sinterizzazione in SPS prevede la generazione di un plasma di scintille tra le particelle, che facilita il rapido riscaldamento e la densificazione. Tuttavia, i meccanismi esatti che regolano questo processo non sono ancora del tutto compresi e sono oggetto di ricerche in corso. Le simulazioni agli elementi finiti sono emerse come uno strumento prezioso per studiare il processo di sinterizzazione, fornendo approfondimenti sulle distribuzioni di temperatura e campo elettrico all'interno del materiale.
Direzioni future
Il continuo miglioramento della tecnologia SPS richiede una ricerca e uno sviluppo costanti. Le aree chiave da esplorare in futuro includono lo sviluppo di nuovi materiali per stampi con proprietà migliorate, l'ottimizzazione dei parametri di sinterizzazione attraverso tecniche di simulazione avanzate e una comprensione più approfondita del meccanismo di sinterizzazione.
In conclusione, la tecnologia SPS offre vantaggi significativi per la sintesi di materiali avanzati, ma presenta anche diverse sfide e considerazioni che devono essere affrontate per ottenere risultati ottimali. Selezionando e mantenendo con cura gli stampi, controllando i parametri di sinterizzazione e migliorando la nostra comprensione del meccanismo di sinterizzazione, possiamo continuare a spingere i confini di ciò che è possibile con la tecnologia SPS.
Tendenze e innovazioni future nella tecnologia SPS
La tecnologia SPS (Spark Plasma Sintering), nota per le sue capacità di sinterizzazione rapida, è stata un punto focale nel campo della scienza dei materiali grazie alla sua capacità di produrre materiali di alta qualità con proprietà uniche. Con la continua evoluzione della ricerca, stanno emergendo diverse tendenze e innovazioni che promettono di aumentare l'efficienza, ampliare le applicazioni e migliorare la sicurezza della tecnologia SPS.
Industrializzazione e produzione di massa
Una delle tendenze più significative della tecnologia SPS è la sua transizione verso l'industrializzazione. Rispetto ai metodi di sinterizzazione tradizionali, la tecnologia SPS offre vantaggi sostanziali in termini di risparmio energetico e di tempo, maggiore efficienza produttiva e controllo superiore sulle prestazioni del prodotto. Paesi come il Giappone hanno già ottenuto applicazioni industriali di SPS, soprattutto nella produzione di materiali magnetici, leghe dure e materiali funzionali a gradiente. Per esempio, Ohta Seiki in Giappone ha implementato con successo la produzione di massa di materiali superduri al 100% di WC utilizzando SPS, fornendo oltre 40 produttori a livello globale. Al contrario, la tecnologia SPS in altre regioni, come la Cina, rimane in gran parte nella fase di ricerca di laboratorio, concentrandosi sulla preparazione e sulla ricerca di processo di nuovi materiali.
Diversificazione delle forme sinterizzate
Attualmente, la tecnologia SPS è limitata alla produzione di semplici campioni cilindrici a causa dei vincoli del meccanismo di sinterizzazione e degli stampi in grafite. Tuttavia, vi è una tendenza crescente a sviluppare la tecnologia SPS per creare forme e strutture più complesse. Questo progresso amplierebbe in modo significativo l'applicabilità di SPS in vari settori dell'ingegneria, consentendo la produzione di componenti intricati attualmente irraggiungibili.
Sintesi e connessione dei materiali
La tecnologia SPS non viene utilizzata solo per la sinterizzazione di materiali sfusi, ma anche per la sintesi di polveri, in particolare quelle difficili da ottenere con i metodi convenzionali. Ad esempio, l'SPS è stato utilizzato per sintetizzare polveri di materiale ZrC ad altissima temperatura, ottenendo un'elevata purezza e una granulometria fine di circa 100 nm. Inoltre, la SPS è in fase di studio per la connessione (saldatura) dei materiali, comprese le giunzioni ceramica-ceramica e ceramica-metallo. La capacità di collegare i materiali senza uno strato intermedio, grazie all'autodiffusione potenziata dal campo elettrico dell'SPS, apre nuove possibilità di creare strutture composite robuste e durevoli.
Ottimizzazione delle prestazioni degli stampi di sinterizzazione
La grafite, pur essendo comunemente utilizzata negli SPS per la sua resistenza alle alte temperature e l'eccellente conducibilità elettrica e termica, presenta limiti quali la bassa resistenza e la potenziale contaminazione dei materiali sinterizzati. C'è una tendenza a sviluppare nuovi materiali per stampi che offrano maggiore resistenza, riutilizzabilità e minore contaminazione. Si stanno studiando materiali come gli stampi in carburo cementato, gli stampi in ceramica conduttiva e gli stampi in fibra di carbonio e grafite, anche se permangono problemi come la deformazione ad alte temperature e i costi elevati.
Progressi nella simulazione e nella modellazione
La comprensione del complesso processo di sinterizzazione in SPS è fondamentale per ottimizzarne i parametri e prevederne i risultati. La simulazione a elementi finiti è emersa come uno strumento prezioso a questo proposito, consentendo ai ricercatori di analizzare le distribuzioni di temperatura e campo elettrico durante la sinterizzazione. Software come ABAQUS, MATLAB e MSC.MARC vengono utilizzati per simulare il processo di sinterizzazione, fornendo indicazioni sull'impatto dei vari parametri e contribuendo alla guida teorica della produzione.
Caratteristiche di sicurezza migliorate
Con la continua evoluzione della tecnologia SPS, l'attenzione si concentra sempre più sul miglioramento delle sue caratteristiche di sicurezza. Ciò include lo sviluppo di protocolli operativi più sicuri, il miglioramento dell'affidabilità delle apparecchiature SPS e la garanzia che la tecnologia possa essere utilizzata in una gamma più ampia di ambienti senza compromettere la sicurezza.
In conclusione, il futuro dellatecnologia SPSpromette bene, grazie alla ricerca e allo sviluppo continui volti a migliorare l'efficienza, ad ampliare le applicazioni dei materiali e a potenziare le caratteristiche di sicurezza. Questi progressi sono destinati a rivoluzionare il campo della scienza dei materiali, consentendo la produzione di materiali e componenti ad alte prestazioni prima irraggiungibili. Con la continua maturazione della tecnologia SPS, essa giocherà senza dubbio un ruolo fondamentale nel plasmare il futuro della produzione e dell'innovazione dei materiali.
CONTATTATECI PER UNA CONSULENZA GRATUITA
I prodotti e i servizi di KINTEK LAB SOLUTION sono stati riconosciuti da clienti di tutto il mondo. Il nostro personale sarà lieto di assistervi per qualsiasi richiesta. Contattateci per una consulenza gratuita e parlate con uno specialista del prodotto per trovare la soluzione più adatta alle vostre esigenze applicative!