Il processo di sinterizzazione è una tecnica di produzione che fonde materiali in polvere in una massa solida utilizzando calore e pressione, senza raggiungere il punto di fusione del materiale.Questo processo è ampiamente utilizzato in settori quali la metallurgia, la ceramica e la plastica per creare prodotti densi e durevoli.Le fasi principali comprendono la preparazione del materiale in polvere, la compressione nella forma desiderata e il riscaldamento per facilitare la diffusione atomica, che lega le particelle tra loro.La sinterizzazione migliora le proprietà dei materiali, come la resistenza, la densità e l'integrità strutturale, rendendola essenziale per la produzione di componenti che vanno dall'acciaio alle ceramiche avanzate.
Punti chiave spiegati:
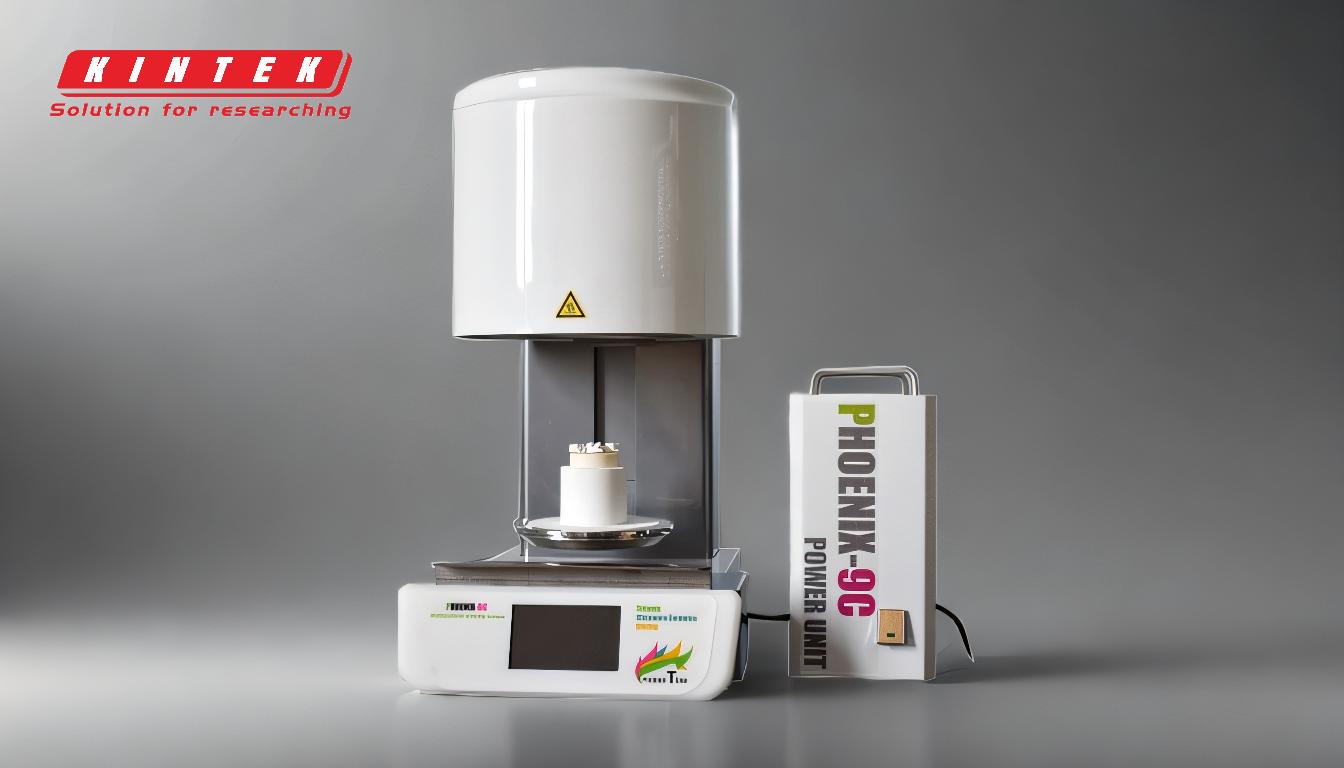
-
Definizione e scopo della sinterizzazione
- La sinterizzazione è un processo che unisce materiali in polvere in una massa solida attraverso il calore e la pressione, senza fondere il materiale.
- Viene utilizzato per creare prodotti densi, forti e durevoli in settori come la metallurgia, la ceramica e la plastica.
- L'obiettivo principale è ridurre la porosità e aumentare l'integrità strutturale fondendo le particelle a livello atomico.
-
Fasi chiave del processo di sinterizzazione
-
Preparazione del materiale in polvere:
- La materia prima viene macinata in polvere fine e miscelata con agenti accoppianti o leganti, se necessario.
- Questa fase garantisce l'uniformità e la consistenza del prodotto finale.
-
Compressione:
- La polvere viene pressata nella forma desiderata utilizzando stampi o strumenti ad alta pressione.
- Questa fase crea un "compatto verde", ovvero una struttura poco legata pronta per la sinterizzazione.
-
Riscaldamento e consolidamento:
- Il compatto verde viene riscaldato in un forno a una temperatura inferiore al punto di fusione del materiale.
- Il calore facilita la diffusione atomica, consentendo alle particelle di legarsi e densificarsi.
-
Raffreddamento e solidificazione:
- Dopo la sinterizzazione, il materiale viene raffreddato per solidificarsi in una massa unificata e densa.
-
Preparazione del materiale in polvere:
-
Tipi di sinterizzazione
-
Sinterizzazione allo stato solido:
- Le particelle si legano per diffusione atomica senza alcuna fase liquida.
- Si usa comunemente per metalli e ceramiche.
-
Sinterizzazione in fase liquida (LPS):
- Viene introdotta una piccola quantità di fase liquida per accelerare l'adesione delle particelle.
- Spesso viene utilizzata per materiali con punti di fusione elevati o forme complesse.
-
Sinterizzazione allo stato solido:
-
Applicazioni della sinterizzazione
-
Metallurgia:
- Utilizzato per produrre acciaio, ferro e altri componenti metallici per uso industriale.
- Esempio:Il minerale di ferro sinterizzato viene utilizzato negli altiforni per produrre acciaio.
-
La ceramica:
- Crea prodotti ceramici forti e resistenti al calore, come piastrelle, isolanti e utensili da taglio.
-
Plastica:
- Produce componenti in plastica durevoli con proprietà meccaniche migliorate.
-
Metallurgia:
-
Vantaggi della sinterizzazione
-
Migliori proprietà del materiale:
- Aumenta la densità, la resistenza e la durata del prodotto finale.
-
Conveniente:
- Riduce lo spreco di materiale e il consumo di energia rispetto ai processi di fusione.
-
Versatilità:
- Può essere utilizzato per un'ampia gamma di materiali e forme complesse.
-
Migliori proprietà del materiale:
-
Sfide e considerazioni
-
Controllo della temperatura:
- Il controllo preciso delle velocità di riscaldamento e raffreddamento è fondamentale per evitare difetti.
-
Gestione della porosità:
- Sebbene la sinterizzazione riduca la porosità, alcuni pori residui possono rimanere, influenzando le prestazioni del materiale.
-
Selezione del materiale:
- Non tutti i materiali sono adatti alla sinterizzazione; alcuni possono richiedere leganti o additivi aggiuntivi.
-
Controllo della temperatura:
-
Implementazione industriale
-
Apparecchiature:
- Forni, presse e stampi sono essenziali per il processo di sinterizzazione.
-
Ottimizzazione del processo:
- Parametri come la temperatura, la pressione e il tempo di sinterizzazione devono essere attentamente controllati per ottenere risultati ottimali.
-
Apparecchiature:
Grazie alla comprensione del processo di sinterizzazione, i produttori possono produrre materiali e componenti di alta qualità su misura per le specifiche esigenze industriali.Questo metodo offre un equilibrio di efficienza, economicità e versatilità, che lo rendono una pietra miliare della produzione moderna.
Tabella riassuntiva:
Aspetto | Dettagli |
---|---|
Definizione | Legare materiali in polvere in una massa solida utilizzando calore e pressione. |
Fasi chiave |
1.Preparazione del materiale in polvere
2.Compressione 3.Riscaldamento 4.Raffreddamento |
Tipi di sinterizzazione | Sinterizzazione allo stato solido, sinterizzazione in fase liquida (LPS) |
Applicazioni | Metallurgia, ceramica, plastica |
Vantaggi | Maggiore resistenza, economicità, versatilità |
Sfide | Controllo della temperatura, gestione della porosità, selezione dei materiali |
Siete pronti a ottimizzare la vostra produzione di materiali? Contattateci oggi stesso per saperne di più sulle soluzioni di sinterizzazione!