Il percorso libero medio dei magnetron sputtering si riferisce alla distanza media percorsa dalle particelle (come atomi, ioni o elettroni) tra le collisioni in un processo di sputtering.Questo concetto è fondamentale per comprendere l'efficienza e il comportamento dei sistemi di sputtering, in quanto influenza fattori quali la velocità di deposizione, la qualità del film e le prestazioni complessive del magnetron.Il percorso libero medio dipende dalla pressione, dalla temperatura e dal tipo di gas utilizzato nella camera di sputtering.Le pressioni più basse determinano percorsi liberi medi più lunghi, mentre le pressioni più elevate li riducono a causa dell'aumento della frequenza di collisione.La comprensione di questo parametro aiuta a ottimizzare le condizioni di sputtering per applicazioni specifiche.
Punti chiave spiegati:
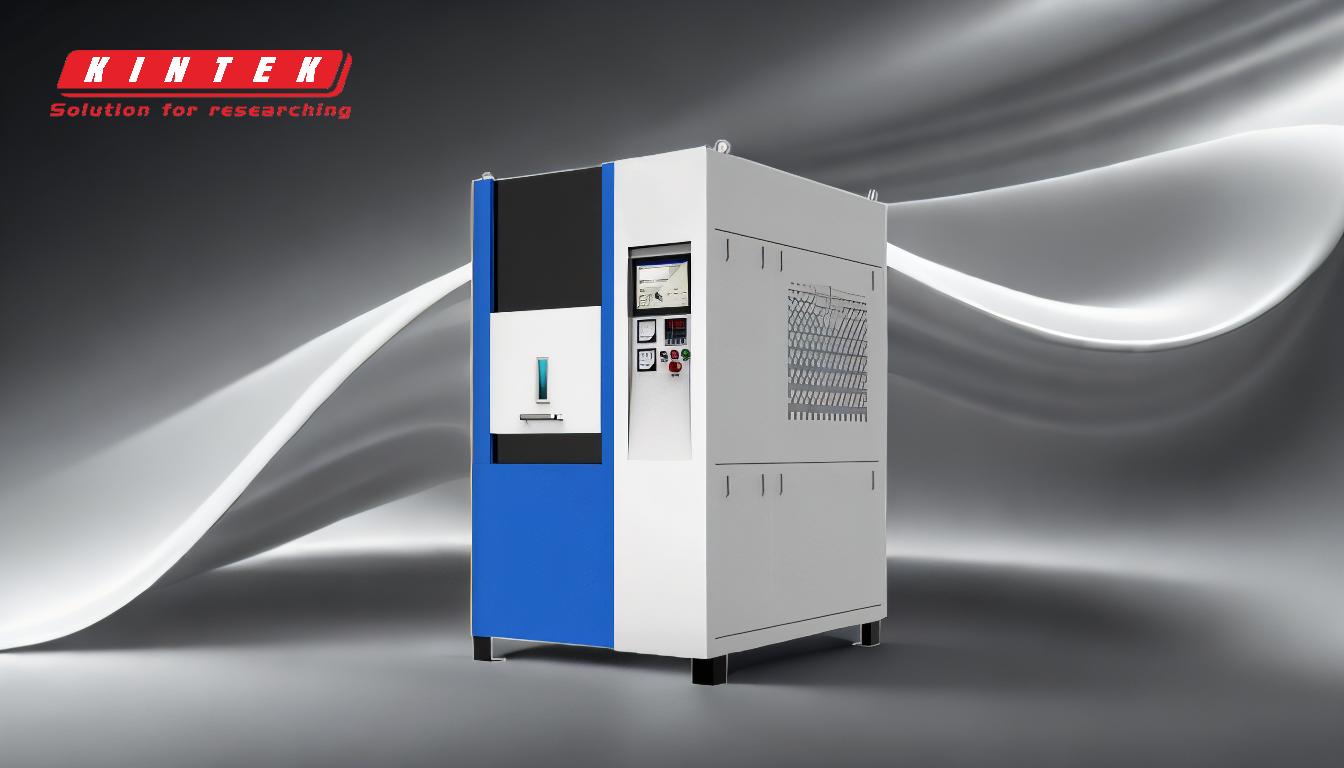
-
Definizione di percorso libero medio:
- Il percorso libero medio è la distanza media percorsa da una particella tra le collisioni successive con altre particelle in un gas o in un plasma.
- Nei magnetron sputtering, questo vale per gli atomi, gli ioni o gli elettroni che si muovono attraverso il gas di sputtering (ad esempio, l'argon).
-
Fattori che influenzano il percorso libero medio:
- Pressione:Le pressioni più basse aumentano il percorso libero medio perché ci sono meno molecole di gas con cui scontrarsi.Al contrario, pressioni più elevate riducono il percorso libero medio a causa di collisioni più frequenti.
- Temperatura:Le temperature più elevate aumentano l'energia cinetica delle particelle, aumentando potenzialmente il percorso libero medio se la pressione rimane costante.
- Tipo di gas:Le dimensioni e la massa delle molecole di gas influenzano la frequenza delle collisioni.Ad esempio, i gas più leggeri come l'elio hanno percorsi liberi medi più lunghi rispetto ai gas più pesanti come l'argon.
-
Rilevanza per i magnetroni sputtering:
- Il percorso libero medio determina la distanza percorsa dalle particelle polverizzate prima di entrare in collisione con le molecole di gas o con le pareti della camera.
- Un percorso libero medio più lungo può portare a tassi di deposizione più elevati e a una migliore uniformità del film, poiché è meno probabile che le particelle si disperdano o perdano energia attraverso le collisioni.
- Al contrario, un percorso libero medio più breve può determinare un maggior numero di collisioni, con conseguente riduzione dell'energia e potenziali difetti nel film depositato.
-
Implicazioni pratiche:
- Sputtering a bassa pressione:Funziona a pressioni intorno a 1-10 mTorr, con conseguente allungamento dei percorsi liberi medi e deposizione efficiente.
- Sputtering ad alta pressione:Utilizzato in applicazioni specifiche, ma può portare a percorsi liberi medi più brevi e a una minore efficienza di deposizione.
- Ottimizzazione:La regolazione della pressione e del tipo di gas può aiutare a bilanciare il percorso libero medio e la qualità della deposizione per materiali e applicazioni specifiche.
-
Calcolo del percorso libero medio:
-
Il percorso libero medio (λ) può essere stimato utilizzando la formula:
- [
- \lambda = \frac{k_B T}{\sqrt{2}\pi d^2 P}
- ]
- dove:
- ( k_B ) è la costante di Boltzmann,
-
Il percorso libero medio (λ) può essere stimato utilizzando la formula:
-
( T ) è la temperatura, ( d ) è il diametro della molecola di gas,
- ( P ) è la pressione. Per il gas argon a temperatura ambiente e a una pressione di 1 mTorr, il percorso libero medio è di circa 6,6 cm.
- Applicazioni e considerazioni:
- Deposizione di film sottili:Un percorso libero medio più lungo è auspicabile per ottenere film uniformi e di alta qualità.
Sputtering reattivo
:Il percorso libero medio influisce sulla cinetica di reazione tra le particelle polverizzate e i gas reattivi.
Design della camera | :La comprensione del percorso libero medio aiuta a progettare le camere di sputtering per ridurre al minimo le collisioni e massimizzare l'efficienza di deposizione. |
---|---|
Considerando questi fattori, gli utenti possono ottimizzare i sistemi magnetronici di sputtering per applicazioni specifiche, garantendo una deposizione di film sottili efficiente e di alta qualità. | Tabella riassuntiva: |
Fattore chiave | Impatto sul percorso libero medio |
La pressione | Una pressione più bassa aumenta il cammino libero medio; una pressione più alta lo diminuisce. |
Temperatura | Una temperatura più elevata può aumentare il percorso libero medio se la pressione rimane costante. |
Tipo di gas | I gas più leggeri (ad esempio, l'elio) hanno percorsi liberi medi più lunghi dei gas più pesanti (ad esempio, l'argon). |
Applicazioni Percorsi liberi medi più lunghi migliorano i tassi di deposizione e l'uniformità del film. Progettazione della camera