I forni a resistenza e a induzione sono entrambi ampiamente utilizzati nei processi industriali di riscaldamento e fusione, ma si differenziano notevolmente per i principi di funzionamento, l'efficienza e le applicazioni.I forni a resistenza si basano su elementi riscaldanti esterni per generare calore, che viene poi trasferito al materiale, mentre i forni a induzione generano calore direttamente all'interno del materiale utilizzando l'induzione elettromagnetica.Questa differenza fondamentale porta a variazioni nell'efficienza energetica, nei livelli di contaminazione e nelle capacità operative.Di seguito, le differenze principali sono spiegate in dettaglio.
Punti chiave spiegati:
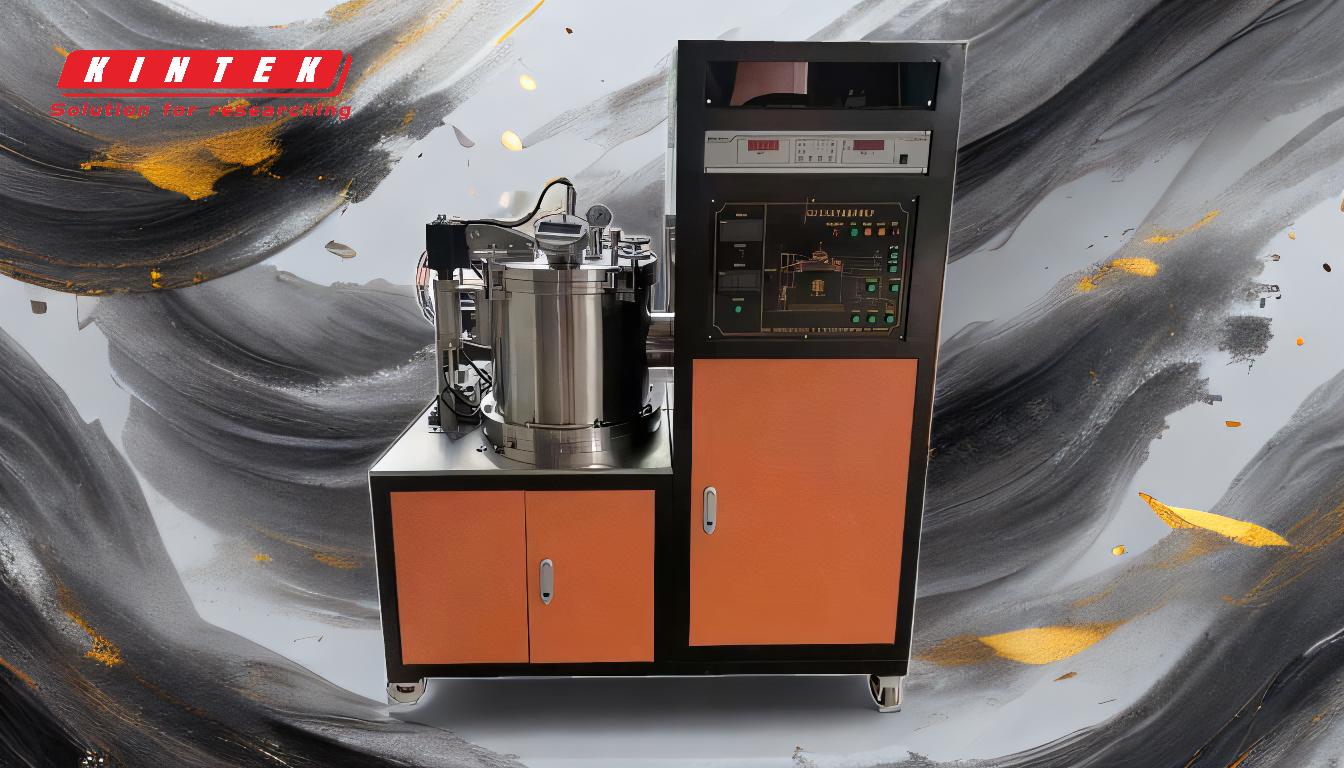
-
Meccanismo di riscaldamento:
-
Forno a resistenza:
- Utilizza elementi di riscaldamento esterni (ad esempio, elementi refrattari o bobine) per generare calore.
- Il calore viene trasferito al materiale per conduzione, convezione o irraggiamento.
- Adatto per processi in cui è richiesto un riscaldamento uniforme, ma la fonte di calore è esterna al materiale.
-
Forno a induzione:
- Genera calore direttamente all'interno del materiale utilizzando l'induzione elettromagnetica.
- La corrente alternata crea un campo magnetico alternato, inducendo correnti parassite nel materiale, che producono calore grazie alla resistenza.
- Garantisce un riscaldamento uniforme e riduce al minimo la contaminazione, poiché non è coinvolta alcuna fonte di calore esterna.
-
Forno a resistenza:
-
Efficienza e consumo energetico:
-
Forno a resistenza:
- Meno efficiente dal punto di vista energetico a causa della perdita di calore durante il trasferimento dalla fonte esterna al materiale.
- Richiede più energia per mantenere alte le temperature, soprattutto nelle operazioni su larga scala.
-
Forno a induzione:
- Più efficiente dal punto di vista energetico, poiché il calore viene generato direttamente all'interno del materiale, riducendo le perdite di calore.
- Raggiunge velocità di riscaldamento più elevate e una maggiore efficienza termica, che la rendono ideale per le applicazioni ad alta temperatura.
-
Forno a resistenza:
-
Temperatura e densità di potenza:
-
Forno a resistenza:
- Funziona a densità di potenza inferiori rispetto ai forni a induzione.
- Adatto per applicazioni che richiedono temperature moderate (ad esempio, ricottura, rinvenimento).
-
Forno a induzione:
- In grado di operare a temperature e densità di potenza più elevate.
- Può raggiungere temperature di forgiatura fino a 1250°C e temperature di fusione fino a 1650°C, rendendolo adatto alla fusione e alla lavorazione ad alta temperatura.
-
Forno a resistenza:
-
Contaminazione e purezza:
-
Forno a resistenza:
- Rischio di contaminazione più elevato a causa dell'uso di elementi riscaldanti esterni, che possono introdurre impurità.
- Richiede un'attenta selezione degli elementi riscaldanti e dei rivestimenti del forno per ridurre al minimo la contaminazione.
-
Forno a induzione:
- Contaminazione minima poiché il calore è generato all'interno del materiale stesso.
- Ideale per le applicazioni che richiedono materiali di elevata purezza, come ad esempio nell'industria dei semiconduttori o in quella aerospaziale.
-
Forno a resistenza:
-
Controllo e automazione:
-
Forno a resistenza:
- In genere si basa su sistemi di controllo manuali o semi-automatici.
- Limitato dalla complessità di mantenere un riscaldamento uniforme su grandi volumi.
-
Forno a induzione:
- Dotato di sistemi di controllo avanzati, tra cui la scansione automatica della frequenza, il controllo costante della potenza e meccanismi di protezione completi.
- Offre un controllo preciso della temperatura e un funzionamento regolare, riducendo la necessità di interventi manuali.
-
Forno a resistenza:
-
Applicazioni:
-
Forno a resistenza:
- Comunemente utilizzato per processi di trattamento termico come ricottura, tempra e rinvenimento.
- Adatto per la lavorazione in lotti di materiali che non richiedono temperature estremamente elevate.
-
Forno a induzione:
- Ampiamente utilizzato nelle applicazioni di fusione e forgiatura, in particolare per metalli come acciaio, alluminio e rame.
- È preferito per i processi continui e le operazioni ad alta temperatura in cui l'efficienza e la purezza sono fondamentali.
-
Forno a resistenza:
-
Progettazione e manutenzione:
-
Forno a resistenza:
- Design più semplice con un minor numero di componenti, che rende la manutenzione relativamente semplice.
- Tuttavia, gli elementi riscaldanti possono richiedere una sostituzione frequente a causa dell'usura.
-
Forno a induzione:
- Progettazione più complessa con componenti come induttori, condensatori e sistemi di controllo.
- Richiede considerazioni accurate sul progetto, come la disposizione dei gioghi e la spaziatura degli induttori, per garantire prestazioni ottimali.
- La manutenzione è più semplice per i modelli avanzati con circuiti integrati e componenti modulari.
-
Forno a resistenza:
-
Idoneità del materiale:
-
Forno a resistenza:
- Adatto a un'ampia gamma di materiali, compresi quelli non metallici e magnetici.
- Limitato dalla capacità del materiale di assorbire calore da una fonte esterna.
-
Forno a induzione:
- È il più adatto per i materiali conduttivi, in particolare per i metalli.
- Le difficoltà sorgono con i materiali non magnetici come l'alluminio, che richiedono un design speciale dell'induttore per garantire un riscaldamento efficiente.
-
Forno a resistenza:
In sintesi, i forni a resistenza e a induzione hanno scopi diversi in base ai meccanismi di riscaldamento, all'efficienza e alle applicazioni.I forni a resistenza sono più adatti ai processi a temperatura moderata e alle operazioni in batch, mentre i forni a induzione eccellono nei processi ad alta temperatura, ad alta purezza e continui.La scelta tra i due dipende dai requisiti specifici dell'applicazione, tra cui la temperatura, il tipo di materiale e l'efficienza desiderata.
Tabella riassuntiva:
Aspetto | Forno a resistenza | Forno a induzione |
---|---|---|
Meccanismo di riscaldamento | Gli elementi riscaldanti esterni trasferiscono il calore per conduzione, convezione o irraggiamento. | Il calore viene generato direttamente all'interno del materiale mediante induzione elettromagnetica. |
Efficienza | Meno efficiente dal punto di vista energetico a causa della perdita di calore durante il trasferimento. | Più efficiente dal punto di vista energetico, grazie alla velocità di riscaldamento e alla riduzione delle perdite di calore. |
Intervallo di temperatura | Adatto a temperature moderate (ad esempio, ricottura, rinvenimento). | In grado di raggiungere temperature elevate (fino a 1650°C) per la fusione e la forgiatura. |
Rischio di contaminazione | Rischio più elevato a causa degli elementi riscaldanti esterni. | Contaminazione minima, ideale per applicazioni ad alta purezza. |
Sistemi di controllo | Sistemi di controllo manuali o semi-automatici. | Automazione avanzata con controllo preciso della temperatura e meccanismi di protezione. |
Applicazioni | Processi di trattamento termico (ad esempio, ricottura, tempra). | Fusione, forgiatura e operazioni ad alta temperatura per metalli come acciaio e alluminio. |
Design e manutenzione | Design più semplice, ma gli elementi riscaldanti possono richiedere una sostituzione frequente. | Design complesso con manutenzione più semplice per i modelli avanzati. |
Idoneità del materiale | Adatto per materiali non metallici e magnetici. | Ideale per i materiali conduttivi, in particolare i metalli. |
Avete bisogno di aiuto per scegliere il forno giusto per la vostra applicazione? Contattate i nostri esperti oggi stesso per una consulenza personalizzata!