Il processo di ricottura, pur essendo ampiamente utilizzato in metallurgia e scienza dei materiali per migliorare le proprietà di metalli e leghe, presenta diverse limitazioni. Tra questi, i vincoli legati al controllo della temperatura, i requisiti di tempo, le sfide specifiche del materiale, il consumo di energia e il potenziale di ossidazione superficiale. Inoltre, il processo potrebbe non raggiungere sempre le proprietà desiderate del materiale a causa di complessità microstrutturali o di una selezione impropria dei parametri. La comprensione di questi limiti è fondamentale per ottimizzare il processo di ricottura e garantire i risultati desiderati per applicazioni specifiche.
Punti chiave spiegati:
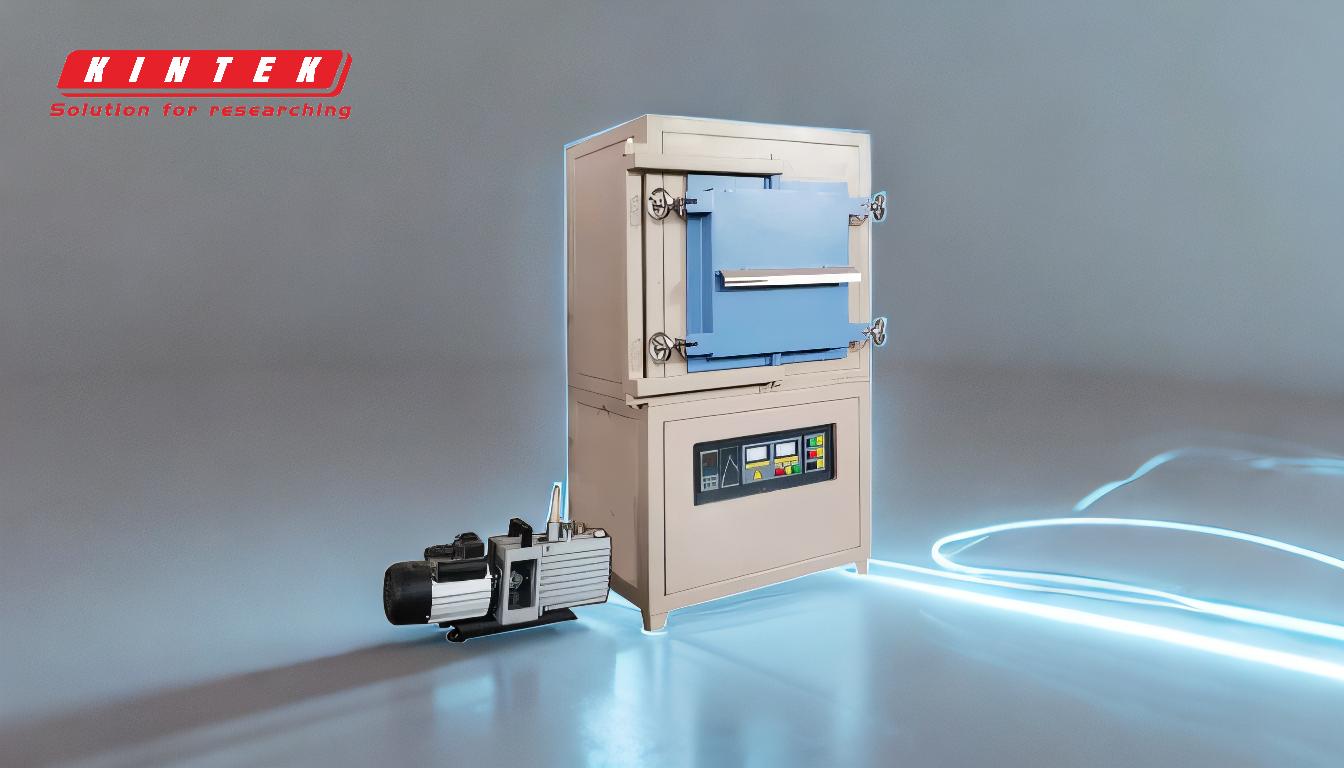
-
Le sfide del controllo della temperatura:
- Requisiti di precisione: La ricottura richiede un controllo preciso della temperatura per ottenere le proprietà desiderate del materiale. Lievi deviazioni possono portare a una ricristallizzazione incompleta o a problemi di crescita dei grani.
- Limitazioni delle apparecchiature: Non tutti i forni sono in grado di mantenere temperature uniformi su pezzi grandi o complessi, con conseguenti risultati incoerenti.
- Sensibilità del materiale: Alcuni materiali, come gli acciai ad alto tenore di carbonio o alcune leghe, presentano intervalli di temperatura ristretti per una ricottura efficace, rendendo il processo più impegnativo.
-
Vincoli temporali:
- Tempi di elaborazione lunghi: La ricottura spesso richiede cicli di riscaldamento e raffreddamento prolungati, che possono richiedere tempo e risultare inefficienti per la produzione di grandi volumi.
- Sensibilità della velocità di raffreddamento: Per alcuni materiali è necessario un raffreddamento lento per evitare tensioni interne, ma questo può allungare ulteriormente i tempi di lavorazione.
-
Limitazioni specifiche del materiale:
- Microstrutture non uniformi: I materiali con composizioni eterogenee o con storie di lavorazione precedenti possono non rispondere in modo uniforme alla ricottura.
- Problemi di crescita dei cereali: La sovralaminazione può portare a una crescita eccessiva dei grani, riducendo la resistenza e la tenacità del materiale.
- Applicabilità limitata: Alcuni materiali, come i materiali compositi non metallici o le ceramiche, non traggono un beneficio significativo dalla ricottura.
-
Consumo di energia:
- Elevato fabbisogno energetico: Il mantenimento di temperature elevate per periodi prolungati consuma molta energia, rendendo il processo costoso e meno rispettoso dell'ambiente.
- Inefficienza nell'elaborazione in lotti: La ricottura a lotti, pur essendo comune, è meno efficiente dal punto di vista energetico rispetto ai processi di ricottura continua.
-
Ossidazione superficiale e decarburazione:
- Rischi di ossidazione: L'esposizione a temperature elevate in presenza di ossigeno può portare all'ossidazione della superficie, degradando la qualità del materiale.
- Decarburazione: Negli acciai, un riscaldamento prolungato può causare la perdita di carbonio dalla superficie, riducendo la durezza e la resistenza all'usura.
-
Complessità del processo e requisiti di competenza:
- Ottimizzazione dei parametri: La scelta della temperatura di ricottura, del tempo e della velocità di raffreddamento corretti richiede esperienza e sperimentazione.
- Trattamenti post-ricottura: Per ottenere le proprietà desiderate possono essere necessari ulteriori processi, come la tempra o il rinvenimento, che aggiungono complessità.
-
Vincoli economici e pratici:
- Costo dell'attrezzatura: I forni di ricottura e i sistemi di controllo della temperatura di alta qualità possono essere costosi da acquistare e mantenere.
- Requisiti di spazio: Le operazioni di ricottura su larga scala richiedono uno spazio significativo, che potrebbe non essere fattibile per le strutture più piccole.
-
Risultati incoerenti:
- Variabilità nella risposta del materiale: Anche con parametri controllati, le variazioni nella composizione del materiale o nella lavorazione precedente possono portare a risultati incoerenti.
- Errore umano: Il controllo manuale dei processi di ricottura aumenta il rischio di errori, come l'impostazione errata della temperatura o della tempistica.
-
Miglioramento limitato per alcune proprietà:
- Scambio tra durezza e resistenza: La ricottura spesso riduce la durezza e la resistenza per migliorare la duttilità, il che può non essere auspicabile per tutte le applicazioni.
- Impatto limitato sui difetti: Sebbene la ricottura possa ridurre le sollecitazioni interne, potrebbe non eliminare tutti i difetti, come vuoti o inclusioni.
-
Problemi ambientali e di sicurezza:
- Calore ed emissioni: I processi ad alta temperatura generano calore ed emissioni che richiedono una ventilazione adeguata e misure di sicurezza.
- Sicurezza dei lavoratori: La manipolazione di materiali caldi e l'utilizzo di apparecchiature ad alta temperatura comportano rischi per la sicurezza.
Comprendendo questi limiti, i produttori e gli ingegneri possono progettare meglio i processi di ricottura, selezionare i materiali appropriati e implementare trattamenti complementari per ottenere risultati ottimali.
Tabella riassuntiva:
Categoria di limitazione | Sfide principali |
---|---|
Controllo della temperatura | Requisiti di precisione, limiti delle apparecchiature, sensibilità dei materiali |
Vincoli temporali | Tempi di lavorazione lunghi, sensibilità alla velocità di raffreddamento |
Problemi specifici del materiale | Microstrutture non uniformi, crescita dei grani, applicabilità limitata |
Consumo di energia | Elevato fabbisogno energetico, inefficienza nella lavorazione in batch |
Ossidazione superficiale | Rischi di ossidazione, decarburazione negli acciai |
Complessità del processo | Ottimizzazione dei parametri, trattamenti di post-cottura |
Vincoli economici | Costo delle attrezzature, requisiti di spazio |
Risultati incoerenti | Variabilità nella risposta dei materiali, errore umano |
Miglioramento limitato della proprietà | Compromessi tra durezza e resistenza, eliminazione limitata dei difetti |
Preoccupazioni ambientali | Calore ed emissioni, rischi per la sicurezza dei lavoratori |
Avete bisogno di aiuto per ottimizzare il vostro processo di ricottura? Contattate i nostri esperti oggi stesso per soluzioni su misura!