Introduzione allo sputtering di magnetron
Panoramica del processo di sputtering con magnetron
Lo sputtering magnetronico è una sofisticata tecnologia di deposizione fisica da vapore (PVD) che prevede la deposizione di un film sottile su un substrato. Questo processo viene condotto all'interno di una camera a vuoto, dove un materiale target viene sottoposto a un plasma ad alta energia. Il plasma, generato dalla combinazione di un gas di sputtering e di un forte campo magnetico vicino al bersaglio, provoca l'espulsione di atomi o molecole del materiale bersaglio e il successivo deposito sul substrato.
Il campo magnetico svolge un ruolo cruciale nello sputtering magnetronico, poiché confina il plasma in una regione vicina al bersaglio. Questo confinamento assicura che gli ioni energetici all'interno del plasma interagiscano principalmente con il materiale bersaglio, riducendo al minimo i danni al film sottile in crescita sul substrato. Il processo inizia con l'evacuazione della camera per ottenere condizioni di alto vuoto, che riduce le pressioni dei gas di fondo e i potenziali contaminanti. Successivamente, il gas di sputtering viene introdotto nella camera e la pressione viene regolata al milliTorr mediante un sistema di controllo di precisione.
In sostanza, lo sputtering magnetronico è un processo di deposizione al plasma in cui gli ioni colpiscono il bersaglio, provocando l'espulsione di atomi. Questi atomi viaggiano poi attraverso l'ambiente del vuoto e si incorporano nel film in crescita sul substrato. L'intricata interazione tra il campo magnetico, il plasma e le condizioni di vuoto garantisce la formazione precisa ed efficiente di film sottili, rendendo lo sputtering magnetronico una tecnica versatile e ampiamente utilizzata in varie applicazioni industriali.
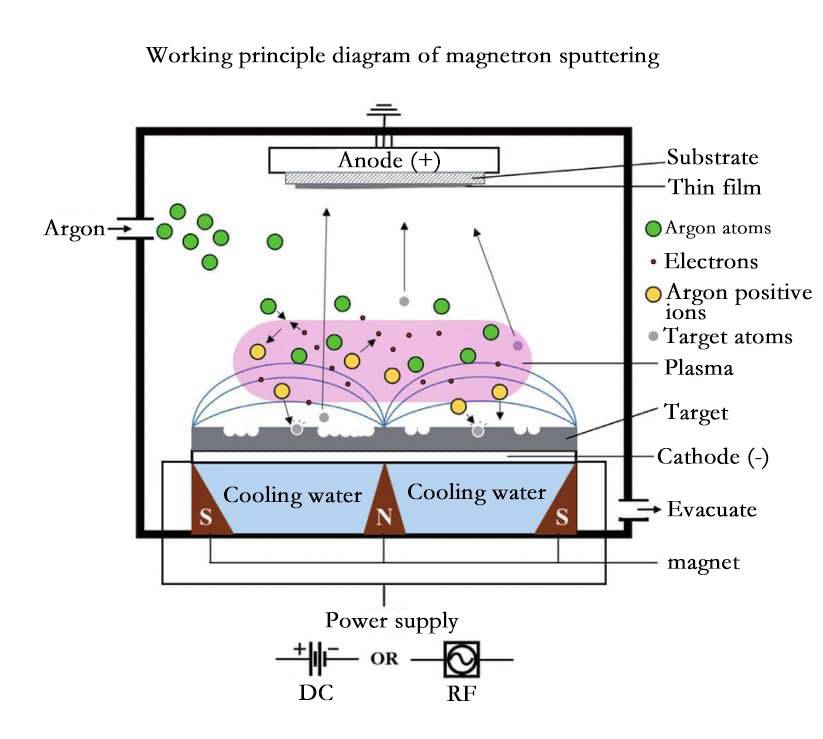
Cause della scintillazione del materiale target
Ossidazione della superficie del materiale target
L'interazione tra il materiale target e le molecole di ossigeno all'interno della camera a vuoto è un fattore critico nel processo di sputtering. Quando il materiale target è esposto all'ossigeno, può subire una reazione chimica che porta alla formazione di ossidi sulla sua superficie. Questi ossidi, inizialmente stabili, possono successivamente decomporsi nelle condizioni di alta energia del processo di sputtering.
La decomposizione di questi ossidi rilascia gas che possono accumularsi all'interno della camera da vuoto. Questo accumulo può portare a variazioni di pressione localizzate e, in casi estremi, causare scintille. Le scintille sono il risultato dell'improvviso rilascio di energia dal processo di decomposizione, che può disturbare l'ambiente di sputtering e potenzialmente danneggiare l'apparecchiatura.
Per ridurre questo problema, è essenziale controllare l'atmosfera all'interno della camera da vuoto. Ciò comporta il mantenimento di una bassa concentrazione di gas reattivi come l'ossigeno, assicurando che l'ambiente rimanga stabile e favorevole al processo di sputtering. Inoltre, la pulizia regolare della superficie del materiale target può prevenire l'accumulo di ossidi, riducendo così il rischio di scintille.
Difetti superficiali sul materiale target
I difetti superficiali del materiale di destinazione, come piccole crepe o fori, possono avere un impatto significativo sul processo di sputtering. Queste imperfezioni agiscono come punti di debolezza localizzati, dove si concentra la scarica elettrica durante lo sputtering. Questa concentrazione di scarica può portare alla formazione di forti archi locali, che sono scariche elettriche intense che possono incendiare il materiale di destinazione.
La presenza di tali difetti è particolarmente problematica perché interrompe la distribuzione uniforme del processo di sputtering. Invece di ottenere un rivestimento liscio e uniforme, i difetti fanno sì che l'energia si concentri in aree specifiche, provocando un surriscaldamento localizzato e una potenziale accensione. Questo non solo compromette la qualità del rivestimento, ma rappresenta anche un rischio per la sicurezza dell'apparecchiatura e degli operatori.
Per ridurre il rischio di scintille dovute a difetti superficiali, è fondamentale ispezionare e preparare accuratamente il materiale di destinazione prima di iniziare il processo di sputtering. Ciò include l'identificazione e la correzione di eventuali imperfezioni superficiali, assicurando che il materiale sia in condizioni ottimali per l'applicazione del rivestimento.
Condizioni di sputtering inadeguate
Condizioni di sputtering inadeguate possono contribuire in modo significativo all'accensione del bersaglio durante il processo di sputtering magnetronico. Queste condizioni spesso derivano da una combinazione di impostazioni di potenza elevate o basse durante il riscaldamento del target e di campi magnetici non uniformi. Le impostazioni di potenza elevate possono causare un riscaldamento eccessivo, con conseguente rapida vaporizzazione e successiva accensione del materiale del target. Al contrario, le impostazioni di bassa potenza possono provocare un riscaldamento insufficiente, causando surriscaldamento localizzato e scintille a causa della distribuzione non uniforme dell'energia.
Inoltre, un campo magnetico non uniforme può disturbare la distribuzione uniforme del plasma all'interno della camera a vuoto, provocando scariche concentrate in punti specifici della superficie del bersaglio. Questa concentrazione di energia può creare forti archi locali, inclini all'accensione. La tabella seguente riassume gli effetti di queste condizioni improprie:
Condizione | Effetto |
---|---|
Impostazione di potenza elevata | Riscaldamento eccessivo, vaporizzazione rapida e accensione del bersaglio |
Impostazione di bassa potenza | Riscaldamento insufficiente, surriscaldamento localizzato e formazione di scintille |
Campo magnetico non uniforme | Distribuzione del plasma disturbata, scariche concentrate e accensioni. |
Per risolvere questi problemi è necessario un approccio meticoloso all'impostazione e al mantenimento dei parametri di sputtering, assicurando che la potenza e il campo magnetico siano stabili e distribuiti in modo uniforme.
Soluzioni per prevenire l'accensione del target
Assicurare la pulizia della superficie del target
La pulizia della superficie del target prima del processo di sputtering è una fase cruciale per prevenire l'insorgere di scintille. Questa procedura prevede la rimozione meticolosa di qualsiasi sporco, contaminante e in particolare degli ossidi che possono essersi formati sulla superficie del materiale del target. Gli ossidi sono particolarmente problematici perché possono decomporsi nelle condizioni di alta energia dello sputtering, rilasciando gas che possono provocare archi localizzati e accensioni.
Per garantire una pulizia accurata, si possono utilizzare diversi metodi:
- Pulizia meccanica: Utilizzo di spazzole o materiali abrasivi per rimuovere fisicamente i contaminanti della superficie.
- Pulizia chimica: Immergere l'obiettivo in solventi o acidi specifici che possono dissolvere ossidi e altre impurità.
- Pulizia a ultrasuoni: Utilizza onde ultrasoniche per staccare e rimuovere le particelle incastrate nella superficie.
- Pulizia a fascio ionico: Bombardamento della superficie del bersaglio con un fascio di ioni per rimuovere i contaminanti a livello atomico.
La scelta del metodo di pulizia dipende dalla natura dei contaminanti e dai requisiti specifici del processo di sputtering. Indipendentemente dal metodo utilizzato, l'obiettivo è ottenere una superficie immacolata, priva di sostanze che potrebbero interferire con il processo di sputtering o causare scintille indesiderate. Questa preparazione meticolosa garantisce che il materiale di destinazione sia in condizioni ottimali per la deposizione di un film sottile di alta qualità.
Controllo dell'atmosfera della camera a vuoto
Mantenere l'atmosfera entro un intervallo controllabile è fondamentale per evitare che la concentrazione di ossigeno e altri gas raggiunga un livello infiammabile. Ciò comporta la creazione e il mantenimento di un'atmosfera modificata all'interno della camera da vuoto, che può ridurre significativamente il rischio di scintille del materiale target durante lo sputtering magnetronico.
Per ottenere questo risultato, è essenziale un recipiente sigillato. Può trattarsi di un tubo di lavoro con guarnizioni terminali specializzate, progettato per l'uso con forni a tubo, o di una storta comunemente usata nei forni a camera. Questi recipienti aiutano a isolare l'ambiente interno dalle influenze esterne, consentendo un controllo preciso delle condizioni atmosferiche.
Il processo di evacuazione di un recipiente riduce il numero di atomi e molecole al suo interno. Tuttavia, ottenere un vuoto perfetto è praticamente impossibile; anche in un vuoto inferiore a 10-7 mbar, ci sono ancora circa 109 particelle per centimetro cubo. Questa presenza residua di gas deve essere gestita con attenzione per evitare l'accumulo di gas infiammabili.
KINTEK offre una gamma di pacchetti di gas standard e di attrezzature associate progettate per contribuire alla creazione e al mantenimento di queste atmosfere modificate. Questi prodotti non sono solo versatili ma anche adattabili, consentendo una maggiore flessibilità operativa. Ad esempio, le apparecchiature e gli accessori opzionali per le atmosfere modificate consentono di utilizzare gli stessi prodotti per più applicazioni che prevedono l'utilizzo di gas, livelli di vuoto o addirittura nessuna atmosfera modificata.
Controllando meticolosamente l'atmosfera della camera da vuoto, è possibile ridurre significativamente la probabilità di accensione del materiale target durante lo sputtering magnetronico, garantendo un processo di rivestimento più sicuro ed efficiente.
Impostare condizioni di sputtering ragionevoli
La regolazione delle condizioni di sputtering è fondamentale per prevenire l'accensione e garantire prestazioni ottimali del processo di sputtering magnetronico. Le impostazioni specifiche devono essere meticolosamente adattate alle caratteristiche del materiale di destinazione e alle specifiche dell'apparecchiatura. Ciò comporta la regolazione fine di parametri quali i livelli di potenza, le configurazioni del campo magnetico e le pressioni della camera a vuoto.
Per esempio,i livelli di potenza devono essere attentamente calibrati per adattarsi alle proprietà termiche del materiale target. Una potenza eccessiva può causare surriscaldamento, con conseguenti archi localizzati e accensione, mentre una potenza insufficiente potrebbe non vaporizzare efficacemente il materiale, con conseguente scarsa qualità del rivestimento. Allo stesso modo,configurazioni del campo magnetico devono essere bilanciate per creare una distribuzione uniforme del plasma, evitando scariche concentrate che possono innescare scintille.
Inoltre, il mantenimento di un'adeguatapressione della camera a vuoto è essenziale. Una pressione troppo elevata può consentire ai gas residui di interagire con il materiale bersaglio, causando reazioni indesiderate e potenziali accensioni. Al contrario, una pressione troppo bassa può portare a una formazione inefficiente del plasma, compromettendo il processo di sputtering.
Regolando sistematicamente queste condizioni, gli operatori possono ridurre significativamente il rischio di accensione del materiale target, garantendo un processo di sputtering stabile ed efficiente.
Ispezione regolare delle apparecchiature
L'ispezione regolare delle apparecchiature è una pratica fondamentale nel contesto dello sputtering magnetronico per garantire la longevità e l'efficienza del processo. Questa manutenzione di routine comporta un esame approfondito di tutti i componenti, dalla camera da vuoto alle unità di alimentazione, per identificare eventuali segni di usura o malfunzionamento. Rispettando un rigoroso programma di ispezioni, gli operatori possono individuare e risolvere i potenziali problemi prima che si trasformino in problemi più significativi.
Uno degli obiettivi principali di queste ispezioni è verificare che tutte le parti meccaniche funzionino correttamente. Ciò include il controllo di eventuali connessioni allentate, componenti disallineati o segni di danni fisici. Inoltre, i sistemi elettrici devono essere esaminati per garantire che funzionino entro parametri sicuri, evitando potenziali cortocircuiti o sbalzi di tensione che potrebbero causare guasti alle apparecchiature o, peggio, rischi per la sicurezza.
Inoltre, le ispezioni regolari contribuiscono a mantenere l'integrità dell'ambiente del vuoto all'interno della camera. Eventuali perdite o degrado delle guarnizioni del vuoto possono compromettere il processo di sputtering, portando a una deposizione non ottimale del film e a potenziali scintille del materiale target. Identificando e correggendo tempestivamente tali problemi, gli operatori possono mantenere un'atmosfera stabile e controllata, necessaria per applicazioni di rivestimento di alta qualità.
In sintesi, l'ispezione regolare delle apparecchiature non è solo una misura preventiva, ma un aspetto essenziale per garantire il funzionamento continuo e sicuro delle apparecchiature di sputtering magnetronico. Comprende una valutazione completa dei componenti meccanici ed elettrici, assicurando che l'intero sistema funzioni come previsto, riducendo così al minimo il rischio di scintille del materiale target e altri problemi correlati.
CONTATTATECI PER UNA CONSULENZA GRATUITA
I prodotti e i servizi di KINTEK LAB SOLUTION sono stati riconosciuti da clienti di tutto il mondo. Il nostro personale sarà lieto di assistervi per qualsiasi richiesta. Contattateci per una consulenza gratuita e parlate con uno specialista del prodotto per trovare la soluzione più adatta alle vostre esigenze applicative!