La deposizione fisica da vapore (PVD) è un processo critico nella produzione moderna, in particolare per la creazione di film sottili e rivestimenti su substrati. La conduzione della PVD in un ambiente sotto vuoto è essenziale per diversi motivi, tra cui la riduzione della contaminazione, l'aumento del percorso libero medio delle particelle e il controllo preciso del processo di deposizione. Il vuoto riduce al minimo la presenza di atomi e molecole indesiderate, garantendo un ambiente pulito e controllato necessario per rivestimenti di alta qualità. Inoltre, consente un trasferimento e un'adesione efficienti dei materiali, fondamentali per le applicazioni nella microelettronica, nell'ottica e in altre tecnologie avanzate.
Punti chiave spiegati:
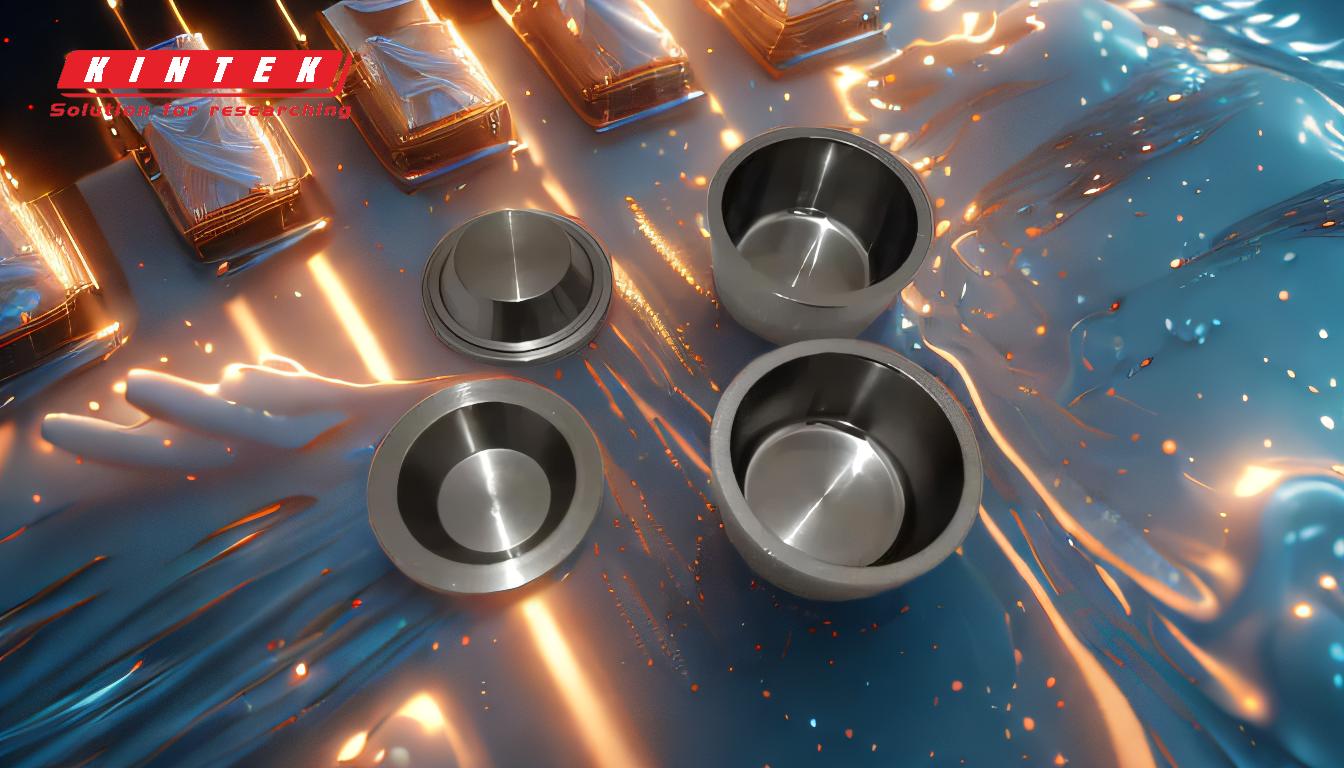
-
Riduzione della densità delle particelle e aumento del cammino libero medio:
- In un ambiente sottovuoto, la densità delle molecole di gas si riduce notevolmente. Questa riduzione aumenta il percorso libero medio delle particelle, ovvero la distanza media percorsa da una particella prima di entrare in collisione con un'altra particella. Un percorso libero medio più lungo garantisce che il materiale vaporizzato possa raggiungere direttamente il substrato senza essere disperso o rallentato dalle collisioni con le molecole di gas. Questo percorso diretto è fondamentale per ottenere rivestimenti uniformi e di alta qualità.
-
Riduzione al minimo della contaminazione:
- Un ambiente sottovuoto riduce la presenza di atomi e molecole indesiderate, come ossigeno, azoto e vapore acqueo, che possono contaminare il film depositato. I contaminanti possono degradare la qualità del rivestimento, causando difetti, riduzione dell'adesione e compromissione delle prestazioni. Mantenendo un vuoto spinto, il processo garantisce un ambiente più pulito e controllato, particolarmente importante per applicazioni come la produzione di microchip, dove anche piccoli contaminanti possono causare problemi significativi.
-
Composizione controllata di gas e vapori:
- Il vuoto consente un controllo preciso della composizione dei gas e dei vapori all'interno della camera di lavorazione. Questo controllo è essenziale per personalizzare le proprietà del film depositato, come lo spessore, l'uniformità e la composizione chimica. Regolando la pressione e la composizione dei gas, i produttori possono ottenere le proprietà specifiche dei materiali richieste per diverse applicazioni, come rivestimenti ottici, strati resistenti all'usura o film conduttivi.
-
Alto tasso di evaporazione termica:
- Nel vuoto, il tasso di evaporazione termica dei materiali è significativamente più alto rispetto alle condizioni atmosferiche. Questo perché la pressione ridotta abbassa il punto di ebollizione dei materiali, consentendo loro di vaporizzare a temperature più basse. Un'elevata velocità di evaporazione garantisce un trasferimento e una deposizione efficienti del materiale, fondamentali per ottenere lo spessore e la qualità del film desiderati in un tempo ragionevole.
-
Maggiore adesione del materiale:
- L'assenza di aria o altri fluidi in un ambiente sottovuoto consente al materiale vaporizzato di raggiungere il substrato con maggiore energia. Questa maggiore energia migliora l'adesione del materiale al substrato, dando vita a un rivestimento più resistente e duraturo. Una migliore adesione è particolarmente importante per le applicazioni in cui il rivestimento è sottoposto a sollecitazioni meccaniche, cicli termici o ambienti corrosivi.
-
Processo di deposizione ripetibile e controllato:
- Un ambiente sottovuoto offre un processo stabile e ripetibile, essenziale per le applicazioni industriali. Mantenendo condizioni di pressione e temperatura costanti, i produttori possono ottenere rivestimenti uniformi con proprietà prevedibili. Questa ripetibilità è fondamentale per la produzione di massa, dove la coerenza e il controllo della qualità sono fondamentali.
-
Ambiente al plasma a bassa pressione:
- Il vuoto facilita la creazione di un ambiente di plasma a bassa pressione, spesso utilizzato nei processi PVD come lo sputtering. Il plasma aumenta la ionizzazione del materiale vaporizzato, migliorando l'energia e la direzionalità delle particelle che si depositano sul substrato. Ciò si traduce in una migliore densità del film, adesione e qualità complessiva.
-
Requisiti specifici dell'applicazione:
- Alcune applicazioni, come la produzione di microchip, CD e DVD, richiedono ambienti estremamente puliti e controllati. Un vuoto spinto garantisce la rimozione anche delle particelle più piccole, evitando difetti che potrebbero compromettere la funzionalità del prodotto finale. Questo livello di pulizia è irraggiungibile in condizioni atmosferiche.
In sintesi, la conduzione della PVD in un ambiente sotto vuoto è essenziale per ottenere rivestimenti di alta qualità, uniformi e privi di contaminazione. Il vuoto fornisce le condizioni necessarie per un trasferimento efficiente del materiale, una deposizione controllata e una maggiore adesione, rendendolo indispensabile per un'ampia gamma di applicazioni industriali e tecnologiche.
Tabella riassuntiva:
Vantaggi principali | Descrizione |
---|---|
Contaminazione ridotta | Riduce al minimo gli atomi/molecole indesiderate, garantendo rivestimenti più puliti e di qualità superiore. |
Aumento del percorso libero medio | Migliora la distanza di spostamento delle particelle per una deposizione uniforme e precisa. |
Composizione del gas controllato | Consente di personalizzare le proprietà del film, come spessore, uniformità e composizione chimica. |
Alto tasso di evaporazione termica | Consente un trasferimento efficiente del materiale e una deposizione più rapida. |
Adesione migliorata | Migliora la resistenza e la durata del rivestimento per le applicazioni più difficili. |
Processo ripetibile | Assicura risultati coerenti e prevedibili per la produzione di massa. |
Ambiente al plasma a bassa pressione | Aumenta la densità e la qualità della pellicola grazie a una maggiore ionizzazione. |
Pulizia specifica per l'applicazione | Soddisfa i severi requisiti di settori come la microelettronica e l'ottica. |
Avete bisogno di una soluzione PVD sotto vuoto per le vostre esigenze di produzione? Contattateci oggi stesso per saperne di più!