Il processo di sinterizzazione tradizionale è un metodo di trattamento termico utilizzato per fondere materiali, come la zirconia, in una massa solida senza fonderli. Questo processo prevede il riscaldamento del materiale ad alta temperatura, consentendo alle particelle di legarsi attraverso la densificazione e la crescita del collo intergranulare, che riduce la porosità e aumenta la densità. Il risultato è un prodotto finale forte e denso, con proprietà meccaniche migliorate. A forno di sinterizzazione dell'ossido di zirconio è essenziale per questo processo, in quanto fornisce un controllo preciso della temperatura, una distribuzione uniforme del calore e un'efficiente circolazione dell'aria per ottenere le proprietà desiderate dell'ossido di zirconio sinterizzato. Il processo comprende tipicamente le fasi di riscaldamento, sinterizzazione e raffreddamento, per garantire che il materiale raggiunga la durezza e l'integrità strutturale finali.
Punti chiave spiegati:
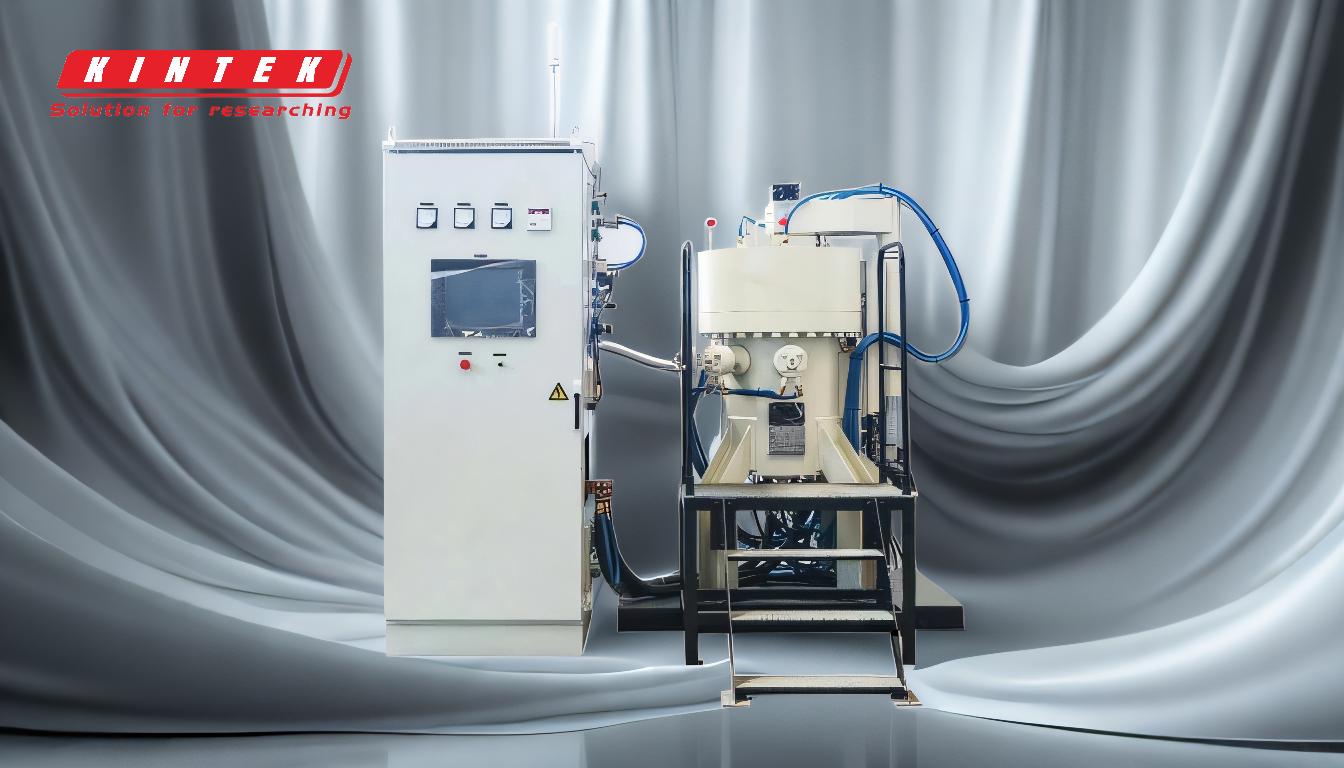
-
Definizione di sinterizzazione tradizionale:
- La sinterizzazione tradizionale è un processo in cui i materiali, come l'ossido di zirconio, vengono fusi insieme con il calore senza raggiungere lo stato liquido. Questo metodo si basa sul trattamento termico e talvolta sulla pressurizzazione per ottenere la densificazione e la crescita del collo intergranulare, che migliora l'integrità strutturale del prodotto finale.
-
Fasi del processo di sinterizzazione:
- Fase di riscaldamento: Il materiale viene gradualmente riscaldato a una temperatura elevata, consentendo al calore di trasferirsi dalla superficie al nucleo.
- Fase di sinterizzazione: Alla temperatura desiderata, le particelle si legano attraverso la densificazione e la crescita del collo intergranulare, riducendo la porosità e aumentando la densità.
- Fase di raffreddamento: Il materiale viene raffreddato lentamente a temperatura ambiente, garantendo il mantenimento della resistenza e della densità.
-
Ruolo di un forno per la sinterizzazione della zirconia:
-
A
forno di sinterizzazione della zirconia
è progettato specificamente per gestire il processo di sinterizzazione della zirconia. Le caratteristiche principali includono:
- Controllo della temperatura ad alta precisione (ad esempio, sistema di controllo intelligente della temperatura PID con precisione di ±1℃).
- Elementi di riscaldamento avanzati per una distribuzione uniforme del calore.
- Circolazione dell'aria efficiente per mantenere livelli ottimali di ossigeno e ottenere il colore e la finitura superficiale desiderati.
-
A
forno di sinterizzazione della zirconia
è progettato specificamente per gestire il processo di sinterizzazione della zirconia. Le caratteristiche principali includono:
-
Vantaggi della sinterizzazione della zirconia:
- Migliore resistenza meccanica: La sinterizzazione riduce la porosità e aumenta la densità, dando vita a un prodotto finale di durezza e durata superiori.
- Miglioramento della finitura superficiale: Il processo garantisce una superficie liscia e uniforme, fondamentale per applicazioni come i restauri dentali.
- Efficienza: I moderni forni di sinterizzazione, come quelli utilizzati per la zirconia, possono completare il processo in soli 65 minuti, comprese le fasi di riscaldamento, sinterizzazione e raffreddamento.
-
Caratteristiche avanzate dei moderni forni di sinterizzazione:
- Programmi di sinterizzazione rapida: Alcuni forni offrono cicli di sinterizzazione rapidi, riducendo i tempi di produzione.
- Elevata capacità: I forni possono impilare più strati di crogioli, consentendo di sinterizzare fino a 150 unità in un singolo ciclo.
- Caratteristiche ambientali e di sicurezza: Utilizzo di materiali ecologici e non inquinanti e funzioni di memoria che riprendono le operazioni dopo le interruzioni di corrente.
-
Applicazioni della zirconia sinterizzata:
- L'ossido di zirconio sinterizzato è ampiamente utilizzato in settori come l'odontoiatria, dove le sue proprietà di resistenza, durata ed estetica sono molto apprezzate. Il processo di sinterizzazione garantisce che i restauri in zirconia soddisfino gli standard richiesti per quanto riguarda l'adattamento, la funzione e l'aspetto.
Comprendendo il processo di sinterizzazione tradizionale e il ruolo delle apparecchiature avanzate come il forno di sinterizzazione della zirconia i produttori possono realizzare prodotti in zirconia di alta qualità con proprietà e prestazioni costanti.
Tabella riassuntiva:
Aspetto | Dettagli |
---|---|
Definizione | Fonde materiali come l'ossido di zirconio in una massa solida senza fondere, migliorando l'integrità strutturale. |
Fasi | Fasi di riscaldamento, sinterizzazione e raffreddamento per garantire resistenza e densità. |
Attrezzatura chiave | Forno di sinterizzazione dell'ossido di zirconio con controllo preciso della temperatura e distribuzione uniforme del calore. |
Vantaggi | Maggiore resistenza meccanica, migliore finitura superficiale ed elevata efficienza. |
Applicazioni | Ampiamente utilizzato in odontoiatria per restauri in zirconia durevoli ed esteticamente gradevoli. |
Siete pronti a ottimizzare il vostro processo di sinterizzazione? Contattateci oggi stesso per saperne di più sui nostri forni avanzati per la sinterizzazione della zirconia!