La frequenza della corrente alternata (CA) nel riscaldamento a induzione svolge un ruolo fondamentale nel determinare la profondità della generazione di calore, l'efficienza e l'idoneità dell'applicazione.Le frequenze più elevate determinano una penetrazione del calore più superficiale a causa dell'effetto pelle, rendendole ideali per il riscaldamento superficiale e le applicazioni di tempra.Le frequenze più basse, invece, consentono una penetrazione del calore più profonda e sono più adatte per il riscaldamento di grandi quantità o per i processi di fusione.La scelta della frequenza influisce anche sulla capacità di potenza, sulla turbolenza nei materiali fusi e sull'efficienza complessiva del sistema di riscaldamento a induzione.La comprensione di questi effetti è essenziale per selezionare la frequenza appropriata per specifiche applicazioni industriali.
Punti chiave spiegati:
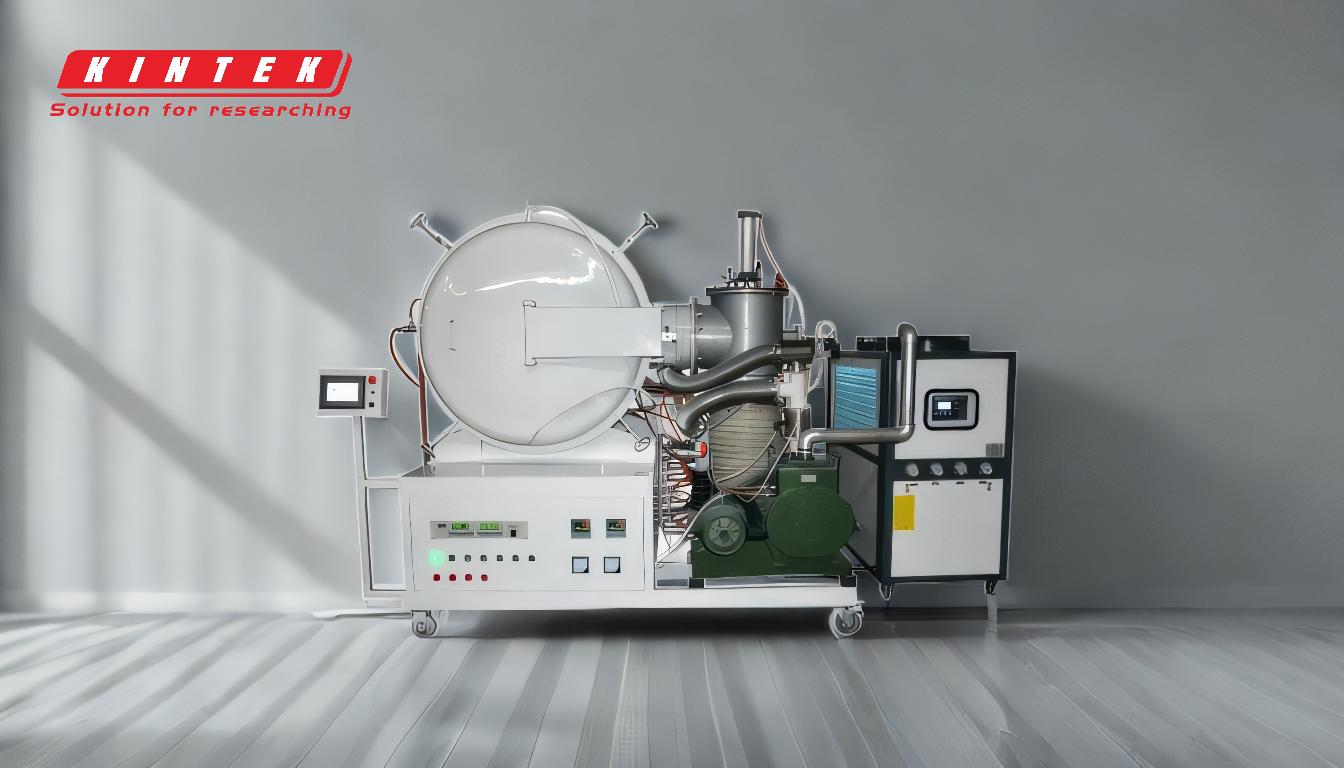
-
Dinamica della frequenza e del campo magnetico:
- La frequenza della corrente alternata determina la velocità con cui il campo magnetico cambia direzione.Ad esempio, una corrente di 60 Hz fa cambiare direzione al campo magnetico 60 volte al secondo, mentre una corrente di 400 kHz provoca 400.000 commutazioni al secondo.
- Questa rapida commutazione induce correnti parassite nel pezzo, che generano calore attraverso la resistenza.La frequenza della corrente nella bobina controlla direttamente la frequenza della corrente indotta nel pezzo.
-
Profondità di generazione del calore (effetto pelle):
- Frequenze più elevate (ad esempio, 400 kHz) creano una maggiore differenza di densità di corrente tra la superficie e l'interno del pezzo, con conseguente assottigliamento dello strato di riscaldamento.Questo fenomeno è noto come effetto pelle.
- Le frequenze più basse (ad esempio, 50-60 Hz) consentono una penetrazione più profonda della corrente indotta, rendendole adatte al riscaldamento di materiali più spessi o al riscaldamento uniforme di materiali sfusi.
-
Applicazioni in base alla frequenza:
- Alte frequenze:Ideale per la tempra superficiale, dove solo lo strato esterno del materiale deve essere riscaldato al di sopra della sua temperatura critica.Il rapido raffreddamento dopo il riscaldamento consente di ottenere la tempra superficiale.
- Basse frequenze:Adatti per fondere o riscaldare grandi volumi di materiale, in quanto consentono una penetrazione più profonda e possono indurre agitazione o turbolenza nei metalli fusi.
-
Capacità di potenza ed efficienza:
- Le frequenze più elevate consentono di applicare una maggiore potenza a un forno di una determinata capacità, permettendo processi di riscaldamento o fusione più rapidi.
- Le frequenze più basse, pur essendo meno potenti per il riscaldamento superficiale, sono più efficienti per il riscaldamento di materiali in massa, grazie alla loro penetrazione più profonda e alla ridotta perdita di energia.
-
Turbolenza e agitazione nei materiali fusi:
- Le frequenze più elevate determinano una minore turbolenza nei materiali fusi, a vantaggio delle applicazioni che richiedono un controllo preciso della fusione.
- Le frequenze più basse possono generare una turbolenza significativa, che può essere vantaggiosa per la miscelazione o l'omogeneizzazione dei metalli fusi.
-
Fattori di selezione della frequenza:
- Proprietà del materiale:La conduttività elettrica e la permeabilità magnetica del materiale influenzano la frequenza ottimale.
- Capacità del forno:I forni o le fusioni più piccole richiedono in genere frequenze più elevate a causa dell'effetto di profondità della pelle.
- Requisiti di applicazione:La profondità di riscaldamento desiderata, l'uniformità della temperatura e la velocità di lavorazione determinano la scelta della frequenza.
Comprendendo questi punti chiave, gli acquirenti di apparecchiature e materiali di consumo possono prendere decisioni informate sulle impostazioni di frequenza dei sistemi di riscaldamento a induzione, garantendo prestazioni ed efficienza ottimali per le loro applicazioni specifiche.
Tabella riassuntiva:
Aspetto | Alta frequenza (ad esempio, 400 kHz) | Bassa frequenza (ad es., 50-60 Hz) |
---|---|---|
Penetrazione del calore | Poco profonda (effetto pelle) | Profondo |
Applicazioni | Indurimento superficiale, materiali sottili | Riscaldamento di massa, fusione, materiali spessi |
Capacità di potenza | Maggiore potenza per un riscaldamento più rapido | Potenza inferiore, efficiente per il riscaldamento di grandi quantità |
Turbolenza nei materiali fusi | Turbolenza minima, controllo preciso | Turbolenza significativa, ideale per la miscelazione |
Idoneità del materiale | Materiali sottili e conduttivi | Materiali spessi e sfusi |
Avete bisogno di aiuto per scegliere la frequenza giusta per il vostro sistema di riscaldamento a induzione? Contattate oggi stesso i nostri esperti per soluzioni su misura!