I forni a induzione senza nucleo, pur essendo efficienti e versatili, presentano diversi svantaggi che possono influire sulle loro prestazioni e sulla loro idoneità per determinate applicazioni.Tra questi, le limitazioni nella capacità di raffinazione, la dipendenza da materiali di carica di alta qualità, la potenziale perdita di elementi di lega e le difficoltà nel trattare tipi specifici di metalli.Inoltre, i costi iniziali di installazione e di funzionamento, insieme alla necessità di un controllo preciso del processo, possono essere significativi.La comprensione di questi inconvenienti è fondamentale per prendere decisioni consapevoli nella scelta delle apparecchiature di fusione per i processi industriali.
Punti chiave spiegati:
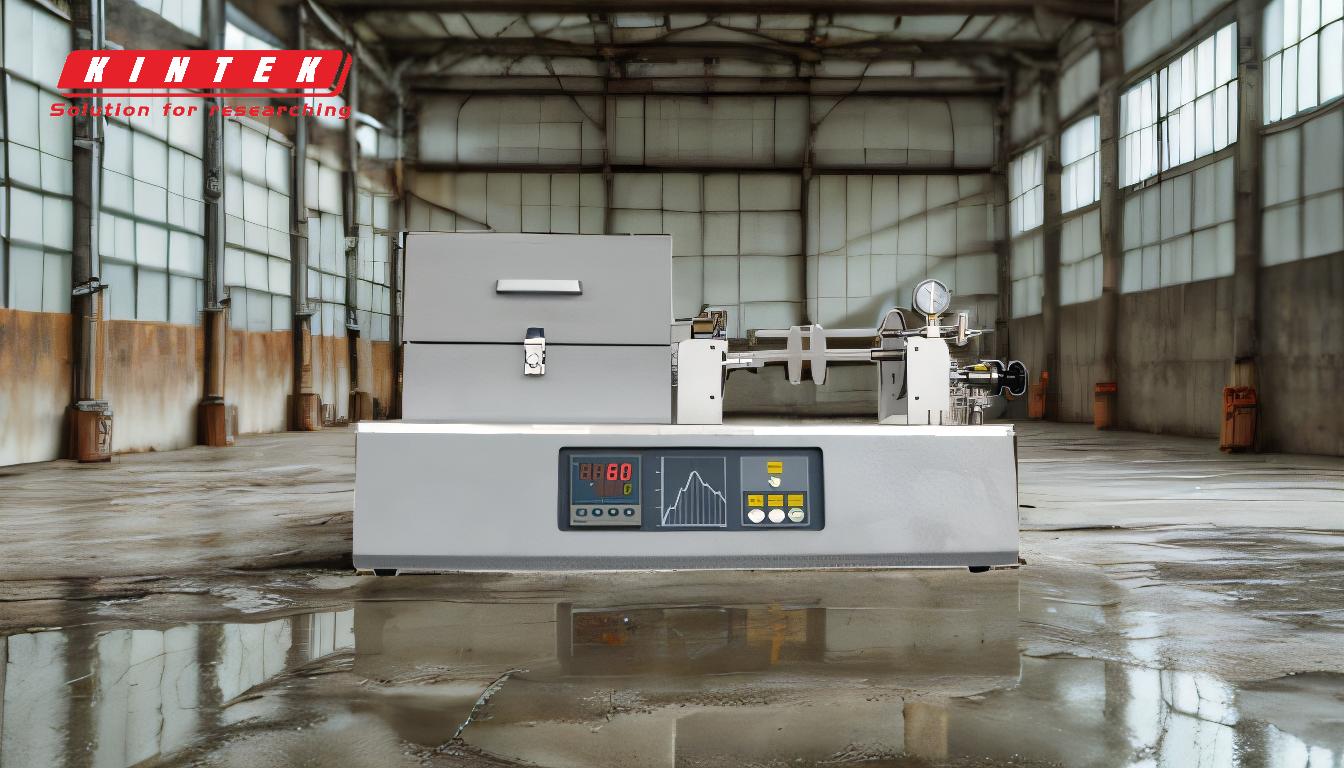
-
Mancanza di capacità di raffinazione:
- I forni a induzione senza nucleo sono principalmente unità di fusione e non hanno la capacità di raffinare i metalli.Ciò significa che i materiali di carica devono essere già privi di ossidi e impurità.Se le materie prime contengono contaminanti, il forno non può rimuoverli, compromettendo la qualità del prodotto finale.
- Questa limitazione lo rende inadatto alle applicazioni in cui è necessaria la raffinazione, come nella produzione di metalli o leghe di elevata purezza.
-
Dipendenza da materiali di carica di alta qualità:
- Poiché il forno non può raffinare la carica, la qualità del prodotto finale dipende fortemente dalla qualità dei materiali in ingresso.Ciò richiede un'attenta selezione e preparazione delle materie prime, che può aumentare i costi e la complessità.
- Eventuali impurità o incongruenze nella carica possono portare a difetti nel prodotto finale, rendendolo meno adatto ad applicazioni di alta precisione.
-
Perdita di elementi di lega:
- Alcuni elementi di lega possono andare persi durante il processo di fusione a causa dell'ossidazione.Questo è particolarmente problematico per gli elementi inclini all'ossidazione, come l'alluminio o il magnesio.
- Per compensare questa perdita, può essere necessario aggiungere ulteriori elementi di lega alla fusione, il che può aumentare i costi dei materiali e complicare il processo.
-
Sfide con metalli specifici:
- I forni a induzione senza nucleo possono non essere adatti alla fusione di alcuni tipi di metalli, come quelli con punti di fusione elevati o quelli che richiedono condizioni atmosferiche specifiche (ad esempio, ambienti sotto vuoto o con gas inerte).
- Per tali applicazioni, un forno a induzione sotto vuoto potrebbe essere più appropriato, in quanto in grado di fornire il controllo necessario sull'ambiente di fusione.
-
Alti costi iniziali e operativi:
- Il costo iniziale di un forno a induzione senza nucleo può essere elevato, soprattutto se si considera la necessità di un'unità di alimentazione robusta, di un sistema di raffreddamento e di un sistema di controllo del processo.
- Anche i costi operativi possono essere significativi, soprattutto in termini di consumo energetico e manutenzione dei componenti del forno.
-
Requisiti di precisione e controllo:
- Sebbene i forni a induzione offrano un'elevata accuratezza nel controllo della temperatura, il raggiungimento di questo livello di precisione richiede sofisticati sistemi di controllo del processo.Qualsiasi guasto in questi sistemi può portare a incongruenze nel processo di fusione, incidendo sulla qualità del prodotto finale.
- La necessità di un controllo preciso implica anche che gli operatori debbano essere altamente qualificati, aumentando la complessità operativa e i costi.
-
Considerazioni sull'ambiente e sulla sicurezza:
- Sebbene i forni a induzione generino scarti e inquinanti minimi, richiedono comunque un impianto di aspirazione dei fumi per gestire le emissioni.Ciò aumenta il costo complessivo e la complessità del sistema.
- La sicurezza è un'altra preoccupazione, soprattutto quando si ha a che fare con alte temperature e metalli fusi.È necessario adottare misure di sicurezza adeguate per proteggere i lavoratori e le attrezzature.
In sintesi, i forni a induzione senza nucleo offrono diversi vantaggi, come il riscaldamento rapido e l'alta efficienza, ma presentano anche notevoli svantaggi.Tra questi, le limitazioni nella capacità di raffinazione, la dipendenza da materiali di carica di alta qualità, la potenziale perdita di elementi di lega e le difficoltà con metalli specifici.Inoltre, gli elevati costi iniziali e operativi, insieme alla necessità di un controllo preciso, possono renderli meno adatti ad alcune applicazioni.La comprensione di questi svantaggi è essenziale per prendere decisioni consapevoli nella scelta delle apparecchiature di fusione.
Tabella riassuntiva:
Svantaggio | Dettagli chiave |
---|---|
Mancanza di capacità di raffinazione | Non può raffinare i metalli; richiede materiali di carica di alta qualità e privi di impurità. |
Dipendenza dalla qualità dei materiali | La qualità del prodotto finale dipende dalla qualità dei materiali in ingresso, con conseguente aumento dei costi. |
Perdita di elementi di lega | L'ossidazione porta alla perdita di elementi come l'alluminio o il magnesio. |
Problemi con metalli specifici | Non adatto a metalli ad alto punto di fusione o che necessitano di atmosfere controllate. |
Alti costi iniziali e operativi | Spese di installazione e di funzionamento significative, comprese quelle per l'energia e la manutenzione. |
Requisiti di precisione e controllo | Richiede operatori qualificati e sistemi avanzati di controllo del processo. |
Problemi ambientali e di sicurezza | Necessita di attrezzature per l'estrazione dei fumi e di misure di sicurezza rigorose. |
Avete bisogno di aiuto per scegliere la giusta attrezzatura per la fusione? Contattate i nostri esperti oggi stesso per soluzioni su misura!