La ricottura è un processo di trattamento termico critico utilizzato per modificare le proprietà fisiche e meccaniche dei materiali, principalmente dei metalli.È necessario in condizioni specifiche in cui il materiale deve essere ammorbidito, reso più duttile o alleggerito dalle tensioni interne.Questo processo è essenziale per migliorare la lavorabilità, facilitare la lavorazione a freddo, migliorare le proprietà meccaniche o elettriche e garantire la stabilità dimensionale.La ricottura è particolarmente utile dopo processi di fabbricazione come la colata o la lavorazione a freddo, dove le tensioni interne e la durezza possono compromettere le prestazioni del materiale.Riscaldando il materiale alla sua temperatura di ricristallizzazione, mantenendolo a quella temperatura e raffreddandolo poi a velocità controllata, la ricottura aiuta a ottenere una struttura più uniforme e lavorabile.
Punti chiave spiegati:
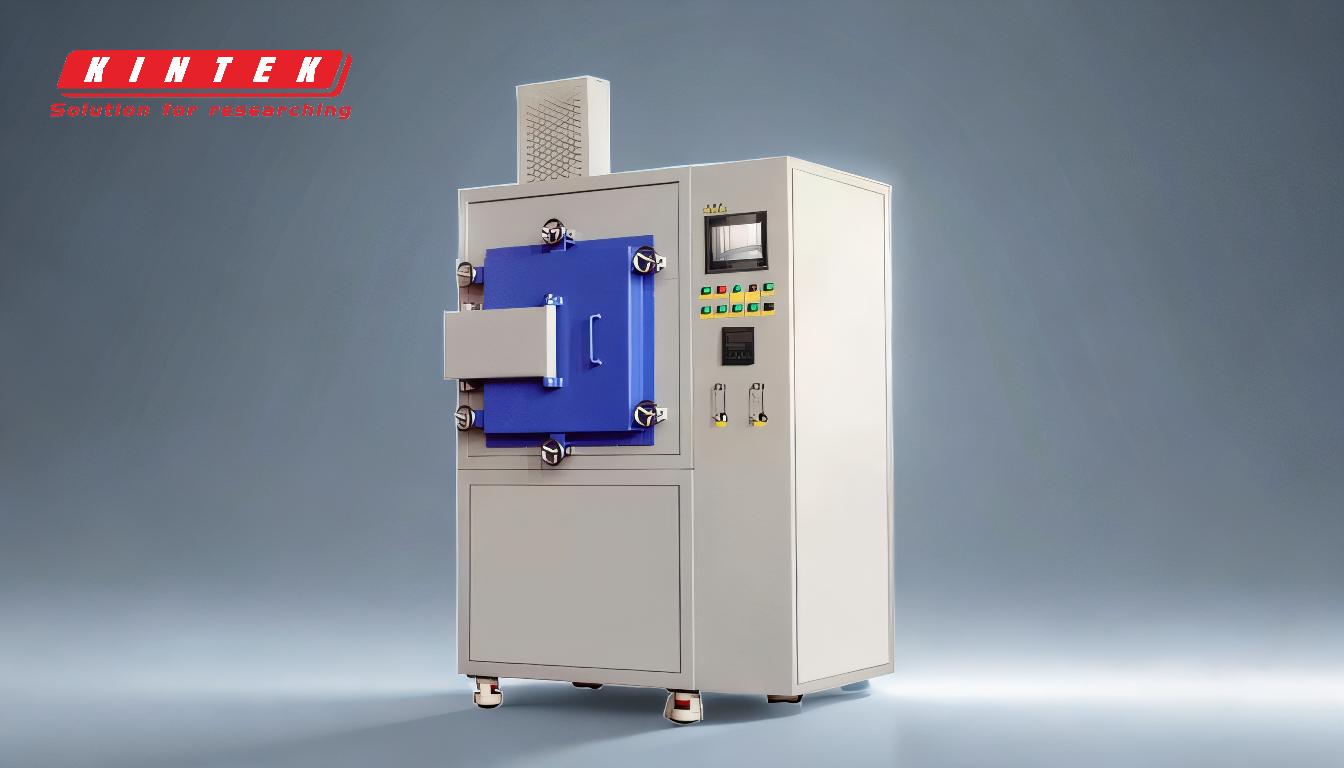
-
Riduzione della durezza e aumento della duttilità:
- La ricottura viene utilizzata principalmente per ridurre la durezza di un materiale, rendendolo più morbido e duttile.Ciò si ottiene riscaldando il materiale a una temperatura specifica (di solito la sua temperatura di ricristallizzazione) e poi raffreddandolo lentamente.Il processo riduce il numero di dislocazioni nella struttura cristallina, diminuendo la durezza e aumentando la duttilità.In questo modo il materiale può essere lavorato, lavorato a freddo o modellato più facilmente, senza il rischio di incrinature o fratture sotto sforzo.
-
Alleggerimento delle sollecitazioni interne:
- Le tensioni interne possono svilupparsi nei materiali durante i processi di produzione come la fusione, la saldatura o la lavorazione a freddo.Queste tensioni possono portare alla rottura o alla deformazione del materiale nel tempo.La ricottura aiuta ad alleviare queste tensioni, consentendo al materiale di raggiungere una struttura interna più stabile e uniforme.Ciò è particolarmente importante per i componenti che saranno sottoposti a carichi meccanici o a cicli termici durante il servizio.
-
Miglioramento della lavorabilità:
- I materiali troppo duri possono essere difficili da lavorare, causando una maggiore usura degli utensili e finiture superficiali scadenti.La ricottura ammorbidisce il materiale, rendendolo più facile da tagliare, forare o modellare.Ciò è particolarmente vantaggioso per i metalli che devono essere sottoposti a lunghe lavorazioni, in quanto riduce il rischio di rottura degli utensili e migliora l'efficienza del processo di lavorazione.
-
Facilitazione della lavorazione a freddo:
- I processi di lavorazione a freddo, come la laminazione, la trafilatura o la forgiatura, possono aumentare significativamente la durezza e la resistenza di un materiale, ma anche renderlo più fragile.La ricottura viene spesso eseguita tra le fasi di lavorazione a freddo per ripristinare la duttilità e ridurre la fragilità, consentendo ulteriori lavorazioni senza il rischio di cricche.Questo è fondamentale per la produzione di forme complesse o sezioni sottili che richiedono più fasi di formatura.
-
Miglioramento delle proprietà meccaniche ed elettriche:
- La ricottura può migliorare le proprietà meccaniche di un materiale, come la resistenza alla trazione, la tenacità e la resistenza alla fatica, affinando la struttura dei grani.Inoltre, per i materiali elettrici come il rame o l'alluminio, la ricottura può migliorare la conducibilità elettrica riducendo i difetti nel reticolo cristallino.Ciò rende il materiale più adatto ad applicazioni in cui sono fondamentali sia la resistenza meccanica che le prestazioni elettriche.
-
Produzione di una struttura uniforme e omogenea:
- Durante la produzione, i materiali possono sviluppare microstrutture non uniformi a causa di un raffreddamento non uniforme o di una deformazione meccanica.La ricottura aiuta a produrre una struttura interna più uniforme e omogenea, consentendo al materiale di ricristallizzare e formare grani equilateri.Questa uniformità migliora le prestazioni complessive e l'affidabilità del materiale, soprattutto nelle applicazioni in cui la costanza è fondamentale.
-
Ripristino del materiale in una condizione "morbida".:
- Dopo processi come la lavorazione a freddo o il trattamento termico, i materiali possono diventare troppo duri o fragili per essere lavorati ulteriormente.La ricottura riporta il materiale a una condizione più morbida, facilitando l'esecuzione di ulteriori operazioni di lavorazione, formatura o trattamento termico.Ciò è particolarmente importante per i materiali che devono essere sottoposti a più fasi di lavorazione per ottenere le proprietà finali desiderate.
-
Stabilità dimensionale:
- La ricottura può contribuire a migliorare la stabilità dimensionale di un materiale riducendo le tensioni residue che possono causare deformazioni o distorsioni nel tempo.Ciò è particolarmente importante per i componenti di precisione che devono mantenere tolleranze ristrette durante la loro vita utile.
In sintesi, la ricottura è necessaria nelle condizioni in cui i materiali devono essere ammorbiditi, resi più duttili o alleggeriti dalle tensioni interne.È un processo versatile che migliora la lavorabilità, facilita la lavorazione a freddo, migliora le proprietà meccaniche ed elettriche e garantisce la stabilità dimensionale, rendendolo indispensabile in diverse applicazioni di produzione e ingegneria.
Tabella riassuntiva:
Vantaggi principali della ricottura | Descrizione |
---|---|
Riduzione della durezza | Ammorbidisce i materiali, rendendoli più duttili e più facili da lavorare o modellare. |
Riduzione delle sollecitazioni interne | Riduce le sollecitazioni interne causate da processi produttivi come la fusione o la saldatura. |
Migliore lavorabilità | Migliora la facilità di taglio, foratura o sagomatura, riducendo l'usura degli utensili. |
Facilitazione della lavorazione a freddo | Ripristina la duttilità tra le fasi di lavorazione a freddo, prevenendo le cricche. |
Migliori proprietà meccaniche | Migliora la resistenza alla trazione, la tenacità e la resistenza alla fatica. |
Microstruttura uniforme | Produce una struttura interna omogenea per una migliore consistenza. |
Ripristino della condizione morbida | Prepara i materiali per un'ulteriore lavorazione dopo l'indurimento. |
Stabilità dimensionale | Riduce le deformazioni e le distorsioni, garantendo tolleranze strette. |
Avete bisogno di soluzioni di ricottura per i vostri materiali? Contattate i nostri esperti oggi stesso per saperne di più!