Introduction
Table of Contents
- Introduction
- Understanding Isostatic Pressing
- Cold Isostatic Pressing (CIP)
- Hot Isostatic Pressing (HIP)
- Applications of HIP in various industries
- Process fundamentals and manufacturing steps
- Role of hermetically sealed containers
- Use of inert gases as pressurized medium
- Density achievement through HIP and its dependence on careful control of various factors
- Requirement of clean, spherical powders and importance of contamination avoidance
- Comparison between CIP and HIP
- Comparison of HIP Capabilities with Other Compaction Methods
- Conclusion
Isostatic pressing is a compaction method that offers unique advantages in achieving uniform density and creating complex shapes. Unlike other compaction methods, isostatic pressing utilizes flexible molds to reduce friction and allow for intricate designs. In this blog post, we will delve into the concept of isostatic pressing and explore its applications in various industries. We will also compare isostatic pressing with other compaction methods to understand its capabilities and limitations. So, if you're curious about the fascinating world of isostatic pressing and how it can benefit your business, keep on reading!
Understanding Isostatic Pressing
Concept of isostatic pressing
Isostatic pressing is a powder processing technique that uses fluid pressure to compact the part. Metal powders are placed in a flexible container, which acts as the mold for the part. Fluid pressure is applied over the entire outside surface of the container, causing it to press and form the powder into the correct geometry. Unlike other processes that exert forces on the powder through an axis, isostatic pressing uses pressure from all around.
Benefits of uniform density
One of the main advantages of isostatic pressing is the ability to achieve uniform density within the compacted part. Conventional processing methods often result in density variations, particularly with certain parts. Isostatic pressing provides a solution to this issue by exerting all-around pressure, ensuring uniform compaction of the powder. This leads to consistent density throughout the part, which is crucial for its performance and material properties.
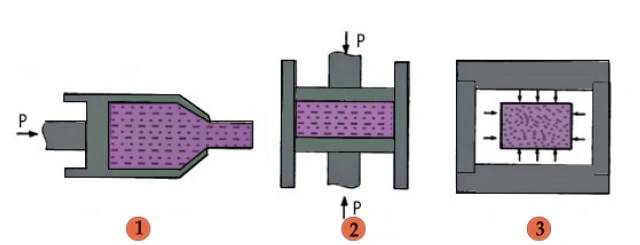
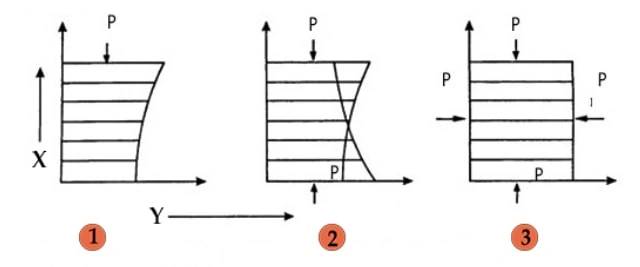
Role of flexible molds in reducing friction and allowing complex shapes
Isostatic pressing utilizes flexible elastomeric molds instead of rigid dies. The powder is loaded into the mold, which is then sealed and placed in a pressure vessel. The pressure is applied via a liquid, allowing the powder to be compacted under hydrostatic conditions. This reduces or eliminates die wall friction, resulting in higher accuracy of pressed surfaces.
Additionally, the use of flexible molds enables the production of complex shapes. The mold can conform to intricate geometries, which is especially beneficial for parts with irregular shapes or high thickness to diameter ratios. The combination of flexible molds and all-around pressure in isostatic pressing allows for the creation of complex and precisely formed parts.
Isostatic pressing, whether cold or hot, offers various advantages in terms of density uniformity, material utilization, and the ability to produce parts with complex shapes. While there are limitations in terms of size and shape capabilities, isostatic pressing remains a valuable powder compaction technique in many industries.
Cold Isostatic Pressing (CIP)
Working mechanism of CIP
Cold isostatic pressing (CIP) is a method of processing materials that involves compacting powders by enclosing them in an elastomer mold. This mold is then subjected to uniform liquid pressure from all directions, compressing the powders and creating a highly compact solid. This process is based on Pascal's law, which states that pressure applied to an enclosed fluid is transmitted in all directions without any change in magnitude.
Use of flexible membranes and various mold materials
CIP utilizes elastomer molds, such as urethane, rubber, or polyvinyl chloride, which have low resistance to deformation. These flexible membranes allow for the uniform distribution of pressure throughout the mold, resulting in the compaction of powders into a solid homogeneous mass.
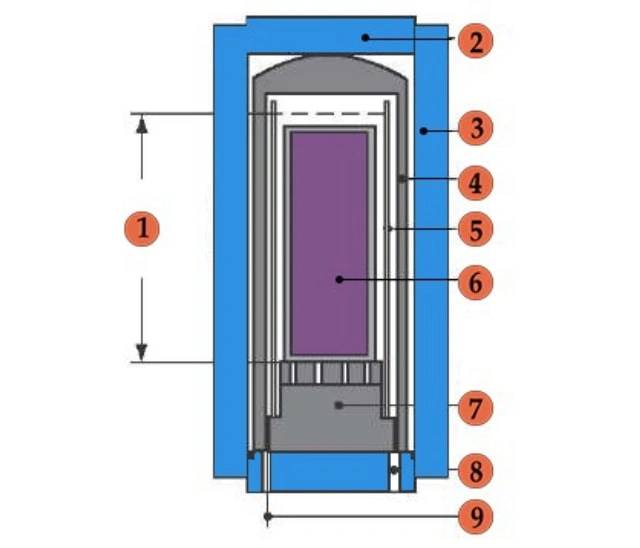
Size limitations based on pressure vessel size
The size limitations of CIP are determined by the capacity of the pressure vessel used. Cold isostatic pressing equipment is available in a range of sizes, from laboratory units with small inner diameters to units that are over 2m wide. The operational pressure levels can reach up to 900 MPa (130,000 psi).
Benefits of minimized friction effects
Compared to die pressing, cold isostatic pressing offers the advantage of achieving more uniform densities due to minimized friction effects. The flexible mold used in CIP allows for the compression of powders without the constraints of rigid tooling. This results in a more uniform distribution of pressure and a higher level of dimensional accuracy.
Limitations in comparison to die pressing
While cold isostatic pressing offers benefits such as uniform densities and minimized friction effects, it does have limitations compared to die pressing. The dimensional control in CIP is generally not as tight as with die pressing due to the flexible tooling. However, rigid members can be incorporated into the mold assembly to produce accurate surfaces where desired.
Overall, cold isostatic pressing is a versatile method of compacting powdered materials into solid homogeneous masses. It is commonly used in various industries, including plastics, ceramics, powdered metallurgy, and sputtering targets, offering benefits such as uniform densities and minimized friction effects. However, it is important to consider the limitations of CIP, such as the dimensional control and size limitations based on pressure vessel size.
Hot Isostatic Pressing (HIP)
Hot Isostatic Pressing (HIP) is a manufacturing technique that uses heat and pressure to improve the physical properties of metals and ceramics. It is commonly used to reduce porosity and increase the density of materials, resulting in improved mechanical properties.
Applications of HIP in various industries
HIP is widely used in various industries for different applications. In powder metallurgy, it allows for the compression of metal powders at high temperatures and pressures, resulting in a product with a homogenous annealed microstructure and minimal impurities. This is especially beneficial for aerospace components and other critical applications.
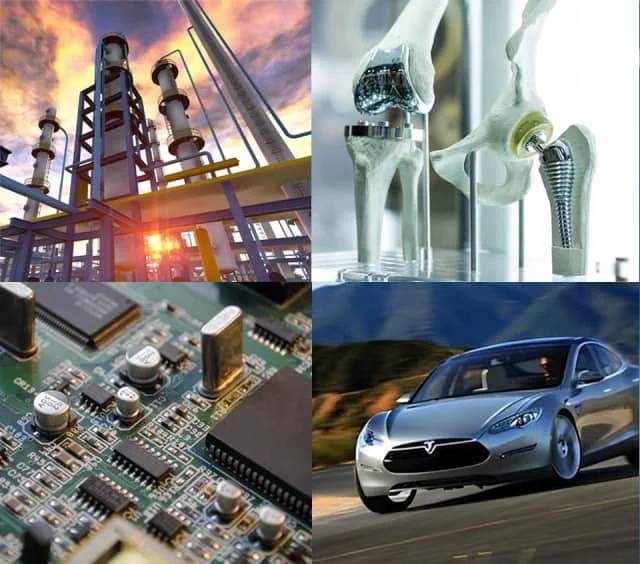
Process fundamentals and manufacturing steps
During HIP, materials are subjected to high temperatures and pressures in a pressure vessel. The temperature, pressure, and process time are precisely controlled to achieve the desired material properties. The parts are heated in an inert gas, such as argon, which applies uniform pressure in all directions. This pressure causes the material to become "plastic," allowing voids to collapse and the surfaces to diffusion bond together, resulting in near theoretical density.
Role of hermetically sealed containers
Hermetically sealed containers play a crucial role in the HIP process. They ensure that the pressure medium, usually an inert gas, does not penetrate the material. This is especially important for additive manufacturing parts, as the high density achieved during manufacturing enables capsule-free HIP processing.
Use of inert gases as pressurized medium
Inert gases, such as argon, are commonly used as the pressurized medium in HIP. These gases prevent chemical reactions with the material during the process. The application of both heat and pressure helps to eliminate small gaps in the material, increasing density and ensuring a uniform composition.
Density achievement through HIP and its dependence on careful control of various factors
HIP plays a crucial role in achieving high material density. By carefully controlling factors such as temperature, pressure, and process time, voids in the material collapse and diffusion bonding occurs, resulting in near theoretical density. The careful control of these factors is essential to ensure the desired material properties.
Requirement of clean, spherical powders and importance of contamination avoidance
To achieve optimal results in HIP, clean and spherical powders are required. Contamination can have a significant impact on the final product, affecting its mechanical properties. Therefore, it is crucial to avoid contamination and use high-quality powders in the HIP process.
Overall, Hot Isostatic Pressing (HIP) is a valuable manufacturing technique that can improve the physical properties of metals and ceramics. By carefully controlling temperature, pressure, and process time, HIP can reduce porosity, increase density, and enhance the mechanical properties of materials. It has various applications in industries such as aerospace, powder metallurgy, and additive manufacturing. To achieve optimal results, it is essential to use clean powders and avoid contamination during the process.
Comparison between CIP and HIP
Comparison of achievable dimensional tolerances
Both the CIP and HIP processes use multi-material constructs. CIP utilizes polymer shells with ceramic powders, while HIP involves welded mild steel sheet material casing with high-end powder metallurgy alloys. These methods offer the opportunity for single-step pre-processing of constructs through multi-material additive manufacturing. This approach can be particularly advantageous for producing small series or prototypes, potentially reducing manufacturing costs by allowing for increased part complexity with fewer processing steps and time.
Potential for producing complex shapes
CIP is excellent for producing intricate shapes due to its ability to create detailed molds. On the other hand, HIP is commonly used for densification of complex geometries and critical components. It can enhance the mechanical properties and uniformity of materials.
Possibility of achieving net surfaces by incorporating rigid members into the mold
Choosing the right method between Cold Isostatic Pressing (CIP) and Hot Isostatic Pressing (HIP) depends on your material's requirements, intended application, and desired properties. CIP is ideal for preliminary shaping and simple geometries. It is suitable for materials sensitive to high temperatures since it is a cold process. On the other hand, HIP requires elevated temperatures for diffusion and consolidation. HIP offers a comprehensive solution for enhancing material properties, minimizing defects, and achieving high-performance outcomes.
Ultimately, the choice between CIP and HIP will depend on the specific needs of your project and the desired outcomes in terms of dimensional tolerances, complexity of shapes, and material properties.
Comparison of HIP Capabilities with Other Compaction Methods
Densification percentage
Hot Isostatic Pressing (HIP) is a compaction method that combines high pressure and high temperature to achieve densification and enhance properties through diffusion and consolidation. This method is especially valuable for materials requiring improved structural integrity, reduced porosity, and higher mechanical properties. In comparison, Cold Isostatic Pressing (CIP) involves cold compaction using isostatic pressure but does not involve high temperatures.
Applications based on part size, complexity, and level of densification
HIP is capable of manufacturing a wide range of component types, including large and massive near net shape metal components weighing up to 30 tonnes. It can also be used to produce small PM HSS cutting tools or even very tiny parts such as dental brackets. CIP, on the other hand, is often used for shaping and initial consolidation of powdered materials.
Impact of size, density, and performance on the P/M approach
The size, density, and performance of a component are key factors that dictate the Powder Metallurgy (P/M) approach. HIP is a high-performance, high-quality, and cost-effective process for the production of metal or ceramic components. It is often used in combination with other PM processes such as Metal Injection Moulding (MIM), pressing and sintering, or additive manufacturing technologies for part densification and the production of semi-finished bars or slabs. The CIP process can also be combined with HIP, known as CHIP, where loose powder is cold-compacted, then sintered, and finally post-HIPed to achieve fully dense parts.
Overall, HIP offers unique capabilities in terms of densification percentage, applications based on part size and complexity, and the impact of size, density, and performance on the P/M approach. It is a versatile and effective compaction method for producing high-performance materials with superior mechanical properties and structural integrity.
Conclusion
In conclusion, isostatic pressing offers numerous advantages in terms of achieving uniform density and creating complex shapes. Cold isostatic pressing (CIP) minimizes friction effects and allows for the use of various mold materials, while hot isostatic pressing (HIP) utilizes hermetically sealed containers and inert gases to achieve high-density components. When comparing CIP and HIP, dimensional tolerances, complex shape production, and net surface incorporation are important factors to consider. Furthermore, when comparing HIP with other compaction methods, factors such as densification percentage, part size and complexity, and the impact on performance should be taken into account. Overall, isostatic pressing proves to be a versatile and efficient compaction method for various industries.
CONTATTATECI PER UNA CONSULENZA GRATUITA
I prodotti e i servizi di KINTEK LAB SOLUTION sono stati riconosciuti da clienti di tutto il mondo. Il nostro personale sarà lieto di assistervi per qualsiasi richiesta. Contattateci per una consulenza gratuita e parlate con uno specialista del prodotto per trovare la soluzione più adatta alle vostre esigenze applicative!