I forni a induzione utilizzano le alte frequenze principalmente per migliorare l'efficienza, la precisione e il controllo del processo di fusione.I forni a induzione ad alta frequenza sono particolarmente efficaci per volumi ridotti di metallo grazie all'effetto di profondità della pelle, che fa sì che la corrente alternata penetri solo nello strato superficiale del materiale.Il risultato è un riscaldamento più rapido, un tempo di fusione ridotto e un migliore controllo della temperatura.Inoltre, le alte frequenze consentono l'agitazione automatica del metallo fuso attraverso correnti parassite, migliorando l'omogeneità.La progettazione di forni ad alta frequenza è più semplice ed economica e li rende ideali per applicazioni che richiedono precisione e rapidità di fusione.In generale, le alte frequenze ottimizzano il trasferimento di energia e l'efficienza operativa dei forni a induzione.
Punti chiave spiegati:
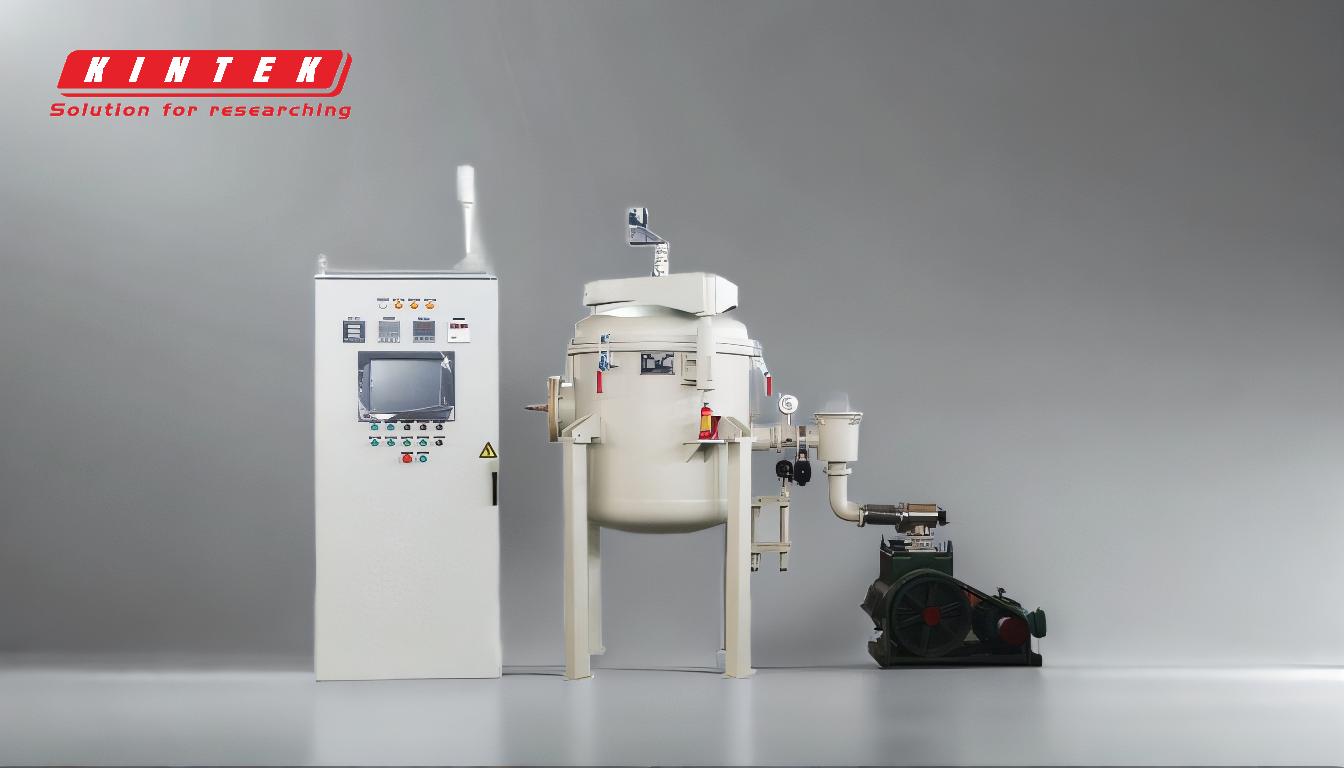
-
Effetto profondità della pelle e penetrazione:
- I forni a induzione ad alta frequenza sfruttano l'effetto effetto profondità della pelle che si riferisce alla profondità con cui la corrente alternata penetra in un materiale conduttore.
- Le frequenze più alte comportano una una penetrazione meno profonda concentrando il calore sulla superficie del materiale.Ciò è particolarmente vantaggioso per i piccoli volumi di metallo, in quanto garantisce un riscaldamento rapido ed efficiente.
- Le frequenze più basse, invece, penetrano più in profondità ma sono meno efficienti per le fusioni più piccole e possono causare turbolenze nel metallo fuso.
-
Fusione più rapida e tempi di lavorazione ridotti:
- Le alte frequenze riducono significativamente riducono il tempo di fusione concentrando l'energia sulla superficie del materiale, dove è più efficace.
- Ciò è particolarmente vantaggioso per le applicazioni che richiedono tempi rapidi, come nelle fonderie o nelle industrie di lavorazione dei metalli.
-
Controllo di precisione della temperatura:
- I forni a induzione ad alta frequenza offrono un un controllo preciso della temperatura garantendo che il metallo raggiunga la temperatura desiderata senza surriscaldarsi.
- Questa precisione è fondamentale per i processi che richiedono proprietà metallurgiche specifiche o per la fusione di leghe con intervalli di temperatura ristretti.
-
Agitazione automatica tramite correnti parassite:
- La corrente alternata ad alta frequenza genera correnti parassite all'interno del metallo fuso, creando un effetto di agitazione naturale.
- Questo mescolamento automatico garantisce omogeneità nel metallo fuso, riducendo la necessità di interventi manuali e migliorando la qualità del prodotto finale.
-
Progettazione semplificata e costi ridotti:
- I forni a induzione ad alta frequenza hanno una struttura un design più semplice del crogiolo e del contenitore riducendo i requisiti di manutenzione e la complessità operativa.
- Il costo complessivo costo di funzionamento è inferiore grazie alla maggiore efficienza energetica e alla riduzione dei tempi di lavorazione.
-
Efficienza energetica e principi dei trasformatori:
- I forni a induzione funzionano secondo principi del trasformatore in cui l'avvolgimento primario (bobina di induzione) trasferisce energia all'avvolgimento secondario (carica metallica).
- Le alte frequenze (in genere da 500 Hz a 1000 Hz) garantiscono un trasferimento efficiente dell'energia, riducendo al minimo le perdite e massimizzando la generazione di calore attraverso le correnti parassite.
-
Applicazioni e idoneità dei materiali:
- I forni a induzione ad alta frequenza sono ideali per la fusione di piccoli volumi di materiali conduttivi come metalli preziosi, leghe e acciai speciali.
- Sono adatti anche per applicazioni che richiedono un riscaldamento rapido e controllo preciso, ad esempio nei laboratori o nella produzione su piccola scala.
-
Confronto con i forni a induzione a bassa frequenza:
- I forni a bassa frequenza sono più adatti per volumi più grandi di metallo, dove è richiesta una penetrazione più profonda.
- Tuttavia, sono meno efficienti per le fusioni più piccole e possono richiedere meccanismi di agitazione aggiuntivi, aumentando la complessità e il costo.
In sintesi, i forni a induzione ad alta frequenza sono preferiti per la loro capacità di fornire un riscaldamento rapido, preciso ed efficiente, in particolare per volumi ridotti di metallo.L'effetto di profondità della pelle, l'agitazione automatica e il design semplificato li rendono una scelta economica e affidabile per un'ampia gamma di applicazioni industriali.
Tabella riassuntiva:
Caratteristiche principali | Benefici |
---|---|
Effetto profondità della pelle | Concentra il calore sulla superficie per un riscaldamento rapido ed efficiente. |
Fusione più rapida | Riduce i tempi di lavorazione, ideale per le applicazioni che richiedono tempi rapidi. |
Controllo della temperatura di precisione | Assicura un riscaldamento accurato senza surriscaldamento, fondamentale per leghe specifiche. |
Agitazione automatica | Le correnti parassite creano omogeneità, migliorando la qualità del metallo fuso. |
Design semplificato | Riduzione dei costi di manutenzione e di esercizio, ideale per le applicazioni su piccola scala. |
Siete pronti a ottimizzare il vostro processo di fusione dei metalli? Contattateci oggi stesso per saperne di più sui forni a induzione ad alta frequenza!