La calcinazione e la fusione sono processi ad alta temperatura che richiedono forni specializzati per ottenere le trasformazioni chimiche e fisiche desiderate.La calcinazione consiste nel riscaldare i materiali ad alte temperature in assenza o con un apporto limitato di aria per indurre la decomposizione termica, mentre la fusione consiste nel fondere i minerali per estrarre i metalli.I tipi di forni utilizzati per questi processi includono forni a muffola, forni a riverbero, forni a pozzo e forni rotativi.Questi forni sono progettati per fornire un riscaldamento uniforme, un controllo preciso della temperatura e la capacità di gestire grandi volumi di materiali.Le applicazioni industriali utilizzano spesso forni di processo elettrici o a fiamma, a seconda dei costi e delle considerazioni ambientali.Qui di seguito vengono illustrati i principali tipi di forni utilizzati per la calcinazione e la fusione, le loro configurazioni e le loro applicazioni.
Punti chiave spiegati:
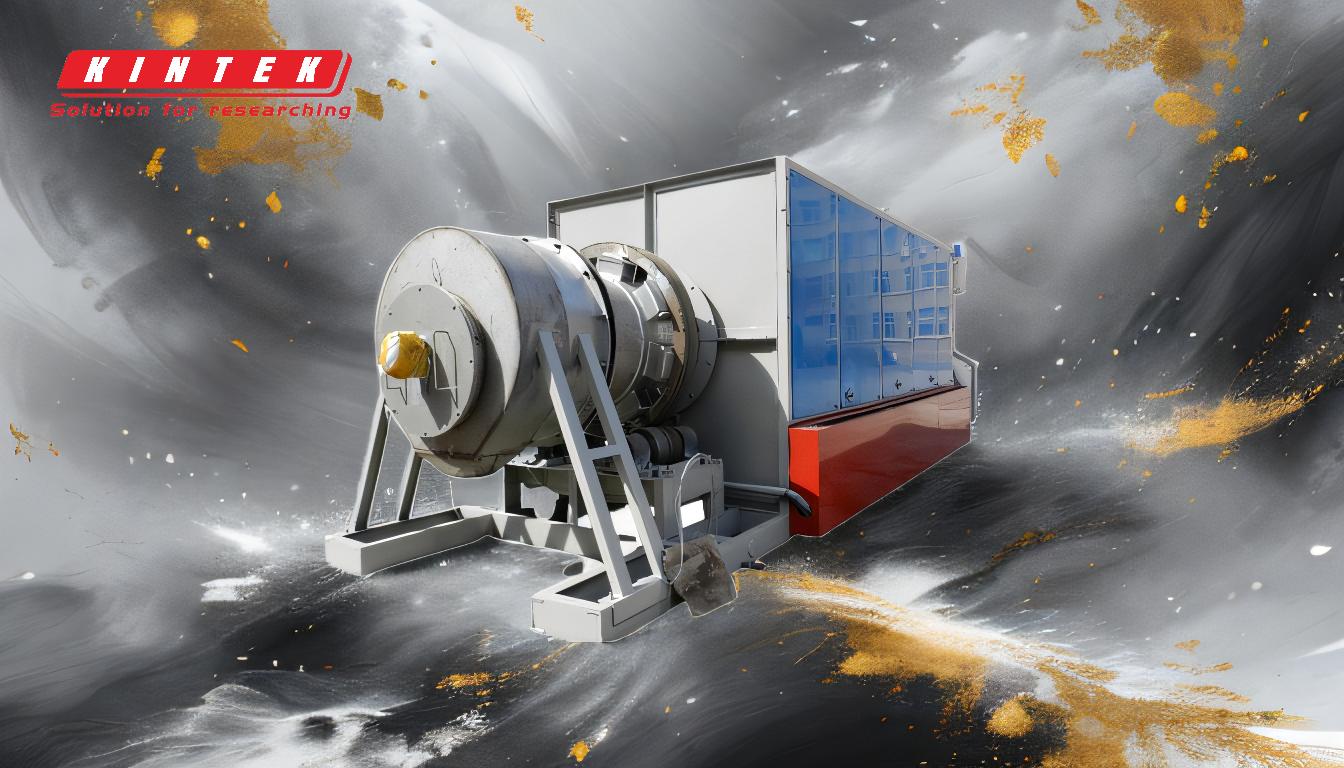
-
Forni a muffola:
- I forni a muffola sono ampiamente utilizzati per la calcinazione grazie alla loro capacità di fornire un riscaldamento uniforme e di isolare il materiale dai gas di combustione.Sono dotati di elementi riscaldanti che circondano una camera, garantendo un controllo preciso della temperatura.
- Applicazioni:Calcinazione di materiali come il calcare (per produrre calce), la ceramica e i catalizzatori.
- Vantaggi:Elevata uniformità della temperatura, isolamento dai contaminanti e idoneità all'uso in laboratorio o industriale su piccola scala.
-
Forni a riverbero:
- I forni a riverbero sono grandi forni su scala industriale utilizzati per la fusione e la calcinazione.Sono caratterizzati da un focolare poco profondo e da un tetto che riflette il calore sul materiale, garantendo un efficiente trasferimento di calore.
- Applicazioni:Fusione di metalli come rame e piombo e calcinazione di minerali.
- Vantaggi:Elevata capacità, capacità di gestire grandi volumi e idoneità al funzionamento continuo.
-
Forni ad albero:
- I forni ad albero sono forni verticali utilizzati per la calcinazione e la fusione.Funzionano alimentando i materiali dall'alto e facendoli scendere attraverso una camera riscaldata, dove subiscono un trattamento termico.
- Applicazioni:Calcinazione di calcare e dolomite, nonché fusione di minerali di ferro negli altiforni.
- Vantaggi:Utilizzo efficiente del calore, funzionamento continuo ed elevata produttività.
-
Forni rotativi:
- I forni rotativi sono forni cilindrici che ruotano per garantire un riscaldamento uniforme dei materiali.Sono comunemente utilizzati per i processi di calcinazione e fusione.
- Applicazioni:Calcinazione di clinker di cemento, allumina e altri minerali industriali, nonché fusione di minerali.
- Vantaggi:Elevata efficienza termica, capacità di gestire un'ampia gamma di materiali e processo continuo.
-
Forni di processo elettrici o a fiamma:
- I forni elettrici di processo sono utilizzati per la calcinazione e la fusione in applicazioni in cui il controllo dell'inquinamento è fondamentale.Sono più costosi, ma offrono un controllo preciso della temperatura e non producono emissioni.
- I forni di processo a combustione utilizzano combustibili (ad esempio, gas o olio) per generare calore e sono ampiamente utilizzati in ambito industriale grazie ai loro costi operativi ridotti.
- Applicazioni:I forni elettrici sono preferiti per i materiali di elevata purezza, mentre i forni a legna sono utilizzati nelle raffinerie, negli impianti petrolchimici e nella fusione dei metalli.
-
Forni specializzati per applicazioni industriali:
- I forni a tamburo rotante, i forni a suola rotante, i forni a platea a spinta e i forni a fondo mobile sono forni specializzati utilizzati per la sinterizzazione e la fusione di prodotti industriali.
- Applicazioni:Sinterizzazione di ceramica, metalli e altri materiali e fusione di minerali.
- Vantaggi:Elevata produttività, controllo preciso della temperatura e idoneità a operazioni industriali su larga scala.
Comprendendo i requisiti specifici dei processi di calcinazione e fusione, come l'intervallo di temperatura, il volume del materiale e le considerazioni ambientali, è possibile scegliere il tipo di forno appropriato per garantire prestazioni ed efficienza ottimali.
Tabella riassuntiva:
Tipo di forno | Applicazioni | Vantaggi |
---|---|---|
Forni a muffola | Calcinazione di calcare, ceramica e catalizzatori | Elevata uniformità di temperatura, isolamento dai contaminanti, utilizzo su piccola scala |
Forni a riverbero | Fusione di rame, piombo; calcinazione di minerali | Elevata capacità, gestione di grandi volumi, funzionamento continuo |
Forni a pozzo | Calcinazione di calcare, dolomite; fusione di minerali di ferro | Utilizzo efficiente del calore, funzionamento continuo, elevata produttività |
Forni rotativi | Calcinazione di clinker di cemento, allumina; fusione di minerali | Elevata efficienza termica, gestisce un'ampia gamma di materiali, lavorazione continua |
Forni elettrici di processo | Materiali di elevata purezza, applicazioni sensibili all'inquinamento | Controllo preciso della temperatura, nessuna emissione |
Forni di processo alimentati | Raffinerie, impianti petrolchimici, fonderia di metalli | Costi operativi ridotti, ampiamente utilizzati in ambito industriale |
Forni specializzati | Sinterizzazione di ceramica e metalli; fusione di minerali | Elevata produttività, controllo preciso della temperatura, funzionamento industriale su larga scala |
Avete bisogno di aiuto per scegliere il forno giusto per il vostro processo di calcinazione o fusione? Contattate i nostri esperti oggi stesso !