La tempra di ricottura, un processo critico in metallurgia, prevede il riscaldamento dei materiali a temperature specifiche per alterarne le proprietà fisiche e talvolta chimiche, seguito da un raffreddamento controllato. L'intervallo di temperatura per la tempra di ricottura varia in modo significativo a seconda del materiale da trattare, in genere da 500°C a 1200°C. Ad esempio, l'acciaio viene spesso ricotto a temperature comprese tra 700°C e 900°C, mentre le leghe di alluminio possono richiedere temperature più basse, tra 300°C e 500°C circa. Il processo mira a ridurre la durezza, aumentare la duttilità ed eliminare le tensioni interne, rendendo il materiale più lavorabile e meno incline alle cricche. La comprensione dell'intervallo di temperatura preciso per un materiale specifico è fondamentale per ottenere le proprietà meccaniche desiderate e garantire le prestazioni del materiale nell'applicazione prevista.
Punti chiave spiegati:
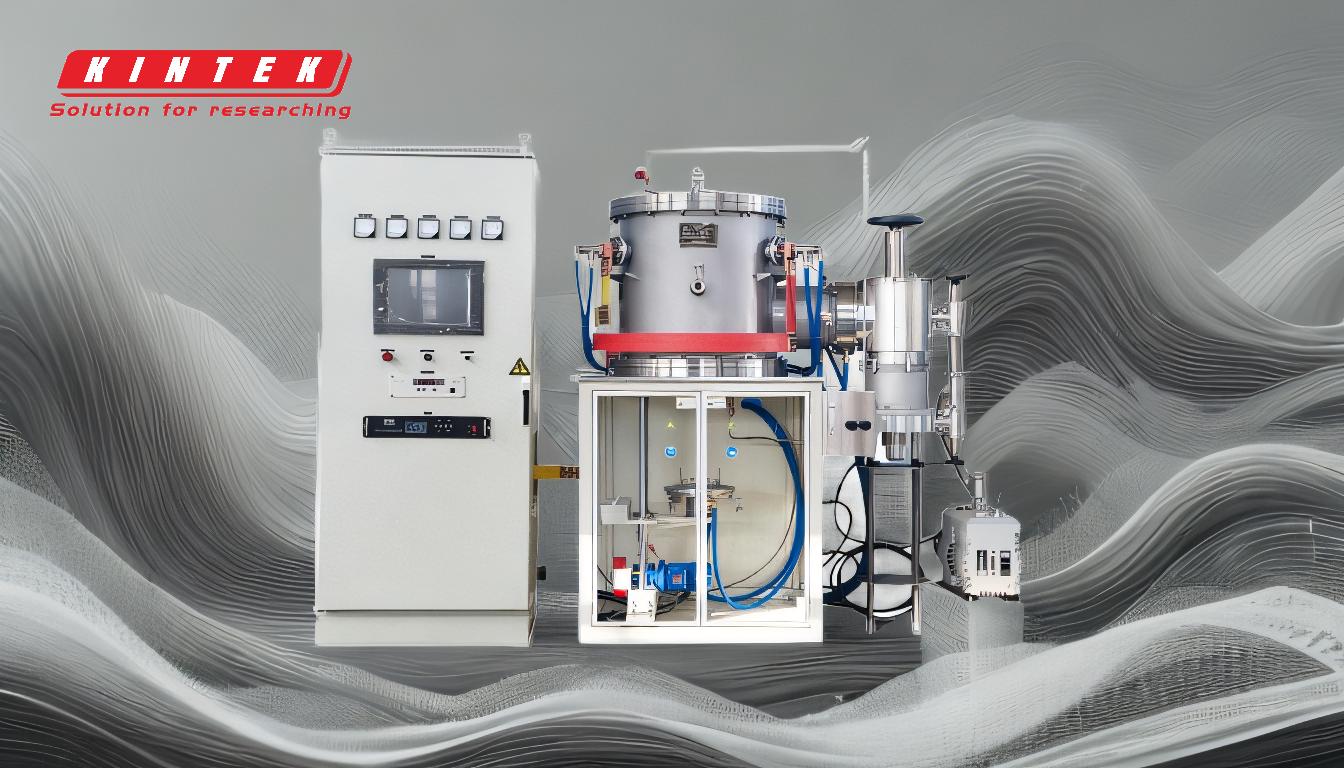
-
Definizione e scopo della ricottura Tempra:
- Definizione: La ricottura è un processo di trattamento termico in cui un materiale viene riscaldato a una temperatura specifica, mantenuto a tale temperatura per un certo periodo di tempo e quindi raffreddato a una velocità controllata.
- Scopo: L'obiettivo principale è ridurre la durezza, aumentare la duttilità e alleviare le tensioni interne del materiale. Ciò rende il materiale più facile da lavorare, formare o saldare.
-
Variabilità dell'intervallo di temperatura:
- Dipendenza dal materiale: L'intervallo di temperatura per la tempra di ricottura dipende in larga misura dal tipo di materiale trattato. I diversi materiali hanno temperature critiche diverse alle quali la loro microstruttura cambia.
- Acciaio: Per l'acciaio, la temperatura di ricottura varia tipicamente da 700°C a 900°C. Questo intervallo consente la trasformazione della microstruttura, che può alterare in modo significativo le proprietà del materiale.
- Leghe di alluminio: L'alluminio e le sue leghe richiedono generalmente temperature di ricottura più basse, in genere tra i 300°C e i 500°C. Questo perché l'alluminio ha un punto di fusione più basso rispetto all'acciaio.
- Altri metalli: Altri metalli come il rame, l'ottone e il titanio hanno i loro specifici intervalli di temperatura di ricottura, che devono essere rispettati per ottenere risultati ottimali.
-
Importanza del raffreddamento controllato:
- Velocità di raffreddamento: Dopo aver raggiunto la temperatura di ricottura, il materiale deve essere raffreddato a una velocità controllata. Un raffreddamento rapido può portare alla formazione di microstrutture indesiderate, mentre un raffreddamento lento aiuta a ottenere le proprietà desiderate.
- Metodi di raffreddamento: I metodi di raffreddamento più comuni includono il raffreddamento in forno, il raffreddamento ad aria e il raffreddamento in atmosfera controllata, ognuno dei quali viene scelto in base al materiale e al risultato desiderato.
-
Impatto sulle proprietà del materiale:
- Durezza e duttilità: Una corretta ricottura riduce la durezza del materiale, rendendolo più duttile e più facile da lavorare. Ciò è particolarmente importante nei processi di produzione in cui il materiale deve essere modellato o formato.
- Alleggerimento delle tensioni: La ricottura aiuta ad alleviare le tensioni interne che possono essere state introdotte durante i precedenti processi di produzione, come la lavorazione o la saldatura. In questo modo si riduce il rischio di rottura del materiale sotto sforzo.
- Struttura del grano: Il processo influisce anche sulla struttura dei grani del materiale, determinando una microstruttura più uniforme e raffinata, che migliora le prestazioni complessive del materiale.
-
Considerazioni pratiche per gli acquirenti di apparecchiature e materiali di consumo:
- Selezione dell'apparecchiatura di ricottura: Gli acquirenti devono tenere conto dei requisiti specifici di temperatura dei materiali da lavorare. Ciò comporta la scelta di forni in grado di raggiungere e mantenere con precisione le temperature necessarie.
- Efficienza energetica: Date le alte temperature in gioco, i forni ad alta efficienza energetica possono portare a significativi risparmi nel tempo.
- Sicurezza e conformità: Garantire che l'apparecchiatura soddisfi gli standard di sicurezza e i requisiti normativi è fondamentale, soprattutto quando si tratta di processi ad alta temperatura.
- Manutenzione e durata: La durata dell'apparecchiatura e la facilità di manutenzione sono fattori importanti, poiché riparazioni o sostituzioni frequenti possono essere costose e interrompere la produzione.
-
Conclusione:
- Precisione e controllo: Il successo del processo di tempra di ricottura dipende in larga misura da un controllo preciso della temperatura e da velocità di raffreddamento adeguate. La comprensione delle esigenze specifiche del materiale da trattare è essenziale per ottenere le proprietà desiderate.
- Efficienza economica e operativa: Per gli acquirenti di attrezzature e materiali di consumo, investire nella giusta apparecchiatura di ricottura e comprendere le sfumature del processo può portare a un miglioramento delle prestazioni dei materiali, a una riduzione dei costi e a una maggiore efficienza operativa.
In sintesi, l'intervallo di temperatura per la tempra di ricottura è un parametro critico che varia notevolmente a seconda del materiale. Un controllo adeguato di questo intervallo, insieme a un raffreddamento controllato, è essenziale per ottenere le proprietà desiderate del materiale. Per gli acquirenti, la scelta dell'apparecchiatura giusta e la comprensione delle complessità del processo sono fondamentali per garantire risultati di successo nel trattamento dei materiali.
Tabella riassuntiva:
Materiale | Intervallo di temperatura di ricottura | Scopo principale |
---|---|---|
Acciaio | 700°C - 900°C | Riduzione della durezza, aumento della duttilità |
Leghe di alluminio | 300°C - 500°C | Abbassamento del punto di fusione, riduzione delle tensioni |
Rame | 400°C - 700°C | Migliora la lavorabilità, affina la struttura dei grani |
Titanio | 700°C - 900°C | Aumentare la resistenza, alleviare le tensioni interne |
Garantire prestazioni ottimali del materiale con una precisa tempra di ricottura... contattate oggi i nostri esperti per soluzioni su misura!