La deposizione fisica da vapore (PVD) è un sofisticato processo di rivestimento utilizzato per depositare film sottili di materiale su un substrato. Il processo prevede la conversione di un materiale solido di destinazione in una fase di vapore, che poi si condensa sul substrato per formare un rivestimento sottile, durevole e spesso altamente specializzato. Il PVD è ampiamente utilizzato in settori quali l'elettronica, l'ottica e la produzione grazie alla sua capacità di produrre rivestimenti di alta qualità, resistenti alla corrosione e alla temperatura. Il processo comprende quattro fasi principali: evaporazione, trasporto, reazione e deposizione. Ogni fase è attentamente controllata per garantire le proprietà desiderate del rivestimento finale, come l'adesione, lo spessore e la composizione.
Punti chiave spiegati:
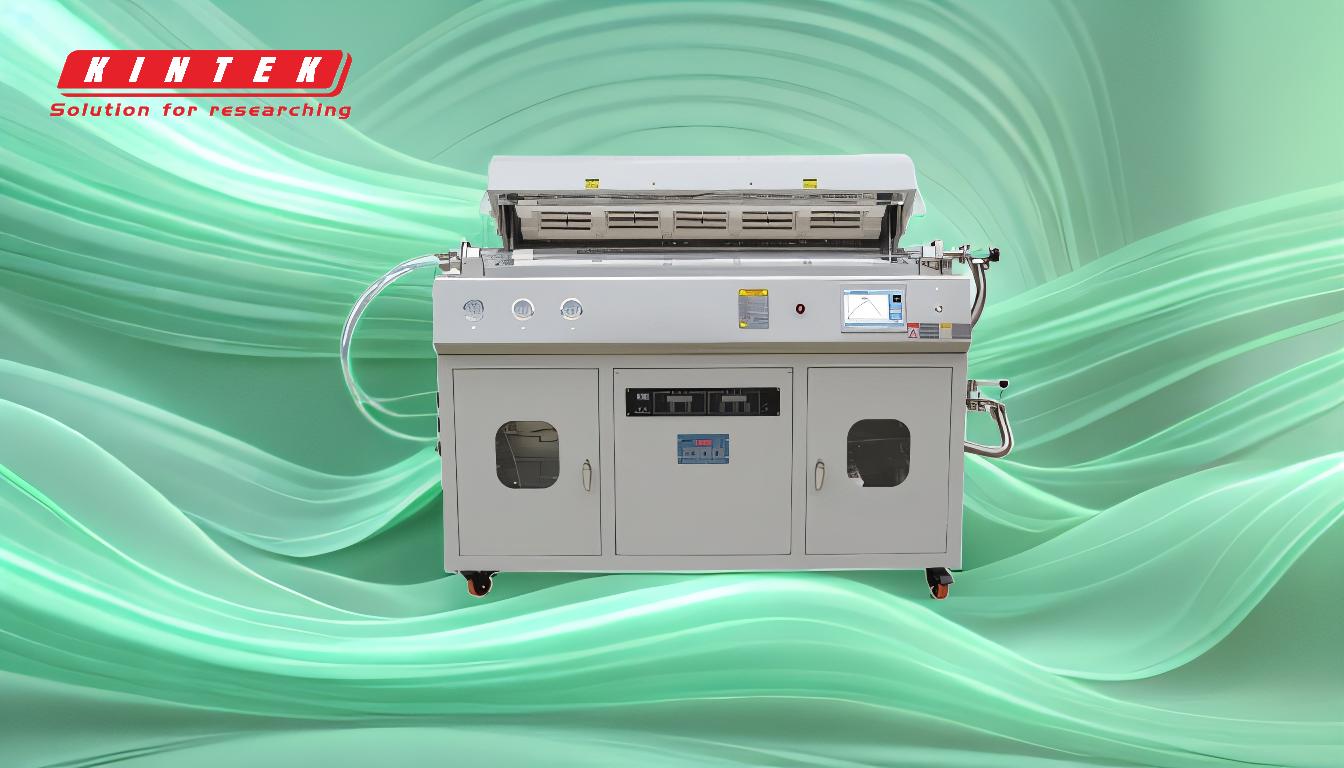
-
Evaporazione del materiale di destinazione:
- La prima fase del processo PVD è l'evaporazione del materiale di destinazione. Ciò si ottiene bombardando il bersaglio solido con una sorgente ad alta energia, come un fascio di elettroni, un laser o un fascio di ioni. L'energia provoca il distacco degli atomi del bersaglio e la transizione dalla fase solida a quella di vapore.
- Il materiale di destinazione può essere un metallo, una ceramica o un'altra sostanza solida, a seconda delle proprietà desiderate del rivestimento finale. Il processo di evaporazione viene generalmente eseguito in un ambiente sotto vuoto o a bassa pressione per ridurre al minimo la contaminazione e garantire un trasferimento pulito del materiale.
-
Trasporto di atomi vaporizzati:
- Una volta vaporizzato il materiale target, gli atomi o le molecole vengono trasportati attraverso la camera di reazione verso il substrato. Il trasporto avviene in un ambiente sotto vuoto o a bassa pressione per evitare interferenze da parte dei gas di fondo.
- La fase di trasporto è fondamentale perché determina l'uniformità con cui il materiale vaporizzato raggiunge il substrato. Spesso si utilizza il metodo della "linea di vista", in cui gli atomi vaporizzati viaggiano direttamente dal bersaglio al substrato senza dispersioni significative.
-
Reazione (opzionale):
- Durante la fase di trasporto, gli atomi vaporizzati possono reagire con i gas introdotti nella camera, come ossigeno o azoto. Questa reazione può formare composti come ossidi, nitruri o carburi, a seconda delle proprietà desiderate del rivestimento.
- Ad esempio, se si utilizza un bersaglio metallico e si introduce ossigeno, il rivestimento risultante può essere un ossido metallico. Questa fase è facoltativa e dipende dall'applicazione specifica e dalle caratteristiche desiderate del rivestimento.
-
Deposizione sul substrato:
- La fase finale consiste nella deposizione del materiale vaporizzato sul substrato. Gli atomi o le molecole si condensano sulla superficie del substrato, formando un film sottile. Il processo di deposizione è controllato per garantire lo spessore, l'adesione e l'uniformità desiderati del rivestimento.
- Il substrato può essere costituito da diversi materiali, tra cui metalli, plastiche o ceramiche, a seconda dell'applicazione. Il processo di deposizione avviene spesso a temperature comprese tra 50 e 600 gradi Celsius, a seconda dei materiali coinvolti e delle proprietà desiderate del rivestimento.
-
Controllo e monitoraggio:
- Il processo PVD è altamente controllato per garantire la qualità del rivestimento finale. Parametri come la temperatura, la pressione e la velocità di deposizione vengono attentamente monitorati e regolati.
- Per misurare e controllare lo spessore del film depositato si utilizzano strumenti come i monitor a cristallo di quarzo. Inoltre, la camera di reazione viene spesso pompata a pressioni molto basse per ridurre al minimo la presenza di gas di fondo che potrebbero interferire con il processo di deposizione.
-
Vantaggi della PVD:
- Durata: I rivestimenti PVD sono noti per la loro durezza, resistenza all'usura e durata, che li rende adatti ad applicazioni ad alta sollecitazione.
- Resistenza alla corrosione: I rivestimenti offrono un'eccellente protezione contro la corrosione, anche in ambienti difficili.
- Tolleranza alle alte temperature: I rivestimenti PVD sono in grado di resistere alle alte temperature, il che li rende ideali per le applicazioni in ambito aerospaziale, automobilistico e industriale.
- Versatilità: Il PVD può essere utilizzato per depositare un'ampia gamma di materiali, tra cui metalli, ceramiche e compositi, su vari substrati.
-
Applicazioni del PVD:
- Elettronica: La PVD è utilizzata per depositare film sottili in dispositivi semiconduttori, pannelli solari e display.
- Ottica: Il processo viene utilizzato per creare rivestimenti riflettenti o antiriflesso su lenti e specchi.
- Produzione: I rivestimenti PVD vengono applicati a utensili da taglio, stampi e altri componenti per migliorarne le prestazioni e la durata.
In sintesi, il processo PVD è un metodo altamente controllato e versatile per depositare film sottili con proprietà eccezionali. Gestendo attentamente ogni fase - evaporazione, trasporto, reazione e deposizione - i produttori possono produrre rivestimenti che soddisfano le esigenze specifiche di un'ampia gamma di applicazioni. La capacità di controllare parametri quali lo spessore, l'adesione e la composizione rende la PVD uno strumento prezioso per la produzione e la tecnologia moderna.
Tabella riassuntiva:
Fase | Descrizione |
---|---|
Evaporazione | Il materiale di destinazione viene vaporizzato utilizzando sorgenti ad alta energia come fasci di elettroni o laser. |
Trasporto | Gli atomi vaporizzati viaggiano attraverso il vuoto o un ambiente a bassa pressione fino al substrato. |
Reazione | Fase opzionale in cui gli atomi vaporizzati reagiscono con i gas per formare composti come gli ossidi. |
Deposizione | Il materiale vaporizzato si condensa sul substrato, formando un rivestimento sottile e resistente. |
Controllo | Parametri come la temperatura, la pressione e la velocità di deposizione vengono attentamente monitorati. |
Vantaggi | Durata, resistenza alla corrosione, tolleranza alle alte temperature e versatilità. |
Applicazioni | Elettronica, ottica e produzione per migliorare le prestazioni e la durata. |
Scoprite come il PVD può migliorare le prestazioni dei vostri prodotti. contattate i nostri esperti oggi stesso !